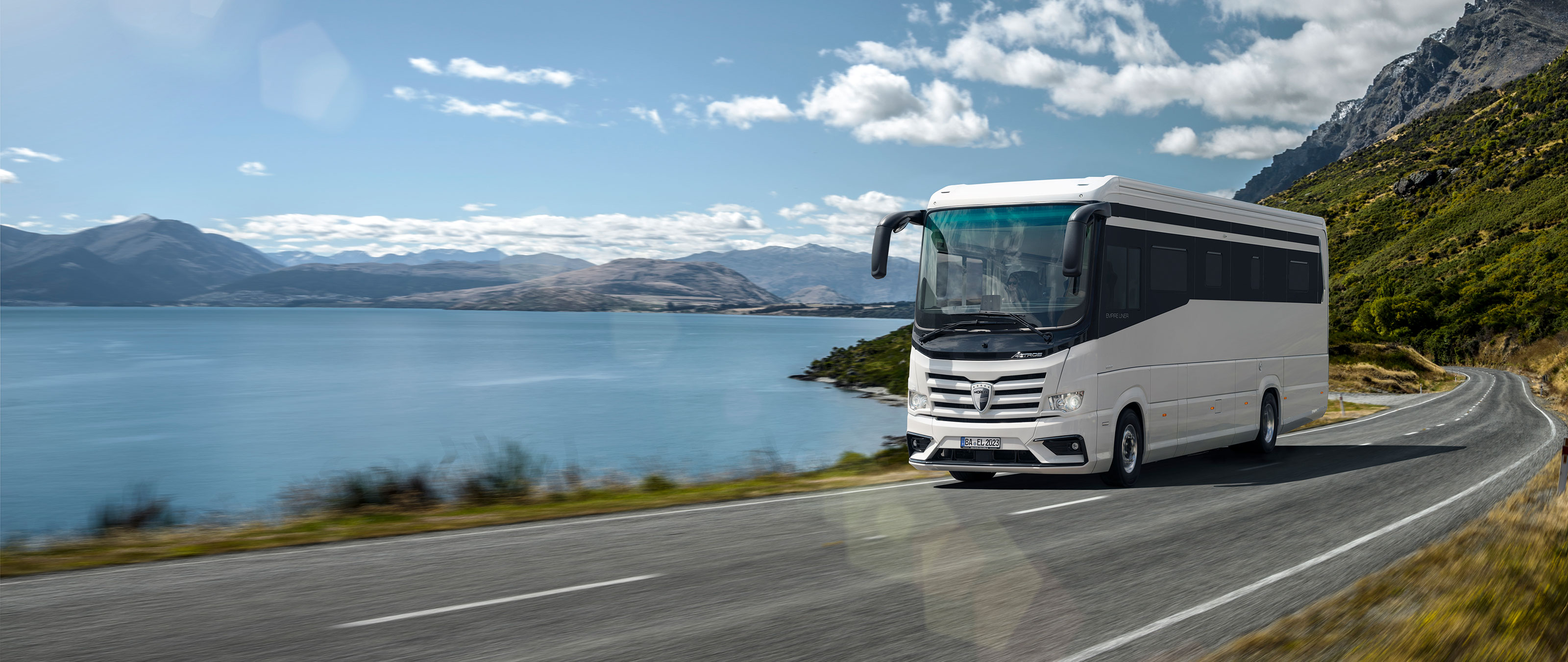
Der Name MORELO steht für First-Class-Reisemobile, die weltweit als Benchmark im Luxussegment gelten dürfen. Mit ihnen gibt das Schlüsselfelder Unternehmen ein Statement ab für Reiselust und exzellenten Komfort. Für Effizienz und Qualität beim Zuschnitt sorgt heute eine hochautomatisierte Lager-Nesting-Zelle der HOMAG Group.
Zu den “Golden” oder auch “Best Ager” zählen Menschen im Alter von 50 plus, denen Gesundheit und körperliche Fitness besonders wichtig sind, die aber auch über eine gewisse finanzielle Unabhängigkeit verfügen. Diese Golden Ager gehören zu über 90 % zur Zielgruppe von MORELO Reisemobile, haben sie doch oft ihr ganzes Berufsleben in führenden Positionen gearbeitet und geben diese nun an die nächste Generation weiter. Ihre neuen Ziele: Europa erleben. Vielleicht sogar ein Stück mehr. Ihr mobiles Zuhause dafür können sie ganz nach Geschmack aus sieben Baureihen wählen, die sich zudem individualisieren lassen. Entscheiden können sie sich zum Beispiel für einen “Home”, “Loft Liner” oder “Palace”. Die Auswahl reicht bis hin zum „Grand Empire“, der Luxusausführung aus Schlüsselfeld.
Benchmark im Luxussegment
Gegründet wurde MORELO 2010 mit dem Anspruch, Marktführer im Luxussegment von Reisemobilen zu werden. “Seit 2019 sind wir Benchmark, haben also das erste Mal den damaligen Marktführer in den Erstzulassungszahlen überholt. Jetzt fertigen wir ungefähr das Doppelte”, berichtet Geschäftsführer Robert Crispens. Diesen Abstand wolle man noch weiter vergrößern: „Nachdem wir im letzten Jahr 562 Luxusreisemobile gebaut haben, sollen es in diesem Jahr über 600 werden.
MORELO ist seit 2011 Teil der Knaus Tabbert Gruppe, die im letzten Jahr einen Umsatz von 1,4 Milliarden Euro erwirtschaftet hat. Die Schlüsselfelder haben dazu 160 Millionen Euro beigetragen. Um die Erfolgsgeschichte fortzuschreiben, ist für MORELO die Art und Weise der Fertigung ganz entscheidend. Neben dem Produktionsumfang bedeutet das zuallererst die Fertigungstiefe weiter auszubauen – um möglichst unabhängig von Zulieferern zu werden und schnell auf wechselnde Umstände reagieren zu können. Investiert wurde dafür unlängst in einen High-Performance-Maschinensaal inkl. Fertigungsleitstandssoftware (Controller MES).
All dies wäre aber nicht ohne die treuen und tatkräftigen Mitarbeiter zu realisieren. Der Faktor Mensch steht bei MORELO im Vordergrund und so wie sie es auf ihrer Homepage schreiben, „Kein exzellentes Reisemobil ohne ein exzellentes Team.“, so leben sie es auch. Daniel Medler, Gebietsverkaufsleiter bei HOMAG, schätz die partnerschaftliche Verbindung zu MORELO, die freundschaftlich geprägt, aber mit vollem Respekt, Professionalität und auf Augenhöhe gelebt wird.
State of the art
Technologisch hat sich MORELO in den vierzehn Jahren seit Gründung mehrfach neu erfunden, um die Messlatte in der Fertigung immer höher zu legen. Regelmäßig hat das Unternehmen dafür hohe Investitionen getätigt. „Letztes Jahr haben wir knapp 11 Millionen Euro investiert, in diesem Jahr werden es 15 Millionen Euro sein“, nennt Crispens die jüngsten Zahlen.
„Derzeit bauen wir ein zweites Werk, um unsere Fertigungslinien zu entkoppeln“, so der Geschäftsführer weiter. „Die aufwendigen Fahrzeuge über 12 t werden dann in einer neuen Halle gebaut. Pro Jahr sollen es ca. 200 Reisemobile sein.“ Hintergrund ist, dass MORELO derzeit mit einem Takt von 3 h produziert. Beabsichtigt ist, in Werk 1 künftig mit 2 oder 2,5 h zu fahren.
Das neue Werk 2 soll mit 11 h anlaufen, um sich später auf 8 h einzupendeln. Um die nötige Kapazität im Zuschnitt zu schaffen, hat MORELO mit der Schreinerei das größte Invest der jüngeren Vergangenheit getätigt, was gleichermaßen den Maschinensaal wie den Maschinenpark umfasste. „Bei der Lager-Nesting-Zelle haben wir uns für die HOMAG Group entschieden, weil sie State of the Art ist“, begründet dazu Crispens. „Die Entscheidung fiel aber auch mit Blick auf unsere Kunden, denen wir unsere Fertigung in Führungen immer wieder transparent machen.“
Getaktete Fahrzeugfertigung
MORELO ist ein Hersteller, der in Baukästen denkt und in diesem Rahmen individuelle Kundenwünsche erfüllt. Von den sieben gebauten Modellen hat jedes bis zu zehn Grundrisse, hinzu kommen diverse Sonderbauoptionen. „Gefertigt wird bewusst in einem Mix dieser Modelle. Und das auftragsbezogen in Losgröße 1, wobei die Fahrzeuge eine getaktete Fertigung durchlaufen“, schildert Produktionsleiter Tobias Jäger.
Die Produktion in Gänze ist teilautomatisiert: Während etwa der Zuschnitt hochautomatisiert ausgelegt ist, wird diese Automatisierung für Folgeschritte wie den Aufbau der Fahrzeuge immer wieder aufgebrochen – was sich zwingend aus den individuellen Kundenwünschen und der manuellen Montage ergibt. „An den verschiedenen Stationen wird dabei in vorgegebener Zeit montiert, die zuliefernden Vorfertigungsbereiche sind an diese Taktzeit angepasst“, so Jäger. „Zugleich liefert das Lager – heruntergebrochen auf das Einzelfahrzeug – die Taktbestückung ans Band.“ Zwischen der Ein- und Ausfahrt eines Fahrzeugs bestehen große Freiheitsgrade, sodass sich die vielseitigen Gewerke sicher in den Takt einplanen und umsetzen lassen.
Komplett überarbeitet planen und fertigen
Mit der neuen Zuschnittzelle, bestehend aus drei Nestinganlagen plus Flächenlager, hat MORELO nicht nur State-of-the-Art-Technologie im Unternehmen verankert, einmal mehr wurden auch die Fertigungsstrategie und -logik neu erfunden: Angefangen beim Maschinenpark samt Software wurde die Art der Planung und Fertigung komplett überarbeitet. So werden künftig vor allem mehrere Fahrzeuge in einem Fertigungsauftrag zusammengefasst, um die Effizienz, aber auch die Materialausbeute zu erhöhen. Zum Teil wird zwar schon heute so gearbeitet, bislang gab es jedoch verschiedene Bedarfstermine und mehrere Fahrzeuge wurden zusammengefasst nach Blockdenken gefertigt.
„Künftig soll nach Bedarfstermin aufgeteilt werden, wobei wir einzeln oder zusammengefasst arbeiten wollen“, erläutert Eric Macke, Projektingenieur bei MORELO. „Dann fräsen wir ein Bauteil exakt zu dem Termin, zu dem es gebraucht wird. Zugleich ist dieses Herunterbrechen auf das Einzellos oder Zusammenfassen von Verschiedenem auch das übergeordnete Ziel, das wir bei allen anderen Prozessen verfolgen.“ Maßgeblich für dessen erfolgreiche Umsetzung ist das neue Fertigungsleitsystem ControllerMES von HOMAG, das für Effizienz und Transparenz bei Produktionsplanung, Steuerung und Monitoring sorgt – von der Übernahme der Auftragsdaten bis zur Vollständigkeitskontrolle in der Kommissionierung.
Die entscheidende Frage
Ausgangspunkt für die Investition in die neue Zuschnittzelle samt automatisiertem Plattenlager war also die zweite Produktionslinie und die damit geplante Kapazitätserhöhung. Speziell bei den großen Reisemobilen sollen damit die Produktionszahlen steigen. Die Frage war: Mit welchem Konzept genau lässt sich der Ausstoß in der Vorfertigung, insbesondere im Zuschnitt, erhöhen? Abzulösen waren zwei Stand-alone-Nestinganlagen, die bis dahin mit einem konventionellen, teilweise manuellen Materialhandling und entsprechendem Personaleinsatz zugeschnitten hatten.
Künftig sollten sich die Plattenmaterialien deutlich effizienter handeln lassen. „Obwohl bald noch ein oder zwei Holzdekore hinzukommen, ergibt sich die Varianz – bei aktuell zwei Holzdekoren – in erster Linie aus der Stärke der Platten“, erzählt Jäger. Vor allem aber – unterstreicht er nochmals – sollte mit der neuen Zelle die Sicherheit der Fertigung gewährleistet und die Effizienz erhöht werden: „Wir haben einen großen Anteil an komplexen Teilen, zum Beispiel Freiformteile. Diese wirtschaftlich durch die Fertigung zu schleusen, ist für unsere ambitionierten Pläne von entscheidender Bedeutung.“
Hochautomatisiert lagern, nesten, handeln
Der Zuschnitt einschließlich Lagerung, Handling und Kommissionierung erfolgt heute in einem hochautomatisierten, mannarmen Prozess. Nach Anlieferung werden die Sperrholzplatten in Kragarmregalen gelagert, um bei Bedarf auf eine von drei Rollenbahnen gesetzt zu werden. Bis zu sechs Stapel lassen sich hier für die sichere Versorgung eines Flächenlagers STORETEQ P-500 puffern. Nach dem Fördern zum Lager übernimmt eine Doppelhubschere das automatische Einlagern der Platten. Für eine vorausschauende Einlagerung können am Abend auch Stapel bereitgestellt werden, da sortenrein ein- und folglich nicht umgelagert wird. Weil das STORETEQ P-500 zudem als Lager für die gesamte Produktion fungiert, verfügt es über zwei weitere Auslagerplätze für vorkommissionierte Stapel, die dann zu den Folgebearbeitungen laufen.
„Die Zuschnittzelle selbst arbeitet mit drei gekoppelten Durchlaufnestingmaschinen der CENTATEQ-N Baureihe", berichtet Manuel Voland , Projektleiter bei HOMAG. „Aufträge werden per ControllerMES an die gesamte Anlage vergeben, die sie dann auf die einzelnen Maschinen verteilt. Hierbei sind unterschiedliche Priorisierungen möglich. Üblicherweise wird jedoch für eine anstehende Bearbeitung automatisch jeweils die erste verfügbare Maschinegewählt.“
Bevor die Teile im Durchlauf genestet werden, laufen die Platten über eine angetriebene Rollenbahn zum automatischen Etikettieren. Dass heute automatisch etikettiert wird, spart Zeit und verhindert Fehler. „Nach dem Labeln wird die Platte automatisch in die Nestingmaschine eingezogen, alle Bohr-, Fräs- und Nutbearbeitungen werden durchgeführt, anschließend werden die fertigen Werkstücke , gereinigt und auf einen Auslauftisch geschoben. Schließlich werden sie von einem Quertransportwagen automatisch abgeholt und ausgefördert“, so Daniel Medler Gebietsverkaufsleiter von HOMAG weiter.
„Ist eine beidseitige Bearbeitung gefordert, läuft die bereits bearbeitete Platte vom Quertransport über einen Plattenwender (zurück ins Plattenlager und automatisch erneut in eine CENTATEQ N ein, wo dann die restlichen Bearbeitungen und das finale aufteilen stattfindet.“ Aktuell betrifft dies circa 75 % der Platten. Bei einseitiger Bearbeitung wird das Nest direkt zum Auslauf in die Handentnahme transportiert. Damit die drei CENTATEQs möglichst durchgängig in Betrieb sind, gibt es verschiedene Pufferplätze, zum Beispiel bei der Etikettierung oder vor dem Querverschiebewagen.
Auch beim Auslauf sind mehrere solcher Plätze eingerichtet, sodass die Mitarbeiter das Material komfortabel aus den verschiedenen Nestern entnehmen und kommissionieren können. „Damit endet aktuell alles, was von der Zelle kommt, an einem einzigen Punkt“, betont Tobias Jäger, Produktionsleiter bei MORELO. „Neben dem geringeren Handlingaufwand sind damit die Wege für die Kommissionierung und Folgebearbeitung entsprechend kurz.“
Wertschöpfung systematisch steigern
Seit November des letzten Jahres ist die Lager-Nesting-Zelle bei MORELO in Betrieb. Auch die Ablösung der Produktion von den bisherigen Stand-alone-Anlagen ist umgesetzt. Bei einem Nutzungsgrad von früher 60 auf mittlerweile 80 % ist der Effizienzsprung deutlich. „Aktuell erreichen wir mit der Zelle die Kapazität von vier Stand-alone-Anlagen“, rechnet Jäger. „Außerdem ist der Personalbedarf deutlich gesunken.“
Damit steht dem Reisemobilhersteller eine Anlage zur Verfügung, die – basierend auf der nötigen Prozessqualität und -sicherheit – die Steigerung der Stückzahlen samt Ressourcenoptimierung garantiert. Freilich werden Prozesse wie die Logistik oder Softwareanwendungen weiter optimiert. Darüber hinaus könnte an Stellschrauben wie dem Durchsatz-Verschnitt-Verhältnis, der konstruktiven Ausrichtung der Teile oder dem Schichtmodell gedreht werden. Es ist also reichlich Potenzial vorhanden, das sich noch heben lässt. Dazu gehört auch, outgesourcte Fertigungsleistungen ins Haus zurückzuholen.
Vor allem aber geht MORELO mit ControlerMES zunehmend von dem Prinzip ab, in Fertigungsblöcken zu fräsen: Der Bedarfstermin wird zum zentralen Steuerungskriterium. „Dadurch sind wir wesentlich schneller, können die Teile für Nachfolgebearbeitungen sauberer abstapeln und erhöhen noch einmal den Durchlauf“, unterstreicht Macke. Ein großer Hebel sei nicht zuletzt, die Lose zusammenzufassen und in die Serienfertigung zu gehen.
Mit den drei Nestinganlagen ist für all das ein weiteres Durchsatzwachstum bereits berücksichtigt. Welches genau sich erreichen lässt, werden die nächsten Monate zeigen. Ans Limit wird die Anlage allerdings nicht kommen, das gibt schon der Markt vor. Und so bleibt eins zu konstatieren: MORELO sichert mit der Lager-Zuschnitt-Zelle das Wachstum beim Bau der Reisemobile zuverlässig ab. Und das vor dem Hintergrund einer sich ändernden Alterspyramide.
„Bei der Lager-Nesting-Zelle haben wir uns für die HOMAG Group entschieden, weil sie State of the Art ist.“Robert Crispens, Geschäftsführer MORELO
MORELO Reisemobile
MORELO steht für First Class Reisemobile, die zu den besten der Welt gehören.
Mehr erfahren