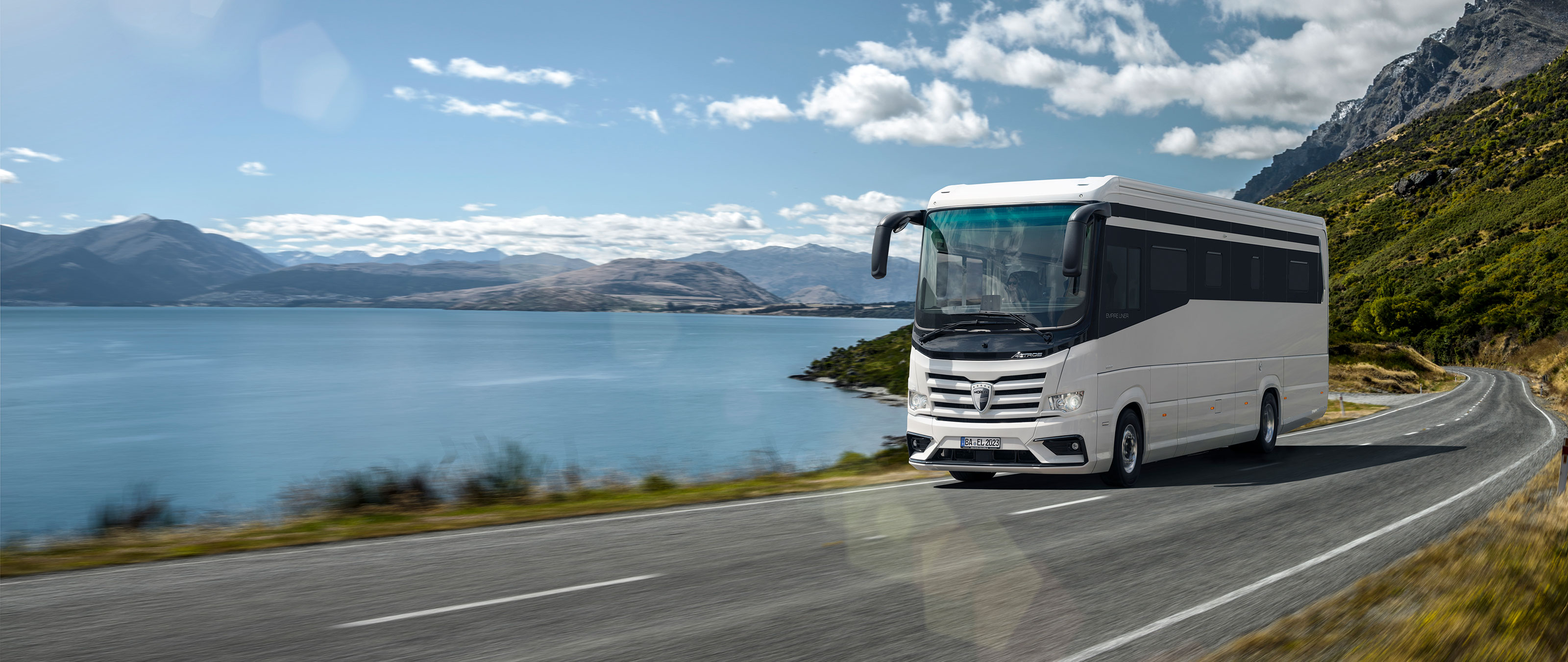
MORELO to najwyższej klasy kampery niemieckiej produkcji, które wyznaczają standardy w segmencie luksusowym na całym świecie. Dla ich producenta stanowią one symbol najwyższego komfortu i przyjemności z podróży. O wydajność i jakość przy wykroju elementów na etapie produkcji dba dziś wysoko zautomatyzowane gniazdo magazynująco-nestingowe firmy Homag Group.
Osoby „w złotym wieku” to ludzie w wieku od 50 lat wzwyż, którzy szczególnie cenią sobie zdrowie i sprawność fizyczną, a są przy tym niezależni finansowo. Często większość swojej kariery przepracowali na stanowiskach kierowniczych, a teraz przekazują je kolejnym pokoleniom. To właśnie oni stanowią nawet 90% grupy docelowej producenta kamperów MORELO. Ich nowym celem jest zwiedzenie Europy, a może nawet jeszcze dalszych rejonów. Mobilny dom na taką podróż znajdą wśród siedmiu serii pojazdów MORELO, które mogą także dostosować do swoich indywidualnych potrzeb i upodobań. Do wyboru mają między innymi modele „Home”, „Loft Liner” czy „Palace”. Najbardziej luksusową wersją jest „Grand Empire”. Wszystkie pojazdy MORELO wyjeżdżają z zakładu produkcyjnego w niemieckim Schlüsselfeld.
Nowy standard w segmencie luksusowym
Firma MORELO powstała w 2010 r., od razu z zamiarem stania się liderem na rynku kamperów w segmencie luksusowym. „Stoimy na czele branży od 2019 r., bo wtedy po raz pierwszy prześcignęliśmy ówczesnego lidera liczbą produkowanych pojazdów. Obecnie nasza produkcja jest jeszcze dwa razy większa” – opowiada prezes Robert Crispens. Tę przewagę postanowiono dalej powiększać: „Po wyprodukowaniu w zeszłym roku 562 luksusowych kamperów w tym roku zamierzamy przekroczyć liczbę 600 sztuk.
Od 2011 r. firma MORELO należy do grupy Knaus Tabbert, która w zeszłym roku osiągnęła obrót 1,4 miliarda euro, z czego 160 milionów euro to udział producenta ze Schlüsselfeld. Czynnikiem decydującym o zdolności firmy MORELO do odnoszenia dalszych sukcesów jest sposób produkcji. Oprócz zakresu produkcji oznacza to przede wszystkim rozbudowę produkcji własnej – aby w jak największym stopniu uniezależnić się od dostawców zewnętrznych i móc szybko reagować na zmieniające się uwarunkowania rynkowe. W związku z tym firma dokonała niedawno inwestycji w wysoko wydajną maszynownię wraz z oprogramowaniem stanowiska dyspozytorskiego (Controller MES).
Wszystko to nie byłoby możliwe bez zaangażowania pracowników.
W MORELO to oni stoją na pierwszym miejscu, ponieważ jak głosi motto firmy: „Bez doskonałego zespołu nie powstanie doskonały kamper”. Daniel Medler, dyrektor ds. sprzedaży regionalnej w firmie HOMAG, ceni sobie partnerskie relacje z MORELO, które cechują serdeczność, ale także pełny szacunek, profesjonalizm i współpraca na równych zasadach.
Najnowocześniejsza technologia
W ciągu 14 lat od założenia firma MORELO wielokrotnie modyfikowała stosowane technologie produkcyjne, aby stale podnosić sobie poprzeczkę. W tym celu regularnie dokonywała sporych inwestycji. „W zeszłym roku zainwestowaliśmy blisko 11 milionów euro, w tym roku będzie to 15 milionów” – wylicza Crispens.
„Obecnie jesteśmy w trakcie budowy drugiego zakładu, aby rozdzielić nasze linie produkcyjne” – ciągnie dalej prezes. „W nowej hali będą produkowane bardziej wymagające pojazdy powyżej 12 ton. Rocznie ma tam powstawać ok. 200 kamperów”. Powodem jest to, że MORELO produkuje obecnie w takcie trzygodzinnym. Zgodnie z założeniem w zakładzie nr 1 takt ma zostać skrócony do 2 lub 2,5 godziny.
Nowy zakład – nr 2 – ma początkowo produkować w takcie 11-godzinnym, aby później ograniczyć ten czas do stabilnych 8 godzin. Aby osiągnąć przy tym odpowiednią wydajność wykroju, firma MORELO poczyniła w swojej stolarni największą inwestycję w ostatnich latach, która objęła w równej mierze maszynownię, jak i sam park maszynowy. „Przy tworzeniu gniazda magazynująco-nestingowego zdecydowaliśmy się na współpracę z Homag Group, ponieważ oferuje najnowocześniejszą technologię” – argumentuje Crispens. „Taką decyzję podjęto jednak również przez wzgląd na naszych klientów, ponieważ chcemy, aby nasza produkcja była dla nich jak najbardziej transparentna”.
Produkcja pojazdów w taktach
MORELO jest producentem, który myśli modułowo i w ramach tych modułów spełnia indywidualne życzenia klientów. Każdy z siedmiu oferowanych modeli może być produkowany według nawet dziesięciu projektów, a tego dochodzą wersje specjalne. „Z pewnością można powiedzieć, że produkowane pojazdy są mieszanką poszczególnych modeli. Powstają przy tym w pojedynczych partiach realizowanych na zlecenie i w ramach produkcji odbywającej się w taktach” – opowiada kierownik produkcji Tobias Jäger.
Cała produkcja przebiega w sposób częściowo zautomatyzowany. Podczas gdy automatyzacja wykrojów jest na wysokim poziomie, to stopień zautomatyzowania kolejnych etapów produkcji oraz montażu jest już różny – co wynika bezpośrednio z indywidualnych życzeń klienta oraz ręcznego montażu. „Montaż na poszczególnych stacjach odbywa się w założonych taktach, a poprzedzające etapy produkcji są do tych przedziałów czasowych dopasowywane” – mówi Jäger. „Jednocześnie magazyn – podzielony odpowiednio do poszczególnych pojazdów – doprowadza do taśmy elementy potrzebne do realizacji taktu”. Proces między wlotem a wylotem można swobodnie planować, aby pomieścić różne zadania w założonym takcie.
Całkowicie nowa koncepcja planowania i produkcji
Wraz z nową komórką wykroju, składającą się z trzech maszyn do nestingu oraz magazynu powierzchni, firma MORELO wprowadziła do swojego zakładu nie tylko najnowocześniejszą technologię, lecz także nowa strategię i logikę produkcyjną. Począwszy od parku maszynowego po oprogramowanie, sposób planowania i realizacji produkcji został całkowicie przemodelowany. Przede wszystkim w przyszłości w ramach jednego zlecenia produkcyjnego będzie produkowanych kilka pojazdów, aby zwiększyć wydajność oraz wykorzystanie materiału. Częściowo już dziś pracuje się tu w ten sposób, jednak do tej pory obowiązywały różne terminy zleceń, a pojazdy były grupowane według bloków.
„W przyszłości produkcja będzie dzielona według terminów i zgodnie z nimi pojazdy będą produkowane pojedynczo lub grupowo” – wyjaśnia Eric Macke, inżynier ds. projektów w MORELO. „Będziemy więc frezować elementy dokładnie na wymagany termin. Taki podział na partie pojedyncze oraz grupy różnych elementów jest celem nadrzędnym, który będziemy realizować także we wszystkich pozostałych procesach”. Zasadnicze znaczenie dla wdrożenia takiego rozwiązania ma nowy system zarządzania produkcją ControllerMES firmy Homag, który służy do utrzymania wydajności i przejrzystości planowania produkcji, a także do sterowania i monitorowania procesów – od otrzymania plików zlecenia aż po kontrolę kompletności podczas komisjonowania.
Decydująca kwestia
Celem inwestycji w nową komórkę wykroju ze zautomatyzowanym magazynem płyt było więc utworzenie drugiej linii produkcyjnej i co za tym idzie – planowane zwiększenie mocy produkcyjnych. Miało to podnieść statystyki produkcyjne dotyczące zwłaszcza dużych kamperów. Pytanie jednak brzmiało: w jaki sposób zwiększyć wydajność prefabrykacji, zwłaszcza w zakresie wykrojów? Dwie oddzielne maszyny do nestingu, które dotychczas wykrawały elementy w sposób konwencjonalny z częściowo ręczną obsługą angażującą pracowników, musiały zostać zastąpione.
W przyszłości materiały płytowe mają być obsługiwane w sposób znacznie bardziej wydajny. „Choć wkrótce do produkcji wejdą jeden lub dwa nowe forniry, to – przy obecnie stosowanych dwóch fornirach – różnorodność procesu wynika głównie z grubości płyt” – opowiada Jäger. Jednak jak sam podkreśla, nowa komórka ma przede wszystkim zagwarantować bezpieczeństwo produkcji oraz podnieść jej wydajność: „Duży udział wszystkich naszych elementów stanowią elementy złożone, na przykład o kształcie dowolnym. Przeprowadzenie ich przez cały proces produkcji w sposób dla nas opłacalny ma dla naszych ambitnych planów kluczowe znaczenie”.
Wysoka automatyzacja magazynowania, nestingu i transportu
Wykrój łącznie z magazynowaniem, transportem i komisjonowaniem odbywa się dziś w sposób wysoko zautomatyzowany bez nadzoru pracowników. Płyty sklejkowe są składowane na regałach wspornikowch, aby w razie potrzeby móc umieścić je na jednym z trzech przenośników rolkowych. W ten sposób można utworzyć bufor dla magazynu powierzchni STORETEQ P-500 w postaci nawet sześciu stosów. Po przetransportowaniu płyt do magazynu podwójny podnośnik nożycowy automatycznie wprowadza je do magazynu. Można również przygotować całe stosy, ponieważ wprowadzanie do magazynu odbywa się według rodzajów płyt i nie są one później przenoszone. Ponieważ STORETEQ P-500 służy także za magazyn dla całej produkcji, ma on dwa dodatkowe miejsca wydawania przeznaczone na wcześniej skomisjonowane stosy. Są one następnie przekazywane do dalszej obróbki.
„Komórka wykroju pracuje z trzema połączonymi maszynami przelotowymi do nestingu z serii CENTATEQ-N” – opowiada Manuel Voland, kierownik projektu w firmie Homag. „Zlecenia są przekazywane przez oprogramowanie ControllerMES do całej instalacji, która rozdziela je na poszczególne maszyny. Można przy tym określić różne priorytety. Jednak zwykle do realizacji oczekującej obróbki automatycznie wybierana jest pierwsza dostępna maszyna”.
Zanim elementy zostaną podzielone w ramach nestingu, płyty są transportowane przez napędzany przenośnik rolkowy w celu automatycznego naniesienia etykiet. Automatyczne etykietowanie oszczędza czas i zapobiega błędom. „Po opatrzeniu etykietą płyta jest automatycznie wciągana do maszyny do nestingu, wykonywane są wszystkie procesy wiercenia, frezowania i wykonywania wpustów, a następnie gotowe elementy są czyszczone i umieszczane na stole wylotowym. Na koniec wózek transportu poprzecznego automatycznie je odbiera” – wyjaśnia Daniel Medler, dyrektor ds. sprzedaży regionalnej z firmy HOMAG.
„Jeśli wymagana jest obróbka dwustronna, wózek kieruje płytę obrobioną z jednej strony przez odwracarkę płyt z powrotem do magazynu płyt i do CENTATEQ-N, gdzie następuje pozostała obróbka oraz ostateczny podział płyty”. Takiemu procesowi poddawanych jest obecnie ok. 75% płyt. W razie obróbki jednostronnej elementy po nestingu są transportowane do wylotu, skąd obiera je ręcznie pracownik. Aby trzy maszyny CENTATEQ mogły jak najsprawniej ze sobą współpracować, dostępne są różne bufory, np. przy etykietowaniu lub przed wózkiem transportu poprzecznego.
Również przy wylocie przewidziano kilka takich buforów, aby pracownicy mogli wygodnie odebrać materiał z różnych maszyn nestingowych i je skomisjonować. „I właściwie wszystko, co wychodzi z tej komórki, trafia zawsze do jednego punktu” – podkreśla Tobias Jäger, kierownik produkcji w MORELO. „Oprócz mniejszego nakładu pracy związanego z przekładaniem elementów również drogi pokonywane podczas komisjonowania i dalszej obróbki są odpowiednio krótsze”.
Systematyczne zwiększanie wartości dodanej
Komórka magazynująco-nestingowa działa w zakładzie MORELO od listopada zeszłego roku. Wyłączono już także z produkcji dotychczasowe pojedyncze maszyny. W efekcie znacznie podniesiono wydajność – stopień wykorzystania wzrósł z 60% do 80%. „Obecnie nowa komórka zapewnia moce produkcyjne równorzędne z czterema maszynami pojedynczymi” – szacuje Jäger. „Ponadto znacznie zmalało zapotrzebowanie na pracowników”.
W ten sposób producent kamperów zyskał instalację, która gwarantuje wzrost liczby produkowanych sztuk i optymalizację wykorzystania zasobów przy jednoczesnym zapewnieniu wymaganego poziomu jakości i bezpieczeństwa procesów. Oczywiście dalszej optymalizacji są poddawane jeszcze takie obszary, jak logistyka czy oprogramowanie. Ponadto można też przyjrzeć się możliwym usprawnieniom pod względem stosunku odpadów do przerobu, ułożenia elementów czy modelu pracy zmianowej. Istnieje więc jeszcze spory potencjał do wykorzystania, tkwiący choćby w procesach produkcyjnych zlecanych na zewnątrz, które firma zamierza ostatecznie realizować we własnych zakładach.
Przede wszystkim jednak MORELO chce z pomocą systemu ControllerMES w coraz większym stopniu odchodzić od koncepcji frezowania gotowych bloków – nowym kryterium dla sterowania ma być termin zlecenia. „W ten sposób możemy znacznie szybciej produkować, dokładniej układać elementy w stosy do dalszej obróbki i dodatkowo usprawnić przebieg” – podkreśla Macke. Sporą korzyścią jest także możliwość grupowania partii i ich realizacji w ramach produkcji seryjnej.
Dzięki zastosowaniu trzech maszyn do nestingu można tu oczekiwać dodatkowego zwiększenia przerobu. To, jakie dokładnie korzyści uda się osiągnąć, pokażą kolejne miesiące. Nowa instalacja daje tu w każdym razie duże możliwości. Jedno można stwierdzić na pewno: wraz z komórką magazynująco-nestingową firma MORELO zagwarantowała sobie pewny wzrost w produkcji kamperów – a to doskonała odpowiedź na potrzeby rynku ze zmieniającą się piramidą wieku.
Wydanie sierpień 2024 r. Wydanie sierpień 2024 r.
„Zdecydowaliśmy się na Grupę HOMAG, ponieważ jest to najnowocześniejsze rozwiązanie.”Robert Crispens, dyrektor zarządzający MORELO
Kampery MORELO
MORELO oznacza najwyższej klasy samochody kempingowe, które są jednymi z najlepszych na świecie.
Mehr erfahren