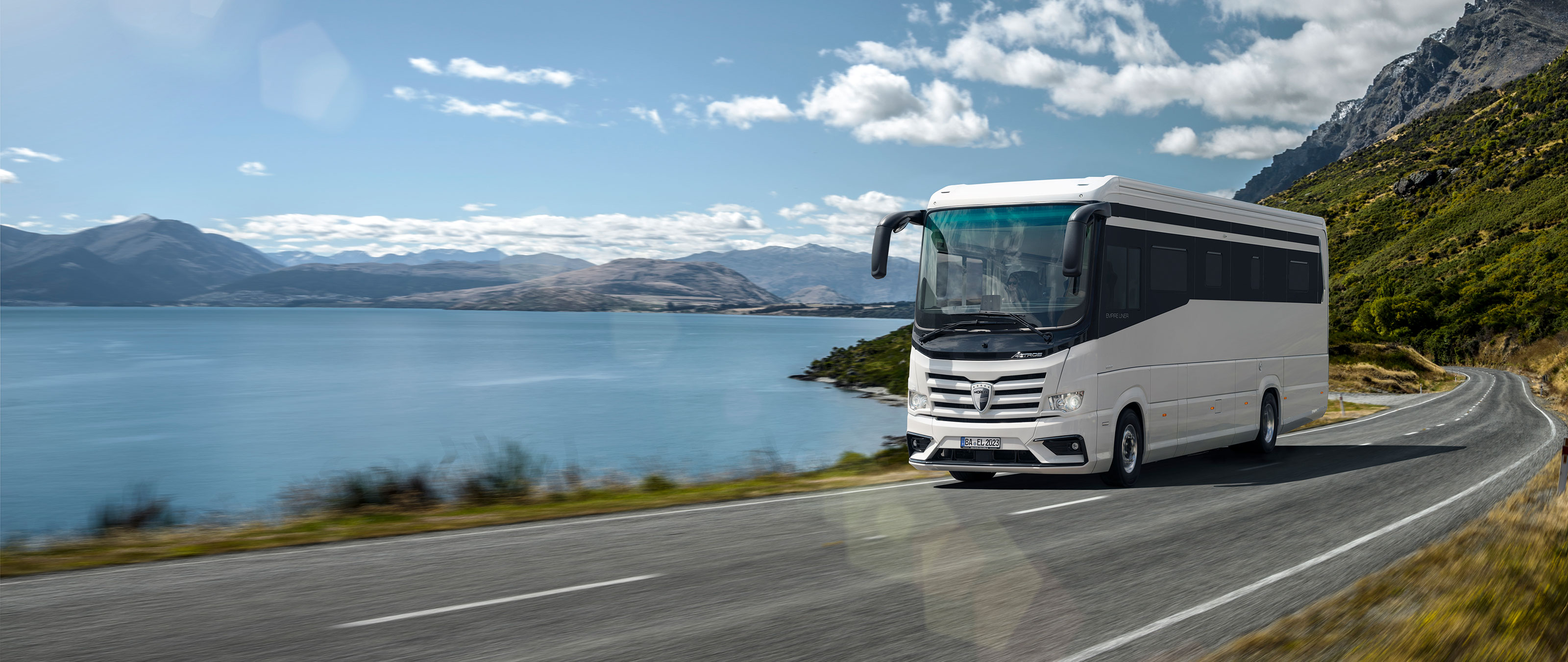
Название MORELO ассоциируется с первоклассными автокемперами, которые считаются эталоном роскоши. Для предприятия из Шлюссельфельда дома на колесах – это их собственный способ рассказать об удовольствии от путешествий и абсолютном комфорте. Об эффективности и качестве при раскрое теперь заботится поставленный Homag Group высокоэффективный производственный участок из склада и обрабатывающих центров, использующих технологию нестинга.
«Золотым» или «лучшим» возрастом считается возраст старше 50 лет; людям в этом возрасте особенно важны здоровье и хорошее самочувствие, при этом они уже добились определенной финансовой независимости. Люди в зрелом возрасте составляют более 90 % целевой группы компании MORELO Reisemobile; зачастую клиенты компании занимали ранее руководящие посты и теперь уступают их следующему поколению. Их новая цель: путешествовать по Европе. Или даже немного дальше. Дом на колесах можно выбрать по собственному вкусу из семи разных серий и при желании индивидуализировать дополнительно. Например, можно выбрать один из домов из серий «Home», «Loft Liner» или «Palace». Максимально роскошное исполнение домов на колесах из Шлюссельфельда носит имя «Grand Empire».
Воплощение роскоши
Фирма MORELO была создана в 2010 году и с самого начала ставила перед собой цель стать лидером рынка автокемперов класса «люкс». «2019 год стал для нас точкой отсчета – мы в первый раз обогнали прежнего лидера рынка по количеству впервые зарегистрированных автомобилей. Теперь мы производим примерно вдвое больше», – рассказывает управляющий предприятия Роберт Криспенс. Эту дистанцию он хотел бы увеличить еще больше: «В прошлом году мы построили 562 роскошных автокемпера, а в этом году их уже будет больше 600».
С 2011 года фирма MORELO входит в состав группы Knaus Tabbert Gruppe, оборот которой в прошлом году составил 1,4 млрд. евро. На долю предприятия из Шлюссельфельда пришлось 160 млн. евро. Продолжить историю успеха без правильных технологических решений для MORELO было бы невозможно. Кроме объемов первостепенное значение имеет дальнейшее увеличение глубины производства – чтобы обеспечить максимальную независимость от поставщиков и быстро реагировать на изменение условий. Поэтому в недавнем прошлом фирма приняла решение вложить средства в новый цех с высокопроизводительным оборудованием и программное обеспечение для центра управления производством (Controller MES).
Но такие вложения не имеют смысла без мотивированных и энергичных сотрудников.
Человеческий фактор имеет для MORELO первостепенное значение, о чем и сказано на их сайте: «Идеальный автокемпер невозможен без идеальной команды», и фирма всегда следует этому принципу. Даниэль Медлер, региональный руководитель по продажам HOMAG, высоко ценит партнерскую и равноправную связь с MORELO, одновременно дружескую и полную уважения и профессионализма. .
Актуальный технический уровень
За четырнадцать лет, прошедших с момента основания, фирма MORELO несколько раз переизобретала себя технологически, чтобы все выше поднимать планку в производстве. Предприятие регулярно делало соответствующие инвестиции. «В прошлом году мы вложили около 11 млн. евро, в этом сумма составила уже 15 млн. евро», – называет г-н Криспенс последние цифры.
«Сейчас мы строим второй завод, чтобы разделить наши производственные линии», – продолжает управляющий. «Особенно трудоемкие автокемперы весом больше 12 тонн теперь производятся в новом цеху. В год должно производиться около 200 таких домов на колесах». В настоящее время продолжительность рабочего цикла на заводе MORELO составляет 3 часа. Планируется, что на заводе 1 длительность цикла в будущем составит 2 или 2,5 часа.
Новый завод 2 должен начать с 11-часового цикла с последующим переходом на 8-часовой. Чтобы добиться необходимой выработки на участке раскроя, фирма MORELO в недавнем прошлом сделала самую большую в своей истории инвестицию, включившую в себя вложения в цех и оборудование. «При выборе оборудования для производственного участка, включающего в себя склад и обрабатывающие центры, использующие технологию нестинга, мы приняли решение в пользу Homag Group, потому что их продукция полностью отвечает актуальному уровню развитию техники», – объясняет свой выбор г-н Криспенс. «Мы также учли возможные ознакомительные экскурсии на производство, которые мы регулярно организуем для наших покупателей».
Поточное производство с заданным тактом
MORELO организует свое производство по модульному принципу, и использует этот подход для выполнения индивидуальных пожеланий заказчиков. Для каждой из семи изготавливаемых моделей предлагается до десяти планировок, которые также дополняются различными специальными опциями. «Мы приняли осознанное решение изготавливать разные модели одновременно. В зависимости от заказа возможно производство единичных изделий, при этом изготовление автомобилей разделено на циклы», – описывает ситуацию руководитель производства Тобиас Егер.
Часть производства автоматизирована: участок раскроя отличается высокой степенью автоматизации, а следующие за ним участки, например, участок монтажа, автоматизированы в гораздо более низкой степени – эти различия вызваны необходимостью выполнять индивидуальные пожелания клиентов и собирать автомобили вручную. «На разных участках монтаж выполняется с заданной скоростью, и ответственные за их снабжение предварительно собранными компонентами подразделения работают в соответствии с их производственным циклом», – объясняет г-н Егер. «Одновременно склад загружает конвейер деталями, предназначенными для определенного автомобиля». Этапы между начальной и завершающей стадией можно планировать достаточно свободно, благодаря чему возможно выполнение сложных комплексных конструкций с точным соблюдением сроков.
Полностью новая система планирования и производства
Новый участок раскроя, который состоит из трех обрабатывающих центров, использующих технологию нестинга, и системы горизонтального хранения, не только приобщил предприятие MORELO к самым современным технологиям, но и позволил внедрить новую стратегию и логику производства: способ планирования и производства был полностью переработан начиная с оборудования и программного обеспечения. Так, в будущем одно производственное задание будет включать в себя несколько автомобилей, что позволит увеличить эффективность и сократить расход материалов. Частично этот подход используется уже сейчас, когда несколько автомобилей изготавливается по модульному принципу одновременно в соответствии с заданными сроками готовности.
«В будущем объединение и разделение заданий будет зависеть от заданного срока готовности», – объясняет Эрик Маке, инженер проекта в компании MORELO. «Фрезерный станок обрабатывает деталь точно к требуемому сроку. В то же время изготовление единичных изделий и объединение разных партий остается для нас основным приоритетом, которому должны быть подчинены все процессы». Определяющее значение для реализации этого принципа имеет новая поставляемая Homag система управления производством ControllerMES, которая обеспечивает эффективность и прозрачность при планировании производства, а также при управлении и мониторинге на всех этапах начиная с получения данных задания и заканчивая проверкой комплектования заказа.
Решающий вопрос
Исходным пунктом для приобретения оборудования для нового участка раскроя с автоматизированным складом плит стало появление второй производственной линии и запланированное одновременное расширение мощностей. В первую очередь должно вырасти производство автокемперов больших размеров. Вопрос состоял в следующем: какая концепция поможет увеличить выработку на этапе производства деталей, в первую очередь – на участке раскроя? Замены требовали два независимых станка для нестинга с обычной загрузкой, частично выполняемой вручную и потому требующей участия соответствующего количества работников.
В будущем перемещение плит должно было стать более эффективным. «Хотя мы планируем вскоре добавить один или два варианта деревянного декора (сейчас таких вариантов всего два), большинство сложностей вызывает разная толщина плит», – рассказывает г-н Егер. Но в первую очередь, как еще раз подчеркивает он, новый производственный участок должен повысить надежность и эффективность производства: «Мы изготавливаем большое количество деталей сложных и свободных форм. Наши амбициозные планы изменения производства должны, и это определяющий фактор, сделать их изготовление экономичным».
Высокая степень автоматизации при складировании, нестинге и транспортировке
Раскрой, который включает складирование, транспортировку и комплектацию заказа, теперь выполняется в рамках высокоавтоматизированного, почти не требующего участия человека процесса. После поставки фанерные плиты укладываются на консольные стеллажи, чтобы при необходимости их можно было переложить на один из трех рольгангов. Для надежного снабжения системы горизонтального хранения STORETEQ P-500 здесь можно разместить до шести штабелей для промежуточного хранения. После поступления на склад укладку плит на хранение выполняет подъемный стол с двойным ножничным механизмом. Для складирования с учетом плана производства штабели с отсортированными плитами, не требующие дальнейшей переукладки, можно подготовить вечером предшествующего дня. Так как STORETEQ P-500 также выполняет функции склада для производства в целом, система оснащена двумя дополнительными местами выгрузки для предварительно скомплектованных штабелей, которые затем направляются к месту последующей обработки.
«Сам участок раскроя работает с тремя соединенными друг с другом проходными обрабатывающими центрами серии CENTATEQ-N», – объясняет Мануэль Фоланд, руководитель проекта компании Homag. «Задания для всей установки поступают из системы ControllerMES и затем распределяются между станками. При этом можно по-разному распределять приоритеты. Обычно для следующей обработки выделяется первый освободившийся станок».
Перед тем, как детали компонуются для нестинга, плиты по рольгангу с приводом подаются для автоматического наклеивания этикеток. Автоматическое наклеивание этикеток позволило сократить затраты времени и помогает избегать ошибок. «После наклеивания этикетки плита автоматически загружается в обрабатывающий центр для нестинга, выполняются все операции по сверлению, фрезерованию и выборке пазов, после чего готовые заготовки очищаются и выталкиваются на стол для выгрузки. Затем их автоматически забирает каретка поперечного транспортера и заготовки выгружаются», – продолжает Даниэль Медлер, региональный руководитель по продажам компании HOMAG.
«Если необходима обработка с двух сторон, уже обработанная плита по поперечному транспортеру через манипулятор плит возвращается на склад плит и автоматически загружается в CENTATEQ N, где выполняются оставшиеся операции обработки и окончательный раскрой». Сейчас этот процесс проходит примерно 75 % плит. При односторонней обработке скомпонованные детали транспортируются прямо к месту ручной выгрузки. Чтобы три станка CENTATEQ работали по возможности непрерывно, используются разные места промежуточного хранения, например, рядом с этикетировщиком или перед тележкой поперечного транспортера.
Также такие места промежуточного хранения есть в зоне выгрузки, благодаря чему сотрудник может без лишних сложностей разобрать вырезанные из одной плиты детали и рассортировать их по разным заказам. «Таким образом сейчас все детали, изготовленные на производственном участке, оказываются в одной точке», – подчеркивает Тобиас Егер, руководитель производства компании MORELO. «Кроме небольших затрат на перемещение плит и деталей, преимущество состоит в более коротких путях при комплектовании заказов и дальнейшей обработке».
Систематическая оптимизация
Производственный участок из склада и обрабатывающих центров для нестинга работает на производстве MORELO с ноября прошлого года. Теперь он полностью заменяет использовавшиеся раньше отдельные станки. Коэффициент загрузки при этом повысился с 60 до 80 %, что означает явный рост эффективности. «Сейчас один производственный участок обеспечивает выработку четырех независимых станков», – подсчитывает г-н Егер. «Кроме того, серьезно сократилась потребность в персонале».
При этом производитель автокемперов эксплуатирует оборудование, которое благодаря качеству и надежности процессов гарантирует повышение выработки и оптимизацию использования ресурсов. Оптимизация процессов будет продолжена в областях логистики и программного управления. Кроме того, можно еще точнее настроить процессы для уменьшения количества расходов, повышения конструктивного соответствия деталей или оптимизации модели сменной работы. Таким образом, потенциал для дальнейших улучшений далеко не исчерпан. Одним из направлений должна стать интеграция процессов, которые на данный момент выполняются сторонними предприятиями.
При использовании системы ControlerMES компания MORELO в первую очередь исходит из необходимости соблюдать производственные циклы: главный критерий при управлении – заданный срок. «Благодаря такому подходу мы работаем намного быстрее, лучше сортируем детали для дальнейшей обработки и еще больше увеличиваем выработку», – подчеркивает г-н Маке. Не в последнюю очередь следует упомянуть возможность объединять изготавливаемые детали в партии и переходить к серийному производству.
При приобретении трех обрабатывающих центров для нестинга учитывалось дальнейшее увеличение производительности. Результаты станут ясны в ближайшие месяцы. Едва ли производственный участок когда-нибудь достигнет верхнего предела своей производительности, это определяется условиями рынка. Остается констатировать: внедрив систему из автоматического склада и оборудования для раскроя, компания MORELO обеспечила себе надежный рост при производстве автокемперов. Даже с учетом изменений в распределении возрастов в демографической структуре общества.
Выпуск август 2024 года Выпуск август 2024 года
«Мы решили выбрать группу HOMAG для ячейки хранения, потому что это современное решение.»Роберт Криспенс, управляющий директор MORELO