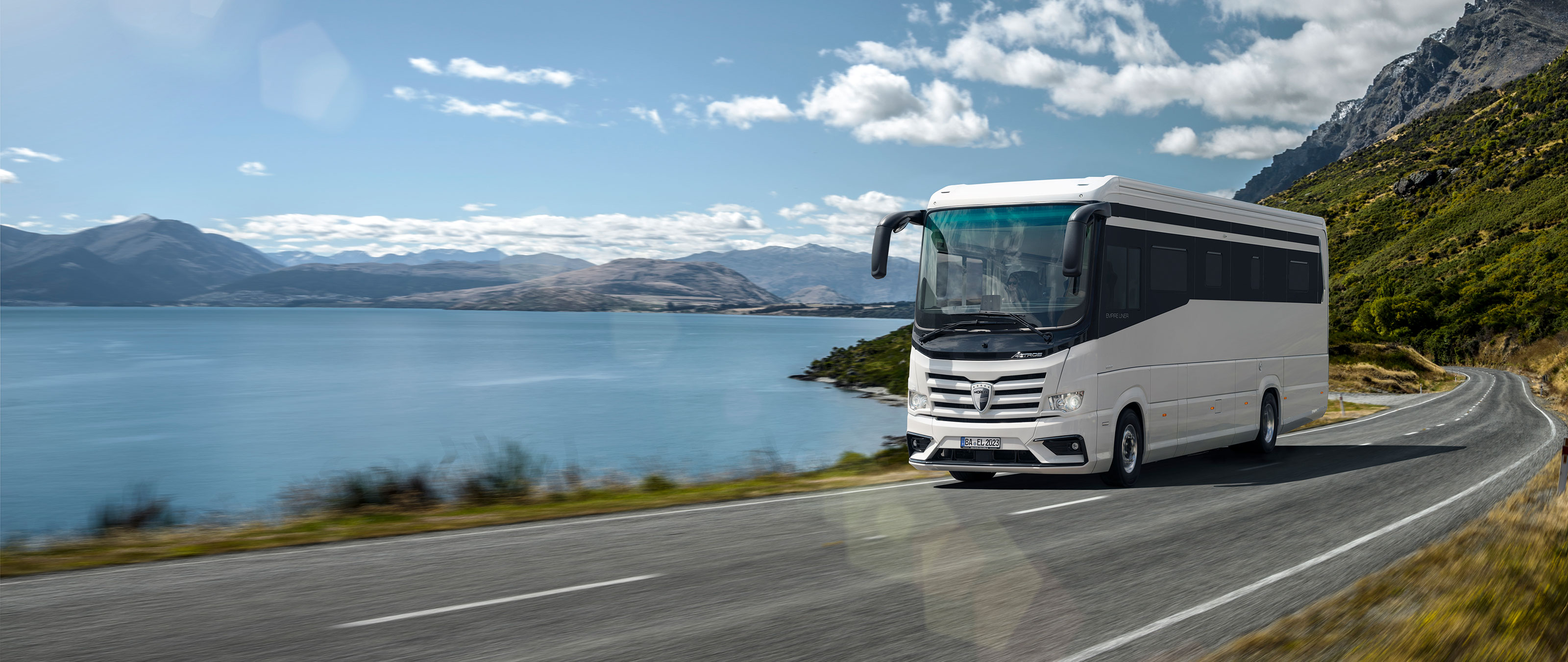
Le nom MORELO est synonyme de camping-cars de première classe, considérés comme une référence mondiale dans le segment du luxe. Grâce à ces derniers, l'entreprise de Schlüsselfeld fait gage d'envie de voyager et d'excellence du confort. Une cellule de stockage-Nesting hautement automatisée de HOMAG Group assure aujourd'hui l'efficacité et la qualité de la découpe.
Les « Best Agers » sont les personnes de 50 ans et plus, soucieuses de leur santé et de leur forme physique, mais qui jouissent également d'une certaine indépendance financière. Ils représentent plus de 90 % du groupe cible de MORELO Reisemobile, car ils ont souvent occupé des postes de direction tout au long de leur parcours professionnel et les transmettent désormais à la génération suivante. Leur nouvel objectif : découvrir l'Europe, voire un peu plus loin. Pour cela, ils peuvent choisir leur maison mobile parmi sept séries qui peuvent être personnalisées. Ils peuvent par exemple opter pour un « Home », un « Loft Liner » ou un « Palace ». Le choix s'étend jusqu'au « Grand Empire », le modèle de luxe de Schlüsselfeld.
Benchmark im Luxussegment
MORELO a été fondée en 2010 avec l'ambition de devenir le leader du marché dans le segment des camping-cars de luxe. « Depuis 2019, nous sommes une référence : pour la première fois, nous avons dépassé le précédent leader du marché quant au nombre de premières immatriculations. Aujourd'hui, nous produisons à peu près le double », explique le directeur Robert Crispens. L'objectif est de continuer à creuser cet écart : « Après avoir fabriqué 562 camping-cars de luxe l'année dernière, nous voulons en fabriquer plus de 600 cette année. »
Depuis 2011, MORELO fait partie du groupe Knaus Tabbert qui a réalisé un chiffre d'affaires de 1,4 milliard d'euros l'année dernière. L'entreprise de Schlüsselfeld y a contribué à hauteur de 160 millions d'euros. Pour perpétuer l'histoire du succès, MORELO accorde une attention particulière à la fabrication. Outre le volume de production, cela signifie tout d'abord développer l'intégration verticale pour bénéficier d'une indépendance maximale vis-à-vis des fournisseurs et être en mesure de réagir rapidement aux changements de circonstances. Pour cela, l'entreprise a récemment investi dans une salle des machines hautement performante comprenant un logiciel de gestion de la production (Controller MES).
Mais rien de tout cela ne serait possible sans les membres du personnel loyaux et investis :
le facteur humain est au premier plan chez MORELO et, comme indiqué sur leur page d'accueil, « Pas d'excellent camping-car sans une excellente équipe », c'est ainsi qu'ils le vivent. Daniel Medler, directeur commercial régional chez HOMAG, apprécie la relation de partenariat avec MORELO : une collaboration marquée par l'amitié, le respect mutuel, l'expertise professionnelle et l'égalité.
A la pointe de la technologie
Au cours des quatorze années qui ont suivi sa création, MORELO s'est réinventée à plusieurs reprises sur le plan technologique afin de placer la barre toujours plus haut en matière de production. L'entreprise a régulièrement réalisé d'importants investissements à cet effet. « L'année dernière, nous avons investi près de 11 millions d'euros. Cette année, ce sera 15 millions d'euros », indique M. Crispens en citant les derniers chiffres.
« Nous construisons actuellement une deuxième usine pour découpler nos lignes de production », poursuit le directeur général. « Les véhicules complexes de plus de 12 tonnes seront ainsi construits dans un nouveau hall. Il devrait en sortir environ 200 camping-cars par an ». Pour situer le contexte, MORELO travaille actuellement à une cadence de 3 h de production. A l'avenir, il est prévu que l'usine 1 tourne à 2 ou 2,5 h.
La nouvelle usine 2 doit démarrer à 11 h pour ensuite se stabiliser à 8 h. Afin de créer la capacité nécessaire pour la découpe, MORELO a réalisé le plus gros investissement de sa jeune histoire avec l'atelier de menuiserie, incluant la salle des machines et le parc des machines. « Pour la cellule de stockage-Nesting, nous avons opté pour HOMAG Group, car il est à la pointe de la technologie », explique M. Crispens. « Mais la prise de décision a aussi eu lieu en pensant à nos clients, auxquels nous présentons toujours notre production de manière transparente lors des visites guidées ».
Une production de véhicules cadencée
MORELO est un fabricant qui pense en matière de modules et qui répond aux souhaits individuels des clients dans ce cadre. Sur les sept modèles fabriqués, chacun possède jusqu'à dix plans auxquels s'ajoutent diverses options de construction spéciales. « Nous produisons délibérément un mélange de ces modèles. Et cela s'effectue en lot unitaire en fonction des commandes, les véhicules étant soumis à une production cadencée », explique Tobias Jäger, responsable de la production.
La production dans son ensemble est partiellement automatisée : par exemple, alors que la coupe est hautement automatisée, cette automatisation est sans cesse interrompue pour les étapes suivantes, comme l'assemblage des véhicules résultant des souhaits individuels des clients et du montage manuel. « Le montage s'effectue sur différentes stations dans un temps donné, les zones de préfabrication étant adaptées à cette cadence », explique M. Jäger. « Dans le même temps, le stockeur fournit à la chaîne de production les pièces détachées en fonction des véhicules individuels. » De grands degrés de liberté existent entre l'entrée et la sortie d'un véhicule afin de permettre aux différents corps de métiers de planifier le travail et d'intervenir en toute sécurité suivant la cadence.
Une planification et une production entièrement révisées
Avec la nouvelle cellule de découpe, composée de trois installations de Nesting et d'un stockeur à plat, MORELO n'a pas seulement ancré une technologie de pointe dans l'entreprise, mais a une fois de plus réinventé la stratégie et la logique de production : en commençant par le parc machines et le logiciel, le mode de planification et de production a été complètement remanié. Ainsi, à l'avenir, une seule commande regroupera plusieurs véhicules afin d'accroître l'efficacité, mais aussi le rendement des matériaux. Bien que le travail s'effectue déjà en partie de cette manière aujourd'hui, il y avait jusqu'à présent différentes dates de besoin et plusieurs véhicules étaient fabriqués ensemble selon une logique de bloc.
« A l'avenir, nous répartirons le travail en fonction des dates de besoin en travaillant individuellement ou en groupe », explique Eric Macke, ingénieur de projet chez MORELO. « Nous allons donc usiner une pièce de construction pile au moment où elle est nécessaire. Dans le même temps, cette décomposition en lot unique ou ce regroupement de différents éléments est aussi l'objectif global que nous poursuivons dans tous les autres processus ». Pour atteindre cet objectif, le facteur déterminant est le nouveau système de gestion de la production « ControllerMES » de HOMAG. Il assure l'efficacité et la transparence de la planification de la production, de la gestion et du suivi, de la reprise des données de commande jusqu'au contrôle de l'intégralité de la préparation de la commande.
La question cruciale
La deuxième ligne de production et l'augmentation prévue de la capacité constituent le point de départ de l'investissement dans la nouvelle cellule de découpe avec stockeur de panneaux automatisé. L'objectif est ainsi d'augmenter les chiffres de production, en particulier pour les grands camping-cars. La question était la suivante : quel concept permet d'augmenter le rendement de la préfabrication, notamment en découpe ? Deux installations de Nesting autonomes ont été remplacées. Jusqu'alors, elles découpaient avec une manutention conventionnelle et en partie manuelle des matériaux avec un personnel prévu à cet effet.
A l'avenir, les panneaux devraient pouvoir être manipulés de manière nettement plus efficace. « Bien qu'un ou deux décors en bois viendront bientôt s'y ajouter, la variance actuelle avec deux décors en bois résulte principalement de l'épaisseur des panneaux », explique M. Jäger. Mais surtout, souligne-t-il une fois de plus, la nouvelle cellule doit garantir la sécurité de la production et accroître l'efficacité : « Nous avons une grande part de pièces complexes, comme des pièces de forme libre. Les transporter de manière économique à travers la production est déterminant pour nos plans ambitieux. »
Stockage, Nesting et manutention hautement automatisés
La découpe, y compris le stockage, la manutention et la préparation des commandes, s'effectue aujourd'hui dans le cadre d'un processus hautement automatisé et nécessitant peu de personnel. Après la livraison, les panneaux de contreplaqué sont stockés dans des rayonnages cantilever pour être placés, si nécessaire, sur l'un des trois convoyeurs à rouleaux. Jusqu'à six piles peuvent être mises en tampon pour alimenter en toute sécurité un stockeur à plat « STORETEQ P-500 ». Après le transport jusqu'au stockeur, un ciseau de levage double assure la mise en stock automatique des panneaux. Pour une mise en stock anticipée, il est également possible de préparer des piles le soir, étant donné que l'entrée en stock s'effectue par type et qu'il n'y a donc pas de transfert. Comme le STORETEQ P-500 sert de stockeur pour l'ensemble de la production, il dispose de deux emplacements de stockage supplémentaires pour les piles prétraitées qui sont ensuite acheminées vers les étapes de traitement suivantes.
« La cellule de découpe fonctionne elle-même avec trois machines de Nesting couplées de la série CENTATEQ-N », rapporte Manuel Voland, chef de projet chez HOMAG. « Les commandes sont attribuées par ControllerMES à l'ensemble de l'installation, qui les répartit ensuite sur les différentes machines. Différentes priorités sont alors possibles. Cependant, c'est habituellement la première machine disponible qui est automatiquement sélectionnée pour un usinage en attente. »
Avant que les pièces ne soient usinées, les panneaux passent sur un convoyeur à rouleaux entraîné pour un étiquetage automatique. L'étiquetage automatique d'aujourd'hui permet de gagner du temps et d'éviter les erreurs. « Après l'étiquetage, le panneau est automatiquement inséré dans la machine Nesting, toutes les opérations de perçage, de fraisage et de rainurage sont effectuées, puis les pièces finies sont nettoyées et poussées sur une table de sortie. Enfin, elles sont automatiquement récupérées et évacuées par un chariot de transport transversal », poursuit Daniel Medler, directeur commercial régional chez HOMAG.
« Si un usinage sur les deux faces est requis, le panneau déjà usiné passe du transport transversal au stockeur via un retourneur de panneaux et entre à nouveau automatiquement dans un CENTATEQ N, où se déroulent les usinages restants et la séparation finale. » Actuellement, environ 75 % des panneaux sont concernés. En cas d'usinage sur une seule face, le panneau est transporté directement vers la sortie pour un retrait manuel. Pour que les trois CENTATEQ fonctionnent de manière aussi continue que possible, il existe différents postes tampons, par exemple au niveau de l'étiquetage ou devant le chariot de transport transversal.
Plusieurs postes de ce type sont également aménagés à la sortie, ce qui permet aux membres du personnel de retirer et de préparer facilement les matériaux à partir des différents Nests. « Tout ce qui vient de la cellule se termine en un seul point », souligne Tobias Jäger, responsable de production chez MORELO. « Outre la réduction des efforts de manutention, les trajets pour la préparation des commandes et le traitement ultérieur sont également plus courts. »
Augmentation systématique de la valeur ajoutée
La cellule de stockage-Nesting est en service chez MORELO depuis novembre dernier. Le remplacement de la production par les installations autonomes existantes a également été effectué. L'efficacité a considérablement augmenté, passant d'un taux d'utilisation de 60 à 80 %. « Actuellement, nous atteignons la capacité de quatre installations autonomes grâce à la cellule », estime M. Jäger. « En outre, les besoins en personnel ont considérablement diminué. »
Le constructeur de camping-cars dispose ainsi d'une installation qui garantit, sur la base de la qualité et de la sécurité des processus nécessaires, l'augmentation du nombre de pièces et l'optimisation des ressources. Bien entendu, les processus comme la logistique ou les applications logicielles continuent d'être améliorés. De plus, il serait possible d'agir sur des leviers, tels que le rapport débit/coupe, l'alignement constructif des pièces ou le modèle d'équipe. Il existe donc un important potentiel exploitable. Il s'agit notamment de rapatrier en interne des prestations de fabrication externalisées.
Mais surtout, avec ControllerMES, MORELO s'éloigne de plus en plus du principe du fraisage en blocs : la date de besoin devient le critère de commande central. « Cela nous permet d'être beaucoup plus rapides, d'empiler plus proprement les pièces pour le post-usinage et d'augmenter encore nos capacités de production », souligne M. Macke. Un grand levier, et non des moindres, est le regroupement en lots et le passage à la fabrication en série.
Avec les trois installations de Nesting, une croissance supplémentaire du rendement est déjà attendue. Les mois à venir nous diront exactement ce que nous pourrons atteindre. L'installation n'atteindra toutefois pas ses limites, le marché le prévoit déjà. Une chose est sûre : avec la cellule de stockage-Nesting, MORELO assure de manière fiable la croissance de la fabrication des camping-cars, et ce, dans le contexte d'une pyramide des âges en pleine évolution.
« Pour la cellule d'emmagasinage, nous avons choisi le groupe HOMAG parce qu'il est à la pointe de la technologie. »Robert Crispens, directeur général de MORELO
MORELO Camping-cars
MORELO est synonyme de camping-cars de première classe, qui comptent parmi les meilleurs du monde.
Mehr erfahren