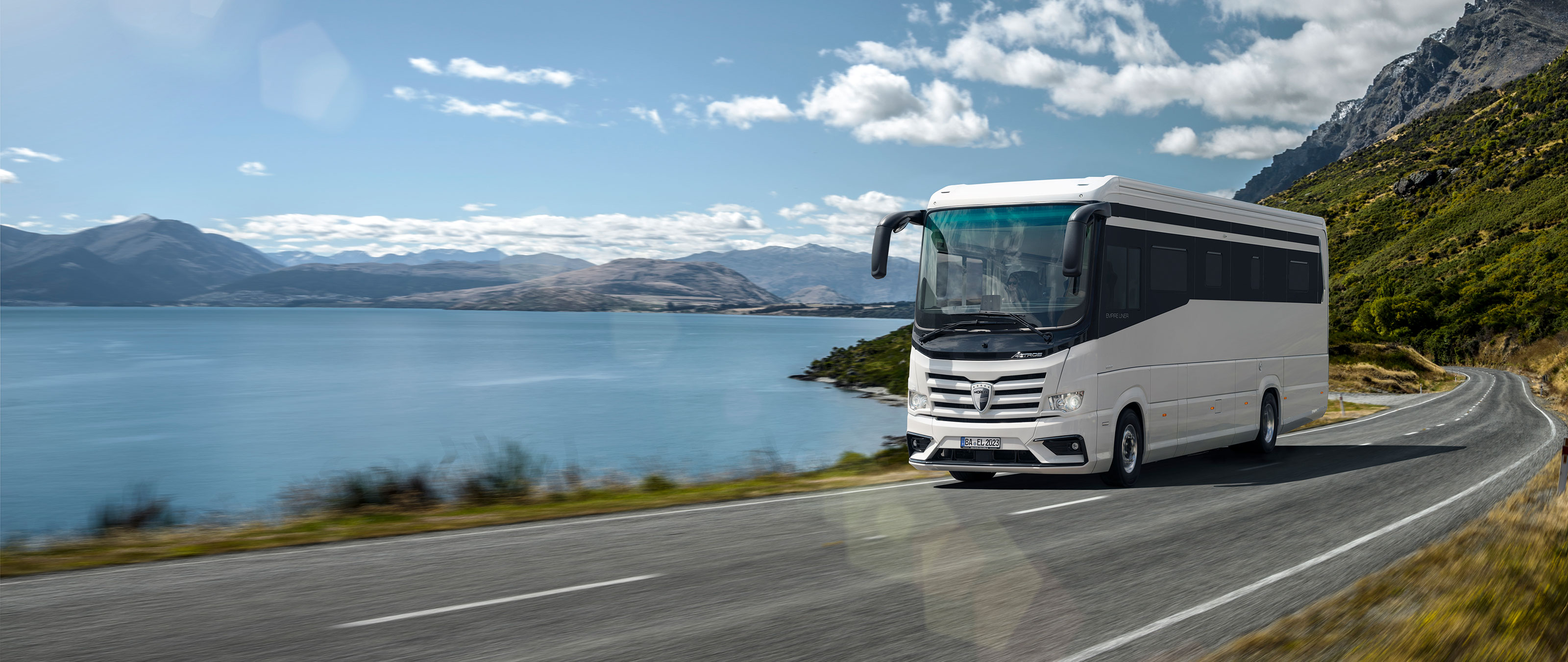
O nome MORELO é sinónimo de autocaravanas de primeira classe, mundialmente reconhecidas como a referência no segmento de luxo. Com elas, a empresa de Schlüsselfeld afirma-se pelo prazer de viajar e pelo excelente conforto. A célula de nesting de armazenamento altamente automatizada do Homag Group garante eficiência e qualidade no corte.
Os "Golden" ou "Best Agers" são pessoas com mais de 50 anos para as quais a saúde e a forma física são particularmente importantes, mas que também têm um certo grau de independência financeira. Mais de 90% destes "Golden Agers" pertencem ao grupo-alvo das autocaravanas MORELO, pois, muitas vezes, assumiram posições de liderança durante toda a vida profissional e estão agora a passar o testemunho à geração seguinte. As suas novas metas: conhecer a Europa. Talvez ir até um pouco mais além. Podem escolher a sua casa móvel ao seu gosto a partir de sete gamas de modelos, que também podem ser personalizadas. Por exemplo, podem optar por uma "Home", "Loft Liner" ou "Palace". A selecção estende-se até à "Grand Empire", a versão de luxo de Schlüsselfeld.
Referência no segmento de luxo
A MORELO foi fundada em 2010 com o objectivo de se tornar líder de mercado no segmento das autocaravanas de luxo. "Somos a referência desde 2019, ultrapassando pela primeira vez o antigo líder de mercado em termos de número de registos iniciais. Actualmente, produzimos cerca do dobro", afirma o director executivo Robert Crispens. O objectivo é aumentar ainda mais esta diferença: "Após a construção de 562 autocaravanas de luxo no ano passado, o nosso objectivo é ultrapassar as 600 este ano.
A MORELO faz parte do Grupo Knaus Tabbert desde 2011, que gerou um volume de negócios de 1,4 mil milhões de euros no ano passado. A empresa de Schlüsselfeld contribuiu com 160 milhões de euros para este valor. A MORELO acredita que o seu método de produção é crucial para dar continuidade à sua história de sucesso. Para além da escala de produção, tal significa, antes de mais, alargar ainda mais a capacidade de produção interna, de modo a tornar-se o mais independente possível dos fornecedores e ser capaz de reagir rapidamente à evolução das circunstâncias. Para o efeito, a empresa investiu recentemente numa sala de máquinas de alto desempenho, incluindo o software de controlo da produção (Controller MES).
No entanto, nada disto seria possível sem os seus fiéis e enérgicos funcionários.
O factor humano está em primeiro plano na MORELO e, como escrevem na página inicial, "Só é possível construir autocaravanas excelentes com uma equipa excelente". Esse é o seu lema. Daniel Medler, gestor de vendas regional da HOMAG, valoriza a relação de parceria com a MORELO, que se caracteriza pela amizade, mas que é vivida com todo o respeito, profissionalismo e em pé de igualdade.
Estado da arte
Em termos de tecnologia, nos catorze anos desde a sua criação, a MORELO reinventou-se várias vezes para continuar a elevar a fasquia do fabrico. A empresa investe regularmente de forma significativa neste domínio. "No ano passado, investimos cerca de 11 milhões de euros, este ano serão 15 milhões", afirma Crispens, citando os números mais recentes.
"Estamos actualmente a construir uma segunda fábrica para dissociar as nossas linhas de produção", prossegue o director executivo. "Os veículos complexos com mais de 12 toneladas serão então construídos numa nova oficina. O objectivo é produzir cerca de 200 autocaravanas por ano." No contexto actual, a MORELO produz num ciclo de 3 horas. A intenção é que, no futuro, a fábrica 1 funcione num ciclo de 2 ou 2,5 horas.
A nova fábrica 2 deverá começar nas 11 horas e estabilizar posteriormente nas 8 horas. Para obter a capacidade de corte necessária, a MORELO efectuou o seu maior investimento dos últimos tempos em carpintaria, que incluiu tanto a sala de máquinas como a maquinaria. "Decidimos recorrer ao Homag Group para a aquisição da célula de nesting de armazenamento porque é a mais moderna em termos tecnológicos", explica Crispens. "No entanto, a decisão também foi tomada a pensar nos nossos clientes, a quem, através de visitas guiadas, somos sempre o mais transparentes no que respeita à nossa produção."
Produção de veículos sincronizada
A MORELO é um fabricante que pensa em termos de sistemas modulares e que responde às necessidades individuais dos clientes neste contexto. Dos sete modelos fabricados, cada um tem até dez disposições, para além de várias opções de personalização. "Produzimos deliberadamente uma mistura destes modelos. Isto é feito em função da encomenda em lotes de tamanho 1, em que os veículos passam por um processo de produção sincronizado", explica o director de produção Tobias Jäger.
A produção como um todo é parcialmente automatizada: enquanto o processo de corte, por exemplo, é altamente automatizado, esta automatização é repetidamente interrompida para os passos subsequentes, como a montagem dos veículos, que resulta obrigatoriamente dos requisitos individuais dos clientes e da montagem manual. "A montagem é realizada nas várias estações num período de tempo especificado e as áreas de pré-fabricação são adaptadas a este tempo de ciclo", afirma Jäger. "Ao mesmo tempo, o armazém – subdividido para o veículo individual – fornece a configuração do ciclo para a linha de montagem." Existe um elevado grau de liberdade entre a entrada e a saída de um veículo, para que as várias operações possam ser planeadas e implementadas com segurança no ciclo.
Planeamento e produção totalmente revistos
Com a nova célula de corte, composta por três sistemas de nesting e uma plataforma de armazenamento, a MORELO não só consolidou a tecnologia de ponta na empresa, como também reinventou a sua estratégia e lógica de produção: começando pela maquinaria e pelo software, o tipo de planeamento e de produção foi totalmente revisto. Assim, no futuro, vários veículos serão agrupados numa única ordem de produção, a fim de aumentar a eficiência e o rendimento dos materiais. Em certa medida, isto já acontece actualmente, mas até agora havia diferentes datas de necessidade e vários veículos eram produzidos agrupados de acordo com uma mentalidade de bloco.
"No futuro, pretendemos dividir o trabalho de acordo com a data de necessidade, trabalhando individualmente ou em grupo", explica Eric Macke, engenheiro de projectos da MORELO. "Assim, fresamos um componente exactamente na data em que é necessário. Ao mesmo tempo, esta divisão em lotes individuais ou o agrupamento de diferentes itens é também o objectivo principal que procuramos em todos os outros processos." O novo sistema de controlo de produção "ControllerMES" da Homag, que garante eficiência e transparência no planeamento da produção, no comando e na monitorização, desde a transferência de dados da tarefa até ao controlo da integridade na preparação de encomendas, é crucial para a sua implementação bem-sucedida.
A questão decisiva
O ponto de partida para o investimento na nova célula de corte e no armazém de placas automático foi a segunda linha de produção e o aumento planeado da capacidade. O objectivo era aumentar os números de produção, especialmente no que respeita às grandes autocaravanas. A questão que se impunha era: qual o conceito exacto a utilizar para aumentar a produção no pré-fabrico, especialmente no corte? Era necessário substituir dois sistemas de nesting autónomos, que até então utilizavam o manuseamento convencional e parcialmente manual de materiais e a correspondente mão de obra para o corte.
No futuro, os materiais das placas deveriam ser manuseados de forma muito mais eficiente. "Embora um ou dois revestimentos de madeira venham a ser adicionados em breve, a variação – nos actuais dois revestimentos de madeira – deve-se principalmente à espessura das placas", explica Jäger. No entanto, acima de tudo – sublinha uma vez mais – a nova célula visa garantir a segurança da produção e aumentar a eficiência: "Temos uma grande proporção de peças complexas, como peças de forma livre. Integrá-las economicamente na produção é crucial para os nossos planos ambiciosos."
Armazenamento, nesting e manuseamento altamente automatizados
O corte, incluindo o armazenamento, o manuseamento e a preparação, é agora efectuado num processo altamente automatizado e com pouca intervenção humana. Após a entrega, as placas de contraplacado são armazenadas em estantes cantiléver para serem colocadas num dos três transportadores de rolos, conforme necessário. Aqui, é possível armazenar até seis pilhas para a alimentação segura de uma plataforma de armazenamento "STORETEQ P-500". Após o transporte para o armazém, uma tesoura de elevação dupla assume o armazenamento automático das placas. As pilhas também podem ser preparadas à noite para um armazenamento previsível, uma vez que são armazenadas por tipo e, por conseguinte, não precisam de ser re-armazenadas. Como a STORETEQ P-500 também funciona como um armazém para toda a produção, possui dois locais de desarmazenamento adicionais para pilhas pré-preparadas, que são depois enviadas para os processos subsequentes.
"A célula de corte propriamente dita funciona com três máquinas de nesting de operação contínua acopladas da série CENTATEQ-N", comenta Manuel Voland, gestor de projectos da Homag. "As tarefas são atribuídas a todo o sistema através do ControllerMES, que depois as distribui pelas máquinas individuais. Assim sendo, é possível atribuir diferentes prioridades. No entanto, por norma, a primeira máquina disponível é automaticamente seleccionada para o processamento pendente."
Antes do nesting das peças em operação contínua, as placas passam por um transportador de rolos accionado para etiquetagem automática. Actualmente, a etiquetagem automática poupa tempo e evita erros. "Após a etiquetagem, a placa é automaticamente introduzida na máquina de nesting, todas as operações de perfuração, fresagem e de processamento de abertura de ranhuras são efectuadas e, em seguida, as peças acabadas são limpas e empurradas para uma mesa de saída. Por fim, são automaticamente recolhidas e removidas através de um carro de transporte transversal", prossegue Daniel Medler, gestor de vendas regional da HOMAG.
"Se for necessário o processamento de ambos os lados, a placa já processada sai do transporte transversal através de um virador de placas de volta para o armazém de placas e automaticamente de novo para um CENTATEQ N, onde é efectuado o processamento restante e a divisão final". Isto afecta actualmente cerca de 75% das placas. No caso do processamento de um lado, o nest é transportado directamente para a saída na remoção manual. Para garantir que os três CENTATEQ estão em funcionamento o mais continuamente possível, existem vários locais de acumulação, por exemplo, na etiquetagem ou à frente do carro de transporte transversal.
Também foram configurados vários locais deste tipo na saída, para que os funcionários possam retirar convenientemente o material dos vários nests e preparar. "Isto significa que tudo o que provém da célula termina agora num único ponto", sublinha Tobias Jäger, director de produção da MORELO. "Para além da redução do esforço de manuseamento, as distâncias para a preparação e o processamento subsequente são correspondentemente curtas."
Aumentar sistematicamente o valor acrescentado
A célula de nesting de armazenamento está em funcionamento na MORELO desde novembro do ano passado. A substituição da produção pelos antigos sistemas autónomos também foi implementada. Com uma taxa de utilização que passou de 60% para 80%, o salto de eficiência é evidente. "Com a célula, atingimos a capacidade de quatro sistemas autónomos", calcula Jäger. "Além disso, a necessidade de mão-de-obra diminuiu significativamente."
Isto proporciona ao fabricante de autocaravanas um sistema que, com base na qualidade e fiabilidade necessárias do processo, garante um aumento do volume de produção, juntamente com a optimização dos recursos. Certamente, processos como a logística e as aplicações de software serão continuamente optimizados. Para além disso, poderiam ser feitos ajustes no rácio produção/desperdício, no alinhamento estrutural das peças ou no modelo de turnos. Por conseguinte, há ainda um potencial considerável por explorar. Tal inclui também a reintegração na empresa de serviços de produção externos.
No entanto, acima de tudo, com o ControllerMES, a MORELO afasta-se cada vez mais do princípio da fresagem em blocos de produção: a data de necessidade passa a ser o critério de controlo central. "Isto torna-nos muito mais rápidos, permite-nos desempilhar as peças de forma mais organizada para processamento posterior e aumenta ainda mais a produção", salienta Macke. Por último, mas não menos importante, o agrupamento dos lotes e a passagem à produção em série é um factor significativo.
Com os três sistemas de nesting, já foi considerado um aumento adicional do rendimento. Os próximos meses mostrarão exactamente o que é possível alcançar. No entanto, o sistema não atingirá o seu limite, como o mercado já indica. Assim, uma coisa é certa: com a célula de nesting de armazenamento, a MORELO assegura de forma fiável o crescimento da construção de autocaravanas. E isto no contexto de uma pirâmide etária em mudança.
Edição de agosto de 2024 Edição de agosto de 2024
«Decidimo-nos pelo Grupo HOMAG para a célula de encaixe de armazenamento, porque é a mais moderna.»Robert Crispens, Diretor Executivo MORELO
Autocaravanas MORELO
MORELO é sinónimo de autocaravanas de primeira classe, entre as melhores do mundo.
Mehr erfahren