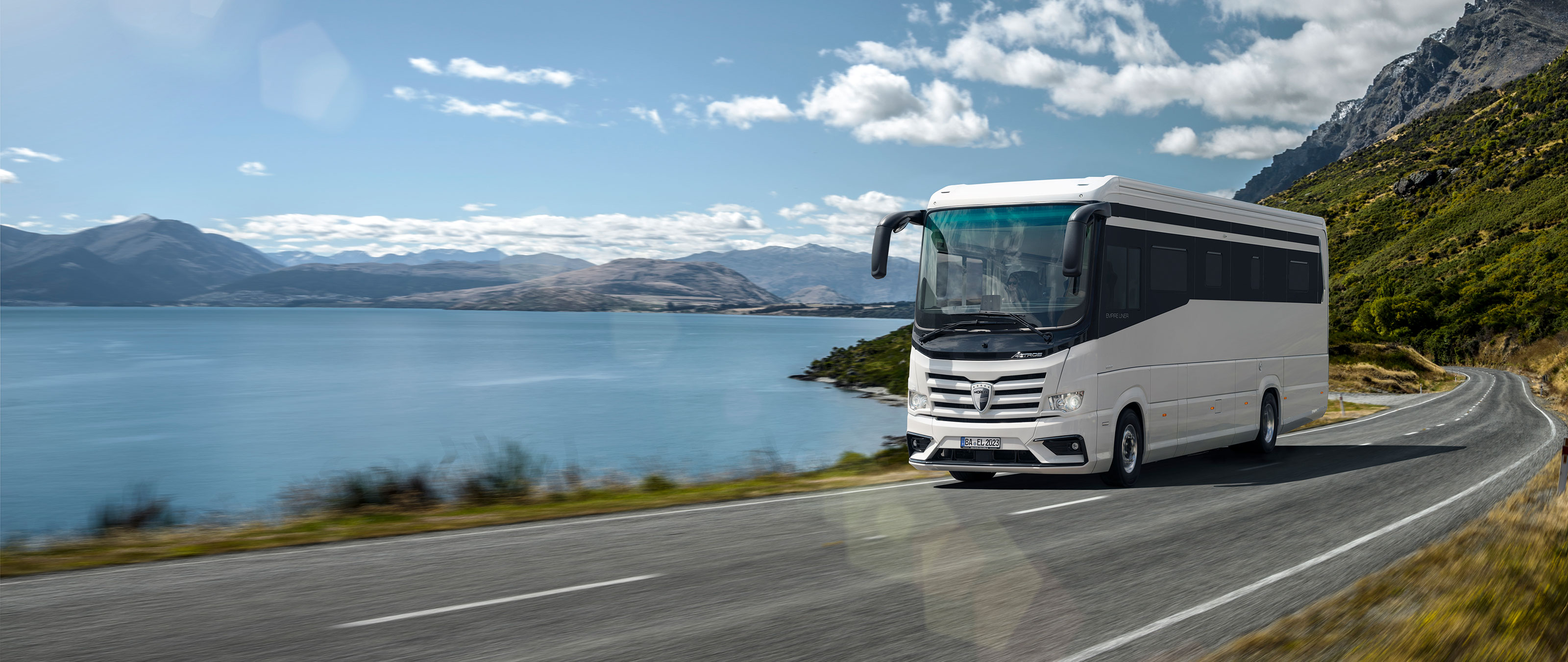
Il nome MORELO è sinonimo di camper di altissima qualità e rappresenta un benchmark mondiale nel segmento del lusso. Con questi veicoli, l'azienda di Schlüsselfeld promuove una filosofia all'insegna della passione per i viaggi e del massimo comfort. Per garantire efficienza e qualità nella sezionatura, è stata inserita un'isola di nesting-magazzino altamente automatizzata di Homag Group.
I cosiddetti "Golden" o "Best Ager" sono le persone over 50 che prestano particolare attenzione alla salute e alla forma fisica, e possono contare su una buona indipendenza finanziaria. I Golden Ager rappresentano oltre il 90% del target di MORELO Reisemobile. Queste persone hanno spesso lavorato per tutta la vita in posizioni di leadership e ora trasmettono il know-how alla generazione successiva. Il loro nuovo obiettivo è scoprire tutta l'Europa. E magari spingersi anche un po' più in là. Possono scegliere il camper che desiderano tra sette diverse serie, tutte personalizzabili. Possono optare, ad esempio, per un "Home", un "Loft Liner" o un "Palace", o anche per un "Grand Empire", il modello di lusso di Schlüsselfeld.
Il benchmark nel segmento del lusso
MORELO è stata fondata nel 2010 con l'obiettivo di diventare leader di mercato nel segmento del lusso dei camper. "Dal 2019, quando abbiamo superato per la prima volta il precedente leader di mercato per numero di immatricolazioni, siamo diventati il benchmark. E oggi i nostri numeri sono quasi raddoppiati", racconta l'amministratore delegato Robert Crispens. L'azienda punta ad aumentare ulteriormente questo margine: "Dopo aver costruito 562 camper di lusso l'anno scorso, quest'anno supereremo i 600 pezzi.
Dal 2011 MORELO fa parte del gruppo Knaus Tabbert, che lo scorso anno ha registrato un fatturato di 1,4 miliardi di euro, 160 milioni dei quali provengono da Schlüsselfeld. Per continuare a scrivere la sua storia di successo, MORELO considera fondamentale il metodo di produzione. Oltre a un incremento della capacità produttiva, il suo obiettivo principale è aumentare anche la profondità di produzione, per ridurre al minimo la dipendenza dai fornitori e rispondere rapidamente ai cambiamenti del mercato. Recentemente sono stati fatti investimenti in una sala macchine ad alte prestazioni, che include anche un software per la gestione della produzione (Controller MES).
Tutto ciò però non sarebbe possibile senza dipendenti fedeli e dinamici.
Il fattore umano gioca un ruolo chiave in MORELO. Sul loro sito vi è l'affermazione "Senza un team eccellente non vi sarebbe alcun camper eccellente", e questo principio è parte integrante del loro modo di lavorare. Daniel Medler, responsabile vendite territoriali di HOMAG, tiene in grande considerazione la collaborazione con MORELO, contraddistinta da un'atmosfera amichevole e fondata su rispetto, professionalità e parità.
State of the art
Dalla sua fondazione, avvenuta quattordici anni fa, MORELO ha saputo reinventarsi più volte sul fronte tecnologico, portando gli standard produttivi a un livello sempre superiore. L'azienda ha fatto regolarmente ingenti investimenti per raggiungere questi obiettivi. "L'anno scorso abbiamo investito quasi 11 milioni di euro e quest'anno arriveremo a 15 milioni", spiega Crispens, condividendo i dati più recenti.
"Attualmente stiamo costruendo un secondo stabilimento per separare le nostre linee di produzione", aggiunge l'amministratore delegato. "I veicoli complessi oltre le 12 tonnellate saranno poi assemblati in un nuovo capannone. Dovrebbe trattarsi di circa 200 camper all'anno". MORELO attualmente opera con un ciclo programmato di 3 ore, che, nello stabilimento 1, prevede di ridurre a 2 o 2,5 ore in futuro.
Il nuovo stabilimento 2 inizierà con un ciclo di 11 ore, per poi stabilizzarsi su 8 ore. Per aumentare la capacità di taglio, MORELO ha recentemente effettuato il suo più ingente investimento in falegnameria, comprendente il potenziamento sia della sala macchine sia del parco macchine. "Per la nostra isola di nesting-magazzino, abbiamo scelto Homag Group perché dispone della tecnologia più avanzata", spiega Crispens. "Abbiamo preso questa decisione tenendo in considerazione anche i nostri clienti, ai quali vogliamo garantire una trasparenza continua riguardo ai nostri processi produttivi".
Produzione di veicoli con cicli programmati
MORELO adotta un approccio modulare per soddisfare le esigenze individuali dei clienti. I sette modelli costruiti vantano fino a dieci configurazioni possibili ciascuno, oltre a varie opzioni personalizzate. "Produciamo consapevolmente un mix di questi modelli su ordinazione in lotto 1, e i veicoli attraversano un processo di produzione con cicli programmati", spiega Tobias Jäger, direttore di produzione.
La produzione nel suo complesso è parzialmente automatizzata: mentre la fase di sezionatura è altamente automatizzata, l'automazione viene interrotta nelle fasi successive, come quella di assemblaggio dei veicoli, per via delle richieste personalizzate dei clienti e della necessità di un montaggio manuale. "Il montaggio viene eseguito nelle varie stazioni entro un tempo prestabilito, e le aree di prefabbricazione sono adattate a questo tempo ciclo", spiega Jäger. "Al contempo, il magazzino, suddiviso sul singolo veicolo, fornisce i componenti necessari per ogni ciclo direttamente al nastro". Tra l'ingresso e l'uscita di ogni veicolo c'è un ampio grado di libertà, il che consente di programmare e inserire in modo sicuro le varie lavorazioni nel ciclo.
Pianificazione e produzione completamente riviste
Con la nuova isola di sezionatura, composta da tre impianti di nesting più magazzino orizzontale, MORELO, oltre ad aver integrato la tecnologia all'avanguardia, ha reinventato ancora una volta la strategia e la logica di produzione: iniziando dal parco macchine e dal software, il tipo di progettazione e produzione è stato completamente rivisto. In futuro, più veicoli verranno raggruppati in un'unica richiesta di produzione per aumentare l'efficienza e la resa dei materiali. In parte questo approccio viene utilizzato già oggi, anche se finora erano previste diverse date di richiesta e i veicoli venivano prodotti in blocchi.
"In futuro, intendiamo suddividere la produzione in base alle date della richiesta, lavorando su singoli veicoli o su gruppi", spiega Eric Macke, ingegnere di progetto presso MORELO. "In questo modo, freseremo i componenti solo quando servono. Allo stesso tempo, questa possibilità di lavorare su singoli lotti o su lotti raggruppati rappresenta l'obiettivo principale che perseguiamo in tutti i processi produttivi". Il nuovo sistema di controllo della produzione "ControllerMES" di Homag, che garantisce efficienza e trasparenza nella pianificazione della produzione, nel controllo e nel monitoraggio, dalla ricezione dei dati dell'ordine al controllo di completezza nella preparazione degli ordini è fondamentale per il successo del commissionamento.
La domanda cruciale
Il punto di partenza per l'investimento nella nuova isola di sezionatura con magazzino pannelli automatizzato era quindi la seconda linea di produzione e l'aumento della capacità programmato. In particolare, si intende aumentare la produzione di grandi camper. La domanda era: quale soluzione può essere adottata per aumentare la produzione nella prefabbricazione, in particolare nella sezionatura? Era necessario sostituire due impianti di nesting stand-alone, che fino ad allora avevano utilizzato una movimentazione dei materiali tradizionale, in parte manuale, e un corrispondente impiego di personale per il taglio.
In futuro, i materiali dei pannelli dovrebbero essere gestiti in modo molto più efficiente. "Anche se presto verranno aggiunte una o due nuove finiture in legno, la variazione, attualmente con due finiture in legno, deriva principalmente dallo spessore dei pannelli", spiega Jäger. Soprattutto, però, sottolinea ancora una volta, la nuova isola è destinata a garantire la sicurezza della produzione e ad aumentare l'efficienza: “Molti dei pezzi sono complessi, come quelli di forma libera. Una produzione economicamente efficiente è fondamentale per realizzare i nostri ambiziosi piani”.
Immagazzinamento altamente automatizzato, nesting, movimentazione
La sezionatura, compresi l'immagazzinamento, la movimentazione e il commissionamento, avviene oggi in un processo altamente automatizzato non presidiato. Dopo la consegna, i pannelli in compensato vengono immagazzinati in scaffalature a sbalzo per essere collocati su uno dei tre trasportatori a rulli, se necessario. È possibile inserire fino a sei cataste per l'alimentazione sicura di un magazzino orizzontale "STORETEQ P-500". Dopo il convogliamento al magazzino, una doppia cesoia consente l'immagazzinamento automatico dei pannelli. Per un immagazzinamento preventivo, è anche possibile predisporre cataste già la sera, poiché vengono immagazzinate per tipologia e non devono quindi essere riorganizzate. Poiché lo STORETEQ P-500 funge anche da magazzino per l'intera produzione, è dotato di altre due posizioni di prelievo per le cataste precommissionate, che poi passano alle lavorazioni successive.
"L'isola di sezionatura stessa utilizza tre macchine di nesting in continuo accoppiate della serie CENTATEQ-N", spiega Manuel Voland, Responsabile di progetto di Homag. "Gli ordini vengono assegnati tramite ControllerMES all'intero impianto, che li distribuisce poi sulle singole macchine. In questo caso sono possibili diverse priorità. Di norma, tuttavia, per ogni lavorazione da effettuare, viene selezionata automaticamente la prima macchina disponibile".
Prima di eseguire il nesting dei pezzi in esercizio continuo, i pannelli scorrono su un trasportatore a rulli motorizzato per l'etichettatura automatica. Oggi, l'etichettatura automatica consente di risparmiare tempo e di evitare errori. "Dopo l'etichettatura, il pannello viene inserito automaticamente nella macchina per nesting, dove vengono eseguite tutte le operazioni di foratura, fresatura e scanalatura, poi i pezzi finiti vengono puliti e trasferiti su un tavolo di uscita. Infine, vengono prelevati e trasportati automaticamente da un carrello di trasporto trasversale", prosegue Daniel Medler, responsabile vendite territoriali di HOMAG.
"Se è richiesta una lavorazione su entrambi i lati, il pannello già lavorato dal trasporto trasversale passa attraverso un ribaltatore pannelli, torna nel magazzino pannelli e poi automaticamente di nuovo in una macchina CENTATEQ N, per completare le lavorazioni e l'ultima suddivisione. "Attualmente questo interessa circa il 75% dei pannelli. In caso di lavorazione su un lato, il nest viene trasportato direttamente all'uscita nel prelievo manuale. Per mantenere le tre macchine CENTATEQ il più a lungo possibile in esercizio, ci sono diverse posizioni di magazzino intermedio, ad esempio nell'etichettatura o prima del carrello di traslazione trasversale.
Anche al momento dell'uscita sono presenti diverse posizioni, in modo tale che i dipendenti possano prelevare e smistare comodamente il materiale dai diversi nest. "In questo modo, tutto ciò che arriva dall'isola finisce in un unico punto", sottolinea Tobias Jäger, direttore di produzione di MORELO. "Oltre a ridurre i costi di movimentazione, abbrevia anche i percorsi necessari per il commissionamento e le lavorazioni successive".
Incremento sistematico del valore aggiunto
Da novembre dello scorso anno, MORELO ha introdotto l'isola di nesting-magazzino. Inoltre, è stata implementata la sostituzione della produzione dei precedenti impianti stand-alone. Con un grado di utilizzo che va dal 60% all'80%, il tasso di efficienza è nettamente migliorato. "Attualmente, con l'isola siamo in grado di ottenere la stessa capacità di produzione di quattro impianti stand-alone", afferma Jäger. "Inoltre, il fabbisogno di personale è diminuito in modo significativo".
In questo modo il produttore di camper MORELO ha a disposizione un impianto che, in base alla qualità e alla sicurezza dei processi necessari, garantisce l'aumento del numero di pezzi e l'ottimizzazione delle risorse. Naturalmente, processi come la logistica o le applicazioni software vengono ulteriormente ottimizzati. Inoltre, possono essere perfezionati alcuni aspetti, come il rapporto tra produttività e scarto, l'allineamento strutturale dei pezzi e il modello di turnazione. C'è quindi un ampio margine di miglioramento ancora da sfruttare, compreso il rientro in azienda di volumi di produzione esternalizzati.
Soprattutto, però, con ControllerMES, MORELO sta gradualmente abbandonando il principio della fresatura in blocchi di produzione: il criterio principale ora è la data della richiesta. "Questo significa che siamo molto più veloci, possiamo accatastare i pezzi in modo più pulito per le lavorazioni successive e aumentare ulteriormente la produttività", sottolinea Macke. Un fattore chiave è rappresentato dalla possibilità di raggruppare i lotti per la produzione in serie.
I tre impianti di nesting sono stati pensati proprio per consentire un'ulteriore crescita della produttività. Nei prossimi mesi si vedrà esattamente ciò che si può ottenere, anche se la capacità dell'impianto non raggiungerà il suo limite, come il mercato già suggerisce. Non resta quindi che constatare che MORELO con l'isola di sezionatura-magazzino si assicura in modo affidabile la crescita nella produzione di camper, rispondendo anche a una popolazione in evoluzione.
Edizione agosto 2024 Edizione agosto 2024
«Per la cella di stoccaggio abbiamo scelto il gruppo HOMAG, perché è all'avanguardia.»Robert Crispens, Amministratore delegato MORELO