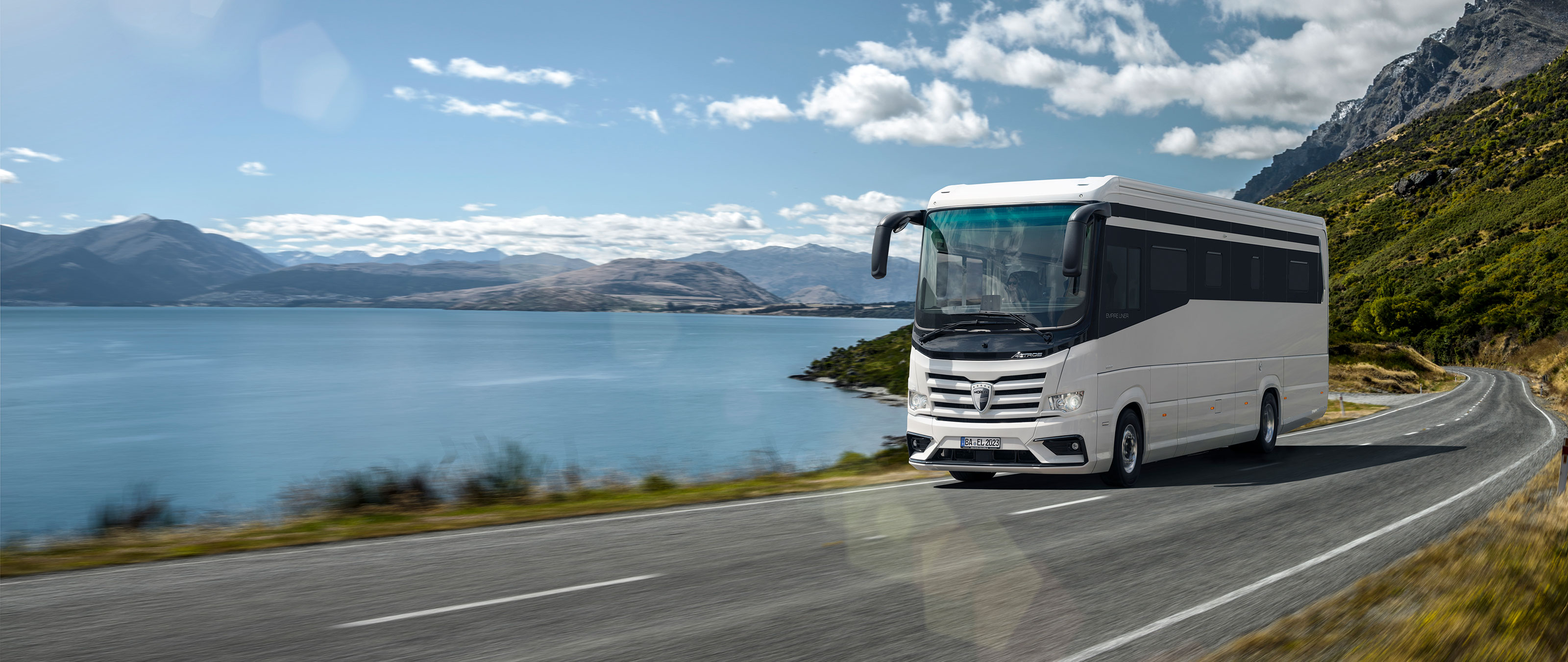
The name MORELO represents first-class motorhomes, which are globally regarded as the benchmark in this luxury segment. The motorhomes manufactured by the Schlüsselfeld-based company are the epitome of comfort and demonstrate a real passion for travel. Today, a highly automated storage-nesting cell from the HOMAG Group ensures efficiency and quality in cutting processes.
"Golden-agers" and "best agers" refer to people aged 50 and over who are particularly keen to look after their health and physical fitness, but who also have a certain level of financial independence. These golden agers make up more than 90% of the target market of MORELO Reisemobile — they have often worked in managerial positions throughout their professional lives and are now passing these duties on to the next generation. Their new goal is to explore Europe, and perhaps even a bit further afield. They can pick their perfect mobile home from seven different models, all of which can be customized further. Their options include the "Home," "Loft Liner" and "Palace" models. The range extends all the way up to the "Grand Empire," the most luxurious model the company produces.
Benchmark in the luxury segment
MORELO was founded in 2010 with the aim of becoming the market leader in the luxury segment of motorhomes. "We have been the benchmark since 2019, when for the first time we overtook the then market leader in terms of first registrations. Now we are producing about twice that," reports Managing Director Robert Crispens. The company aims to increase this number further still: "After building 562 luxury motorhomes last year, this year we plan to build over 600."
Since 2011, MORELO has been part of the Knaus Tabbert Group, which generated sales of 1.4 billion euro last year. MORELO contributed 160 million euro to this figure. MORELO believes that the method of production is crucial for continuing its success story. In addition to the scope of production, this means first and foremost expanding the depth of production in order to become suppliers that are as independent as possible and to be able to react quickly to changing circumstances. For this purpose, investments have recently been made in a high-performance machine hall, including production control system software (Controller MES).
However, all of this would not be possible without loyal and hard-working employees.
The human factor is important to MORELO — their website says "an excellent motorhome cannot be created without an excellent team" and this is something the company truly believes in. Daniel Medler, Regional Sales Manager at HOMAG, appreciates the company's partnership with MORELO as the two businesses have a friendly yet respectful and professional relationship and treat each other as equals.
State of the art
In the fourteen years since its founding, MORELO has reinvented itself technologically in order to raise the bar in production ever higher. The company has regularly invested heavily in this area. "Last year we invested almost 11 million euro, this year it will be 15 million euro," says Crispens, citing the latest figures.
"We are currently building a second plant to decouple our production lines," continues the Managing Director. "Complex vehicles weighing over 12 t will then be built in a new hall. This should amount to around 200 motorhomes per year." The backdrop to this is that MORELO currently has a
production cycle time of 3 hours. The intention is for plant 1 to operate on a 2 or 2.5 hour cycle in the future.
The new plant 2 will initially have an 11 hour cycle, which will eventually be reduced to 8 hours. In order to create the necessary capacity in the cutting process, MORELO made the largest investment in its recent history in the joinery, which included investing in both the machine hall and the machine pool. "We chose a storage-nesting cell from the HOMAG Group because it is state of the art," explains Crispens. "However, the decision was also made with our customers in mind, who we take on guided tours so that they have a clear understanding of our production process."
Cycled vehicle production
MORELO is a manufacturer that thinks in modular designs and uses these to meet individual customer requirements. Each of the seven models built has up to ten layout plans, as well as various special construction options. "We deliberately manufacture a mix of these models. And this is done on an order-related basis in batch size 1, with the vehicles going through cycled production," explains Production Manager Tobias Jäger.
The production process is partially automated: While the cutting process, for example, has a high degree of automation, this automation is not present in subsequent steps such as the assembly of the vehicles — this lack of automation is necessary due to the individual customer requirements and manual assembly process. "Assembly is carried out within a predetermined time at the various stations and the supplying prefabrication areas are adapted to this cycle time," said Jäger. "At the same time, the storage system delivers the equipment for the cycle—broken down by individual vehicle—to the production line." There is a large degree of freedom between a vehicle entering and exiting the production line, allowing the wide variety of tasks to be easily planned into the cycle and implemented.
Complete overhaul of planning and production
With the new cutting cell, which consists of three nesting systems and a storage system, MORELO has not only incorporated state-of-the-art technology in the company, but also reinvented their production strategy and logic once again: Starting with the machine pool and software, the planning and production method has been completely overhauled. In future, several vehicles will be combined in one production order to increase both efficiency and material yield. The company is already partially working in this way, but until now various due dates and multiple vehicles have been combined into one production block.
"In the future, we want to split up production according to the due date, and we want to be able to work on either one vehicle at a time or multiple vehicles at once," explains Eric Macke, Project Engineer at MORELO. "Then we will be able to rout a component for the exact date when it is needed. At the same time, this ability to split production up into individual vehicles or to combine different vehicles together also forms the overarching goal that we are pursuing in all our other processes." The new "ControllerMES" production control system from HOMAG is crucial for implementing this successfully. It ensures efficiency and transparency in production planning, control and monitoring — from transferring order data to checking for completeness in picking.
The crucial question
The new cutting cell and automated panel storage was therefore firstly invested into the second production line and the corresponding capacity expansion. The aim of this is to increase production figures, particularly for large motorhomes. The question was: Which concept would increase output in prefabrication, in particular in the cutting process? Two stand-alone nesting systems were to be replaced, which until then had been working together with a conventional, partially manual material handling process and the corresponding personnel.
In the future, it should be possible to handle panel materials much more efficiently. "Although one or two more decorative wood finishes will soon be added, the variation—with just two wood finishes at the moment—primarily comes from the thickness of the panels," says Jäger. However, he points out once again that, above all, the new cell was designed to ensure production reliability and increase efficiency: "We have a large proportion of complex parts, such as free-formed workpieces. Being able to produce these parts in an economical way is crucial to our ambitious plans."
Highly automated storage, nesting and handling
The cutting process, including storage, handling and picking, is now carried out in a highly automated way with minimal personnel. After delivery, the plywood panels are stored in cantilever racks, ready to be placed on one of three roller conveyors when needed. Up to six stacks can be kept here in order to reliably supply a STORETEQ P-500 storage system. After being transported to the storage system, a double scissor lift takes over the automatic storage of the panels. It is also possible to prepare stacks the evening before storage, as items are stored by type and do not require subsequent repositioning. Because the STORETEQ P-500 also functions as a storage system for the entire production process, it has two additional storage removal positions for pre-picked stacks, which are then moved onto subsequent processing steps.
"The cutting cell itself works with three coupled throughfeed nesting machines from the CENTATEQ N-series," explains Manuel Voland, Project Manager at HOMAG. "Orders are assigned to the entire system via ControllerMES, which then distributes them to the individual machines. It is possible to set different priorities here. However, the first available machine is usually selected automatically for an upcoming processing step."
Before the parts are nested during throughfeed, the panels are transported over a driven roller conveyor for automatic labeling. The fact that automatic labeling is now being used saves time and prevents errors. "After labeling, the panel is automatically fed into the nesting machine, all drilling, routing and grooving steps are carried out, then the finished workpieces are cleaned and pushed onto an outfeed table. Finally they are automatically picked up and transported out by a cross transport carriage," continues Daniel Medler, Regional Sales Manager at HOMAG.
"If both sides need to be processed, the panel that has already been processed is moved from the cross transport carriage via a panel turner, then returned to the panel storage system and automatically fed back into a CENTATEQ N-series CNC machine, where the remaining processing steps and the final cutting process take place." Currently, this is carried out on around 75% of the panels. If only one side needs to be processed, the nest is transported straight to the outfeed for manual removal. To ensure that the three CENTATEQs operate as continuously as possible, there are different buffer positions available, for example at the labeling step or upstream of the cross transport carriage.
Several such positions are also set up at the outfeed, allowing employees to conveniently remove and pick materials from the various nests. "This means that everything that comes from the cell now ends at a single point," highlights Tobias Jäger, Production Manager at MORELO. "In addition to the lower handling costs, the routes for picking and subsequent processing are short too."
Systematic increase to added value
The storage-nesting cell has been in operation at MORELO since November of last year. The previous stand-alone production systems have also been replaced. With an increase in utilization from 60% to 80%, the efficiency improvement is plain to see. "We are currently using the cell to achieve the capacity of four stand-alone systems," says Jäger. "In addition, personnel requirements have fallen significantly."
This means that the motorhome manufacturer has a system at its disposal that—based on the process quality and reliability required—ensures an increase in both workpiece quantity and resource optimization. Of course, processes such as logistics and software applications can also be optimized. In addition, key factors such as the ratio of throughput to waste, the structural alignment of the parts and the shift model can be adjusted. There is therefore still plenty of potential to be harnessed. This also includes bringing outsourced production back in house.
Above all, however, the ControllerMES is allowing MORELO to increasingly move away from routing multiple orders in one production block, instead using the due date as the most important criterium for organizing production. "This means that we can operate much more efficiently, destack parts in a more organized way for subsequent processing and increase throughfeed even further," emphasizes Macke. Last but not least, the ability to combine batches and begin series production is a huge advantage.
The three nesting systems will enable further throughput growth to take place. The next few months will reveal exactly what can be achieved. However, as already dictated by the market, the system will not reach its limit. One thing is plain to see: With this storage-cutting cell, MORELO is ensuring reliable growth in the construction of motorhomes, and is doing so against the backdrop of a changing age pyramid.
“We chose the HOMAG Group for the storage nesting cell because it is state of the art.”Robert Crispens, Managing Director of MORELO.
MORELO Reisemobile
MORELO steht für First Class Reisemobile, die zu den besten der Welt gehören.
Mehr erfahren