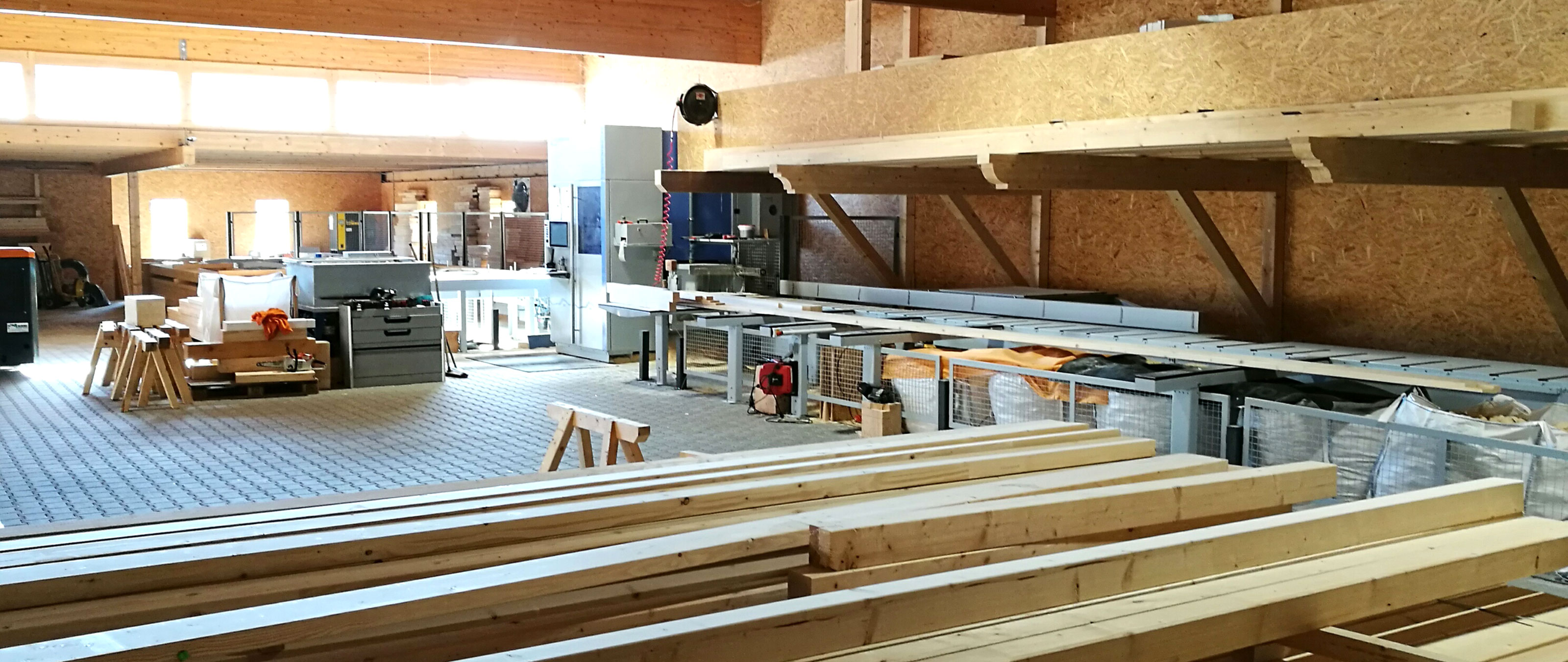
Auch ein kleines Unternehmen mit acht Mitarbeitern kann Großes leisten. Möglicherweise macht es den gleichen Umsatz wie ein Wettbewerber mit 15 Mitarbeitern, möglicherweise verzeichnet es im Vergleich sogar ein kleines Plus an Gewinn. So zumindest sieht es Marco Büsing, der in seiner Zimmerei früher selbst deutlich mehr Mitarbeiter hatte: „Und damals haben wir weder mehr Umsatz gemacht, noch mehr verdient.“
Von manuell zu automatisiert
Zwischen damals und heute liegt ein Wechsel von der manuellen zur automatisieren Fertigung, der sich in einer WEINMANN WBS 140 in der Abbundhalle niederschlägt. Die Nachfolgerin dieser Abbundmaschine, eine WBZ 160 powerSIX, ist bereits in Lonsingen bestellt.
Entschieden hat sich Marco Büsing für diese beiden Abbundanlagen zum einen aus Platzgründen: „Sie passen einfach besser bei uns in die Halle als die Maschinen der Wettbewerber, außerdem braucht man weniger Vorbereitungen.“
Ein weiterer Faktor war die Bearbeitungsqualität. In diesem Punkt hinterließen die WEINMANN-Maschinen bei Marco Büsing einen hervorragenden Eindruck. „Zwar können wir hier »nur« Formate bis 200 x 455 mm bearbeiten, aber größere Balkenquerschnitte kommen bei uns ohnehin nur alle Jahre mal vor. Da gibt es dann alternative Lösungen.“
Bevor sein im niedersächsischen Barßel angesiedeltes Unternehmen vor zweieinhalb Jahren die WBS 140 angeschafft hatte, produzierte er seine Dachstühle traditionell mit Handkreissäge und Bohrmaschine.
Hoher Vorfertigungsgrad, Qualität & Verlässlichkeit
Schon damals hatte Marco Büsing allerdings alle Dachstühle mit einem CAD-Programm von Weto geplant, das er schon seit 15 Jahren intensiv nutzt. „Damals waren diese Planungen sicher nicht so detailliert wie heute, weil man im Handabbund noch vieles in der Bearbeitung oder sogar auf der Baustelle richten kann. Heute dagegen muss ich in der Arbeitsvorbereitung exakt planen. Änderungen nach dem Abbund sollten nicht mehr erforderlich sein.“
Dies unter anderem deshalb, weil die Zimmerei Büsing in einer Region mit hoher Abbunddichte und starkem Wettbewerb nicht in den allgemeinen Preiskampf einsteigt, sondern auf einen Qualitätsvorsprung gegenüber den Wettbewerbern setzt: „Deshalb sind wir beim Abbund vielleicht 20 ct/m teurer, bieten unseren Kunden aber Leistungen, die ein Wettbewerber vielleicht nicht beherrscht oder extra in Rechnung stellt.“
Kunden sind in der Regel Bauunternehmer aus dem konventionellen Massivbau, die Büsing im Jahr mit rund 100 Dachstühlen für Wohnhäuser beliefert. In diesem Geschäft zählt neben der Qualität vor allem die Verlässlichkeit, weshalb Büsing sich seinerseits auf seine Produktionsanlage verlassen muss: „Es ist zum einen wichtig zu wissen, dass der Auftrag, der heute über die WBS 140 läuft, morgen auch ausgeliefert werden kann.
Zum anderen wird auch unsere mittelfristige Auftragsplanung durch klar definierte Produktionszeiten vereinfacht. Allerdings verlassen wir uns hier weniger auf die Berechnungen der Software als auf unsere Erfahrungswerte. Die Software kann schließlich nicht voraussehen, dass zwischendurch ein LKW entladen werden muss und die Maschine deshalb einige Zeit steht.“
Mit den besonderen „Leistungen“ meint Büsing in erster Linie einen hohen Vorfertigungsgrad in ebenso hoher Präzision: „Wenn unsere Kunden sehen, wie gut unsere Bauteile vorbereitet sind, wie schnell und problemlos alles zu montieren ist und dass wir praktisch keine Nacharbeit haben, geben wir bei ihnen ein entsprechend gutes Bild ab.“
Perfektes Zusammenspiel Software – Maschine
Der erste Schritt zu diesem Bild ist die CAD-Planung des gesamten Dachs mit Weto Viscon V10. Büsing übernimmt diesen Part in der Regel selbst, hat aber noch zwei im Programm erfahrene Mitarbeiter, die bei Bedarf für ihn einspringen können.
Überraschend: An einer Schulung auf dem Programm hat keiner der drei teilgenommen: „Als ich vor 15 Jahren in diese Software eingestiegen bin, hieß sie noch »Easy Abbund«, und dieser Name war Programm: Diese Software ist wirklich »easy«. Den Umgang damit habe ich mir im Lauf der Jahre im »learning by doing«-Verfahren angeeignet.
Als Ergänzung liefert uns WEINMANN mit wupWorks eine hervorragende Software, die BTL-Daten aus allen gängigen CAD-Programmen vollautomatisch in CNC-Programme umwandelt.“ Die Übernahme und Umwandlung der Daten erfolgt automatisch, so dass keine Nachbearbeitung mehr nötig ist.
Falls gewünscht, kann der Anwender natürlich Details im Bearbeitungsvorgang an die individuellen Anforderungen seines Unternehmens anpassen. So kann er zum Beispiel in der automatischen Werkzeugzuordnung eine Säge durch einen Fräser ersetzen und dies auch als Standard für künftige Bearbeitungen hinterlegen. Werkzeuge, Bearbeitungen und Werkstück werden ihm zu diesem Zweck in der grafischen Darstellung des Programms angezeigt, so dass er das Ergebnis vor Start der Maschine auf der Bedienoberfläche kontrollieren kann.
So ist es für Marco Büsing mit geringem Aufwand möglich, ausgehend von verschiedenen hinterlegten Standardformen individuelle Dächer in Viscon V10 zu definieren und anschließend an die WBS 140 zu übergeben. Gleiches gilt für Zwerchgiebel und Gauben in unterschiedlichen Formen. Möglich ist dabei eine breite Palette von Gaubenformen bis hin zur Schleppgaube, auch Kehlsparren, Schiftungen, Bohlenschiftung etc. lassen sich einfach eingeben und ausführen. Standarddetails, zum Beispiel eine regional häufige Gaubenform, kann er auch im CAD-Programm als Voreinstellung hinterlegen.
Büsing räumt ein, dass andere CAD-Programme möglicherweise noch mehr können, „aber dafür wird dann eben eine umfangreiche Schulung erforderlich. Für uns entscheidend: Wir stoßen mit unserem CAD-Programm praktisch nie an unsere Grenzen. Natürlich planen wir auch keine komplizierten Hallendächer, sondern Dächer für Einfamilienhäuser, bei denen architektonisch und konstruktiv eher Standardlösungen gefragt sind.“
Lösung eines Personalproblems
Dennoch sieht sich Büsing nicht als Lieferant von Standardbauteilen, weil der bei ihm übliche Vorfertigungsgrad deutlich über dem regionalen Standard liegt und bis zur Vorkonfektionierung der Dachlattung reicht. „Wenn unser Dachstuhl auf die Baustelle kommt, sind auch die Stirnbretter fertig, und die Dachziegelabstände sind schon passend eingeteilt. Unser Kunde muss also nicht mehr großartig rechnen – vorausgesetzt, er lässt uns in der Anlaufphase genügend Zeit und informiert uns, wenn es in der Planung noch eine Änderung bei den Dachpfannen gibt.“
Dass bei diesem Vorfertigungsgrad trotz des höheren Aufwands in der Arbeitsvorbereitung mehr Geld verdient wird, merkt Marco Büsing regelmäßig in der Nachkalkulation: „Je besser wir vorbereiten und je exakter wir laden, desto mehr bleibt für uns am Ende übrig.“
Verladen wird von den beiden Mitarbeitern, die in der Halle für die Bedienung und den Materialnachschub der WBS 140 zuständig sind. Da die Abbundanlage von WEINMANN mit einem vollautomatischen Transportsystem ausgestattet wurde, haben beide Kapazitäten frei. Sie können unter anderem auch die Dachbauteile schon so weit zusammenschrauben, dass sich die Montagezeit auf der Baustelle deutlich verkürzt. Das spart nicht nur Zeit und Geld, es löst für Marco Büsing auch ein massives Fachkräfteproblem: „Hätten wir genügend qualifizierte Handwerker für die Montage auf der Baustelle, wären wir vielleicht gar nicht bis zu diesem Punkt gekommen, So aber waren wir gezwungen, den Vorfertigungsgrad stetig weiter zu erhöhen, um die Fehlerquote und die Unfallgefahr auf der Baustelle zu minimieren.“
Datenübergabe ohne Probleme
Heute verlässt trotz des knappen Personals in Stoßzeiten jeden Tag ein LKW den Hof der Zimmerei, während der vom Vortag leer zurückkommt und gleich wieder beladen wird. Eine Taktung, die auch in der Zusammenarbeit zwischen CAD-Software und Maschine keinen Spielraum für Störungen lässt.
Was aber, wenn hier doch mal etwas schief geht? „Damit haben wir in der Regel wenig Probleme“, erläutert Marco Büsing: „Das liegt zum einen daran, dass in der Ruhe des Büros bis ins Detail durchdacht ist, was später von der WBS 140 produziert werden soll.
Zum anderen ist wupWorks sehr sicher, denn es gibt schon sehr früh eine Fehlermeldung aus und stoppt den Verarbeitungsprozess, falls mal eine Kollision droht oder ein Bauteil nicht komplett produziert werden kann.“
Mehr Kapazität & neue Arbeitsmöglichkeiten
Alles gut also? „Im Prinzip schon, wir sind mit der Qualität unserer WBS 140 sehr zufrieden, beliefern inzwischen auch andere Firmen mit Abbund, die das genau so sehen. Allerdings sind wir heute mit unserer Sägekapazität an der Grenze angelangt.
Deshalb auch die Anschaffung der WBZ 160 powerSIX, bei der sich die Bearbeitungszeiten noch einmal deutlich verkürzen. Das gibt den Mitarbeitern in der Halle mehr Zeit für die Vormontage und das Verladen. In Stoßzeiten bedeutet das deutlich weniger Stress.“
Willkommen sind auch die zusätzlichen Bearbeitungsmöglichkeiten durch das Unterfluraggregat, die im Dachstuhlabbund zu einer deutlichen Zeitersparnis führen. Mit einem 6,6 kW Scheibenfräser und einem 7,5 kW Antrieb für Fingerfräser, Schwalbenschwanzfräser und Bohrer ausgestattet, ermöglicht dieses Aggregat die sechsseitige Bearbeitung von Bauteilen ohne Umkanten und vereinfacht so das Materialhandling.
Zusätzlich mit einer Hauptspindel, einem 12-fach Werkzeugwechsler, einer 5-Achs Säge und einem hochauflösenden Positioniersystem bestückt, ermöglicht die WBZ 160 powerSIX eine nahezu unbeschränkte Bauteilbearbeitung in hoher Präzision.
Auch die effiziente Verschnittoptimierung – der Nutzungsgrad liegt laut Hersteller bei bis zu 98 Prozent – wird Marco Büsing zupass kommen. Um Zeitverluste beim Werkzeugwechsel zu minimieren, arbeitet der Zimmerer nämlich prinzipiell mit 13 m langem Rohmaterial: „Wenn wir also drei Bauteile von vier Metern Länge brauchen, führen wir bei einem solchen Balken jeden Arbeitsgang dreimal durch, bevor wir das Werkzeug wechseln. Am Ende trennen wir ihn dann in die einzelnen Bauteile auf.
Natürlich müssen wir bei dieser Arbeitsweise darauf achten, dass unsere Resthölzer noch vernünftig verwendet werden.“ Ein Problem, das ihm seine neue Maschine möglicherweise abnehmen wird.
Erschienen in Bauen mit Holz, Ausgabe 11/2016
Wir danken den verantwortlichen Redakteuren Markus Langenbach und Dr. Joachim Mohr.
Wir danken auch unserem Kunden Zimmerei Büsing.
Bildrechte/Fotograf: Zimmerei Büsing und WEINMANN Holzbausystemtechnik
„Es ist zum einen wichtig zu wissen, dass der Auftrag, der heute über die WBS 140 läuft, morgen auch ausgeliefert werden kann.
Zum anderen wird auch unsere mittelfristige Auftragsplanung durch klar definierte Produktionszeiten vereinfacht.“Marco Büsing, Büsing Zimmerei GmbH
Intern gewachsen
Die Büsing Zimmerei GmbH wurde am 01.09.2008 von Marco Büsing gegründet. Büsing beschäftigt inzwischen acht Mitarbeiter im Bereich Holzbau, Altbausanierung und Innenausbau. Der Einsatzschwerpunkt liegt in einem Umkreis von ca. 200 km um Barßel. Neben den klassischen Zimmererarbeiten bietet die Zimmerei Büsing heute vor allem individuelle Lösungen und Ideen für den Alt- und Neubau.
Zur Website von Zimmerei Büsing