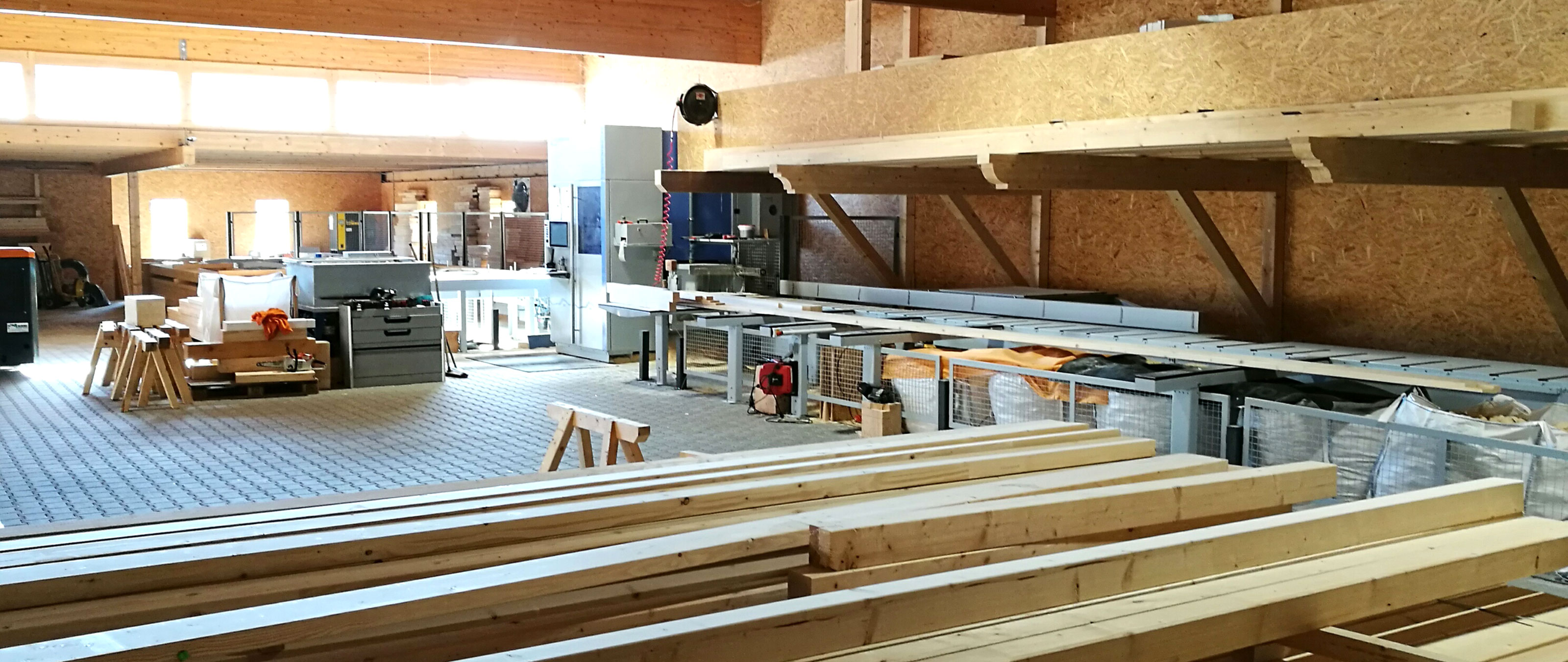
Selv en lille virksomhed med otte ansatte kan opnå store resultater. Måske er det den samme omsætning som en konkurrent med 15 medarbejdere, måske er der faktisk ved sammenligningen en lille stigning i overskuddet. Sådan ser Marco Büsing i hvert fald på det. Før havde han betydeligt flere medarbejdere i sin tømrerforretning: "Og dengang havde vi hverken større produktion eller større indtjening."
Fra manuel til automatiseret
Mellem dengang og nu har der været en ændring fra manuel til automatiseret produktion, hvilket afspejles i en WEINMANN WBS 140 i bjælkebearbejdningscentret. Efterfølgeren til denne bjælkebearbejdningsmaskine, en WBZ 160 powerSIX, er allerede bestilt i Lonsingen.
Marco Büsing besluttede sig for begge disse bjælkebearbejdningsanlæg først og fremmest af pladsårsager: "De passer simpelt hen bedre ind i vores center end konkurrenternes maskiner, og så kræver de mindre forberedelse."
En yderligere faktor var bearbejdningskvaliteten. På dette punkt har WEINMANN-maskinerne gjort et stort indtryk på Marco Büsing. "Vi kan »kun« bearbejde formater op til 200 x 455 mm, men større bjælkediametre forekommer alligevel kun en gang om året. Og så er der alternative løsninger."
Før hans virksomhed i Niedersachsens Barßel anskaffede en WBS 140 for to og et halvt år siden, producerede han sine tagspær med traditionel rundsav og boremaskine.
Høj grad af præfabrikation, kvalitet og pålidelighed
Selv dengang planlagde Marco Büsing alle tagspær med et CAD-program fra WETO, som han har brugt intensivt i 15 år. "Dengang var planlægningen ikke så detaljeret som i dag, fordi man kan justere meget i den manuelle afbinding eller på byggepladsen. Men i dag skal jeg planlægge præcist i arbejdsforberedelsen. Ændringer efter afbindingsfasen er ikke længere nødvendige."
Det skyldes blandt andet, at tømrervirksomheden Büsing, i et område med høj afbindingsvolumen og stærk konkurrence, ikke indgår i den almindelige priskrig, men i stedet satser på en kvalitetsfordel i forhold til konkurrenterne: "Derfor er vi måske 20 ct/m dyrere hvad angår afbinding, men vi tilbyder også vores kunder ydelser, som vores konkurrenter måske ikke behersker, eller som de skriver på regningen som en ekstra omkostning."
Kunderne er ofte entreprenører fra konventionelle byggevirksomheder, hvortil Büsing hvert år leverer ca. 100 tagspær til boliger. I denne forretning er det, ud overkvaliteten, især pålidelighed, der tæller, hvilket er grunden til, at Büsing skal kunne stole på sit produktionsanlæg: "Det er for det første vigtigt at vide, at den ordre, der i dag kører igennem WBS 140, rent faktisk kan leveres i morgen.
For det andet bliver vores mellemlange opgaveplanlægning forenklet ved klart definerede produktionstider. Men vi stoler her mindre på beregningerne fra softwaren end på vores erfaringer. Softwaren kan trods alt ikke forudse, at en lastbil skal aflæsses i mellemtiden, og at maskinen derfor står stille imens."
Med de særlige "ydelser" tænker Büsing først og fremmest på en høj grad af præfabrikation med lige så høj præcision: "Når vores kunder ser, hvor godt vores komponenter er forberedt, og hvor hurtigt og nemt alt kan monteres, og at vi stort set intet efterarbejde har, gør vi et godt indtryk."
Perfekt samspil mellem software og maskine
Det første trin i processen er CAD-planlægningen af hele taget med WETO Viscon V10. Büsing klarer som regel denne del selv, men har to medarbejdere med erfaring i programmet, der kan træde til, når det er nødvendigt.
Og det er overraskende: Ingen af de tre har fået undervisning i programmet: "Da jeg for 15 år siden begyndte at anvende softwaren, hed det stadig »Easy Abbund«, og programmet levede op til sit navn: Denne software er virkelig »easy«. Brugen af programmet har jeg tilegnet mig gennem årene via »learning by doing«.
Som supplement leverer WEINMANN en fremragende wupWorks-software, som automatisk konverterer BTL-data fra alle større CAD-programmer til CNC-programmer. "Lagring og konvertering af data sker automatisk, så der er intet behov for efterbearbejdning.
Hvis det ønskes, kan brugeren naturligvis justere detaljer i bearbejdningsprocessen til de individuelle behov i hans virksomhed. Således kan han erstatte en sav med en fræser i den automatiske værktøjsallokering og gemme dette som standard til fremtidige bearbejdninger. Værktøj, bearbejdninger og emner vises i programmets grafiske visning af programmet, så han kan kontrollere resultatet på brugerfladen inden start af maskinen.
På den måde er det muligt for Marco Büsing, med minimalt besvær, at definere individuelle tage på grundlag af forskellige gemte standardformularer i Viscon V10 og derefter overføre dem til WBS 140. Det samme gælder for gavle og kviste i forskellige former. En bred vifte af kvisttyper, som f.eks. taskekviste og også spær, skeletter, plankeskeletter osv. er på den måde lette at indtaste og udføre. Standarddetaljer, for eksempel en lokal hyppigt forekommende kvisttype, kan også gemmes som en forudindstilling i CAD-programmet.
Büsing anerkender, at andre CAD-programmer måske kan mere, "men i så fald kræves en omfattende uddannelse. Det afgørende for os: Med vores CAD-program når vi næsten aldrig grænsen for vores formåen. Selvfølgelig planlægger vi heller ikke nogen komplicerede haltage, men tage til enfamiliehuse, hvor der er behov for arkitektoniske og konstruktive standardløsninger."
En løsning på et personaleproblem
Ikke desto mindre ser Büsing ikke sig selv som leverandør af standardkomponenter, fordi hans grad af præfabrikation tydeligvis ligger langt over den regionale standard og omfatter præsamling af taglægterne. "Når vores tagspær kommer til byggepladsen, er også gavlene færdige, og tagstensafstanden er allerede inddelt. Vores kunde behøver ikke længere foretage beregningen - forudsat at han i opstartsfasen giver os nok tid og lader os vide, hvis der i planlægningen sker en ændring i tagstenene "
At der med dette niveau af præfabrikation, på trods af den øgede tid, der bruges på forberedelsen, tjenes flere penge, er noget Marco Büsing bemærker i den endelige omkostningsberegning: "Jo mere vi forbereder os, og jo mere præcist vi laster, jo mere er der tilbage til os."
Lastningen foretages af de to medarbejdere, der er ansvarlige for betjening og materialeforsyning af WBS 140 i hallen. Da bjælkebearbejdningsanlægget fra WEINMANN blev udstyret med et fuldautomatisk transportsystem, fik begge medarbejdere frigjort tid. De kan blandt andet skrue tagkomponenter sammen, så installationstiden på byggepladsen forkortes betydeligt. Dette sparer ikke kun tid og penge, det løser også et massivt problem med at skaffe fagfolk for Marco Büsing: "Hvis vi havde haft nok dygtige håndværkere til installation på stedet, var vi måske ikke nået til dette punkt. Men vi blev tvunget til konstant at øge niveauet af præfabrikation for fortsat at minimere fejlprocenten og risikoen for ulykker på byggepladsen."
Dataoverførsel uden problemer
Trods de få medarbejdere forlader en lastbil nu tømrervirksomhedens gård hver dag, når der er travlt, mens den tomme lastbil kommer tilbage fra den foregående dag og bliver lastet igen. En cyklus, der ikke giver plads til fejl i samarbejdet mellem CAD-software og maskine.
Hvad hvis der alligevel går noget galt? "Som regel har vi ikke de store problemer"“, fortæller Marco Büsing: "Dette skyldes det faktum, at det i detaljer og i fred og ro på kontoret er gennemtænkt, hvad der skal produceres senere af WBS 140.
For det andet er wupWorks meget sikker, da den meget tidligt viser en fejlmeddelelse og stopper bearbejdningsprocessen, hvis der er risiko for en kollision, eller hvis en komponent ikke kan produceres."
Mere kapacitet og nye arbejdsmuligheder
Så alt er godt? "Ja, i princippet, vi er meget tilfredse med kvaliteten af vores WBS 140, og vi leverer til tider også bjælker til andre virksomheder, som har samme opfattelse. Imidlertid har vi nu nået grænsen for vores savningskapacitet.
Derfor har vi anskaffet WBZ 160 powerSIX, hvormed bearbejdningstiderne bliver endnu kortere. Det giver medarbejderne i hallen mere tid til formontage og forsendelse. På travle tidspunkter betyder det også betydeligt mindre stress."
De er også glade for de ekstra bearbejdningsmuligheder vha. det forsænkede aggregat, der sparer meget tid i afbinding af tagspær. Udstyret med en 6,6 kW skivefræser og et 7,5 kW drev til fingerfræser, svalehalefræser og bor muliggør dette aggregat bearbejdning på seks sider af komponenterne uden omkantning og forenkler derved materialehåndteringen.
Men en hovedspindel, en 12-rums værktøjsveksler, en 5-akset sav og et positioneringssystem med høj opløsning giver WBZ 160 powerSIX mulighed for næsten ubegrænset bearbejdning af komponenter med høj præcision.
Også den optimerede mindre mængde af affald – udnyttelsesgraden ligger ifølge producenten på op til 98 procent – er Marco Büsing meget tilfreds med. For at minimere tidsspilde, når der skiftes værktøj, arbejder tømreren i princippet med 13 m langt råmateriale: "Så hvis vi skal bruge tre komponenter i fire meters længde, udfører vi processen tre gange for hver bjælke, før vi ændrer værktøjet. Til sidst inddeler vi den i de enkelte komponenter.
Selvfølgelig skal vi i denne procedure sørge for, at vores resttræ bruges med omtanke." Et problem, som den nye maskine sandsynligvis kan løse.
Kilde:
Byggeri med træ, udgave 11/ 2016
Forfatter:
Dr. Joachim Mohr, Tübingen
„Es ist zum einen wichtig zu wissen, dass der Auftrag, der heute über die WBS 140 läuft, morgen auch ausgeliefert werden kann.
Zum anderen wird auch unsere mittelfristige Auftragsplanung durch klar definierte Produktionszeiten vereinfacht.“Marco Büsing, Büsing Zimmerei GmbH
Intern gewachsen
Die Büsing Zimmerei GmbH wurde am 01.09.2008 von Marco Büsing gegründet. Büsing beschäftigt inzwischen acht Mitarbeiter im Bereich Holzbau, Altbausanierung und Innenausbau. Der Einsatzschwerpunkt liegt in einem Umkreis von ca. 200 km um Barßel. Neben den klassischen Zimmererarbeiten bietet die Zimmerei Büsing heute vor allem individuelle Lösungen und Ideen für den Alt- und Neubau.
Zur Website von Zimmerei Büsing