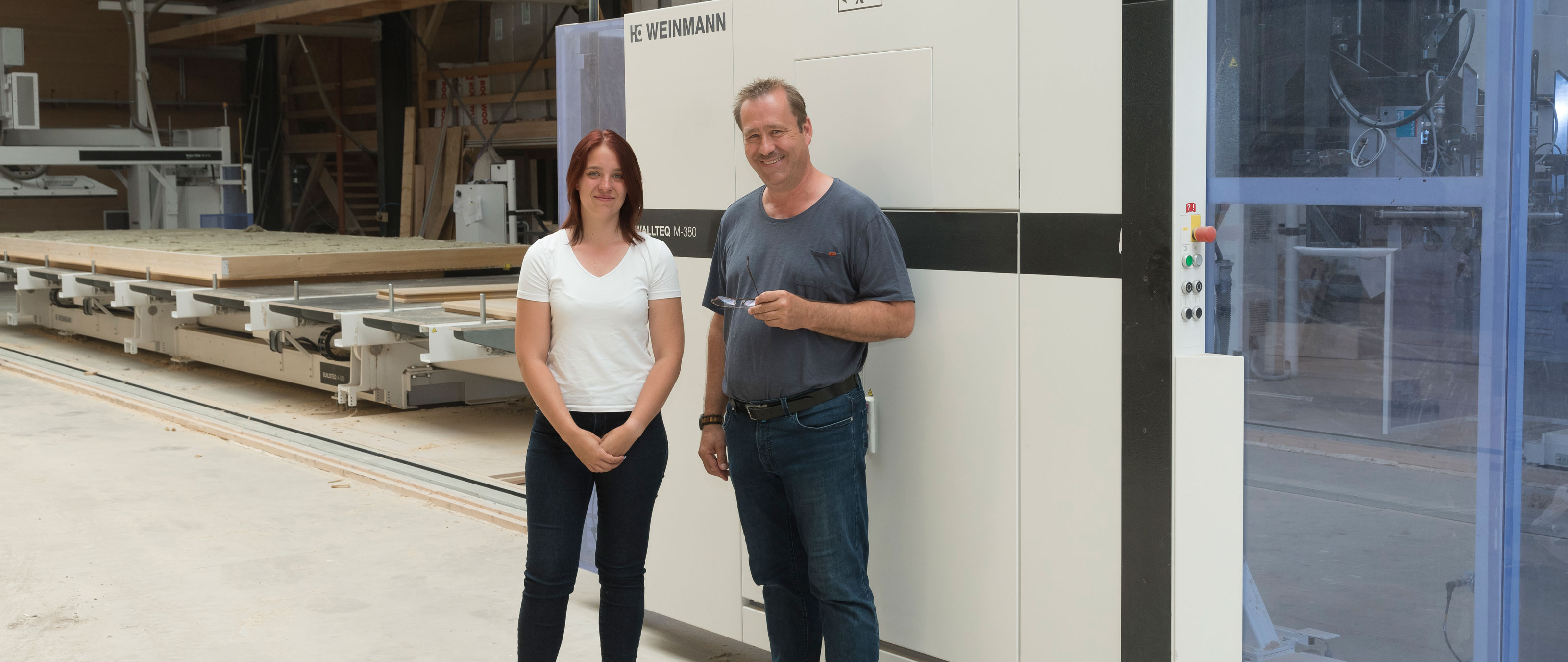
Einer der Trends im Holzbau ist der Einstieg von Abbundzentren in die Elementfertigung. Beliefert werden dabei nicht nur Kleinbetriebe ohne eigene Fertigungskapazität, sondern auch mittelständische Betriebe mit eigener Fertigung, die über den Zukauf von Elementen Auftragsspitzen abfangen oder Sonderaufträge abwickeln. Mit diesem Trend geht eine stetige Steigerung des Vorfertigungsgrads einher, weshalb viele Abbundzentren einen besonderen Fokus auf ein breites Bearbeitungsspektrum legen. Dies versetzt ihre Kunden in die Lage, die georderten Elemente auf der Baustelle schnell und mit wenig Personal zu montieren. Bei Lohnabbund Schuth im rheinland-pfälzischen Ochtendung steht als nächster Schritt der Einstieg in die Hausmontage an. Was nicht verwundert, hat doch das Unternehmen, dessen Geschichte sich wie ein Kaleidoskop der Holzbauentwicklung der letzten 40 Jahre liest, bereits in früheren Jahren Holzhäuser gebaut.
Wechselvolle Geschichte
Aus einer klassischen Zimmerei hervorgegangen, stieg das damals in Mülheim-Kärlich angesiedelte Unternehmen bereits in den 80er Jahren in den Einfamilienhausbau ein. Anfang der 90er Jahre folgte der erste Kindergarten, der Holzhausbau begann sich als festes Geschäftsfeld zu etablieren. Ab 1999 folgte der Bau von Ferienhäusern als eigene Produktlinie, die Zimmerei investierte in eine gebrauchte Fertigungsanlage. Mit der Finanzkrise 2008 kam der Bruch. Dieter Schuth und Ehefrau Silke entschieden sich unter dem zunehmenden Druck auf den Markt, ihre Geschäftsaktivitäten auf den Lohnabbund zu reduzieren. Ihre Firma schrumpfte auf ein Zweipersonen-Unternehmen: „Meine Frau stand an der Abbundmaschine, ich war für die Materialzufuhr und den Abtransport zuständig und habe abends die AV gemacht“, erinnert sich Dieter Schuth. Das Gros des Abbunds ging an eine Einkaufsgenossenschaft und ein großes Baustoffzentrum, mit denen man kontinuierlich zusammenarbeitete. Da die Nachfrage nach Holzrahmenelementen zunahm, stieg man in dieser Phase nach und nach in die Elementierung ein. In den Jahren von 2013-15 kamen sechs weitere Mitarbeiter hinzu. Die Halle wurde wieder mit einem Fertigungstisch ausgestattet, auf dem man manuell Wand- und Deckenelemente fertigte. 2018 bezog das Unternehmen ein neues Firmengelände in Ochtendung, das eine bessere Verkehrsanbindung und mit 10000 m2 Fläche bessere Wachstumsmöglichkeiten bot. Für die neue, größere Halle hatten Dieter Schuth und Tochter Cheyenne, die das Unternehmen später weiterführen soll, bereits eine automatisierte Elementfertigung ins Auge gefasst. „Es hatte sich herauskristallisiert, dass wir einen größeren Teil der kräftig wachsenden Holzbauumsätze abschöpfen wollten“, erläutert Dieter Schuth die damaligen Überlegungen. „Wir wollten auf dem Markt etwas bewegen und zum Beispiel auch in die Gebäudeklassen 4 und 5 einsteigen.“
Neue Halle, neue Technik
Dass dies nur mit einer automatisierten Fertigung umsetzbar war, stand für den Zimmerermeister außer Frage: „Zum einen kann ich die Präzision, die ich mit einer solchen Anlage erreiche, manuell einfach nicht erbringen. Präzision und hohe Qualität sind heute aber die Voraussetzungen, wenn man ganz oben mitspielen will. Zum anderen hatten wir schon vor dem Umzug in die neue Halle eine Nachfrage zu verzeichnen, die unsere Kapazitäten bei weitem überschritt. Diese Nachfrage kam zu 99 Prozent aus Zimmereien und kaum noch aus dem Handel, und sie entwickelte sich immer mehr in Richtung Elementzulieferung. Der Trend ging außerdem zu gedämmten und geschlossenen Elementen mit steigendem Vorfertigungsgrad. Diese Nachfrage war mit einer manuellen Fertigung nicht mehr zu bewältigen. Selbst wenn ich mehr Mitarbeiter eingestellt hätte die es nicht gab wären wir da sehr bald an die Grenze gestoßen. Angesichts der Personalprobleme ist es außerdem ratsam, möglichst viele Arbeitsgänge vom Tisch auf den Rechner zu verlagern. Wenn ich dann auch noch die Fertigung automatisiere, laufen die Elemente in der Halle mit wenig Manpower durch ohne Reibungsverluste durch Missverständnisse, Rückfragen und Diskussionen. Da sie durch Kapselungen etc. immer komplexer werden, ist das ein wesentlicher Vorteil.“ Nicht zuletzt ging es bei der Automatisierung um eine Verbesserung der Ergonomie: „Ich habe zum Beispiel einen Mitarbeiter, der stark auf die 60 zugeht“, erläutert Dieter Schuth. „Den möchte ich unbedingt im Unternehmen halten, weil er erfahren ist und voll hinter uns steht. Ich kann ihm aber nicht zumuten, den ganzen Tag OSB-Platten zu schleppen und auf den Knien rutschend zu klammern. Stattdessen kann ich ihm aber mit Hebeanlage und Multifunktionsbrücke einen attraktiven Arbeitsplatz bieten, damit er sich nicht nach einem körperlich weniger belastenden Job umsieht.“
Sollzeiten unterschritten
Gute Gründe für eine Automatisierung, weshalb sich Vater und Tochter auf die Suche nach einem geeigneten Maschinenbauer machten. Dabei legten sie sich zügig auf die Firma Weinmann Holzbausystemtechnik fest: „Für den Maschinenbauer in Lonsingen sprach zum einen, dass er die Steuerprogramme für seine Maschinen im eigenen Haus entwickelt“, erklärt Dieter Schuth. So greifen Software und Maschinentechnik ineinander und künftige Updates sind langfristig gesichert für uns ein ausschlaggebender Punkt.“ Wichtig war dem Geschäftsführer von Lohnabbund Schuth auch, „dass es in Lonsingen maßgeschneiderte Lösungen für jede Betriebsgröße gibt. Anderswo hatten wir teilweise das Gefühl, dass man uns auf industrielle Unternehmen zugeschnittene Lösungen anbot oder integrierte Bearbeitungsmöglichkeiten für den Ingenieurholzbau, die wir nicht brauchten, aber trotzdem bezahlen mussten.“ Auch eine Lösung mit separater Plattenbearbeitung konnte Dieter Schuth nicht überzeugen: „Da leistet mir bei unserer Stückzahl die Brücke zu wenig, und wenn ich für ein großes Projekt die Platten separat bearbeite, habe ich zwei softwaregesteuerte Anlagen, muss die Platten nach der Bearbeitung sortieren und absolut exakt im Bauteil positionieren: in meinen Augen zu viele potentielle Fehlerquellen. Da fand ich die Lösung von Weinmann, bei der die Brücke alles kann, sehr viel interessanter.“ Also orderten Dieter und Cheyenne Schuth zwei Bearbeitungstische und eine WALLTEQ M-380 Multifunktionsbrücke in Lonsingen, wo man sie auch beim Antrag auf Fördergelder für die neue Anlage unterstützt hatte. Hinzu kam eine WALLTEQ insuFill Dämmbrücke mit drehbarer Einblasplatte, wollte man auf der neuen Linie doch nicht nur Wände, sondern auch Dach- und Deckenelemente produzieren. 2021 geliefert, wurde die Anlage zügig und ohne Produktionsunterbrechung in Betrieb genommen. Seither hat sich der Umsatz des Unternehmens mehr als verdoppelt, was vor allem den schnelleren Taktzeiten in der Fertigung zu verdanken ist: „Schon bei den ersten Projekten haben wir unsere Sollzeiten immens unterschritten, hatten zum Beispiel bei einem Hotelneubau einen Elementausstoß von nahezu 100 m2 mit nur zwei Mitarbeitern in der Fertigung. Dank Automatisierung können wir heute außerdem schnell auf Auftragsspitzen reagieren. Das ist in unserem Metier wichtig, weil Großaufträge mit engem Zeitfenster sozusagen zur Jobbeschreibung gehören. Bei Bedarf können wir durch Zwei- oder Dreischichtbetrieb die Kapazitäten noch einmal drastisch erhöhen. Im Abbund sind wir schon beim Zweischichtbetrieb, als nächstes steht er jetzt auch in der Elementfertigung an ein Fragezeichen steht bloß noch vor dem zusätzlichen Personalbedarf.“ Auch der Wiedereinstieg in die Montage steht in Ochtendung unmittelbar bevor. „Auch wenn das personell nicht ganz einfach wird, wollen wir da wieder hin, um die Qualität unserer Produkte bis hinein in die Montage zu gewährleisten.“ Dafür betreibt man in Ochtendung einiges an Aufwand, setzt etwa den Stexon-Nachfolger HCW (Hilti Coupler Wood) für die exakte Wandpositionierung ein „viel präziser als Nivellierschwellen, aber ohne CNC kaum umsetzbar“. Auch den starken Trend zu mehr Vorfertigung kann man in Ochtendung dank CNC-Fertigung besser bedienen: „Man nehme nur das Thema Installationsebene, die von immer mehr Kunden nachgefragt wird. Da fertigen wir die Wände auf Wunsch inklusive Leerrohre und Hohlraumsteckdosen, die wir in eine Agepan-Platte integrieren. Nicht nur, dass sich die notwendigen Öffnungen maschinell mit wenig Aufwand fräsen lassen – wir müssen die Platte auch an jeder anstoßenden Innenwand exakt ausklinken. Manuell haben wir das schon versucht, und glauben Sie mir, das passt nie. Maschinell ist es dagegen kein Problem.“
Ausblick
Die Elementfertigung hat Lohnabbund Schuth nicht nur neue Kunden und Aufträge gesichert, sie bietet auch eine erheblich höhere Wertschöpfung als der reine Stababbund: „Letzterer ist und bleibt für uns ein gutes Standbein, aber die Elementfertigung ist viel lukrativer. Nur mit Abbund hätten wir die Investitionen in Halle und Technik niemals stemmen können.“ Dieter Schuth sieht deshalb in der Elementfertigung auch künftig die Hauptsäule seines Geschäfts. Wobei er derzeit infolge der Rahmenbedingungen eine Seitwärtsbewegung vom Einfamilienhausbau zu den Großprojekten feststellt. „Für uns prinzipiell kein Problem, weil wir technisch auch für diesen Bereich bestens aufgestellt sind. Großprojekte bringen uns sogar zusätzliche Synergien: In der AV können wir höher standardisieren und ganze Stockwerke kopieren, in der Fertigung können wir, da am Tisch keine Pläne gelesen werden müssen, die Standardbauteile schnell und reibungslos durchlaufen lassen. So sparen wir Kosten und können unsere Kapazität noch einmal erhöhen.“ Für die nächsten Jahre plant Dieter Schuth eine zweite Halle auf dem neuen Betriebsgelände. Künftig soll hier die Abbundanlage stehen, während in der bestehenden Halle eine Linie für den Fenstereinbau integriert werden soll. So will man in Ochtendung dem Trend zum höheren Vorfertigungsgrad gerecht werden. Dies natürlich in altbewährter Qualität: „Sie ist der Grundstock unseres Erfolges, denn das Gros unserer Aufträge verdanken wir der Mundpropaganda zufriedener Kunden.“
Text: Dr. Joachim Mohr
Ein Artikel aus dem Fachmagazin der Zimmermann, Ausgabe 10/2022. Mehr Informationen finden Sie hier.
„Präzision und hohe Qualität sind heute die Voraussetzungen, wenn man ganz oben mitspielen will.“Dieter Schuth, Geschäftsführer Lohnabbund Schuth GmbH
Lohnabbund Schuth GmbH
Die Lohnabbund GmbH mit Sitz in Ochtendung ist historisch aus einer klassischen Zimmerei gewachsen. Mit einem Fokus auf den Lohnabbund begonnen, ist das Unternehmen heute deutschlandweit als Partner des Handwerks etabliert und geschätzter Lieferant für Lohnabbund und vorgerfertigten Holzrahmenelementen in der Branche.
Mehr Informationen finden Sie hier.