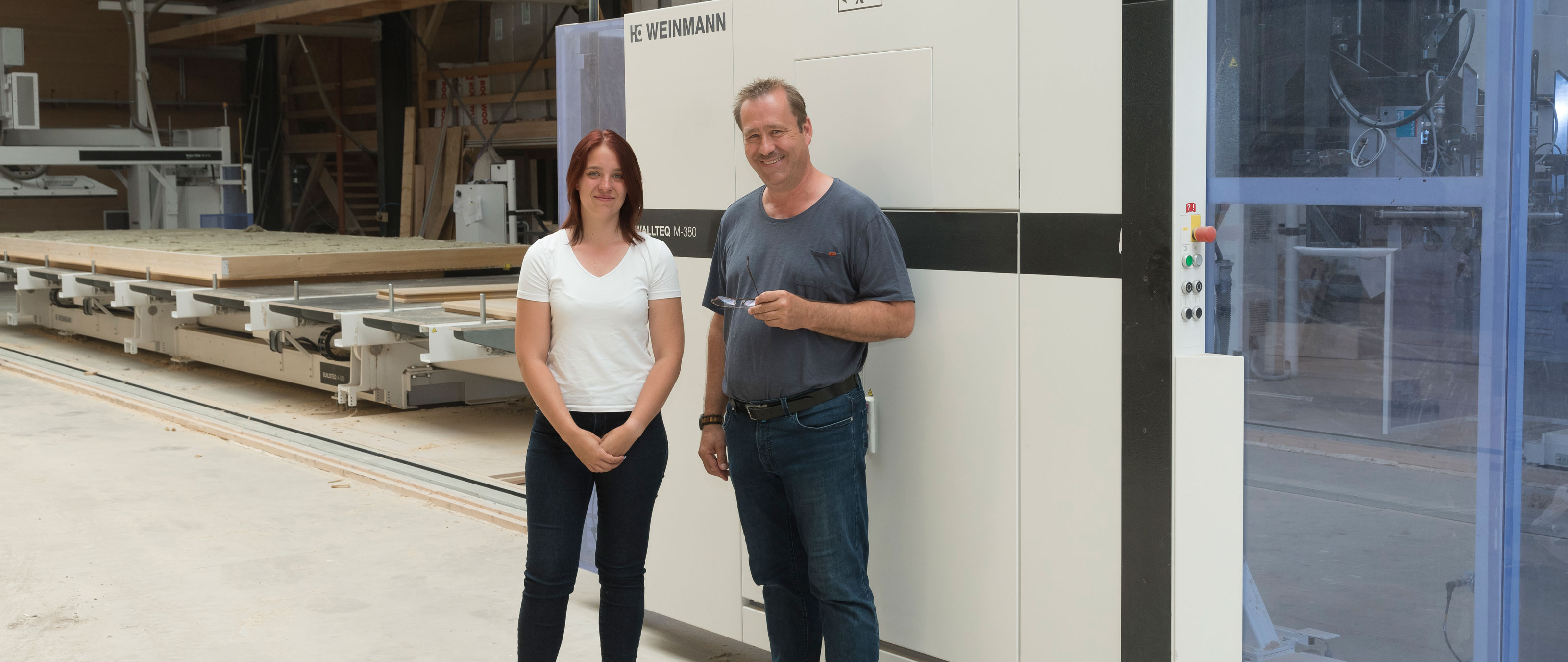
Jednym z trendów obserwowanych na rynku budownictwa drewnianego jest produkcja elementów budowlanych w centrach stolarskich. Zaopatrują one przy tym nie tylko małe zakłady, które nie mają swojej zdolności produkcyjnej, ale także zakłady średniej wielkości, które prowadzą własną produkcję, ale wspomagają się zakupem elementów z zewnątrz w celu realizacji zleceń w okresach szczytowych lub wykonywania zamówień specjalnych. Trend ten idzie w parze z ciągłym wzrostem stopnia prefabrykacji, w związku z czym wiele centrów stolarskich kładzie szczególny nacisk na poszerzanie zakresu prac obróbczych. Umożliwia to ich klientom montaż zamówionych elementów na budowie w sposób szybki i przy pomocy mniejszej liczby pracowników. Dla firmy Lohnabbund Schuth z siedzibą w Ochtendung (Nadrenia-Palatynat, Niemcy) kolejnym krokiem w rozwoju jest wkroczenie w segment montażu domów. Co wcale nie dziwi, biorąc pod uwagę, że to przedsiębiorstwo, którego historia rozwoju na rynku budownictwa drewnianego kształtowała się w ciągu ostatnich 40 lat niczym w kalejdoskopie, zajmowało się już w przeszłości stawianiem drewnianych domów.
Historia pełna zwrotów akcji
To przedsiębiorstwo, które początkowo działało w Mülheim-Kärlich jako klasyczny zakład ciesielski, już w latach 80. XX w. zaczęło wchodzić do sektora budowy domów jednorodzinnych. Na początku lat 90. firma postawiła pierwsze przedszkole i tak budownictwo drewniane weszło na stałe do zakresu jej działalności. W 1999 r. firma zaczęła oferować budowę domów letniskowych jako własną linię produktów i zainwestowała w używaną maszynę produkcyjną. Kryzys finansowy w 2008 r. doprowadził jednak do załamania. Ze względu na rosnącą presję, jaką dało się odczuć na rynku, Dieter Schuth razem z żoną Silke podjęli decyzję o ograniczeniu swojej działalności jedynie do obróbki ciesielskiej. Ich firma skurczyła się do dwóch osób: „Moja żona pracowała przy maszynie ciesielskiej, ja z kolei byłem odpowiedzialny za transport materiałów, a wieczorami zajmowałem się przygotowaniem pracy” – wspomina Dieter Schuth. Większość produkowanych przez nich złączy ciesielskich trafiała do stowarzyszenia handlowców i do dużego centrum materiałów budowlanych, z którym prowadzili stałą współpracę. Gdy popyt na elementy ram drewnianych zaczął rosnąć, stopniowo zwiększali ich produkcję. W końcu w latach 2013–15 do zespołu dołączyło sześć osób. Halę ponownie wyposażono w stół produkcyjny, na którym ręcznie wykonywano elementy ścienne i stropowe. W 2018 r. przedsiębiorstwo kupiło teren w Ochtendung, który był lepiej skomunikowany, a ze względu na powierzchnię 10 000 m2 dawał także większe możliwości rozwoju. W nowej, przestronniejszej hali Dieter Schuth wraz z córką Cheyenne, która ma w przyszłości przejąć kierownictwo, przewidzieli już miejsce na rozwiązania automatyzacji produkcji elementów. „Doszliśmy do wniosku, że chcemy wykorzystać dynamiczny rozwój budownictwa drewnianego” – wspomina Diego Schuth. „Chcieliśmy nieco szerzej spenetrować rynek i wejść na przykład także do sektora budynków klas 4 i 5”.
Nowa hala, nowa technologia
Ten mistrz ciesielstwa nie miał wątpliwości, że było to możliwe tylko przy zastosowaniu produkcji zautomatyzowanej: „Z jednej strony nie jestem w stanie ręcznie uzyskać takiego stopnia precyzji, jaką osiągam przy użyciu maszyn. A precyzja i wysoka jakość to dziś absolutne wymogi, jeśli chce się na tym polu odnieść sukces. Z drugiej strony jeszcze przed przeprowadzką do nowej hali mieliśmy do czynienia z popytem, który znacznie przekraczał nasze możliwości. W 99% były to zamówienia z zakładów ciesielskich, a jedynie w niewielkim stopniu od handlowców i coraz większe było zapotrzebowanie na dostawy elementów. Ponadto coraz mocniejszy nacisk kładziono na elementy zamknięte i izolowane o coraz większym stopniu prefabrykacji. Tego popytu nie dało się już zaspokoić produkcją ręczną. Nawet gdybym zatrudnił więcej pracowników – których zresztą na rynku pracy nie było – i tak szybko dotarlibyśmy do granic naszych możliwości. Zresztą ze względu na problemy kadrowe warto też przenieść jak najwięcej operacji ze stołu na komputer. Jeśli później zautomatyzuję także produkcję, to elementy będą obrabiane na hali przy zaangażowaniu jedynie niewielkiej liczby pracowników – co się z kolei przełoży na wyeliminowanie strat wynikających z nieporozumień, pytań i dyskusji. To istotna korzyść, ponieważ procesy stają się coraz bardziej złożone, choćby w związku z hermetyzacją itp.” Automatyzacja miała na celu także poprawę ergonomii: „Mam na przykład jednego pracownika, który zbliża się już do sześćdziesiątki” – wyjaśnia Dieter Schuth. „Koniecznie chcę go w firmie zatrzymać, ponieważ ma duże doświadczenie i jest bardzo lojalny. Nie mogę jednak od niego wymagać, żeby cały dzień klęczał czy dźwigał płyty OSB. Zamiast tego mogę zapewnić mu atrakcyjne miejsce pracy z podnośnikiem i mostkiem wielofunkcyjnym, żeby nie musiał szukać innej, mniej obciążającej fizycznie pracy.
Krótszy czas realizacji
To dobre uzasadnienie dla automatyzacji, dlatego ojciec z córką zaczęli szukać odpowiedniego producenta maszyn. Szybko zdecydowali się nawiązać współpracę z firmą Weinmann Holzbausystemtechnik: „Za tym konstruktorem maszyn z Lonsingen przemawiało po pierwsze to, że samodzielnie tworzy programy sterowania do swoich maszyn” – wyjaśnia Dieter Schuth. „Dzięki temu oprogramowanie i maszyny są ze sobą zintegrowane, a w przyszłości nie będzie problemu z aktualizacjami. To była dla nas kwestia rozstrzygająca”. Dla prezesa Lohnabbund Schuth ważne było także to, „że w Lonsingen oferowali rozwiązania, które można było dostosować do każdej wielkości zakładu. Mieliśmy wrażenie, że niektórzy producenci proponowali nam rozwiązania przeznaczone dla firm działających na skalę przemysłową albo zintegrowane rozwiązania do obróbki drewnianych konstrukcji inżynierskich, których nie potrzebujemy, a za które i tak musielibyśmy płacić”. Również rozwiązanie z odrębną obróbką płyt nie przekonało Dietera Schutha: „Taki mostek jest niewystarczający przy naszej skali produkcji, a jeśli chciałbym wykonać osobną obróbkę płyt do jakiegoś dużego projektu, to miałbym do obsługi dwie maszyny sterowane oprogramowaniem, a po obróbce musiałbym te płyty posortować i idealnie poukładać. Moim zdaniem to zbyt wiele potencjalnych źródeł błędów. Rozwiązanie firmy Weinmann, w którym mostek jest w stanie zrobić wszystko, uznałem za o wiele bardziej interesujące”. Wobec tego Dieter i Cheyenne Schuth zamówili w Lonsingen dwa stoły obróbkowe i jeden mostek wielofunkcyjny WALLTEQ M-380. Od swojego nowego partnera uzyskali również wsparcie w złożeniu wniosku o dofinansowanie do nowego sprzętu. Park maszynowy uzupełnili jeszcze o mostek izolacyjny WALLTEQ insuFill z obrotową płytą wdmuchującą, aby na nowej linii produkować nie tylko ściany, ale również elementy dachów i stropów. Maszynę dostarczono w 2021 r. i sprawnie włączono do eksploatacji bez konieczności przerywania produkcji. Od tego czasu obroty przedsiębiorstwa zwiększyły się ponaddwukrotnie, co jest zasługą głównie krótszego czasu taktu w produkcji: „Już pierwsze projekty udało się zrealizować na długo przed terminem, a w ramach projektu budowy nowego hotelu wyprodukowaliśmy elementy o łącznej powierzchni niemal 100 m2 – i to z pomocą jedynie dwóch pracowników na produkcji. Dzięki automatyzacji możemy również szybko reagować na zwiększoną liczbę zleceń. Jest to ważne w naszej branży, ponieważ duże zlecenia z krótkim terminem realizacji są nieodłączną częścią tej pracy. W razie potrzeby możemy znacznie zwiększyć zdolności produkcyjne, wprowadzając pracę w trybie dwu- lub trzyzmianowym. W warsztacie ciesielskim już pracujemy na dwie zmiany, a następnym krokiem będzie wprowadzenie tego trybu także na produkcji elementów. Rodzi się jedynie pytanie o dodatkowe potrzeby personalne”. Firma z Ochtendung planuje również powrót do realizacji zadań montażowych. „Nawet jeśli nie będzie to łatwe zadanie z punktu widzenia obsady pracowniczej, chcemy do tego wrócić, aby zapewnić jakość naszych produktów na wszystkich etapach aż po montaż”. W Ochtendung wykorzystuje się przykładowo rozwiązanie HCW (Hilti Coupler Wood), które zastąpiło Stexon, do dokładnego pozycjonowania ścian: „Efekt jest znacznie precyzyjniejszy niż w przypadku podwalin, ale niemożliwy do osiągnięcia bez centrum CNC”. Dzięki produkcji CNC można również lepiej zaspokoić silny trend zwiększania stopnia prefabrykacji: „Weźmy za przykład choćby warstwę instalacyjną, na którą rośnie zapotrzebowanie wśród klientów. Na życzenie produkujemy ściany łącznie z rurami i puszkami instalacyjnymi, które integrujemy z płytami Agepan. Maszynowe frezowanie takich otworów wiąże się z mniejszym wysiłkiem. Do tego na płycie trzeba jeszcze wykonać precyzyjnie wycięcia na styczne ścianki wewnętrzne. Próbowaliśmy robić to ręcznie i proszę mi wierzyć, że nigdy się to nie udaje. Za to przy użyciu maszyny nie stanowi to żadnego problemu”.
Perspektywy
Produkcja elementów nie tylko przysporzyła firmie Lohnabbund Schuth nowych klientów i nowych zleceń, ale także zwielokrotniła wartość dodaną w porównaniu z samym wytwarzaniem złączy ciesielskich: „Złącza ciesielskie są i będą dla nas dobrym fundamentem, ale produkcja elementów jest o wiele bardziej rentowna. Zyskami z samych złączy ciesielskich nigdy nie pokrylibyśmy inwestycji w nową halę i technologie”. W związku z tym Dieter Schuth przewiduje, że produkcja elementów pozostanie w przyszłości głównym filarem działalności firmy. W wyniku obecnych uwarunkowań zmienia jednak nieco kurs z budynków jednorodzinnych na większe projekty. „Zasadniczo nie jest to dla nas problem, ponieważ technicznie jesteśmy doskonale przygotowani do realizacji również tego typu zadań. Duże projekty wiążą się nawet z dodatkowym efektem synergii. Na etapie przygotowania pracy możemy korzystać z większej standaryzacji i kopiować całe kondygnacje, a w produkcji – ponieważ nie ma potrzeby czytania na stole żadnych planów – pozwala nam to szybko i sprawnie wytwarzać standardowe podzespoły. W ten sposób obniżamy koszty i możemy dodatkowo zwiększyć naszą zdolność produkcyjną”. W nadchodzących latach Dieter Schuth planuje otworzyć na nowym terenie drugą halę. Ma się w niej znaleźć maszyna do konstrukcji ciesielskich, podczas gdy w dotychczasowej hali ma zostać zintegrowana linia do montażu okien. Taka ma być w Ochtendung odpowiedź na trend zwiększania stopnia prefabrykacji. Wszystko oczywiście w sprawdzonej jakości: „Ona jest podstawą naszego sukcesu, ponieważ gros naszych zleceń zawdzięczamy zadowolonym klientom, którzy dzielą się swoją pozytywną opinią z innymi”.
Tekst: Dr. Joachim Mohr
Artykuł z czasopisma branżowego der Zimmermann, numer 10/2022. Więcej informacji znajdziesz tutaj.
„Precyzja i wysoka jakość to dziś absolutne wymogi, jeśli chce się odnieść sukces.”Dieter Schuth, prezes Lohnabbund Schuth GmbH
Lohnabbund Schuth GmbH
Firma Lohnabbund GmbH z siedzibą w Ochtendung zaczynała działalność jako klasyczny zakład ciesielski. Choć początkowo zajmowała się złączami ciesielskimi, dziś może się cieszyć w Niemczech ugruntowaną pozycją partnera dla wielu zakładów rzemieślniczych oraz cenionego dostawcy konstrukcji ciesielskich i prefabrykowanych elementów ram drewnianych.
Więcej informacji znajdziesz tutaj.