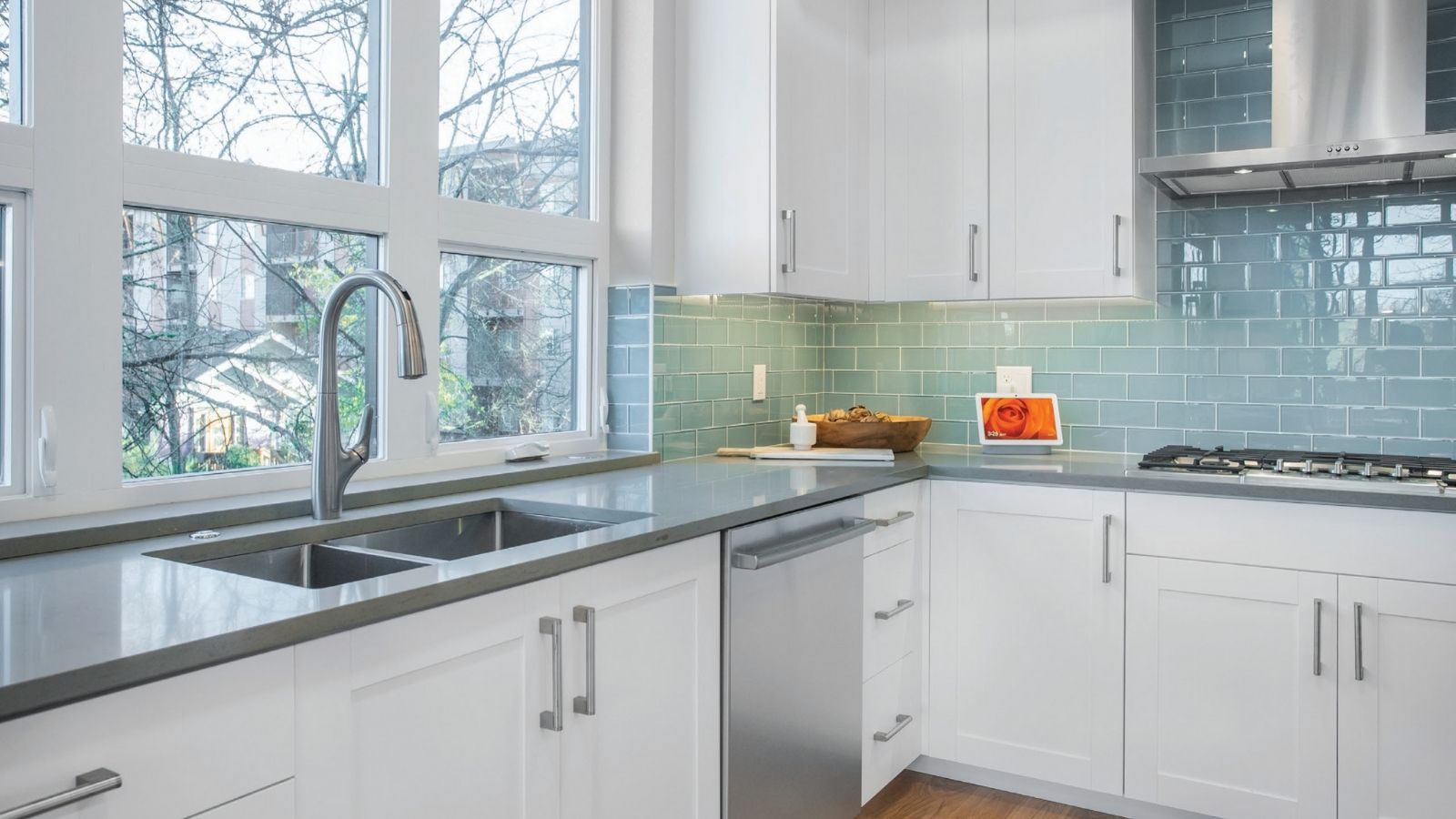
Gegründet vor 50 Jahren in Eugene, Oregon USA, ist Lanz Cabinets von einem Handwerksbetrieb zu einem fortschrittlichen Produktionsunternehmen herangewachsen, das auf den westlichen US-Markt ausgerichtet ist. Mit SCHULER Consulting fand das Unternehmen einem Partner, der ihn bei den nächsten Entwicklungsschritten begleitet und es befähigt, mit den Marktanforderungen zu wachsen.
Eine Fertigung im Fluss – Die IST-Situation
Lanz Cabinets produziert die typisch amerikanischen „face frame“ Küchen ebenso wie die „frameless“ Küchen im europäischen Stil. Darüber hinaus stellt die Firma Quartz- und Granit-Arbeitsflächen her. In drei Produktionsgebäuden werden wöchentlich auf rund 15.000 m2 bis zu 7.500 Schränke mit einem 280 Mann starken Produktionsteam gefertigt. Jeder Schrank wird für einen bestimmten Grund gefertigt, d.h. für einen bestimmten Auftrag und hat seine eigenen Anforderungen. Dank schlanker Fertigungsprozesse nach dem Lean-Ansatz fließen die Teile kontinuierlich durch die verschiedenen Prozessschritte. Ein MES-System (Manufacturing Execution System, deutsch: Fertigungsleitsystem) steuert die durch die Fabrik laufenden Komponenten. Heute sorgt der lineare Fluss in der Produktion für einen soliden Prozessablauf. Er führt von Zelle zu Zelle, verbunden über Rollenbahnen, über Materiallagerung, Schneiden oder Nesting, Bohren, Montage und Versand. An jeder Maschine wird ein Code gescannt, der die Genauigkeit der Bearbeitung sicherstellt.
Im Segment der Mehrfamilienhäuser strebt Lanz Cabinets danach, der bevorzugte Lieferant auf dem westlichen US-Markt zu sein. Um dieses Ziel zu verfolgen und in den nächsten Jahrzehnten wettbewerbsfähig zu sein, muss das Unternehmen einen höheren Automatisierungsgrad erreichen. Zu diesem Zweck sollte die derzeitige Produktionsweise optimiert werden, um die Produktionskapazität zu erhöhen, ohne die Produktionsfläche und den Personalaufwand zu vergrößern. "Wir brauchten Hilfe, um unsere Produktion auf das nächste Level zu heben, und wir wussten, dass die Zusammenarbeit mit dem Team von Schuler Consulting der einzige Weg sein würde, dies zu erreichen", erklärt Kyle Bressler, Präsident von Lanz Cabinets.
Der Weg vom „Heute“ zum „Morgen“ – Unser Vorgehen
Im Projekt nutzte das Schuler Consulting Team datengetriebene Optimierungsprozesse, um eine individuelle Lösung für Lanz zu entwickeln. In der ersten Phase des Projekts mussten so viele Daten wie möglich gesammelt werden, sortiert nach jedem relevanten Produktionsbereich. Anschließend wurde Big Data in Smart Data umgewandelt. "Das heißt, wir filtern und analysieren die gesammelten Daten im Kontext der zuvor festgelegten Ziele", erklärt Martin Kintscher, Regional Manager in Amerika für Schuler Consulting. Die Hauptziele waren, den allgemeinen Automatisierungsgrads zu erhöhen, die Produktionskapazität zu steigern und die Herstellungskosten zu senken. "Nachdem wir die Daten gesammelt und analysiert haben, erarbeiteten wir für Lanz verschiedene Wege, um die Projektziele zu erreichen und präsentierten sie dem Projektteam. Das Unternehmen entschied sich für die Investition in drei neue automatische Lager, wodurch die Produktionsprozesse räumlich neu organisiert und bestimmte Arbeitsschritte näher zusammengebracht werden konnten (z. B. Integration der Säge in das automatische Lagersystem)."
Die Automatisierung wird Realität – So funktioniert’s
Mit der vom Schuler-Team erarbeiteten Lösung macht Lanz nun den nächsten Schritt in die Zukunft. Das Unternehmen produziert bereits mit einer Hightech-Maschine wie dem Homag-CNC-Bearbeitungszentrum "CENTATEQ", das die moderne Art des Schneidens hochflexibler und individueller Schnittmuster ermöglicht. Die Integration der CNC in das Materiallager bringt nun mehr Flexibilität in die Produktion: Das automatisierte Lagersystem bevorratet das Plattenmaterial, beschickt die Maschinen und sortiert seinen Bestand auf den effizientesten Produktionsweg. Die Kombination von zwei Prozessschritten wie Lagerung und Zuschnitt führt zu einer Steigerung der Produktivität und bietet gleichzeitig die Möglichkeit, Mitarbeiter anderweitig einzusetzen. Sie senkt die Produktionskosten durch Zeitersparnis und steigert die Leistung der angeschlossenen Maschinen, indem sie diese just in time beschickt. Der Gesamtoutput der Produktion wird um ca. 33 % steigen, so dass Lanz mit der Herstellung von 10.000 Schränken pro Woche einen neuen Rekord aufstellen kann. Lanz rechnet damit, Mitte 2022 mit der Umsetzung dieser Änderungen beginnen zu können. Der neu gewonnene Produktionsfluss erhöht die Produktionskapazität und senkt gleichzeitig die Produktionskosten.
Das Ende der Reise? – Wie es weitergehen könnte
"Mit unserer für Lanz entwickelten maßgeschneiderten Lösung sahen wir die Möglichkeit, die Kapazität in Zukunft noch weiter zu steigern", berichtet René Hanuscheck, Consultant im Team Amerika. Unter Beibehaltung des gesamten Produktionsflusses können wir eine Zellenproduktion generieren, bei der jeder Prozessschritt als eigene Produktionszelle mit einem Input und einem Output gesehen wird. Hier geht es um zwei verschiedene Methoden, um noch mehr zu automatisieren. Die Beibehaltung der Zellen selbst mit manueller Materialzuführung, aber automatisierte Rollenbahnen sorgen für einen übersichtlichen Prozessablauf. Um den Weg von einer Maschine zur anderen zu überbrücken, sind AGVs flexibler und individueller in ihren Transportwegen. Die Automatisierung der gesamten Prozesslinie ist noch nicht üblich, könnte aber bald zum Standard werden. Daher könnte die zweite Methode ein weiterer Schritt für Lanz sein, die Produktion noch weiter zu automatisieren. Eine vollautomatische Lösung, bei der sich fast alles bewegt, be- und entladen wird, ganz ohne manuelle Arbeit. Robotik und KI sind Stand der Technik, wir sollten sie in unserer Branche nicht vergessen.
Autoren: Martin Kintscher (Regional Manager America, SCHULER Consulting) und René Hanuscheck (Team USA, SCHULER Consulting)