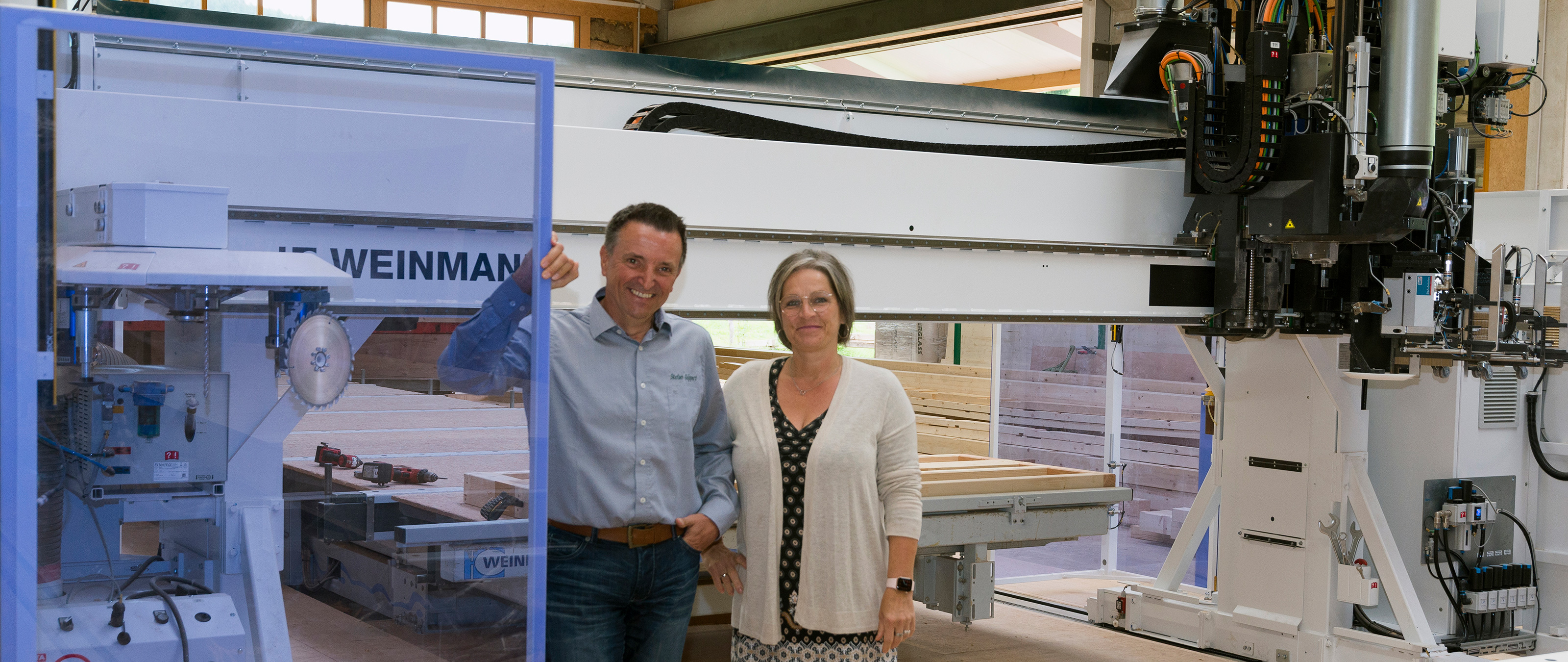
Das Interesse an automatisierter Fertigungstechnik ist derzeit auch bei kleinen Holzbaubetrieben groß. Das kann, wenn der Platz in der vorhandenen Halle knapp und eine Erweiterung nicht möglich ist, zur Herausforderung für die Planer werden. Dabei geht es nicht nur um die Aufgabe, die gewünschten Maschinen ins Hallenlayout zu integrieren. Noch spannender kann die Frage sein, welcher Bereich der Fertigung überhaupt automatisiert werden soll.
Ausbau in 2 Abschnitten
Genau vor dieser Frage stand Stefan Göppert Anfang letzten Jahres. Zuvor hatte er sein Unternehmen erweitert, hatte in einem ersten Bauabschnitt seine Halle auf 15 x 35 m ausgebaut und im zweiten ein neues Bürogebäude errichtet. Dies nach einer längeren Phase des Aufschwungs, die seiner vor 20 Jahren gegründeten Elztal Holzhaus GmbH ein solides Wachstum beschert hatte: „In den letzten zehn Jahren haben wir die Stückzahlen und Umsätze praktisch verdoppelt, so dass wir heute ein Unternehmen mit rund 50 Mitarbeitern sind, das etwa 15 Einfamilienhäuser im Jahr baut.“ Im Ein- und Zweifamilienhausbau liegt mit ca. 70 Prozent des Umsatzes der Schwerpunkt des Unternehmens. Daneben ist es im kommunalen und gewerblichen Holzbau aktiv (ca. 20 Prozent) und führt als GU energetische Gebäudesanierungen durch (ca. 10 Prozent). Der Lieferradius reicht von der Schweizer Grenze bis in den Raum Karlsruhe/Stuttgart. Die Kooperation mit verschiedenen Architekten ermöglicht der Kundschaft die individuelle Planung, weshalb man praktisch nur Unikate baut. Konstruktiv bietet man eine biologische Bauweise mit MHM-, BSP- oder selbstgefertigten Holzrahmen-Elementen an. Letztere bilden mit 80 Prozent den Löwenanteil. Alle Bauteile werden in der mit vier Arbeitsplätzen ausgestatteten Arbeitsvorbereitung geplant, um die Ausgestaltung von Details in der Hand zu behalten
Nadelöhr Fertigungstisch
Die Geschäftsentwicklung hätte sicher noch eine umfassendere Erweiterung des Unternehmens ermöglicht, aber das Firmengrundstück war mit den oben beschriebenen Bauabschnitten ausgereizt. Klar war, dass man deshalb nur einen Teil der Fertigung automatisieren konnte.Im Kern hatte Stefan Göppert die Grundsatzfrage bereits beantwortet: Die neue Halle war auf eine Abbundanlage zugeschnitten um den bisher zugekauften Abbund selbst durchzuführen. Dabei wäre es wohl geblieben, hätte sich der Zimmerer nicht Anfang 2020 die Zeit genommen, seine Fertigungsabläufe einer kritischen Überprüfung zu unterziehen.
„Da kam ich schnell ins Grübeln, denn Staus gab es nur in der manuellen Elementfertigung. Hier war unser Nadelöhr, eine neue Abbundanlage konnte unsere Effektivität also nicht steigern. Sie hätte im Gegenteil nur für noch größere Staus vor dem Fertigungstisch gesorgt.“ So beschäftige sich Stefan Göppert in der Sommerpause 2020 mit der automatisierten Elementfertigung, nahm Kontakt zu verschiedenen Herstellern auf, schaute sich Anlagen von Kollegen an. Im November orderte er nach rekordverdächtig schnellem Entscheidungsprozess bei der WEINMANN Holzbausystemtechnik GmbH in Lonsingen einen weiteren Zimmermeistertisch und eine WALLTEQ M-340. Der bereits 2015 installierte Montagetisch von WEINMANN konnte problemlos in die neue Linie integriert werden.
Aufstelltische & Hallenkran
„Für diese Multifunktionsbrücke habe ich mich wegen des Werkzeugwechslers entschieden. Mit ihm kann man Sägeblätter einwechseln, die beim Zuschnitt von Holzfaserplatten wenig Späne verursachen.“
Die Anordnung der Zimmermeistertische kristallisierte sich in der intensiven Beratungsphase mit WEINMANN heraus. Um den vorhandenen Platz optimal zu nutzen, wurden beide Montagetische zusätzlich zur Aufstellfunktion mit einem spiegelverkehrten Anschlag ausgestattet. Für den Zwischentransport wird der Hallenkran genutzt. „Das erlaubt uns das Wenden auf einer schmalen Achse. So konnten wir trotz des beengten Raums unsere Kapazität steigern und unsere Fertigungsqualität erhöhen.“
Ergonomischer arbeiten
Zur Arbeitserleichterung für seine Mitarbeiter investierte der Zimmermeister zusätzlich in zwei Plattenheber:. „Wir sind ja oft in Gebäudeklasse 4 unterwegs, wo wir die Brandschutzebene auf der Außenseite meist mit 15 mm starken Fermacellplatten ausführen. Die aufzulegen ist ein Knochenjob, den ich meinen Mitarbeitern ersparen wollte. Entsprechend gut wird die neue Technik angenommen, zumal auch die Zimmerei etwas davon hat: „Wenn wir heute Fermacellplatten auflegen und verkleben, ist der Workflow deutlich flüssiger als früher.“ An die Fertigungstische hat Stefan Göppert bewusst zwei ältere Gesellen aus der Baustellenmontage gestellt, „um diese erfahrenen Mitarbeiter durch eine neue interessante Aufgabe und ein ergonomisches Arbeitsumfeld bis zur Rente zu halten.“
Rund 30 Prozent schneller
Beide fuhren als Vorbereitung auf ihre neuen Aufgaben zur Schulung in Lonsingen: „Diese versetzte sie in die Lage, nach Lieferung der Fertigungslinie im Juni 2021 im fliegenden Wechsel weiter zu produzieren.“ – Teil eines Betreuungsprozesses, in dem sich der Zimmerer immer wieder bestens beraten und mit guten Ideen versorgt sah: „Etwa, wie wir in der nicht allzu hohen Halle Kran, Plattenheber und neue Absaugung kollisionsfrei platzieren konnten.“ Auch sein Fazit nach der Inbetriebnahme ist positiv: Schon heute zeichnet sich ab, „dass wir in der Fertigung eine Zeitersparnis von etwa 30 Prozent haben. Und da ist noch Luft nach oben: Mit mehr Personal könnten wir die Stückzahl deutlich erhöhen, mit optimierter Logistik auch Dach- und Deckenelemente auf der Linie fertigen.“ Pläne für später, denn dazu fehlt dank hoher Auslastung momentan die Zeit. Etwas entspannt wird die Situation durch Vereinfachungen im Qualitätsmanagement: „Zum einen bringt uns die Fertigungslinie ein deutliches Plus an Präzision – für uns ein wichtiger Grund, in die Automatisierung zu investieren –, zum anderen wird die Dokumentation für die Fremdüberwachung einfacher, weil wir alle wichtigen Daten automatisch in der Maschine haben.“ Unter dem Strich ein Zuwachs an Qualität, der für alle Auftraggeber gleichermaßen von Bedeutung ist. „Gerade sind wir in der Bewerbungsphase für ein größeres Objekt in Karlsruhe, und es kam schon eine Delegation vorbei, um sich den Betrieb anzusehen. Da schafft es Vertrauen, dass wir in die Qualität und Wertigkeit unserer Produkte investiert haben.“ Die Perspektive in Schuttertal ist entsprechend positiv. Stefan Göppert rechnet trotz Schwierigkeiten bei der Holzbeschaffung auch künftig mit steigenden Auftragszahlen.
Text: Dr. Joachim Mohr
Ein Artikel aus dem Fachmagazin Holzbau - die neue quadriga Ausgabe Oktober 2021 Mehr Informationen finden Sie hier
„Zum einen bringt uns die Fertigungslinie ein deutliches Plus an Präzision – für uns ein wichtiger Grund, in die Automatisierung zu investieren –, zum anderen wird die Dokumentation für die Fremdüberwachung einfacher, weil wir alle wichtigen Daten automatisch in der Maschine haben.“Stefan Göppert, Geschäftsführer Elztal Holzhaus GmbH
Elztal Holzhaus GmbH
Das Familienunternehmen Elztal Holzhaus GmbH steht seit seiner Gründung im Jahr 2001 für qualitativ hochwertige und individuelle Holzhäuser in ökologischer Holzbauweise. Die Zimmerei mit Sitz in Schuttertal-Schweighausen ist auf den schlüsselfertigen Hausbau spezialisiert und realisiert sowohl Wohnhäuser, als auch Gewerbebauten oder Kommunalgebäude. Mit den rund 50 Mitarbeitern werden pro Jahr circa 15 Wohnhäuser verwirklicht.
Mehr Informationen finden Sie hier.