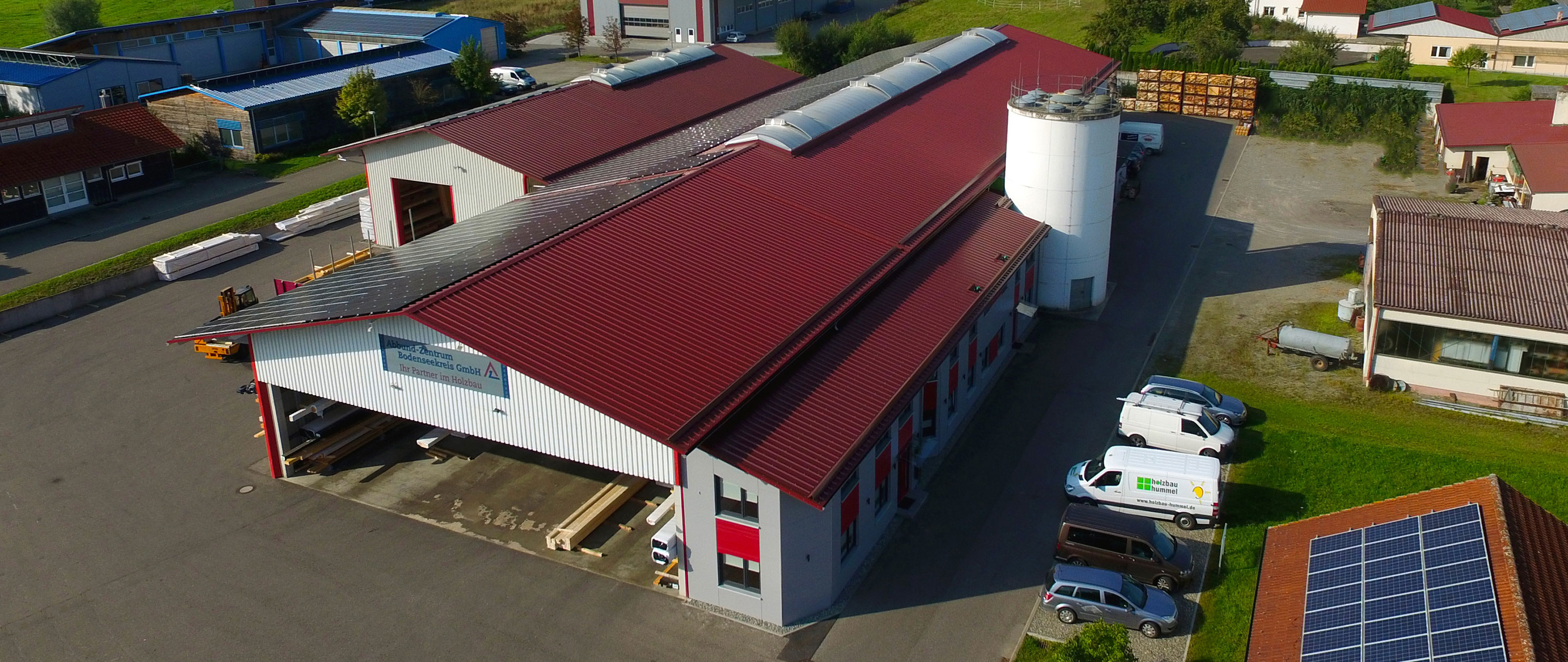
Ein Geschäftsfeld, das sich in den letzten Jahren so positiv entwickelte, dass man angesichts der angespannten Personalsituation in eine automatisierte Elementfertigung investierte. Das anhaltende Hoch im Holzbau hat in vielen Abbundzentren zu einem strukturellen Wandel geführt: Unter dem Eindruck einer stetig steigenden Nachfrage nach vorkonfektionierten Holzbauelementen ist ein Großteil dieser traditionell auf hohem technischem Niveau produzierenden Zulieferer dazu übergegangen, zusätzlich zum Stababbund fertige Wand-, Dach- und Deckenelemente anzubieten. Den Kunden, oft kleinen Zimmereien ohne eigene Produktionskapazität, bietet dieser zusätzliche Service einen vergleichsweise risikolosen Einstieg in den Holzbau: Ohne Investitionen in Gebäude, Manpower oder Maschinen haben sie die Sicherheit, dass die von ihnen in Auftrag gegebenen Elemente in professioneller Qualität just in time auf der Baustelle sind. Dass die Abbundzentren bei stabiler Nachfrage auf lange Sicht auch den Bereich der Elementfertigung automatisieren würden, war bereits zu Beginn dieses Strukturwandels zu erwarten. Inzwischen ist dieser Automatisierungsprozess bereits seit einigen Jahren in vollem Gang – zum Nutzen aller Beteiligten.
Elementfertigung seit Ende der 90er
Besonders gut funktioniert ein Zulieferungsmodell in ländlichen Regionen, wo viele kleine Holzbaubetriebe auf dem Markt sind, während die Dichte an automatisierten Fertigungslinien gering ist. In einem solchen Umfeld bewegt sich das Abbundzentrum Bodenseekreis in Heiligenberg. 1992 gegründet, verzeichnet das Unternehmen seither ein gesundes Wachstum, nahm im Lauf der Jahre eine zweite Abbundmaschine in Betrieb und fertigte seit Ende der 90er Jahre erste Holzrahmenelemente für seine Kunden. Ein Geschäftsbereich, der sich nach und nach entwickelte und dem Abbundzentrum eine solidere Geschäftsbasis verlieh.
Geschäftsführer Manfred Fritz, gelernter Zimmermann und Betriebswirt: „Nur mit Stababbund ist es schwierig, sich über Wasser zu halten. Man hat auf der Sollseite einen teuren Maschinenpark mit laufenden Kosten, auf der Habenseite Einnahmen nach laufenden Metern, die immer wieder einem starken Preiskampf unterworfen sind. Bei der Wandfertigung blieb mehr Wertschöpfung im Unternehmen, zumal die Kosten anfangs niedrig waren.“
Neue Hallen und geliehenes Personal
In diesen Anfängen fertigte man in Heiligenberg Wandelemente auf dem Boden der bestehenden Halle, ein selbst gebauter Rahmen diente als Anschlag. Produziert wurden vornehmlich Drempel- und Giebelwände für die Aufstockungen handverlesener Kunden. Bei kräftig steigender Nachfrage war aber schon 2006 eine erste Kapazitätsgrenze erreicht: Das AZ Bodenseekreis baute eine erste Produktionshalle mit Fertigungstisch, in der Folge stieg die Stückzahl bei den Wandelementen bis 2010 auf etwa 20 Häuser im Jahr. Die Geschäftsentwicklung wies weiterhin kräftig nach oben, zumal unter dem Druck steigender Stahlpreise auch die Nachfrage nach Gewerbeobjekten in Holzbauweise stieg. Da es mangels Platz bei wetterbedingten Auslieferungsstopps immer wieder zu Produktionsstaus kam, folgte schon 2012 eine zweite, deutliche größere Fertigungshalle. Seither dient die kleine Halle als Elementlager. Allerdings zeichnete sich schon bald die nächste Kapazitätsgrenze ab: „Wir leiden schon seit etwa zwei Jahren an Personalmangel“, erläutert Manfred Fritz: „Anfangs konnten wir uns noch Manpower bei Kunden ausleihen, dann kamen zum Beispiel zwei Externe für vier Wochen zum Mithelfen. So haben wir in der Fertigung Fremdleistungen im Wert von rund 100000 Euro im Jahr zugekauft.“ Das war angenehm und effizient, denn man zahlte nur die Arbeit, die man brauchte. Aber eine langfristige Lösung war es nicht: „Unsere Kunden waren irgendwann selbst so ausgelastet, dass sie uns kein Personal mehr schicken konnten.“
Maßgenschneidert für ein breites Anforderungsprofil
Da auch auf dem prekären Arbeitsmarkt kein Fachpersonal zu bekommen war, fasste man in Heiligenberg die Investition in eine automatisierte Fertigung ins Auge. „Wir haben zunächst im Internet recherchiert und verschiedene Alternativen geprüft. Dabei schälte sich ziemlich schnell die Firma WEINMANN als Favorit heraus, weil wir kurze Ersatzteilwege bevorzugen und weil dieses Unternehmen uns eine Lösung ganz nach unseren Bedürfnissen bieten konnte. Das erfuhren wir in intensiven Gesprächen beim WEINMANN-Treff, am Messestand und bei Kundenbesuchen.“ Einer der Referenzkunden arbeitete mit einer Multifunktionsbrücke WALLTEQ M-340, die ihm mit 12-fach Werkzeugwechsler und einer separaten Pick-up Station für ein Sägeblatt eine extreme Flexibilität bot – exakt passend zum Anforderungsprofil des AZ Bodenseekreis. Das umfasst eine breite Palette an Wandaufbauten und Materialien: „Wir sind hier sehr individuell aufgestellt, jeder Kunde ist anders, einer will zum Beispiel nur geschlossene Wände, der andere offene mit einseitiger OSB-Beplankung. Das war bei diesem Kunden genauso, und er bereute eigentlich nur, dass er zunächst in eine kleinere Linie investiert hatte.“ Um die Flexibilität weiter zu erhöhen, orderte man in Heiligenberg zusätzlich zur WALLTEQ M-340 zwei Zimmermeistertische, die mit Dach- und Deckenspannern ausgestattet sind. Man wollte neben Wänden auch Dach- und Deckenelemente fertigen. „Für WEINMANN kein Problem, das ist in Lonsingen Routine.“ Zum Leistungsumfang des Maschinenbauers gehörte auch eine Optimierung des Hallenworkflows, in deren Rahmen sich ein WEINMANN-Berater über zwei Tage intensiv mit den Mitarbeitern in der Fertigung austauschte. „Da ging es darum, wie wir hier arbeiten, wie man die Beschickung der Tische und den Abtransport der Elemente optimal organisieren oder welchen Arbeitsschritt man am besten an welchem Tisch machen könnte.“ So entstand Schritt für Schritt eine flexible Lösung mit Materiallagern vor und hinter den Tischen, was an jedem Tisch den Zugriff auf alle Materialien ermöglicht. Die Tische sind Aufstell- aber keine Wendetische. Das bringt dem Abbundzentrum mehr Flexibilität, etwa wenn einseitig beplankte Elemente auf zwei Tischen gleichzeitig gefertigt werden. Wird gewendet, erfolgt der Transport von Tisch zu Tisch mit dem Hallenkran. Die Beratung durch WEINMANN bezeichnet Manfred Fritz im Rückblick als „exzellent. Man riet uns zum Beispiel explizit von einem Wendetisch ab, obwohl man daran mehr verdient hätte.“ Auch bei der Inbetriebnahme der neuen Anlage fühlte sich der Geschäftsführer „hervorragend betreut, der Wechsel von manueller zu automatisierter Fertigung lief nahtlos und ohne Produktionsunterbrechungen. Der Berater kam aus dem Holzbau und gibt uns bis heute Tipps zur Arbeitsvorbereitung, die für uns Gold wert sind.“
Moderner Dienstleister für Holzbauunternehmen
Seit der Umstrukturierung ist das Abbundzentrum Bodenseekreis ein moderner Dienstleister, der seine Produkte vorwiegend im Umkreis von 60-100 km auf die Sanierungs- und Gewerbebaustellen von Zimmereien liefert. Hinzu kommt hin und wieder ein Holzhaus, außerdem ein Stammkunde in der Schweiz, den man schon seit Jahren mit Abbund und seit 2020 auch mit Dachelementen versorgt. Die maximale Elementlänge liegt derzeit bei 13 m, längere Elemente wären zwar von der Fertigungslinie her möglich, „sie machen den Transport und die Montage aber unnötig kompliziert.“ Holzrahmen werden auf der WEINMANN-Anlage ab 75 cm Stärke eingespannt, aber auch eine 360 mm starke Holzrippenkonstruktion, wie man sie momentan für ein Effizienzhaus 40 produziert, ist kein Problem. Gefertigt wird in einer Präzision, die sich durch die Automatisierung „spürbar verbessert“ hat – für den Dienstleister ein wichtiges Qualitätskriterium. „So konnten wir Fehlerquellen und Nacharbeiten auf der Baustelle minimieren. Man sieht den Unterschied schon beim Verladen: Alles passt und sitzt perfekt, das macht auch auf unseren Kunden einen positiven Eindruck.“ Zur Qualitätssteigerung trägt ebenfalls bei, dass die Mitarbeiter heute deutlich motivierter sind. „Die Arbeitsplatzqualität hat sich spürbar verbessert, man muss nicht mehr auf Knien auf den Elementen rumrutschen, alle haben mehr Freude an ihrer Arbeit.“ Lediglich beim Thema Gefachdämmung hat man sich beschränkt und auf eine Einblasanlage verzichtet: „Diesen Arbeitsgang übernehmen unsere Kunden wegen der Wertschöpfung in der Regel selbst, so dass sich eine Investition hier für uns nicht rechnet“, erläutert Manfred Fritz: Wir bohren also nur die Löcher fürs Einblasen und dämmen die Gefache auf Wunsch mit Holzfaserplatten.“
Weiteres Wachstum vorprogrammiert
Derzeit arbeiten in Heiligenberg zwei Mitarbeiter in der Fertigung, fünf wickeln im Zweischichtbetrieb den Stababbund ab. Drei Mitarbeiter sitzen in der Arbeitsvorbereitung, wo sie auf der Basis von gezeichneten Plänen oder CAD-Dateien unterschiedlicher Qualität die Elementierung und die Vorbereitung der Maschinendaten übernehmen. Mit diesem Personalbestand fertigt man im Jahr Wandelemente für etwa 40 Häuser. Im Vergleich zum Vorjahr hat man damit die Stückzahl leicht gesteigert und die Kosten für Fremdleistungen eingespart. Im Gegenzug müssen die Kosten für die Aufstockung der AV sowie die neue Fertigungslinie finanzieret werden. Deshalb ist die Investition in den Augen von Manfred Fritz momentan noch ein Nullsummenspiel. Allerdings eines mit Luft nach oben: „Durch einen dritten Mann, der zwischen den Tischen pendelt, könnten wir die Standzeiten der Multifunktionsbrücke reduzieren und unsere Kapazität nahezu verdoppeln. Ab da wird sich die neue Linie richtig rechnen.“ Wahrscheinlich, dass es bald so kommen wird – nicht nur, weil die weiterhin steigende Nachfrage dem AZ Bodenseekreis schon wieder einen neuen Wachstumsschritt nahelegt. Darüber hinaus hat vor nicht allzu langer Zeit ein Hausvertrieb angefragt, ob man ihm nicht die Elemente für seine Bauprojekte liefern könne. Sollte dieses Geschäft zustande kommen, würde sich die jährliche Stückzahl schlagartig um weitere 20 Häuser im Jahr erhöhen.
Autor: Dr. Joachim Mohr
Ein Artikel aus dem Fachmagazin mikado Ausgabe September/Oktober 2021 Mehr Informationen finden Sie hier.
„Bei der Inbetriebnahme der neuen Anlage wurden wir hervorragend betreut, der Wechsel von manueller zu automatisierter Fertigung lief nahtlos und ohne Produktionsunterbrechungen.“Manfred Fritz, Geschäftsführer Abbundzentrum Bodenseekreis
Abbundzentrum Bodenseekreis GmbH
Das Abbundzentrum Bodenseekreis sitzt in Heiligenberg und wurde 1992 gegründet. Seither verzeichnet das Unternehmen ein gesundes Wachstum, nahm im Lauf der Jahre eine zweite Abbundmaschine in Betrieb und fertigt seit Ende der 90er Jahre erste Holzrahmenelemente für seine Kunden. Ein Geschäftsbereich, der sich nach und nach entwickelte und dem Abbundzentrum eine solidere Geschäftsbasis verlieh.
Website