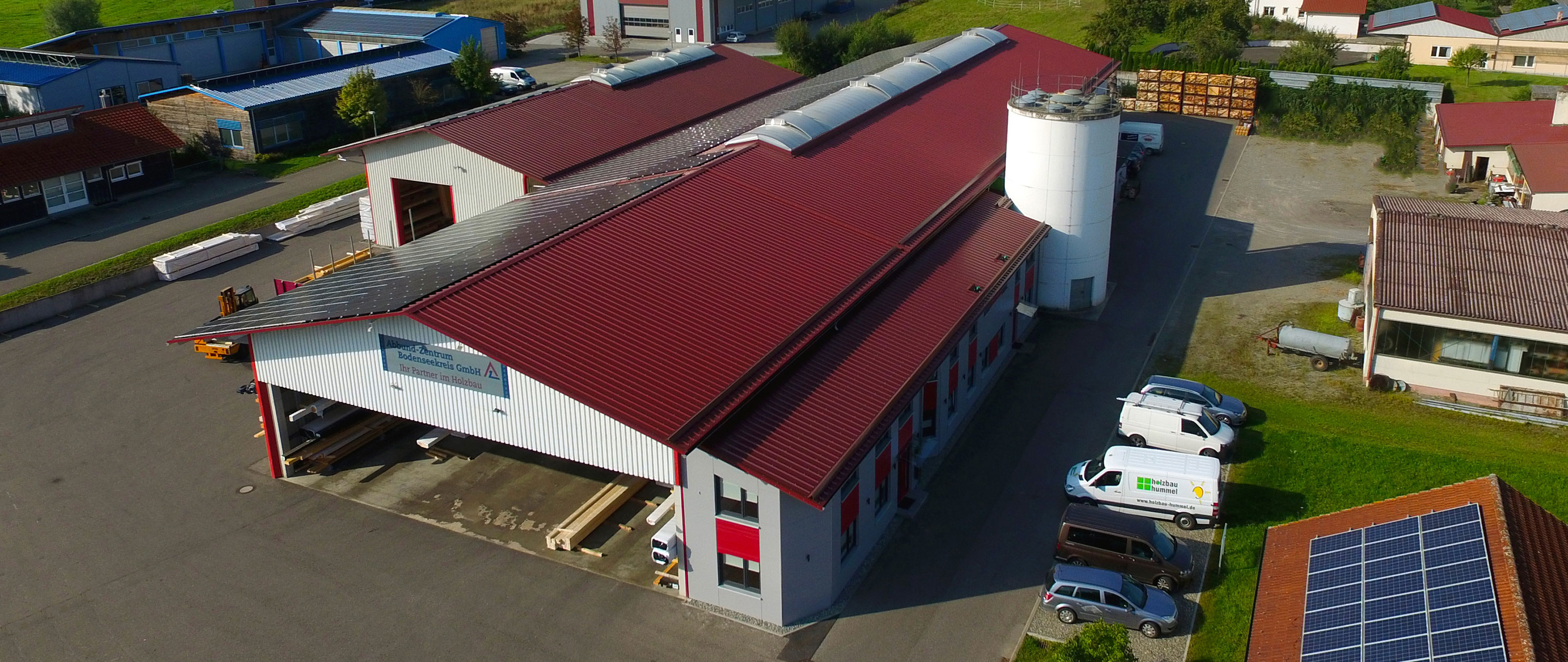
To segment działalności, który w ostatnich latach rozwinął się tak pozytywnie, że w obliczu napiętej sytuacji kadrowej firma zainwestowała w zautomatyzowaną produkcję elementów. Pierwszy rozwój budownictwa drewnianego doprowadził do zmian strukturalnych w wielu centrach stolarskich: pod wrażeniem stale rosnącego popytu na prefabrykowane elementy konstrukcji drewnianych wielu z tych dostawców, którzy tradycyjnie produkują na wysokim poziomie technicznym, przestawiło się na oferowanie gotowych elementów ściennych, dachowych i stropowych oprócz stolarki belkowej. Dla klientów, często małych zakładów stolarskich bez własnych mocy produkcyjnych, ta dodatkowa usługa zapewnia stosunkowo wolne od ryzyka wejście w budownictwo drewniane: bez inwestowania w budynki, siłę roboczą czy maszyny mają oni pewność, że zamówione przez nich elementy znajdą się na placu budowy w profesjonalnej jakości i na czas. To, że w dłuższej perspektywie centra stolarskie zautomatyzują również obszar produkcji elementów przy stabilnym popycie, było do przewidzenia już na początku tej zmiany strukturalnej. Tymczasem ten proces automatyzacji trwa już od kilku lat — z korzyścią dla wszystkich zainteresowanych.
Produkcja elementów od końca lat 90.
Model podwykonawstwa sprawdza się szczególnie dobrze w regionach wiejskich, gdzie na rynku działa wiele małych firm zajmujących się budownictwem drewnianym, a liczba zautomatyzowanych linii produkcyjnych jest niewielka. Centrum stolarskie Abbundzentrum Bodenseekreis w Heiligenbergu działa w takim właśnie środowisku. Założona w 1992 roku firma cieszy się od tego czasu zdrowym wzrostem. Z biegiem lat uruchomiła drugą maszynę ciesielską i od końca lat 90. produkuje dla swoich klientów pierwsze elementy szkieletu drewnianego. To działalność, która stopniowo rozwijała się i dała centrum stolarskiemu solidniejszą podstawę biznesową. Dyrektor zarządzający Manfred Fritz, z wykształcenia stolarz i ekonomista: „Trudno jest utrzymać się na powierzchni za pomocą samej belki. Chce się mieć drogi park maszyn z kosztami eksploatacyjnymi, a ma się przychody według metrów bieżących, które zawsze są przedmiotem sporów cenowych. Dzięki produkcji elementów ściennych w przedsiębiorstwie pozostało więcej wartości dodanej, tym bardziej, że koszty początkowo były niskie”.
Nowe hale i wypożyczony personel
W tych pierwszych dniach elementy ścienne były wykonywane w Heiligenbergu na podłodze istniejącej hali, a jako ogranicznik służyła samodzielnie zbudowana rama. Produkowano głównie ściany ościeżnicowe i szczytowe na potrzeby rozbudowy dla wybranych klientów. Jednak przy silnie rosnącym popycie już w 2006 roku osiągnięto pierwszy limit mocy produkcyjnych: AZ Bodenseekreis wybudowała pierwszą halę produkcyjną ze stołem produkcyjnym, a liczba elementów ściennych wzrosła następnie do około 20 domów rocznie do 2010 roku. Rozwój działalności nadal wykazywał silną tendencję wzrostową, zwłaszcza że popyt na budynki komercyjne w konstrukcji drewnianej wzrósł również pod presją rosnących cen stali. Jako że zawsze brakowało miejsca, gdy dostawy były wstrzymywane z powodu warunków pogodowych, w 2012 roku wybudowano drugą, znacznie większą halę produkcyjną. Od tego czasu mniejsza hala pełni funkcję magazynu elementów. Wkrótce jednak ujawniła się kolejna granica możliwości: „Od około dwóch lat zmagamy się problemem braku personelu”, wyjaśnia Manfred Fritz. „Na początku mogliśmy jeszcze pożyczać siłę roboczą od klientów, potem np. na cztery tygodnie przychodziły dwie osoby z zewnątrz, aby pomóc. W ten sposób w ciągu roku nabyliśmy usługi zewnętrzne o wartości około 100 000 euro”. Było to wygodne i skuteczne, ponieważ płaciliśmy tylko za pracę, która była nam potrzebna. Nie było to jednak rozwiązanie długoterminowe: „W pewnym momencie nasi klienci sami zmagali się z takim obciążeniem, że nie mogli już wysyłać do nas pracowników”.
Dostosowane do szerokiego profilu wymagań
Ponieważ nawet na niepewnym rynku pracy nie można było znaleźć wykwalifikowanych pracowników, w Heiligenbergu rozważano zainwestowanie w zautomatyzowaną produkcję. „W pierwszej kolejności szukaliśmy w Internecie i przyglądaliśmy się różnym alternatywom. Firma WEINMANN szybko stała się naszym faworytem, ponieważ preferujemy krótkie drogi części zamiennych, a ta firma była w stanie zaoferować nam rozwiązanie, które spełniało nasze potrzeby. Dowiedzieliśmy się tego podczas intensywnych dyskusji na spotkaniu firmy WEINMANN, na stoisku targowym i podczas wizyt u klientów”. Jeden z klientów referencyjnych pracował przy mostku wielofunkcyjnym WALLTEQ M-340, który oferował mu niezwykłą elastyczność dzięki 12-krotnemu wymiennikowi narzędzi i oddzielnej stacji odbioru dla piły tarczowej, co idealnie odpowiadało profilowi wymagań AZ Bodenseekreis. Obejmuje to szeroką gamę konstrukcji ścian i materiałów: „Mamy bardzo indywidualne podejście, każdy klient jest inny. Jeden chce na przykład tylko ściany zamknięte, inny otwarte z deskami OSB po jednej stronie. Tak samo było w przypadku tego klienta, który jedyne czego żałował to to, że początkowo zainwestował w mniejszą linię”. Aby jeszcze bardziej zwiększyć elastyczność, zakład w Heiligenbergu zamówił oprócz WALLTEQ M-340 dwa stoły ciesielskie, które są wyposażone w napinacze dachowe i sufitowe. Oprócz ścian chciano również wykonywać elementy dachowe i sufitowe. „Dla firmy WEINMANN to żaden problem, w Lonsingen to rutyna”. Zakres usług producenta maszyn obejmował również optymalizację pracy w hali, w ramach której konsultant firmy WEINMANN w ciągu dwóch dni intensywnie wymieniał pomysły z pracownikami produkcji. „Rozmawialiśmy o tym, jak tu pracujemy, jak optymalnie zorganizować załadunek stołów i demontaż elementów, czy też który etap pracy najlepiej wykonać przy którym stole”. Krok po kroku opracowano elastyczne rozwiązanie z magazynami materiałów przed i za stołami, które umożliwiają dostęp do wszystkich materiałów przy każdym stole. Stoły są stołami ustawczymi, ale nie obrotowymi. Daje to centrum stolarskiemu większą elastyczność, np. gdy elementy jednostronnie obłożone deskami są produkowane na dwóch stołach w tym samym czasie. Podczas obracania transport ze stołu na stół odbywa się za pomocą suwnicy. Patrząc wstecz, Manfred Fritz opisuje doradztwo, jakie otrzymał od firmy WEINMANN, jako „doskonałe”. Na przykład wyraźnie odradzili nam stół obrotowy, choć sami zarobiliby na nim więcej.” Podczas uruchamiania nowej instalacji dyrektor zarządzający czuł także, że otrzymał „doskonałą opiekę, a przejście z produkcji ręcznej na automatyczną przebiegło bez zakłóceń i przerw w produkcji”. Konsultant poruszał się w dziedzinie budownictwa drewnianego i do dziś udziela nam wskazówek dotyczących przygotowania do pracy, które są dla nas na wagę złota”.
Nowoczesny usługodawca dla przedsiębiorstw budowlanych
Od czasu restrukturyzacji centrum stolarskie Abbundzentrum Bodenseekreis stało się nowoczesnym usługodawcą, który dostarcza swoje produkty głównie w promieniu 60–100 km do zakładów stolarskich zajmujących się renowacją i budową obiektów komercyjnych. Od czasu do czasu pojawia się również dom z drewna, jak również stały klient w Szwajcarii, któremu od lat dostarczamy stolarkę, a od 2020 roku również elementy dachowe. Maksymalna długość elementu wynosi obecnie 13 m. Dłuższe elementy byłyby możliwe do wykonania na linii produkcyjnej, „ale niepotrzebnie komplikują transport i montaż”. W systemie WEINMANN mocowane są ramy drewniane o grubości 75 cm i większej, ale również konstrukcja drewniana żebrowa o grubości 360 mm, jak obecnie produkowana dla domu Smart Home 40, nie stanowi problemu. Produkcja odbywa się z precyzją, która została „zauważalnie udoskonalona” dzięki automatyzacji — jest to ważne kryterium jakości dla usługodawcy. „Dzięki temu udało nam się ograniczyć do minimum przyczyny błędów i czynności dodatkowe na budowie. Już podczas ładowania widać różnicę: wszystko pasuje i siedzi idealnie, co również robi pozytywne wrażenie na naszych klientach”. Do wzrostu jakości przyczynia się również fakt, że pracownicy są dziś znacznie bardziej zmotywowani. „Jakość miejsca pracy wyraźnie się poprawiła, nie trzeba już ślizgać się na kolanach po elementach, wszyscy czerpią większą przyjemność z pracy. Jedynie w przypadku izolacji więźby dachowej firma ograniczyła się do rezygnacji z systemu wdmuchiwania: „Nasi klienci z reguły wykonują te prace we własnym zakresie ze względu na wartość dodaną, więc nie ma sensu, abyśmy w to inwestowali”, wyjaśnia Manfred Fritz. „Dlatego my tylko wiercimy otwory do wdmuchiwania izolacji i na życzenie izolujemy więźbę dachową płytami z włókna drzewnego”.
Plany na dalszy rozwój
Obecnie w Heiligenbergu dwóch pracowników pracuje w dziale produkcji, a pięciu na dwie zmiany w dziale konstrukcji szkieletowych. Trzech pracowników pracuje w dziale przygotowania pracy, gdzie zajmują się elementami i przygotowywaniem danych maszynowych na podstawie rysunków lub plików CAD o różnej jakości. Przy tej liczbie pracowników firma produkuje rocznie elementy ścienne do około 40 domów. W porównaniu z rokiem ubiegłym liczba jednostek nieznacznie wzrosła i zaoszczędzono na kosztach usług zewnętrznych. W zamian trzeba będzie dokonać refinansowania kosztów związanych ze zwiększeniem sektora AV oraz nowej linii produkcyjnej. Dlatego też, w oczach Manfreda Fritza, inwestycja jest obecnie nadal grą o sumie stałej. Jest jednak miejsce na udoskonalenia: „Dodając trzecią osobę, która przemieszcza się pomiędzy stołami, moglibyśmy zredukować czas eksploatacji mostka wielofunkcyjnego i prawie podwoić naszą wydajność. Od tego momentu nowa linia będzie naprawdę opłacalna”. Prawdopodobnie wkrótce tak się stanie — nie tylko dlatego, że stały wzrost popytu sugeruje, że AZ Bodenseekreis już teraz robi kolejny krok w kierunku rozwoju. Ponadto nie tak dawno temu dystrybutor domów zapytał, czy nie moglibyśmy im dostarczyć elementów do ich projektów budowlanych. Gdyby ta umowa doszła do skutku, roczny wynik wzrósłby o kolejne 20 domów rocznie.
Tekst: Heimo Fischer
Artykuł z magazynu mikado, wydanie wrzesień/październik 2021 r. Więcej informacji można znaleźć tutaj.
„Otrzymaliśmy doskonałe wsparcie podczas uruchamiania nowego zakładu, a zmiana z produkcji ręcznej na zautomatyzowaną przebiegła płynnie i bez żadnych przerw w produkcji.”Manfred Fritz, dyrektor naczelny Abbundzentrum Bodenseekreis
Abbundzentrum Bodenseekreis GmbH
Abbundzentrum Bodensee zostało założone w 1992 r. i ma swoją siedzibę w Heiligenbergu. Od tego czasu przedsiębiorstwo odnotowało zdrowy wzrost, w ciągu ostatnich lat uruchomiło drugą maszynę do odwiązywania konstrukcji ciesielskich i od końca lat 90. produkuje dla swoich klientów pierwsze elementy ramy drewnianej. To działalność, która stopniowo rozwijała się i dała centrum stolarskiemu solidniejszą podstawę biznesową.
Website