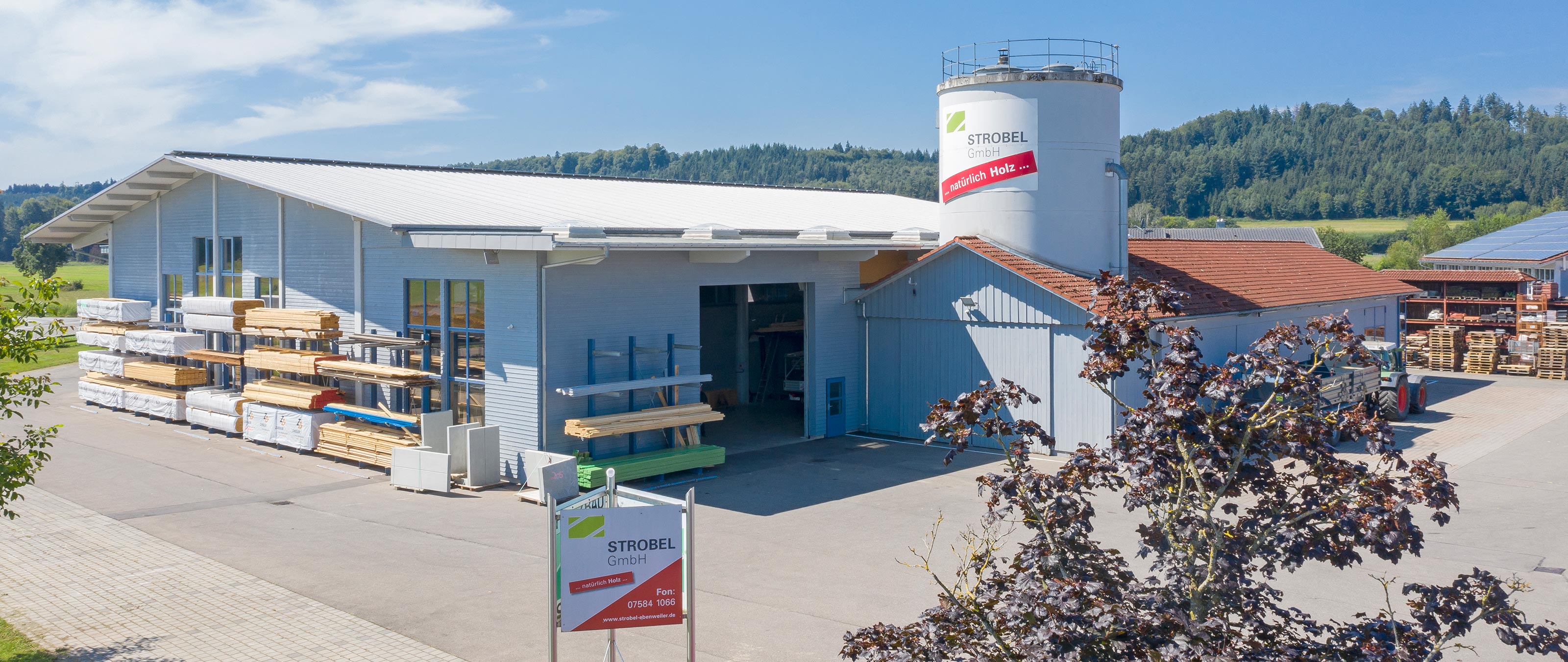
Würde man den Holzbau in Epochen einteilen, wäre jetzt vermutlich das Zeitalter der Universalisten. Denn die Auftragsrückgänge im Einfamilienhausbau, im Gewerbe- und dann auch im Wohnbau haben vor allem eines deutlich gemacht: Dass es von Vorteil ist, breit aufgestellt zu sein. Denn dann ist es kein Problem, Verluste in einem Geschäftsfeld durch Verlagerungen in andere auszugleichen. Das ist auch bei der Strobel GmbH so, die im schwäbischen Ebenweiler im Kreis Ravensburg angesiedelt ist. Der Holzhausbau, den Firmengründer Arthur Strobel schon Ende der 1980er-Jahre aufgenommen hat, hatte auch in dieser Region deutliche Einbrüche zu verzeichnen. Allerdings hatte Arthur Strobel die klassischen Zimmereigewerke im Unternehmen weitergeführt. Hinzu kamen im Laufe der Jahre viele neue Geschäftsfelder wie der mehrgeschossige Gewerbe- und Wohnbau, der Bau von Kitas und Schulen, Sanierungen, Aufstockungen und einige Modulbauten. Dies alles mit zunehmender Tendenz schlüsselfertig, auch wenn man Ausbaustufen nach individuellem Kundenwunsch anbietet. Und daneben baut man in Ebenweiler auch heute noch mit rund 45 Mitarbeitern Carports, Gartenhäuser und Dachstühle – Planung, moderne Fertigung und Spenglerarbeiten inklusive.
Wirtschaftsstarke Region
Da die Strobel GmbH in einer wirtschaftsstarken Region mit großen Pharma- und Technologieunternehmen angesiedelt ist, kamen die neuen Geschäftsfelder im Zuge erhöhter Nachfrage auf das Unternehmen zu. Bis heute hat sich an dieser Situation wenig geändert, auch wenn es in den Geschäftsfeldern einige Seitwärtsbewegungen gab. Als der Einfamilienhausbau von 30 bis 35 auf etwa zehn Häuser im Jahr zurückging, war der Mehrgeschossbau eine Möglichkeit, die Verluste auszugleichen. Zusammen mit Sanierungen und Aufstockungen, für die es nach wie vor eine starke Nachfrage in der Region gibt, ist die Strobel GmbH auch weiterhin sehr gut ausgelastet – bei einem relativ kleinen Lieferradius von 40 bis 50 km und ohne Werbung zu betreiben: Die Kundschaft kommt auch heute noch zu fast 100 Prozent über Mundpropaganda.
„Kleine“ Brücke mit Säge
2016 rückte Johannes Strobel neben seinen Vater Arthur in die Geschäftsführung auf. Angesichts der guten Marktlage machten Vater und Sohn 2019 einen ersten Anlauf, die Fertigung der Holzrahmenelemente zu automatisieren: „Damals hätten wir aber in eine große Multifunktionsbrücke investieren müssen, weil uns eine Säge für die Bearbeitung von Holzfaserplatten wichtig war. Das hat uns abgeschreckt.“ 2023 hatte sich diese Situation mit Einführung der WEINMANN WALLTEQ M-300 grundlegend verändert. Auch diese Multifunktionsbrücke ist eine Einstiegslösung für das Handwerk mit geringem Platzbedarf, sie bietet aber nicht nur eine Fräsfunktion, sondern ist neben den üblichen Klammer-, Nagel- und Markierungsaggregaten auch mit einer Säge ausgestattet. Für Johannes Strobel, der vor allem wegen der gleichbleibend hohen Präzision in eine automatisierte Fertigung investieren wollte, „eine bezahlbare Lösung, die für Unternehmen in unserer Größenordnung maßgeschneidert ist“.
Präzision & Ergonomie
Neben der Präzision stand für Johannes Strobel die Ergonomie im Vordergrund: „Mir lag viel an einer Arbeitserleichterung für meine Mitarbeiter. Sie sollten nicht mehr auf den Elementen knien und Platten von Hand auflegen.“ Positiver Nebeneffekt: Ältere Mitarbeiter, die nicht länger auf der Baustelle arbeiten wollen, kann er nun in der Halle einsetzen, sodass sie seinem Unternehmen länger erhalten bleiben. Angesichts der angespannten Personalsituation in der Region ein deutlicher Vorteil. Dies umso mehr, als man dank Automatisierung Mitarbeiter in der Fertigung einspart, die Strobel in anderen Bereichen einsetzen kann. Ende 2022 nahm Johannes Strobel erneut Kontakt zu dem zuständigen WEINMANN-Mitarbeiter auf: „Der kommt aus der Region und kennt unseren Betrieb schon seit Jahren. Es gab also in puncto Planung wenig zu klären.“ Wichtig war ihm angesichts des breiten Produktportfolios unter anderem, dass sich auf der neuen Fertigungslinie auch Dach- und Deckenelemente bearbeiten lassen.
Maximale Flexibilität
Am Ende der Gespräche stand die Bestellung für eine WALLTEQ M-300 mit Montagetisch. Da das Unternehmen bereits einen Montagetisch von WEINMANN besaß, ergibt sich so quasi eine Zwei-Tisch-Anlage, die der Zimmermeister durch zwei Plattenheber ergänzte. Einzige Einschränkung auf Wunsch der Zimmerei: Gewendet werden die Elemente momentan nicht mit einem Schmetterlingswender, sondern per Hallenkran, „aber das ist für uns völlig ausreichend. Wir dachten zuerst an einen zusätzlichen Wendetisch, entschieden uns dann aber für ein etwas langsameres Entwicklungstempo. Das macht für mich bei solchen Umstrukturierungen Sinn, weil man ja auch die Prozesse im Unternehmen auf die neue Technik abstimmen und optimieren muss. Und falls wir die Anlage später erweitern möchten, ist das wegen des bei WEINMANN üblichen modularen Aufbaus kein Problem.“
Nahtloser Wechsel
Die kurze Lieferfrist erwies sich für die Zimmerei als sportliche Herausforderung: „Die neue Technik sollte in rund drei Monaten kommen, und in dieser Zeit mussten wir nicht nur einen Hallenausbau stemmen, sondern auch unsere Arbeitsvorbereitung auf die neuen Aufgaben vorbereiten“, erläutert Johannes Strobel. Aufgaben, die das Unternehmen mit Bravour löste: Der Hallenanbau lief aus Sicht der Geschäftsführung inklusive Bauantrag, Bauteilproduktion und -montage „ziemlich unproblematisch“. Vorteil für das Unternehmen: Eine klare Trennung zwischen der Fertigung und anderen Arbeitsbereichen, sodass sich die Abläufe in jedem Bereich besser optimieren lassen. Sehr zufrieden ist der Zimmerer auch mit den Abläufen in der Arbeitsvorbereitung. „Als sie vom Liefertermin hörten, haben die beiden Meister in dieser Abteilung schon etwas die Augenbrauen hochgezogen. Aber sie standen voll hinter der Umstrukturierung, waren engagiert und sie haben alle Aufgaben hervorragend gelöst.“ Ihre Vorbereitung begann mit einer mehrtägigen Schulung bei dem Software-Unternehmen SEMA, danach gingen sie an die Entwicklung eines firmeneigenen Bauteilkatalogs, die bis heute läuft: „So ein Prozess bedeutet viel Arbeit und dauert seine Zeit, zumal man einen solchen Bauteilkatalog ja auch nach seiner Fertigstellung weiter pflegen muss. Inzwischen haben wir in der Arbeitsvorbereitung einen dritten Mann eingestellt, und das scheint mir jetzt so zu passen.“ Das Nahziel wurde aber schon mit zwei Mitarbeitern erreicht: Die Inbetriebnahme der neuen Technik im Frühjahr 2023 verlief unkompliziert, ohne Ruckeln, Stillstand oder Produktionsausfälle. „Was wir auch den WEINMANN-Mitarbeitern verdanken, die den Produktionsstart begleiteten“, erinnert sich Johannes Strobel: „Die waren richtig fit, egal ob es um die CAD-Software oder um die Arbeit an der Maschine ging. So haben sie mehrere Tage lang an den Schlüsselstellen Lösungen mit unseren Mitarbeitern erarbeitet, und das war absolut top.“
30 Prozent schneller
Und, dank eines seltenen Zusammentreffens, auch ausgesprochen aufschlussreich. Die Strobel GmbH fertigte zu diesem Zeitpunkt nämlich gerade Bauteile für ein Großprojekt: Zwei der drei baugleichen Mehrgeschosser waren bereits manuell produziert und montiert, der dritte lief komplett über die neue Fertigungslinie. So hatte man einen direkten Vergleich: Obwohl die Mitarbeiter nach rund fünf Tagen Einlernzeit alleine mit der neuen Technik arbeiteten, gelang ihnen bei diesem ersten Projekt eine Verkürzung der Fertigungszeit von sechs auf vier Wochen. „Das war schon extrem, wie schnell das alles gegangen ist und wie viel Zeit man in der Produktion gewonnen hat. Wir erreichten hier aus dem Stand die von WEINMANN angekündigten 30 Prozent, und inzwischen dürfte es noch etwas mehr sein, weil wir noch besser mit den Arbeitsabläufen vertraut sind.“ Unter dem Strich bedeutet dies eine deutliche Kapazitätssteigerung, und die nimmt man in Ebenweiler gerne mit, wenn man Wand-, Decken- und Dachelemente zeitnah an Großprojekte liefern muss. Höhere Stückzahlen waren für die Geschäftsführer aber nicht das primäre Ziel ihrer Investition, weshalb sie den Zuwachs an Kapazität zu einem guten Teil für eine Erhöhung des Vorfertigungsgrads nutzen. So ist das Volumen nicht proportional gestiegen: „Wir produzieren heute schon mehr und die Maschine ist gut ausgelastet, aber wir fertigen jetzt auch solche Bauteile vor, die uns in Zeiten der manuellen Fertigung zu kompliziert waren“, so der Juniorchef. Ein Beispiel? Komplizierte Dachgeometrien, die man heute mit Dachelementen realisiert, während man sie früher Balken für Balken vor Ort zusammenbaute.
Positives Fazit
Heute kommen also alle Bauteile aus Ebenweiler komplett vorgefertigt auf die Baustelle, und die Rückmeldungen aus der Montage sind ebenfalls aufschlussreich. Johannes Strobel: „Wir waren auch in der manuellen Fertigung schon sehr präzise, aber auf der Baustelle passt heute alles noch einmal besser. Dachelemente gleiten wie von selbst an die richtige Position, Nacharbeit ist praktisch kein Thema mehr. Allgemein herrscht bezüglich der neuen Technik vor allem eine Meinung vor: Die hätten wir schon viel früher einführen sollen.“ Das gilt auch für die Mitarbeiter in der Fertigung, deren Zahl auf vier bis fünf im Einschichtbetrieb geschrumpft ist: „Hier gibt es viel Lob für die neue rücken- und knieschonende Arbeitsweise“, erläutert Johannes Strobel. „Ein Mitarbeiter sagte mir neulich, dass er seit der Umstellung nicht mehr jeden Abend todmüde nach Hause fährt. Mich lässt das hoffen, dass er und die anderen länger für uns arbeiten können.“ So lautet das Fazit in Ebenweiler: Alle Ziele erreicht! Man fertigt in höherer Präzision, hat das Problem der Personalknappheit entschärft, die Fertigungszeiten drastisch verkürzt. Auch die Kundschaft ist von der neuen Technik angetan, begrüßt die Sicherheit am Bau, die mit der industriellen Präzision und der automatischen Dokumentation aller Arbeitsgänge verbunden ist. Beworben wird die Umstrukturierung allerdings nicht, da noch immer fast alle Kunden per Empfehlungsmanagement kommen. Und es spricht viel dafür, dass dies noch lange so bleiben wird.
„Das war schon extrem, wie schnell das alles gegangen ist und wie viel Zeit man in der Produktion gewonnen hat. Wir erreichten hier aus dem Stand die von WEINMANN angekündigten 30 Prozent, und inzwischen dürfte es noch etwas mehr sein, weil wir noch besser mit den Arbeitsabläufen vertraut sind.“Johannes Strobel, Geschäftsführer Strobel GmbH
Strobel GmbH
Die Strobel GmbH mit Sitz in Ebenweiler, im Kreis Ravensburg, produziert Holzbauelemente wie Wand-, Decken- und Dachelemente sowie andere Holzkomponenten für den Einsatz in unterschiedlichen Bauprojekten, darunter Mehrgeschossbauten, Kitas, Schulen und Sanierungsprojekte. Im Jahr 1987 gründete Alfons Strobel das Unternehmen in der hauseigenen Garage. Im Jahr 1990 erfolgt der Umzug in das Gewerbegebiet und im Jahr 2016 kommt Sohn Johannes Strobel nach bestandener Meisterprüfung mit in die Geschäftsführung. Heute umfasst das Betriebsgelände circa 11.000 Quadratmeter mit vier großen Hallen. Rund 45 Mitarbeiter sind im Unternehmen beschäftigt, fünf davon sind Auszubildende.
Mehr Informationen