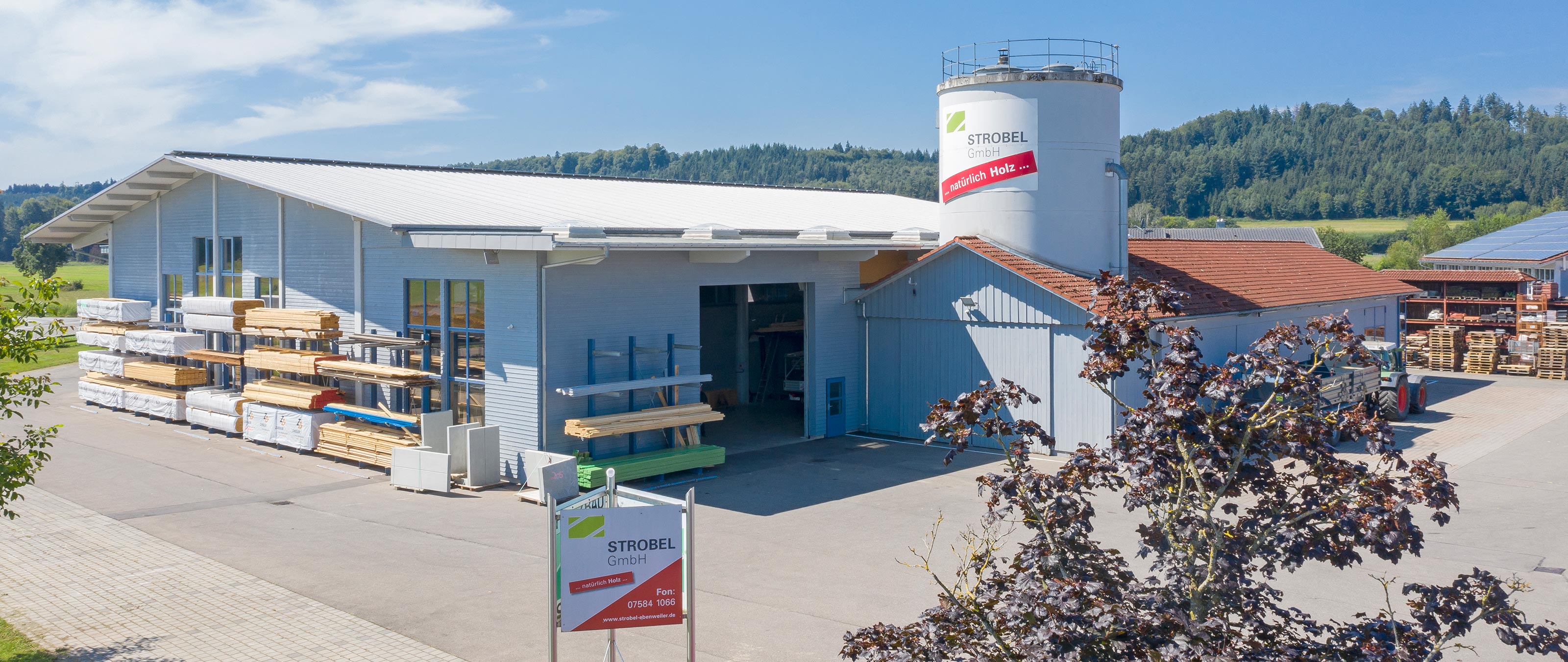
Se volessimo suddividere in periodi la storia delle costruzioni in legno, potremmo definire l'attuale periodo come l'era degli universalisti. In effetti, il calo degli ordini nella costruzione di case unifamiliari, nell'edilizia commerciale e poi in quella residenziale hanno quantomeno chiarito una cosa: avere una base ampia rappresenta un vantaggio. Questo perché le perdite in un'area di business possono facilmente essere compensate spostandosi verso altri settori. È il caso di Strobel GmbH, azienda con sede nel comune tedesco di Ebenweiler (circondario di Ravensburg), nella regione storica della Svevia. La costruzione di case in legno, attività intrapresa dal suo fondatore Arthur Strobel alla fine degli anni '80 del '900, faceva registrare cali significativi anche in questa regione. Tuttavia, Strobel ha continuato a eseguire in azienda anche i classici lavori di falegnameria. Negli anni sono stati aggiunti diversi nuovi settori di attività, come l'edilizia commerciale e residenziale multipiano, la costruzione di asili e scuole, le ristrutturazioni, gli ampliamenti e alcuni edifici modulari. Tutto questo sta diventando sempre più "chiavi in mano", anche se vengono offerti livelli di sviluppo che rispondono alle esigenze dei singoli clienti. Ancora oggi nella sede di Ebenweiler – che conta circa 45 dipendenti – si realizzano inoltre carport, casette da giardino e capriate (progettazione, produzione moderna e lavori di lattoneria inclusi).
Una regione economicamente forte
Poiché Strobel GmbH ha sede in una regione dall'economia fortemente sviluppata, con grandi aziende farmaceutiche e tecnologiche, l'azienda è potuta entrare nei nuovi settori di attività grazie all'aumento della domanda. A oggi tale situazione è pressoché immutata, anche se si sono registrati alcuni fenomeni marginali non irrilevanti. Quando la costruzione di case unifamiliari è scesa da 30-35 a circa dieci unità l'anno, realizzare strutture a più piani è diventato un modo per compensare le perdite. Grazie anche alle ristrutturazioni e agli ampliamenti, per i quali nella regione esiste ancora una forte domanda, Strobel GmbH opera sempre a pieno regime, e tutto questo con un raggio di consegna relativamente piccolo, da 40 a 50 km, e senza fare pubblicità: ancora oggi, infatti, i nuovi clienti arrivano quasi tutti tramite il passaparola.
Un ponte "piccolo" con sezionatrice
Dal 2016, Johannes Strobel è entrato a far parte del management aziendale, a fianco del padre. Vista la buona situazione del mercato, nel 2019 padre e figlio hanno iniziato ad automatizzare la produzione degli elementi d'intelaiatura in legno: "All'epoca avremmo però dovuto investire in un grande ponte multifunzione, perché per noi era importante disporre di una sezionatrice per lavorare i pannelli in fibra di legno. Questo ci ha scoraggiati." Nel 2023, con l'introduzione della WEINMANN WALLTEQ M-300, la situazione è radicalmente cambiata. Anche questo ponte multifunzione è una soluzione entry-level con ingombro ridotto per imprese artigiane, ma oltre a includere la funzione di fresatura, è dotato di una sezionatrice in aggiunta ai comuni gruppi di pinzatura, chiodatura e marcatura. Per Johannes Strobel, che voleva investire in una produzione automatizzata soprattutto in virtù della precisione costante, si tratta di "una soluzione conveniente, pensata per aziende delle nostre stesse dimensioni".
Precisione ed ergonomia
Oltre alla precisione, anche l'ergonomia era una priorità per Johannes Strobel: "Desideravo semplificare il lavoro dei miei dipendenti. Adesso non devono più inginocchiarsi sugli elementi e posare a mano i pannelli." Effetto collaterale positivo: i lavoratori più anziani, che non vogliono più lavorare in cantiere, possono spostarsi nel capannone, così restano in azienda più a lungo. Considerato che nella regione la situazione con il personale è piuttosto tesa, questo rappresenta un evidente vantaggio. Tanto più che, grazie all'automazione, Strobel può liberare dipendenti dalla produzione e impiegarli in altre aree. Così, a fine 2022, Johannes Strobel ha ricontattato il responsabile di WEINMANN: "È anche lui della zona e conosce la nostra azienda da anni. C'era poco da chiarire in termini di progettazione." Considerata l'ampiezza della gamma di prodotti, era importante, tra l'altro, che la nuova linea di produzione potesse servire anche per gli elementi di tetti e soffitti.
Massima flessibilità
Al termine della trattativa, è stato passato l'ordine per una WALLTEQ M-300 con tavolo di montaggio. Dato che l'azienda possedeva già un tavolo di montaggio WEINMANN, si otteneva così quasi un impianto a due tavoli, che il mastro carpentiere ha poi integrato con due sollevatori di pannelli. Unica limitazione su richiesta della carpenteria: gli elementi non vengono girati con un ribaltatore a farfalla, bensì con un carroponte, "Ma per noi basta così. Dapprima pensavamo a un tavolo di rotazione supplementare, ma poi abbiamo deciso di seguire un ritmo di sviluppo un po' più lento. Per me è sensato nelle riorganizzazioni di questo genere, perché bisogna anche adattare e ottimizzare i processi aziendali alla nuova tecnologia. E se in futuro volessimo potenziare l'impianto, non sarebbe un problema grazie alla ben nota modularità delle soluzioni WEINMANN."
Cambi senza interruzioni
Per la carpenteria, i tempi di consegna ridotti si sono rivelati una sfida sportiva: "Con la nuova tecnologia in arrivo nel giro di tre mesi, dovevamo non solo gestire l'ampliamento di un capannone, ma anche predisporre le operazioni preliminari di produzione in vista delle nuove attività", spiega Johannes Strobel. Tutti compiti che l'azienda ha portato a termine con successo: dal punto di vista del management, la costruzione del capannone si è svolta "sostanzialmente senza problemi", inclusa la richiesta di permesso edilizio e la produzione e l'assemblaggio dei componenti. Un vantaggio per l'azienda: la netta separazione tra la produzione e le altre aree di lavoro permette di ottimizzare al meglio le operazioni in ogni settore. Il carpentiere è molto soddisfatto anche dei procedimenti preliminari alla produzione. "Quando hanno saputo la data di consegna, i due capireparto già aggrottavano le sopracciglia. Ma erano pienamente a favore della riorganizzazione, si sono impegnati e hanno svolto tutti i compiti alla perfezione." La loro preparazione è iniziata con una formazione di più giorni presso la casa software SEMA, dopodiché si sono dedicati allo sviluppo di un catalogo di componenti dell'azienda, che è in vigore ancora oggi: "Un processo del genere comporta molto lavoro e richiede tempo, tanto più che un catalogo così necessita di aggiornamenti periodici. Nel frattempo, abbiamo assunto un terzo uomo per le operazioni preliminari di produzione, e per ora mi sembra possa andare bene." Tuttavia, l'obiettivo a breve termine era già stato raggiunto con due dipendenti: la messa in esercizio della nuova tecnologia a primavera 2023 si è svolta senza problemi, senza scosse, tempi morti o perdite di produzione. "Il merito è anche del personale di WEINMANN, che ci ha affiancati durante l'avvio della produzione", ricorda Johannes Strobel. "Erano davvero operativi, sia per quanto riguarda il software CAD che nel lavoro sulla macchina. Per molti giorni hanno elaborato soluzioni con i nostri dipendenti nelle aree chiave, ed è stato assolutamente fantastico."
Del 30% più veloci
E grazie a una felice coincidenza, anche estremamente rivelatore. In quel momento, infatti, Strobel GmbH stava fabbricando componenti per un grosso progetto: due di tre edifici multipiano identici erano già stati prodotti e montati manualmente, mentre il terzo veniva eseguito interamente sulla nuova linea di produzione. In questo modo abbiamo potuto fare un confronto diretto: sebbene abbiano impiegato cinque giorni per lavorare da soli una volta acquisita familiarità con la nuova tecnologia, in questo primo progetto gli operatori sono riusciti a ridurre i tempi di produzione da sei a quattro settimane. "È incredibile quanto siano andate veloci le cose e quanto tempo abbiamo guadagnato in fase di produzione. Abbiamo raggiunto il 30% preannunciato da WEINMANN partendo da zero, e ora il dato dovrebbe essere ancora migliore, perché abbiamo una maggiore familiarità con i procedimenti di lavoro. Il risultato è un significativo incremento della capacità, che a Ebenweiler è benvenuto, visto che l'obiettivo è consegnare tempestivamente elementi di pareti, soffitti e tetti per grossi progetti. Tuttavia, per il management l'obiettivo primario dell'investimento non era realizzare un maggior numero di pezzi, bensì utilizzare l'aumentata capacità in buona parte per accrescere il livello di prefabbricazione. In effetti il volume non è cresciuto in proporzione: "Produciamo già di più e la macchina è ben utilizzata, ma ora approntiamo anche componenti che erano troppo complicati per la produzione manuale", dichiara il giovane capo. Un esempio? Geometrie di tetti complesse, realizzate mediante elementi prefabbricati laddove ieri venivano assemblate in loco una trave alla volta.
Un bilancio positivo
Oggi tutti i componenti arrivano in cantiere da Ebenweiler completamente prefabbricati, e anche il feedback del reparto montaggio è illuminante. Johannes Strobel: "Nella produzione manuale eravamo già molto precisi, ma adesso in cantiere va addirittura meglio. Gli elementi del tetto scivolano in posizione da soli, senza bisogno di ulteriori lavorazioni. L'opinione prevalente sulla nuova tecnologia è questa: avremmo dovuto pensarci prima." Ciò vale anche per gli addetti alla produzione, il cui numero si è ridotto a quattro o cinque nell'esercizio su un turno: "In quest'area il nuovo metodo di lavoro è molto apprezzato, perché salvaguarda la schiena e le ginocchia", spiega Johannes Strobel. "Un dipendente mi ha confidato che, dopo l'implementazione, non torna più a casa stanco morto ogni sera. Questo mi lascia ben sperare che lui e gli altri possano restare ancora a lungo con noi. E se dovessi riepilogare il risultato ottenuto a Ebenweiler, direi così: "Tutti gli obiettivi raggiunti!" Produciamo con maggiore precisione, abbiamo alleviato il problema della penuria di personale e abbreviato drasticamente i tempi di produzione. La nuova tecnologia piace anche ai clienti, che accolgono con favore la sicurezza che deriva dalla precisione industriale e dalla documentazione automatica delle operazioni di costruzione. Tuttavia, questa nostra riorganizzazione non verrà pubblicizzata, perché la quasi totalità dei clienti proviene ancora dalla gestione dei referral. E molti elementi ci fanno pensare che sarà così ancora per molto tempo.
«È incredibile quanto siano andate veloci le cose e quanto tempo abbiamo guadagnato in fase di produzione. Abbiamo raggiunto il 30% preannunciato da WEINMANN partendo da zero, e ora il dato dovrebbe essere ancora migliore, perché abbiamo una maggiore familiarità con i procedimenti di lavoro.»Johannes Strobel, amministratore di Strobel GmbH
Strobel GmbH
Strobel GmbH, con sede a Ebenweiler nel circondario di Ravensburg, in Germania, produce elementi strutturali in legno per pareti, soffitti e tetti, nonché altri componenti in legno per l'impiego nei più svariati progetti di costruzione, come edifici a più piani, asili, scuole e progetti di ristrutturazione. Nel 1987 Alfons Strobel dà inizio all'attività nel garage di casa sua. Nel 1990 l'impresa si trasferisce nella zona industriale e nel 2016 Johannes Strobel affianca il padre nella gestione, dopo aver superato l'esame di mastro artigiano. Oggi l'azienda ha quattro grandi capannoni e occupa una superficie di circa 11.000 metri quadrati. Dà lavoro a 45 dipendenti, cinque dei quali apprendisti.
Maggiori informazioni