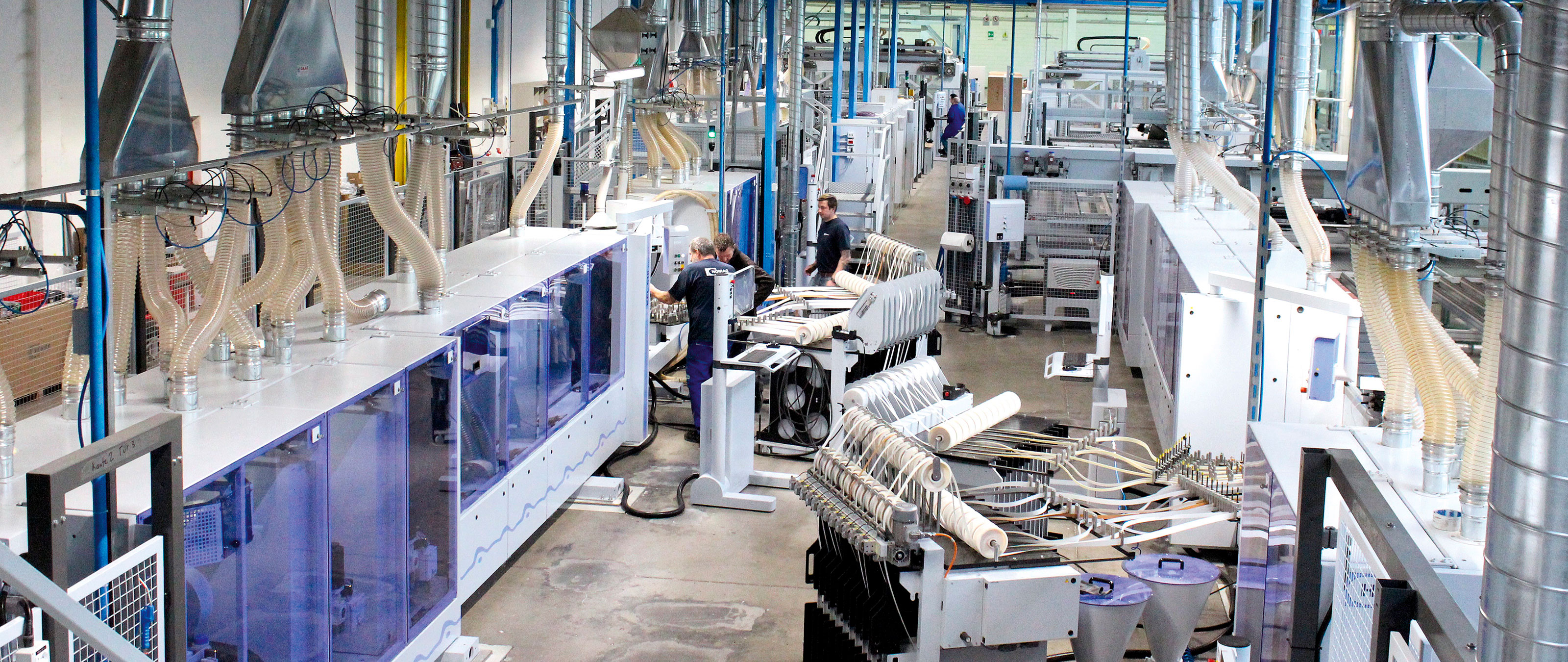
Ein Artikel des Fachmagazins möbelfertigung, Ausgabe 03/2017. Hier lesen Sie den Artikel auf möbelfertigung online.
Mit einem Terminal eine komplette Produktionsstraße steuern und die Produktion visualisieren – das gelingt mit der neuen Zellensteuerung „Woodflex“ der HOMAG Group. Baco, das konzerneigene Zulieferunternehmen der Battistella Company aus Italien, ist einer der ersten Anwender, bei dem die Steuerung installiert wurde – auf einer im letzten Jahr gelieferten Zelle zur vierseitigen Kantenbearbeitung für Kleinserien und Losgröße 1, die 6.000 Teile pro Schicht bewältigt.
Einen Meilenstein in der Steuerung intelligenter und vernetzter Maschinen setzt die HOMAG Group mit der im März endgültig abgenommenen, neuen Produktionsanlage bei Baco, einem Produktionsunternehmen der Battistella Company. Denn die im vergangenen Jahr gelieferte und in Betrieb genommene Kantenzelle verfügt nicht nur über maschinenbauliche Highlights, sondern zeichnet sich durch den Einsatz von „Woodflex“, eine neuartige Zellensteuerung, aus.
Dass die Battistella Company auf diesen technischen Vorsprung setzt, kommt nicht von ungefähr: Bereits seit der Gründung im Jahr 1953 in Pieve di Soligo durch Alfredo Battistella ist die Geschichte des Unternehmens immer wieder dadurch geprägt, dass modernste Technik zum Einsatz kam – oftmals als Vorreiter in ganz Italien. Allein die Gründung von Baco als firmeneigenes Produktionsunternehmen im Jahr 1996, um die Marken Battistella und Novamobili qualitativ zu pushen und hochgradig effizient zu fertigen, war mutig und visionär.
Dieses zukunftsgerichtete Denken ist letztlich das Erfolgsrezept von Battistella – auch heute noch, da Enkel Alberto als dritte Generation nach Mario Battistella die Geschicke des Wohn-, Kinder-, Jugend-, Büro- und Kastenmöbelproduzenten mitbestimmt. Und es begrenzt sich nicht nur auf eine moderne Produktion, sondern auch ein hervorragendes Möbeldesign, wie bei den Programmen „Nidi“ oder „Cinquanta3“ und eine erstklassige Vermarktung in Möbelhäusern und dem eigenen Novamobili-Flagship-Store in Mailand.
Rund 90 Mio. Euro erwirtschaftete die Battistella Company im Jahr 2016 mit beiden Marken, 80 Prozent davon im In- und 20 Prozent im Ausland – mit steigender Tendenz im Export. Etwa 450 Mitarbeiter gehören dem Unternehmen an, wobei Battistella seit 2014 hier auf ein besonderes Rotationsprinzip setzt: Je nach Auslastung pendeln Angestellte zwischen den Tochterunternehmen Baco, Battistella und Novamobili. Zumindest dort, wo es aufgrund der individuellen Anforderungen möglich ist.
Als es um die Investition in eine neue, vierseitige Kantenanlage bei Baco ging, waren die Ansprüche des Produktionsunternehmens klar: „Wir wollten mehr Flexibilität in der Produktion, die Qualität weiter steigern und vor allem die Kapazitäten erhöhen, um für die Anforderungen der Zukunft gerüstet zu sein“, erklärt Demis Marsura, Betriebsleiter bei Baco, der spürbar stolz ist auf die neue Anlage. Nach einigen Gesprächen mit verschiedenen Maschinenlieferanten fiel die Entscheidung letztlich zugunsten der HOMAG Group. Unter anderem auch, weil bei Baco als erstem italienischen Unternehmen „Woodflex“ zum Einsatz kommen sollte.
„Wir produzieren ganz individuelle Teile in Losgröße 1, vorwiegend aber sehr flexible Kleinlose an Halbfertigteilen für das Lager. Was bedeutet, dass wir in der Regel auftragsbezogen Wochenlose zusammenfassen, diese verschnittoptimiert zuschneiden und in Stapeln weiterverarbeiten.“
Bislang wurde je nach Kommission oder sogar Stapel entschieden, auf welcher Anlage bekantet wird. Die neue Anlage, die aus drei Format- und Kantenanleimmaschinen der „K600er“-Baureihe und modernster technologischer Ausstattung besteht, sollte Abhilfe schaffen, indem sie für jede eventuell zu produzierende Variante gerüstet ist. Was im Falle von Baco rund 9.000 Varianten sind, die sich durch rund 75 Dekore, 9 Dicken zwischen 8 und 50 Millimeter und diverse Bauteilabmessungen ergeben. Verarbeitet werden vorwiegend melaminbeschichtete Holzwerkstoffträger, einen kleinen Teil der Bauteile lackiert Novamobili in der Sonderteilfertigung in Pieve di Soligo in Norditalien selber.
Die Werkstücke werden der HOMAG-Group-Kantenzelle mit einem Beschicksystem „Power TBH 510“ in Kleinserienstapeln oder Losgröße 1 zugeführt. Anschließend folgt die Kantenverleimung mit EVA. Auf den beiden Maschinen der Baureihe „KF610“ sind aktuell zwei Leimbehälter aufgebaut, die für schnellen Farbwechsel sorgen. Sollte Baco in der Zukunft auch „Lasertec“ einsetzen wollen, so sind die Maschinen bereits jetzt dafür gerüstet. Nach der Längsbearbeitung werden die Bauteile über ein Kurvenband und einer Winkelübergabe der Querbearbeitung zugeführt. Diese Kantenanleimmaschine der Baureihe „KF624“ ist ebenfalls mit zwei Leimbehältern versehen. Alle Maschinen besitzen ein 24-fach-Kantenmagazin.
Im Anschluss dreht eine Drehstation „Power TD 530“ alle Bauteile wieder in Längsrichtung für das nachfolgende Abstapel-System „Power TSH 510“.
Ein hoher Grad der Vernetzung in der Produktion war für Battistella schon immer wichtig. Über sein Fertigungsleitsystem kann Marsura minutengenau in Echtzeit nachvollziehen, was wo auf welcher Anlage gerade entsteht, wie viele Soll- und Ist-Teile beziehungsweise Ausschuss es gibt und zu welcher Kommission und welchem Auftrag die jeweiligen Teile gehören.
Die Einzelteile eines jeden Möbelstücks liegen dafür jeweils als Datensatz vor – bei Prototypen wird geprüft, ob vorhandene Daten genutzt oder neue Datensätze für alle notwendigen Prozessschritte erstellt werden müssen. Die einzelnen Werkstücke durchlaufen die Produktion dann mittels Barcode-Identifikation – bei Einzelteilen für Losgröße 1 oder bei kompletten Stapeln mit unterschiedlichen Stückzahlen. Die Barcodes werden für jeden Prozessschritt eingelesen und nach erfolgter Bearbeitung mit einem neuen Identifikationscode versehen, dessen Erstellung gleichzeitig die Fertigungsrückmeldung ist.
Die Zellensteuerung „Woodflex“ sorgt für absolute Transparenz der gesamten Anlage in allen Zellen und Sektionen, wie beispielsweise der Transporteinheit, der Kantenzelle oder der Abstapelung. Auch die einfache Analyse und Optimierung des Produktionsablaufs wird mit „Woodflex“ erreicht. Benutzer bekommen so die Chance einer deutlichen Produktivitätssteigerung durch optimale Berechnung des minimalen Teileabstandes oder schnellere Beseitigung von Störungen sowie einer permanenten Sicherung des Anlagenzustandes mit der Möglichkeit, Fehler wesentlich schneller zu beheben.
Eine Visualisierung des Teileflusses in Echtzeit und die kontinuierliche Rückmeldung der Werkstückproduktion gibt wichtige Aufschlüsse über den Bearbeitungsstand einzelner Aufträge. Punkte, die Masura auch deutlich als Vorteile hervorhebt: „Wir wissen jederzeit um den Zustand der gesamten Anlage, das Ampelsystem erleichtert die Visualisierung. Gibt es einen Fehler, beispielsweise einen gedrückten Not-aus-Knopf oder eine offene Tür, so ist das auf einen Blick ersichtlich, und der Maschinenbediener kann Abhilfe schaffen.“ Wobei sich Baco noch lange nicht am Ende der Möglichkeiten sieht: „Aktuell lernen wir noch. Wir loten gerade aus, wie wir welche Funktionen optimal für uns nutzen können und wie die Auswertung von Informationen aus der Zelle zu einer weiteren Erhöhung der Produktivität beiträgt. Sehr positiv ist auf jeden Fall die Tatsache, dass die Maschinenbediener durch ,Woodflex’ grundsätzlich entlastet werden, die Wahrscheinlichkeit von Fehlern sinkt deutlich.“ Insofern verwundert es nicht, dass sich der Italiener für jede der Produktionsstraßen eine solche Zellensteuerung wünschen würde: „Wenn es technisch möglich wäre und Sinn macht, dann würden wir auf jeden Fall nachrüsten. ,Woodflex’ ist ein gutes und vor allem wertvolles Tool.“
Auf der „Ligna“ 2013 kam es zu den ersten intensiven Gesprächen zu der Anlage. Nach der Projektierungszeit und dem Bau der Maschinen wurde es dann im Jahr 2016 konkret. Ab Anfang Juni rollten insgesamt 25 Lkw über die Alpen. Der Platz in der Halle war zu diesem Zeitpunkt schon leer. Trotzdem war es eine logistische Meisterleistung die Produktionsstraße in die Halle zu bringen – bei laufendem Betrieb und einem mittigen, umbauten Standort. Entsprechend der Fertigstellung der Einzelkomponenten in Schopfloch und Hemmoor hielt mit der „KF624“ erst der größte Maschinenteil Einzug, danach die beiden Längsmaschinen und später alle Handlingseinheiten. Bereits Mitte September wurde das erste Teil gefahren, der offizielle Produktionsstart erfolgte im November. Marsura zeigt sich mit den Abläufen insgesamt sehr zufrieden. „Natürlich gab es auch immer wieder Probleme – immerhin ist es eine Pilotanlage. Doch in enger Zusammenarbeit mit dem Projektleiter Wolfgang Kläger von der HOMAG-Business-Unit ,Systems’ und den HOMAG-Teams aus Deutschland und Italien wurden alle Probleme zügig analysiert und behoben. Auch die Schulungseinheiten haben gut funktioniert, wir fühlen uns insgesamt sehr gut betreut. Mein Fazit zum jetzigen Zeitpunkt fällt ausgesprochen positiv aus. Und wenn wir letztlich so produzieren, wie wir es im Vorfeld projektiert haben, dann kann ich von einer idealen Anlage sprechen.“
Ideal auch darum, weil neben der größtmöglichen Automatisierung Battistellas Wunsch nach manueller Bestückung und Abstapelung entsprochen wurde. „Automatisierte Prozesse sind wichtig – noch wichtiger ist uns aber die Stabilität einer Anlage. Wenn wir ausschließlich automatisch anliefern oder Werkstücke entnehmen, dann würde die Anlage bei einem Problem in diesem Bereich komplett ausfallen. Das kann uns nicht passieren, da wir auch manuell zugreifen können.“
Die neue Anlage, die zwei bis drei Bediener benötigt, läuft bei Baco im Zweischichtbetrieb mit einem Vorschub von 40 Metern pro Minute in der Längsbearbeitung sowie 30 Metern pro Minute in der Querbearbeitung. Das Leistungsvermögen umfasst dank modernster Aggregate-Technik letztlich bis zu 6.000 Teile pro Schicht und könnte damit schon fast allein das Volumen von 13.000 Teilen liefern, die aktuell das Werk verlassen – ein deutlicher Hinweis darauf, wie sehr Baco seine Kapazitäten erhöht hat.
Ein Bericht von Doris Bauer.
Videos
Bitte bestätigen Sie, dass bei der Nutzung von YouTube Daten wie Ihre IP-Adresse, Browser-Kennung und ähnliches an Google übermittelt werden können.
» Datenschutzerklärung
Battistella Company: Hochwertige Möbel in Losgröße 1 mit Zellensteuerung woodFlex
„Aktuell lernen wir noch. Wir loten gerade aus, wie wir welche Funktionen optimal für uns nutzen können und wie die Auswertung von Informationen aus der Zelle zu einer weiteren Erhöhung der Produktivität beiträgt. Sehr positiv ist auf jeden Fall die Tatsache, dass die Maschinenbediener durch ,Woodflex’ grundsätzlich entlastet werden, die Wahrscheinlichkeit von Fehlern sinkt deutlich.“Demis Marsura, Betriebsleiter bei Baco.