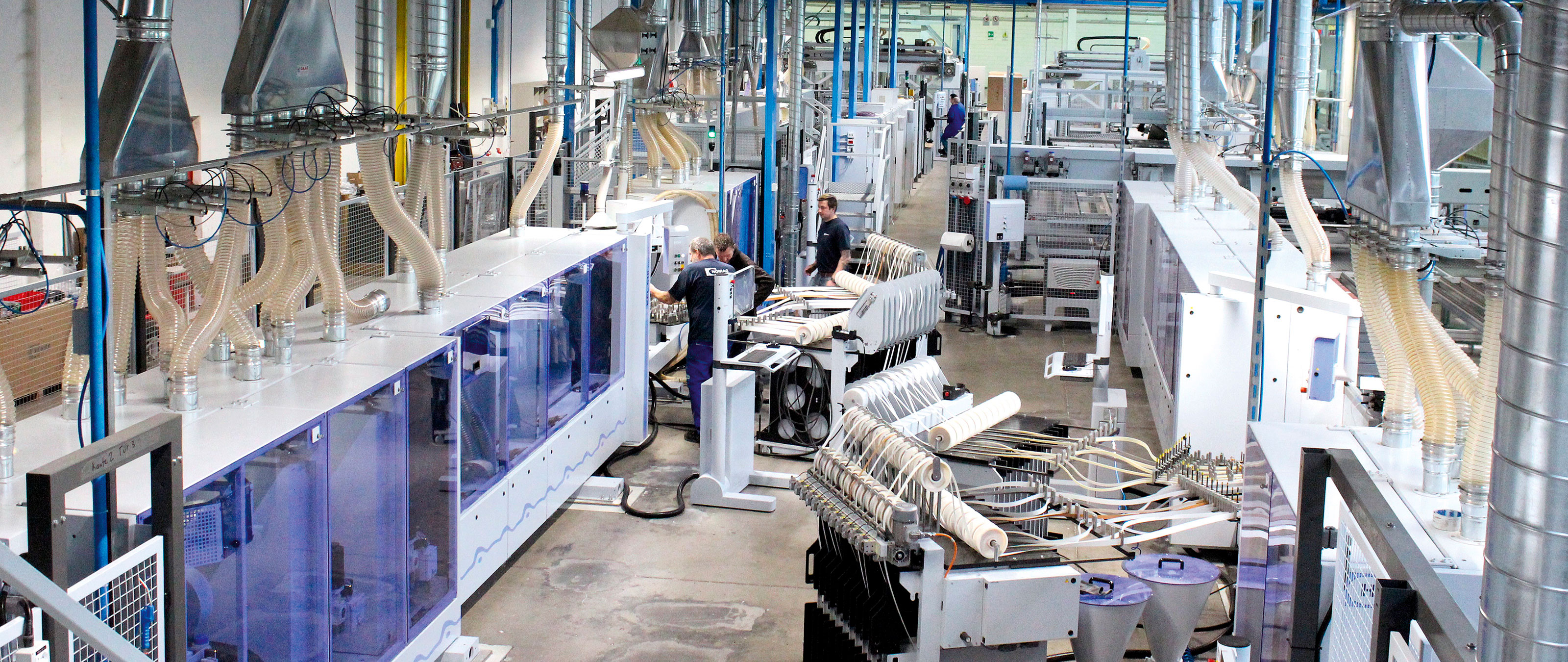
Un articolo di "Fachpresse Möbelfertigung". Edizione 03/2017
Gestire con un unico terminale una linea di produzione completa e visualizzare la produzione – questo si ottiene con il nuovo comando dell’isola di produzione “Woodflex” di Homag Group. Baco, fornitore interno di Battistella Company in Italia, è la prima azienda ad avere installato il comando. Sulla linea fornita lo scorso anno per la bordatura su quattro lati per piccole serie e Lotto 1 si producono 6.000 pezzi / turno.
Una pietra miliare nel comando di macchine intelligenti e collegate che Homag Group pone con il collaudo finale in marzo della nuova linea di produzione presso Baco, divisione produttiva di Battistella Company. La linea di bordatura fornita e messa in funzione lo scorso anno dispone non solo di Highlights costruttivi, ma si distingue anche per l’impiego di “Woodflex”, uno dei più innovativi comandi di isole di produzione. Che Battistella Company si porti in vantaggio tecnico, non è un caso: già dalla sua fondazione nel 1953 a Pieve di Soligo grazie ad Alfredo Battistella, la storia dell’azienda è sempre più caratterizzata dall’impiego delle tecniche più moderne – spesso come precursori in tutta Italia. Già la fondazione di Baco come propria azienda produttiva nel 1996, per spingere qualitativamente i marchi Battistella e Novamobili e per produrre con un altro grado di efficienza, è stata coraggiosa e visionaria. Questo pensiero futuristico è alla fine la ricetta per il successo di Battistella – ancora oggi con il nipote Alberto, terza generazione dopo Mario Battistella, influenza l’andamento dei produttori di mobili da soggiorno, camere da bambino e teen-ager, mobili da ufficio modulari e componibili. E non si limita solo ad una moderna produzione, ma anche eccellenti mobili di design come nella gamma “Nidi” o “Cinquanta3” ed una commercializzazione di prima classe nei mobili da interni nel proprio Flagshipstore Novamobili a Milano.
Circa 90 mil. Euro è il fatturato complessivo di Battistella Company nel 2016 con entrambi i marchi, del quale 80% mercato interno e 20% all’estero, con una tendenza all’aumento nell’export. Quasi 450 i dipendenti delle aziende del gruppo, dove Battistella dal 2014 ha introdotto un principio di rotazione: in base ai carichi di lavoro i dipendenti si alternano nelle società Baco, Battistella e Novamobili, per lo meno dove le capacità individuali lo permettono. Quando si è trattato di investire in un impianto di bordatura per la lavorazione sui quattro lati, le richieste della società erano chiare: “vogliamo maggiore flessibilità nella produzione, incrementare ulteriormente la qualità ed innanzitutto aumentare la capacità, per essere preparati alle future richieste” spiega Demis Marsura, direttore di stabilimento presso Baco, evidentemente orgoglioso del nuovo impianto. Dopo alcune consultazioni con diversi fornitori di macchinari, la decisione in ultima analisi è caduta a favore di Homag Group. Anche perché Baco sarebbe stata la prima azienda in Italia ad impiegare “Woodflex”.
“Produciamo elementi molto individuali a Lotto 1, principalmente in piccole serie molto flessibili su pezzi semi-lavorati per il magazzino. Ciò significa che noi di regola consegnamo lotti settimanali in base agli ordini, ottimizziamo i tagli e proseguiamo con l’accatastamento.” Sinora si decideva in base alla commessa o alla catasta, su quale impianto bordare. Il nuovo impianto composto da tre squadrabordatrici della serie K600 e della più moderna dotazione tecnologica dovrebbe aiutare, essendo attrezzato per ogni eventuale variante da produrre. Per quanto riguarda Baco risultano circa 9.000 varianti che consistono in 75 decori, 9 spessori tra 8 e 50 mm e diverse dimensioni degli elementi. Vengono lavorati principalmente pannelli rivestiti in melamina, una piccola parte degli elementi vengono laccati da Battistella stessa a Pieve di Soligo (Veneto – Italia del nord). I pezzi vengono alimentati all’isola di bordatura di Homag Group con un caricatore “TBH 510” in cataste di piccole serie o lotti 1. Segue la bordatura con colla EVA. Su entrambe le macchine della serie “KF610” sono attualmente montati due contenitori colla che provvedono al veloce cambio colore. Se in futuro Baco dovesse voler inserire la tecnica “Lasertec” le macchine sono già attrezzate per questa soluzione. Dopo la bordatura longitudinale gli elementi, mediante un nastro a curva ed un traslatore angolare, vengono condotti alla bordatura trasversale. Anche questa bordatrice della serie “KF624” è provvista di due contenitori colla. Tutte le macchine possiedono un magazzino bordi da 24 rotoli. Dopo di ciò la stazione di rotazione “Power TD 530” ruota tutti gli elementi di nuovo in direzione longitudinale per il successivo sistema di accatastamento “Power TSH 510”. Un alto grado di collegamento nella produzione era da sempre fondamentale per Battistella. Mediante il suo sistema di gestione di produzione il Sig. Marsura può conoscere al minuto in tempo reale, cosa, dove e su quale impianto si sta producendo, la quantità teorica e reale dei pezzi e/o degli scarti e a quale commessa o ordine gli stessi pezzi appartengono.
I singoli elementi di un particolare del mobile sono presenti come record di dati – con prototipi viene verificato, se i dati esistenti sono utilizzabili oppure se devono essere creati nuovi record di dati per tutti i passi necessari al processo. I singoli pezzi attraversano i passaggi della produzione, poi mediante codice a barre identificativo per i singoli elementi del Lotto 1 oppure per catasta completa con lotti diversi, i codici a barre vengono letti ad ogni passo del processo e dopo l’avvenuta lavorazione sono provvisti di un nuovo codice identificativo che viene generato in contemporanea all’avviso di pronto produzione. Il comando dell’isola di produzione “Woodflex” provvede all’assoluta trasparenza sull’intero impianto, in ogni sua isola e sezione come ad es. l’unità di trasporto, la bordatura o l’accatastamento. Anche la semplice analisi e l’ottimizzazione del ciclo di produzione vengono ottenuti grazie a “Woodflex”. Gli operatori hanno quindi modo di incrementare significativamente la produzione grazie al calcolo ottimale delle distanze minime tra i pezzi, di eliminare velocemente i guasti come pure assicurare permanentemente lo stato dell’impianto con la possibilità di risolvere rapidamente l’errore.
La visualizzazione del flusso di pezzi in tempo reale e la continuità degli avvisi sulla produzione consentono l’importante aggiornamento sullo stato della lavorazione di ogni singolo ordine. Argomenti che Marsura evidenzia come chiari vantaggi: “siamo sempre a conoscenza dello “Status” dell’impianto complessivo, il sistema a semaforo facilita la visualizzazione. Ad esempio viene subito segnalato se c’è un guasto, un tasto di emergenza premuto o una porta di sicurezza aperta - l’operatore può intervenire”. Baco però non vede la fine delle sue possibilità: “attualmente stiamo ancora imparando. Stiamo verificando come e quali funzioni sfruttare in modo ottimale e come la valorizzazione delle informazioni provenienti dall’isola di lavorazione aiuta ad aumentare ulteriormente la produttività. Molto positivo è comunque il fatto che gli operatori macchina grazie a “Woodflex” sono sensibilmente sollevati dalla riduzione di probabilità di guasti. Per questo non meraviglia che gli italiani vorrebbero tale comando per ogni linea di produzione: “se fosse possibile tecnicamente e ne valesse la pena, lo installeremmo successivamente in ogni caso. “Woodflex” è un ottimo utensile, ma soprattutto di grande valore”. Alla “Ligna 2013” si giunse al primo intensivo colloquio per l’impianto. Con i tempi di progettazione e la costruzione effettiva dei macchinari, esso si è concretizzato nel 2016. Da inizio luglio dello scorso anno, in totale 25 bilici hanno attraversato le Alpi. Il capannone in quel momento era già vuoto. Nonostante ciò è stata un’impresa logistica piazzare la linea nella fabbrica, con la produzione ancora in funzione ed erigere il cantiere al centro dello stabile. Corrispondentemente all’approntamento dei singoli componenti a Schopfloch ed Hemmor veniva caricata prima la parte più grande della “KF624”, poi entrambe le macchine longitudinali ed infine le unità di automazione. Già a metà settembre veniva lavorato il primo pezzo, l’avvio di produzione ufficiale fu in novembre. Marsura si dimostra nel complesso soddisfatto dello svolgimento. “Ovviamente ci sono state difficoltà – considerato poi che si tratta di un impianto pilota. Ma in stretta collaborazione con il responsabile progettista Wolfang Kläger di HOMAG-Business Unit “Systems”, con i team di HOMAG in Germania ed in Italia i problemi venivano analizzati e risolti con rapidità. Anche l’aspetto addestramento ha funzionato bene, ci sentiamo complessivamente ben assistiti. La mia conclusione a questo punto è molto positiva. E se alla fine potremo produrre come era stato a suo tempo preventivato, potrò allora parlare di un impianto ideale.”
Ideale anche perché accanto alla grande potenzialità di automazione, il desiderio di Battistella di attrezzaggio e accatastamento manuale è stato corrisposto. “I processi automatizzati sono importanti – ma ancora più fondamentale è la stabilità dell’impianto. Se il carico o il prelievo dei pezzi avvenisse solo in automatico, nel caso di un guasto in questo settore l’impianto si fermerebbe completamente. Questo non può accadere da noi, dato che possiamo intervenire manualmente”.
Il nuovo impianto che necessita di due/tre operatori lavora in Baco su due turni con un avanzamento di 40 m/minuto nella lavorazione longitudinale e a 30 m/minuto in quella trasversale. La performance infine comprende fino a 6.000 pezzi a turno e potrebbe quindi da sola fornire il volume di 13.000 pezzi che attualmente lascia lo stabilimento – una nota importante a questo proposito, è quanto Baco ha incrementato la propria capacità.
Doris Bauer, Möbelfertigung
«Attualmente stiamo ancora imparando. Stiamo verificando come possiamo utilizzare le varie funzioni in modo ottimale per noi e come la valutazione delle informazioni dell'isola contribuisce ad un ulteriore aumento della produttività. Molto positivo è in ogni caso, che grazie a Woodflex il carico di lavoro degli operatori della macchina viene diminuito e la probabilità di errori si abbassa notevolmente.»Demis Marsura, direttore di stabilimento presso Baco.