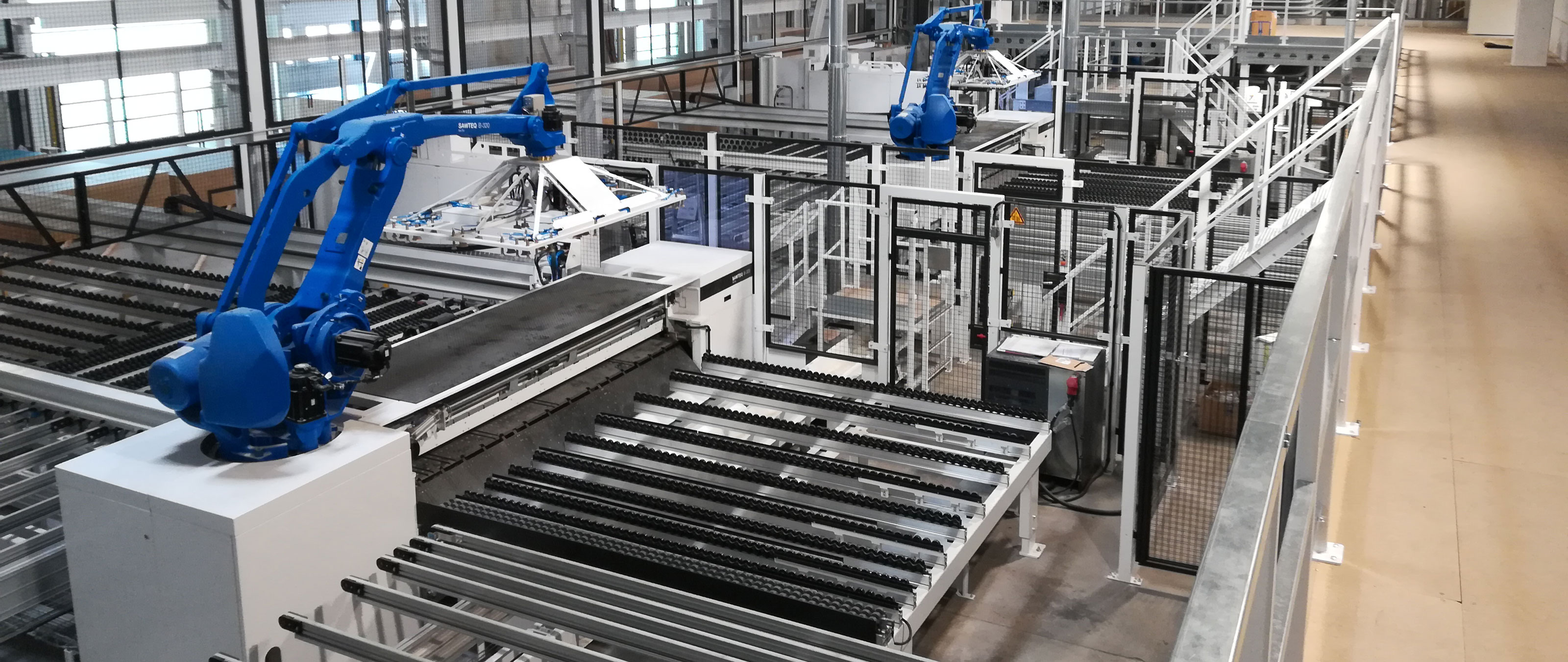
Hochwertige Küchen seit über 100 Jahren
Die Burger Küchenmöbel GmbH blickt auf eine über 100-jährige Historie zurück. Die Anfänge liegen in den 1910er-Jahren mit der handwerklichen Fertigung von Küchenmöbeln durch Otto Aßmann. In den 1950ern stieg das in Ostdeutschland angesiedelte Unternehmen in das Exportgeschäft — unter anderem in die damalige BRD, die Niederlande und die Sowjetunion — ein. Durch die Etablierung der Einbauküche im Laufe der Wirtschaftswunder-Jahre stellte auch Burger seine Produktion auf den Trend um, der den heutigen Standard darstellt. Anfang der 90er schloss man sich mit Bauformat zusammen und entwickelte sich stetig weiter.
Burger fertigt aktuell die Produktlinien „Trend" und „Linea", die im hochwertigen Basis-Segment anzusiedeln sind und sich vor allem in der Varianz des Korpus-Rasters, des Frontenprogramms und der angebotenen Griffe unterscheiden. Kunden können hier zwischen 14 Korpus-Dekoren und über 180 Frontenmodellen wählen. Die Oberflächen der Fronten werden mit Kunststoffdekoren, Furnier und farbiger Lackierung angeboten. Neben den Küchenschränken vertreibt Burger auch integrierte Elektrogeräte unter einer Eigenmarke. Der Vertrieb des Produktportfolios wird dabei zum großen Teil über kleinere Küchenstudios im B2C-Geschäft abgewickelt. Vereinzelt findet der Absatz auch über Projektgeschäfte statt. Burger erwirtschaftete 2018 zusammen mit Bauformat einen Umsatz von 240 Mio. Euro. Das Produktionsvolumen lag dabei bei rund 140 000 Küchen, die mit etwa 1 000 Mitarbeitern hergestellt wurden. Das entspricht einem Schnitt von 650 Küchen pro Tag, was in etwa 7 000 Schränke sind. Davon werden 5 000 bei Burger in Burg (dreischichtig) und 2 000 bei Bauformat in Löhne (einschichtig) produziert.
Smarte, individuelle Fertigungszellen
Burger ist ein sehr gut organisierter Betrieb und verfügt über eine gut funktionierende und ausgeklügelte Logistik. Die Organisation wird durch das MES bestens unterstützt. Der Maschinenpark ist hochmodern und allgemein sind keine großen „Fehler" im Produktionsablauf ersichtlich. In den letzten Jahren wurden die Prozesse bei Burger Küchen konsequent automatisiert und optimiert. Bis vor wenigen Jahren wurden bei Burger nur 1 000 Teile pro Tag auftragsbezogen produziert. Mittlerweile fertig Burger 8 000 Fronten- und Korpus-Teile auftragsbezogen in flexiblen und hochautomatisierten Fertigungszellen. Auch der Sortierprozess der Fronten wurde erfolgreich automatisiert. Dabei setzt Burger immer auf smarte individuelle Fertigungszellen. In einer Roboterzelle werden alle Fronten, die aus unterschiedlichen Quellen stammen (JIT-Zukaufs Fronten, Frontenlager, auftragsbezogene Fertigung etc.) vom Tetris-Stapel in die Frontenwägen kommissioniert. Der große Vorteil des automatisierten Prozesses ist die Vollständigkeitskontrolle und die Vermeidung von Fehlern beim Sortierprozess. Die Einsparung von Personal muss hier auch erwähnt werden. Die Frontenwägen werden dann den Bearbeitungszentren mit Roboterbeschickung zugeführt, wo die Beschlagsbohrungen durchgeführt und die Beschläge automatisch gesetzt werden. In naher Zukunft soll der Transport zwischen den Zellen mit fahrerlosen Transportsystemen optimiert werden.
Trotz dieses soliden Fundaments konnten in der Vergangenheit die anvisierten Kapazitäten nicht erreicht werden. Deshalb wurde das Projekt „5 000" ins Leben gerufen. Bei diesem Projekt sollte SCHULER Consulting Burger Küchen erneut unterstützen. Um die Ursache des Verfehlens der Kapazitätsziele zu analysieren, liegen bei Burger die gleichen Steine wie den meisten anderen Unternehmen im Weg. Mit den Jahren schleicht sich eine Art „Betriebsblindheit" ein, die es oftmals nicht ermöglicht, objektiv aus der Vogelperspektive heraus Probleme zu identifizieren, zu analysieren, richtig zu interpretieren und schließlich daraus Optimierungsmaßnahmen abzuleiten. Das Projekt „5 000" sollte an dieser Stelle Abhilfe schaffen. Mit der Unterstützung von SCHULER Consulting wollte man die Ursachen der nicht erreichten Kapazitätsziele identifizieren und eine Strategie zur Optimierung entwickeln.
Kleine Änderungen bringen große Wirkung
Wie es in einem gut organisierten Betrieb zu erwarten ist, gibt es bei Burger keine gravierenden Mängel. Es sind vielmehr viele kleine Probleme, die sich im Laufe der Zeit im betrieblichen Alltag eingeschlichen haben und mit der Zeit unter der Parole „Das war schon immer so!" abgefertigt werden. Die Hauptprobleme liegen dabei in den Bereichen der Wartung, Arbeitsorganisation, Synchronisierung der Fertigungsprozesse sowie des Qualitäts- und Fehlermanagements. Bei der Wartung liegt das Problem hauptsächlich bei den „Schlüssel-Maschinen". Diese sind zwischen fünf und zwölf Jahre alt. Das Problem ist weniger das Alter als die fehlende vorbeugende Instandhaltung. Dadurch kam es immer wieder zu unvorhersehbaren Ausfällen, die schließlich die Produktionsplanung durcheinander brachten. Um dem vorzubeugen, wurden Maßnahmen ausgearbeitet, die diese Probleme minimieren. Hierzu zählt das konkrete Aufzeigen von Instandhaltungsdefiziten und die Vorausplanung der Instandhaltung mit der Nutzung von Zeiten der Betriebsruhe. Die Umsetzung der Maßnahmen an verschiedenen Problemschwerpunkten konnte die Kapazität bereits erheblich erhöhen, doch muss der eingeschlagene Weg — die Optimierung der Instandhaltung — konsequent und kontinuierlich weitergeführt werden.
Ein weiteres Optimierungspotenzial war in der Qualität und der Nachfertigung zu finden. Im Lean-Ansatz gilt es, kontinuierlich im Produktionsablauf die Qualität zu überwachen, um möglichst wenig Wertschöpfung an fehlerhafte Teile zu verlieren und somit Verschwendung zu vermeiden. Bei Burger wurde dieser Lean-Gedanke in der kompletten Logistikkette konsequent umgesetzt, damit alle Teile fehlerfrei in der richtigen Qualität zum richtigen Zeitpunkt am Montageband ankommen. Eine konsequente Einstufung in A/B-Qualitäten hilft auch kleinere Mängel direkt vor Ort zu beheben. Ein Korpus mit einer defekten Front beeinflusst die Leistung der Fabrik mit einem Faktor von zwei bis vier des ursprünglichen Aufwands. Diese Maßnahmen wurden bereits umgesetzt, müssen jedoch noch weiter vorangetrieben werden.
Den Nachfertigungsprozess hat man optimiert und beschleunigt. Von einem defekten Teil wird sofort ein Nachfertigungsauftrag erstellt, wenn es als defektes Teil identifiziert ist und vor allem, wenn es sich um ein auftragsbezogenes Teil handelt. Somit werden die Fehler bereits in vorgelagerten Prozessen erkannt und es können die Nachfertigungsaufträge rechtzeitig zum Montagetermin fertiggestellt sein. Somit wird eine vollständige Montage ohne Fehlteile ermöglicht. Um dieses Vorgehen erfolgreich umzusetzen, ist ein definierter Ablauf der Nachfertigung essenziell. Der Ablauf wurde bei Burger definiert und konsequent realisiert. Hier gilt es, definierte Abläufe und Zeitplanung abteilungsübergreifend und diszipliniert einzuhalten. Das kann nur mit der notwendigen Disziplin und Kontinuität durchgeführt werden.
Durch Abstimmung der Taktzeiten entlang der Endmontagelinien und durch Synchronisierung der Prozesse konnte die Produktivität erheblich gesteigert werden. Durch eine detaillierte Kapazitätsplanung vor den Endfertigungsabrufen konnte auf Engpässe an bestimmten Fertigungsprozessen rechtzeitig reagiert werden, um die Zyklen-Zeiten an den Montagelinien nicht negativ zu beeinflussen. In den automatischen Montagelinien fielen große Mengen an Beschlägen durchs „Raster" und wurden entsorgt, anstatt sie konsequent zu sammeln und sofort wieder in den Kreislauf zurückzuführen. Hierbei handelt es sich um Sockelelemente, Schubkastenclips und Topfbänder. Der hierdurch entstandene finanzielle Schaden lag im sechsstelligen Bereich. Um dem entgegenzuwirken, wurden die Ursachen behoben. Defekte Türen und Fronten stellten ein weiteres „schwarzes Loch" für Material dar. Die Menge an Türen und Fronten mit Defekten belief sich auf rund 350 bis 400 Stück pro Tag. Oftmals ist es jedoch möglich, diese defekten Teile wieder „gut zu schneiden", um sie erneut dem Produktionsprozess zuzuführen. Ziel ist es, 40 Prozent der Türen und Fronten zu retten und somit ein Einsparpotenzial von rund 1 Mio. Euro pro Jahr zu erreichen.
Der allgegenwärtige Fachkräftemangel schlägt sich bei Burger besonders in der Montage nieder. Es wird versucht, die mangelnden Fachkräfte durch Leiharbeiter zu ersetzen, jedoch ist mit nicht qualifizierten Arbeitern der Aufbau von eingespielten Teams nicht möglich. Hier wurde ein Projekt aufgesetzt, um qualifizierte und eingespielte Montageteams aufzubauen und langfristig zu halten. Bei diesem Prozess müssen die Führungskräfte konsequent am Aufbau der Teams beteiligt sein. Dabei ist Präsenz im Fertigungsbereich nötig, um unter anderem die Problematik der Arbeitszeiteinhaltung und den stetigen Produktionsfluss zu überwachen. Um hierfür Kapazitäten für die Führung zu schaffen, sind die administrativen Tätigkeiten zu reduzieren oder abzugeben.
Durch eine kontinuierliche Verbesserung in allen Fertigungsprozessen konnte die geplante Produktivitätssteigerung bei Burger sogar mit Verzicht auf eine dritte Schicht erzielt werden. Die erfolgreiche langjährige Zusammenarbeit zwischen SCHULER Consulting und Burger Küchen trägt Früchte. Es ist schön zu sehen, wie sich Burger Küchen in kürzester Zeit zu einem technologisch führenden Unternehmen weiterentwickelt hat.
Autor: Volker Jahnel, Senior Manager Europa bei SCHULER Consulting zuständig für die Bereiche Fabrikplanung und Losgröße-1.
Ein Artikel aus dem Fachmagazin HK Ausgabe 6/2019 Hier kommen Sie zum ganzen Artikel
Burger Küchen
Burger produziert mit rund 1000 Mitarbeitern etwa 140000 Küchen im Jahr. Trotz vorbildlicher Fertigungstechnik kam es immer wieder zu unvorhersehbaren Ausfällen, die schließlich die Produktionsplanung durcheinanderbrachten. Um dem vorzubeugen, wurden gemeinsam mit SCHULER Consulting Maßnahmen ausgearbeitet, die diese Probleme minimieren.
burger-kuechen.de