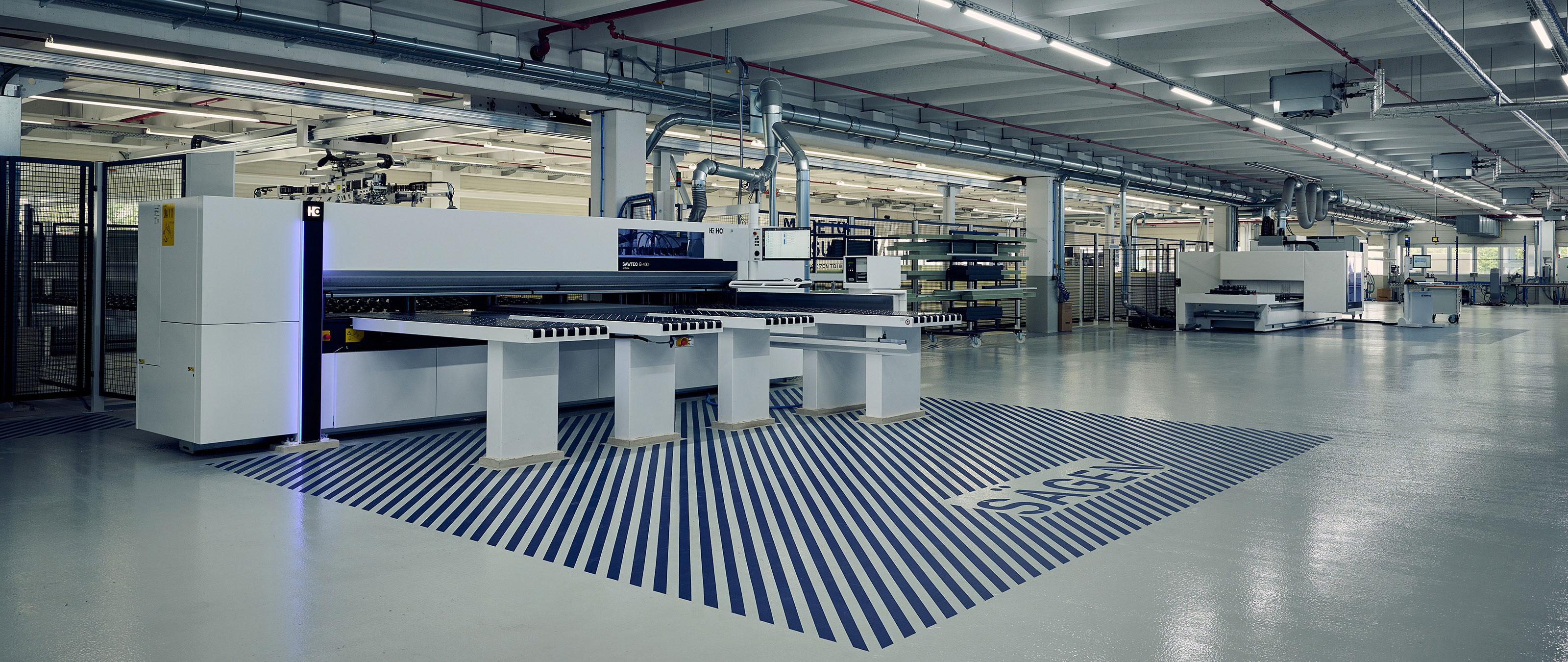
Okucia budowlane i meblowe, narzędzia, maszyny, środki bezpieczeństwa pracy, produkty chemii budowlanej i wiele innych — z ponad 120 tys. produktów w swoim asortymencie Meesenburg Großhandel KG to prawdziwy megastore dla klientów korporacyjnych z branży budowlanej i przemysłowej. Nie zawsze tak jednak było. Założone w 1758 roku przedsiębiorstwo w ciągu swojej historii wielokrotnie wprowadzało w życie nowe pomysły — tak jak obecnie. Najnowszy rozdział to nic innego jak transformacja z hurtowni do producenta również własnych innowacyjnych produktów. W roli głównej: nowo zainstalowane „Centrum produkcyjne Made to Measure HOMAG”.
Ojczyzną Meesenburg Großhandel KG jest daleka północ na granicy niemiecko-duńskiej. Założona ponad 260 lat temu we Flensburgu firma jest nadal własnością rodzinną i zajmuje się handlem artykułami żelaznymi, tak jak w momencie jej powstania. Ale to tyle w kwestii stałych. Przy bliższym poznaniu historia firmy Meesenburg okazuje się być pełna ciągłych zmian i przekształceń. Wszystko zaczęło się od artykułów żelaznych dla klientów z branży rolniczej, a w pewnym momencie dołączyły okucia i materiały montażowe do okien i drzwi, które do dziś charakteryzują asortyment — choć nie zawsze z taką dominacją jak dziś. „Kiedy ponad 30 lat temu przejąłem zarządzanie od mojego ojca, mieliśmy w ofercie również porcelanę i artykuły gospodarstwa domowego w naszych własnych domach towarowych” — wspomina właściciel Martin Meesenburg.
Wiodąca hurtownia materiałów montażowych i okuć budowlanych w Europie
Od tego czasu firma rozwinęła się w jedną z wiodących europejskich hurtowni materiałów montażowych i okuć budowlanych. Rodzinne przedsiębiorstwo generuje roczny obrót w wysokości około 330 milionów euro. Oprócz centrali we Flensburgu firma Meesenburg posiada w samych Niemczech 31 dalszych lokalizacji oraz oddziały w innych krajach europejskich. W sumie hurtownia zatrudnia ponad 1200 osób. „Z tym bilansem należymy do 100 najstarszych firm rodzinnych w Niemczech z rocznym obrotem ponad 100 milionów euro”, mówi Meesenburg i zaraz dodaje: „Jednak za tę dumną historię firmy nie możemy nic kupić. Musimy też być w stanie opłacić wszystkie koszty i pensje na koniec miesiąca. Jest to możliwe tylko wtedy, gdy odniesiemy sukces ekonomiczny i pokonamy konkurencję”.
Środowisko, w którym hurtownia i jej klienci muszą się odnaleźć, jest kształtowane przez megatrendy naszych czasów. Trzy najważniejsze: cyfryzacja, niedobór wykwalifikowanych pracowników i wielka kwestia zrównoważonego rozwoju. Firma Meesenburg stoi przed tymi wyzwaniami i postrzega je jako szansę. Tym samym przedsiębiorstwo konsekwentnie stawia na cyfryzację i już teraz generuje coraz większą część swoich obrotów online. „Opracowujemy produkty i systemy, aby spełnić wymagania rynku i zaoferować naszym klientom właściwe rozwiązanie” — mówi Robert Leinert, dyrektor ds. zarządzania produktem w firmie Meesenburg.
Nowość w ofercie: szyte na miarę akcesoria do okien i drzwi
Przykładem tego są innowacyjne produkty, które Meesenburg od niedawna produkuje w nowo zainstalowanym centrum produkcyjnym HOMAG w zakładzie w Bischofswerdzie. Impuls, który za tym stoi? W przypadku nowych budynków i energooszczędnych remontów podejmuje się wiele wysiłków technicznych, aby coraz lepiej izolować domy. Na przykład dzięki wysoce izolowanym elementom elewacji i oknom, które mają utrzymywać hałas na zewnątrz, a ciepło w środku — a przynajmniej tak mówi teoria. „W rzeczywistości wokół okien i drzwi budynku często występują ogromne szczeliny. Luki, przez które przenika dźwięk i ucieka ciepło — wyjaśnia Leinert. Przyczyną tego jest brak rozwiązań montażowych. W przeszłości firmy zajmujące się budownictwem po prostu wykonywały te połączenia konstrukcyjne na własną rękę, mniej lub bardziej improwizując. Było to kosztowne i mało efektywne energetycznie.
„Naszym celem jest wypełnienie tej luki na rynku i zaoferowanie naszym klientom precyzyjnie dopasowanych rozwiązań systemowych profili do zoptymalizowanego energetycznie montażu okien i drzwi”, wyjaśnia Leinert. W tym celu zespół skupiony wokół managera produktu stopniowo rozwijał całe portfolio produktów. Spektrum sięga od izolacji podstawowej i profili adaptacyjnych, poprzez profile łączące do parapetów i poszerzenia ościeżnic, aż po profile specjalne do drzwi podnoszono-przesuwnych. „Te produkty są jak szyte na miarę garnitury do okien i drzwi” — mówi Meesenburg — „po prostu idealnie pasują”.
Nowy proces produkcji: wysoce zautomatyzowany
„Początkowo nowe rozwiązania systemowe profili produkowaliśmy z dużym wysiłkiem na prostej frezarce stołowej — cięcie odbywało się za pomocą piły tarczowej. W 2019 roku, w fazie pilotażowej, sprawdzało się to”, wspomina Linert. Jednak popyt rósł tak szybko, że trudno było poradzić sobie z przyjmowaniem zleceń — pod względem zarówno technicznym, jak i kadrowym. Początkowo zespół produkował głównie profile łączące do parapetów. Szybko jednak pojawiły się kolejne rozwiązania i dziś portfolio rozwiązań systemowych profili własnej produkcji obejmuje około 4 tys. artykułów.
Ten szybki wzrost był możliwy tylko dzięki konsekwentnej inwestycji w inteligentne, wysoce zautomatyzowane i wydajne centrum produkcyjne w zakładzie Meesenburg w Bischofswerdzie. W jego skład wchodzi połączenie pilarki i magazynu HOMAG składające się z pilarki do rozkroju płyt SAWTEQ B-400 w połączeniu z automatycznym magazynem STORETEQ S-200, jak również centrum obróbcze CNC CENTATEQ P-200 HOMAG. Impuls rozwojowy był ogromny: „Podczas gdy na początku musieliśmy umieszczać materiały płytowe na pilarce stołowej i przycinać je na wymiar z dużym wysiłkiem fizycznym, następnie przenosić części na frezarkę CNC, układać wszystko w stosy i przechowywać resztki w międzyczasie, dziś wszystko przebiega w dużej mierze w pełni automatycznie dzięki naszemu nowemu centrum produkcyjnemu HOMAG”, mówi z zadowoleniem Leinert.
Skoki wydajności w zestawie
W firmie Meesenburg cyfryzacja jest kluczem do postępującej automatyzacji. Przykład: proces zamówień w firmie jest oparty na systemie SAP. Jeśli klient zamówi online nowe profile do swojego systemu, wszystkie dane zamówienia są rejestrowane w SAP i przekazywane stamtąd do oprogramowania optymalizacyjnego Cut Rite HOMAG w celu przygotowania pracy. Jest to następnie wykorzystywane do tworzenia planu rozkroju i dostarczania maszynom danych o zleceniach. Podczas gdy w fazie pilotażowej co najmniej trzech wykwalifikowanych pracowników było zajętych znalezieniem odpowiedniego materiału płytowego, przycięciem go na wymiar, a następnie obróbką na frezarce CNC, ta sama praca jest obecnie wykonywana w znacznie krótszym czasie i znacznie dokładniej przez jednego wykwalifikowanego pracownika.
Na wielu stanowiskach pracy jest znacznie wydajniej. Na przykład w zarządzaniu resztkami. Z jednej strony, optymalizacja rozkroju powoduje, że powstaje znacznie mniej odpadów i skrawków. Ponadto te ostatnie są natychmiast wyłapywane i bezpośrednio dostępne ponownie do produkcji, co jest zrównoważone w najlepszym znaczeniu tego słowa. Wszystko to odbywa się całkowicie automatycznie dzięki oprogramowaniu magazynowemu HOMAG woodStore. Proces stał się również znacznie krótszy, jeśli chodzi o czas przygotowania. „Z naszą starą frezarką stołową musieliśmy ręcznie zmieniać narzędzie do frezowania dla każdego nowego profilu. Było to bardzo pracochłonne, stale przerywało proces i kosztowało wiele czasu”, mówi Leinert i dodaje: „Dzięki nowemu centrum obróbczemu HOMAG ten wysiłek został całkowicie wyeliminowany. Agregat jest wyposażony w system automatycznej wymiany narzędzi i praktycznie sam się ustawia”.
Połączenie pilarki i magazynu zapewnia jeszcze większą przepustowość i odciążenie CNC. „Na przykład w przypadku pilarki zdecydowaliśmy się na opcję szybkiego wykonywania rowków wpustowych”, potwierdza Leinert. Wyposażona w tą opcję pilarka wykonuje jednocześnie wszystkie wymagane rowki w jednym przebiegu — i to z niezrównaną prędkością. Na wpust pilarka HOMAG potrzebuje zaledwie 5 sekund. Czynność ta trwałaby około 20 sekund w CNC. „Teraz całkowicie oszczędzamy ten czterokrotnie dłuższy czas obróbki na stanowisku CNC”, potwierdza kierownik produktu i podsumowuje: „To ogromnie zwiększa naszą efektywność i przepustowość”.
Wnioski i perspektywy
W sierpniu 2022 roku, wraz z oddaniem do użytku nowego centrum produkcyjnego HOMAG w Bischofswerdzie, bogata w tradycje hurtownia opanowała wreszcie pożądaną transformację w producenta innowacyjnych rozwiązań systemowych profili do drzwi i okien w budownictwie. Duży i prawdopodobnie jedyny w swoim rodzaju krok w branży, wyjaśnia Natalie Schell, szefowa zarządzania marką własną w Meesenburg: „Dzięki produkowanym przez nas na wyłączność profilowym rozwiązaniom systemowym marki własnej blaugelb staliśmy się łącznikiem pomiędzy firmami montażowymi, inwestorami, architektami i firmami produkcyjnymi. Pierwszy certyfikat C2C SILVER profili blaugelb Triotherm+ oraz produktów blaugelb z rodziny EPS daje wszystkim uczestnikom możliwość połączenia w przyszłości swoich projektów pod względem ekonomicznym i ekologicznym. Z niecierpliwością czekamy na nasz wkład w ciągłe oszczędzanie CO2”.
Innowacyjne produkty mogą zostać zamówione przez całą dobę w nowym sklepie internetowym Meesenburg i szybko dostarczone z własnych zakładów produkcyjnych. Ponadto zwiększają one trwałość energetyczną wyposażonych w nie budynków i minimalizują nakłady na budowie. To samo dotyczy samego procesu produkcyjnego, potwierdza Meesenburg: „Dzięki komórce produkcyjnej HOMAG produkujemy w tak zdigitalizowany, zautomatyzowany i zrównoważony sposób, że możemy całkowicie obsłużyć zupełnie nowy segment rynku na razie przy stosunkowo niskich wydatkach energetycznych i bardzo małej ilości odpadów i nadal rozwijać się jako producent — bez konieczności zatrudniania dodatkowych wykwalifikowanych pracowników”.
„Współpraca z HOMAG jest optymalna. Otrzymaliśmy wzorowe wsparcie pod każdym względem i w każdym punkcie od momentu złożenia zamówienia do dziś. Jest to wyjątkowe i imponująco ugruntowuje reputację HOMAG jako lidera rynku.”Martin Meesenburg, właściciel Meesenburg Großhandel KG