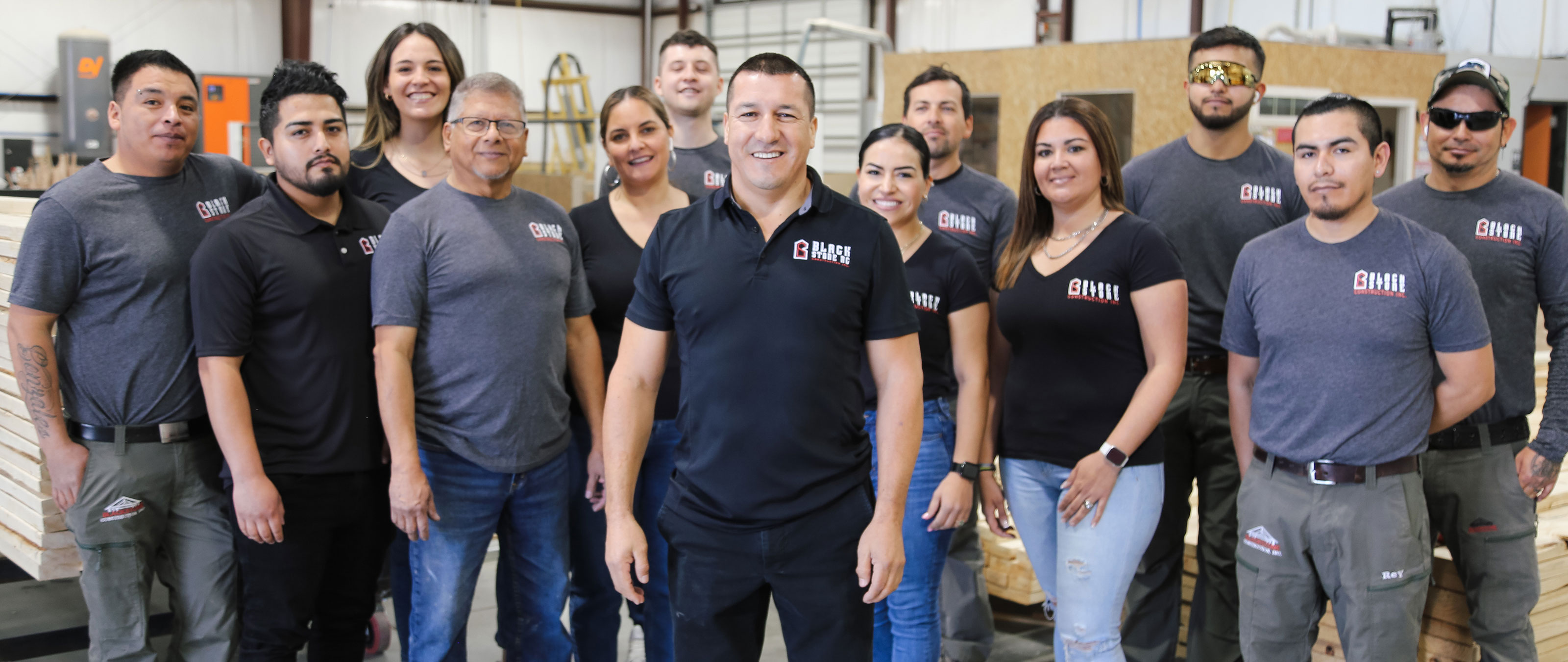
When Jhon Castro immigrated to the United States more than 30 years ago, he began working in the construction industry. He recalls that these jobs were his only option to earn a living. Castro moved to Colfax, North Carolina, in the late 1990s and started his own construction business, Black Stone Construction. In the beginning, Black Stone completed roughly 15 single-family homes a year. Now, Black Stone is producing 900 to 1300 homes a year, including single-family homes and apartment complexes.
Despite the growth Black Stone had, they were consistently limited by the availability of local skilled labor. This hindered Black Stone's ability to increase the number of homes they could build annually. Castro began exploring the possibilities of using off-site construction methods to increase output. His search led him to Stiles Machinery, and they recommended panelized construction using WEINMANN equipment. Black Stone invested in a WEINMANN production line, and they now build interior and exterior walls as well as flooring and ceiling panels in their facility. Every panel is framed and prepared in the factory for on-site installation. Wall panel production must be prepared for all the on-site processing steps, including mechanics, electric, and plumbing. The main advantage for Castro of producing wall panels in a factory is that it requires less workforce than framing on-site. Black Stone can manufacture panels in any weather and work multiple shifts, significantly increasing output. Castro maintains his installation crews to ensure control over critical on-site processes, which is vital for scaling his business. He believes that off-site construction is the future of the housing market. However, on-site work is still essential, and employees must be trained and able to meet the rigorous physical demands required by this type of on-site work. Stiles Machinery is the exclusive sales and service company of the HOMAG Group in North America. The Stiles team engineered the factory layout and improved the manufacturing process for Black Stone. Due to space constraints, the WEINMANN line was designed in a U-shape to fit their existing building. Stiles provided significant support during the pre-sales and post-sales phases, helping Black Stone make the ramp-up phase as smooth as possible by offering various training programs to their machine operators. Once again, Stiles' mission of "solutions built around you" was successfully demonstrated by helping a customer find the right solution. This project began a long-term partnership between Stiles and Black Stone as Castro prepares to expand. Transitioning from on-site framing to utilizing automated equipment marks a significant shift for many in the construction industry. Initially, there is a training process to learn the various machinery functionalities, programming, and maintenance. As construction professionals acclimate to this new paradigm, they discover the benefits of increased precision, scalability, and productivity the off-site work offers. Although transitioning to off-site work may pose initial challenges for business owners, the benefits of increased efficiency, reduced labor costs, and improved project timelines ultimately validate the switch. Black Stone has achieved higher productivity with less waste and fewer workers while reducing the need for rework. First, all the raw lumber is cut to size and then sorted based on how and where it will be used in the manufacturing process. Building of the wall starts on the framing station, a WEINMANN FRAMETEQ F-300. The powerTouch interface visually guides the operator to load pieces while integrated data flow spaces studs and subassemblies. When the frame is complete, it is moved from the framing station to a series of BUILDTEQ element tables. After transferring, the wall panel can be removed from the line as a complete open frame or moved to the following table to add sheathing. The final two tables are designed to clamp the frame against an x and y stop to ensure the frame is square during the sheathing and machining processes. Once the OSB sheathing is applied and tacked, the frame is ready to move to the final table. The final table is where the sheathing will be permanently attached and machined to complete the panel. These operations are done with a WEINMANN Multifunction Bridge. This bridge, a WALLTEQ, has one nail gun capable of firing up to five nails per second and a router for cutting the perimeter and rough openings needed for exterior walls or floor and ceiling panels. When the bridge is finished, the completed panel is labeled and moved off the line. The labeled panels are stacked in the order of how they will be needed on the job site and placed on trucks for transport.
The president and owner of Black Stone, Jhon Castro, is particularly impressed by how simple it is to operate the WEINMANN Multifunction Bridge. The operator presses a button, and the software-driven machine handles the rest of the process. With integrated software solutions, it has been easier for Castro and his team to keep up with their order book and produce high-quality panels in their factory. Castro is already considering buying an additional WEINMANN line to increase the production of wall panels and expand Black Stone. He is particularly fond of the German engineering of the WEINMANN machines and their level of craftsmanship. These wall production lines are known for their speed, safety, and service–resulting in minimal downtime and enhanced operational efficiency. Facing the challenge of finding skilled labor, Castro pivoted to panelized construction, significantly enhancing productivity by manufacturing wall panels, floors, and ceilings in all weather conditions and multiple shifts. Off-site construction requires fewer workers and improves quality control in a protected environment. Black Stone's success is attributed to the efficient use of WEINMANN's automated panel equipment, the support from Stiles Machinery, and the integration of advanced software solutions, signaling a substantial shift in the construction industry towards off-site, automated production for increased efficiency, scalability, and quality.
Ein Artikel aus dem Kundenmagazin performance 23 | 2024. Mehr Informationen finden Sie hier!
Black Stone NC Construction Inc.
The mission of Black Stone NC Construction Inc. is to revolutionize the construction industry through innovative, efficient and sustainable construction practices. The company strives to build high-quality houses and commercial properties that are durable and reflect the company's commitment to craftsmanship and customer satisfaction.
Learn more!