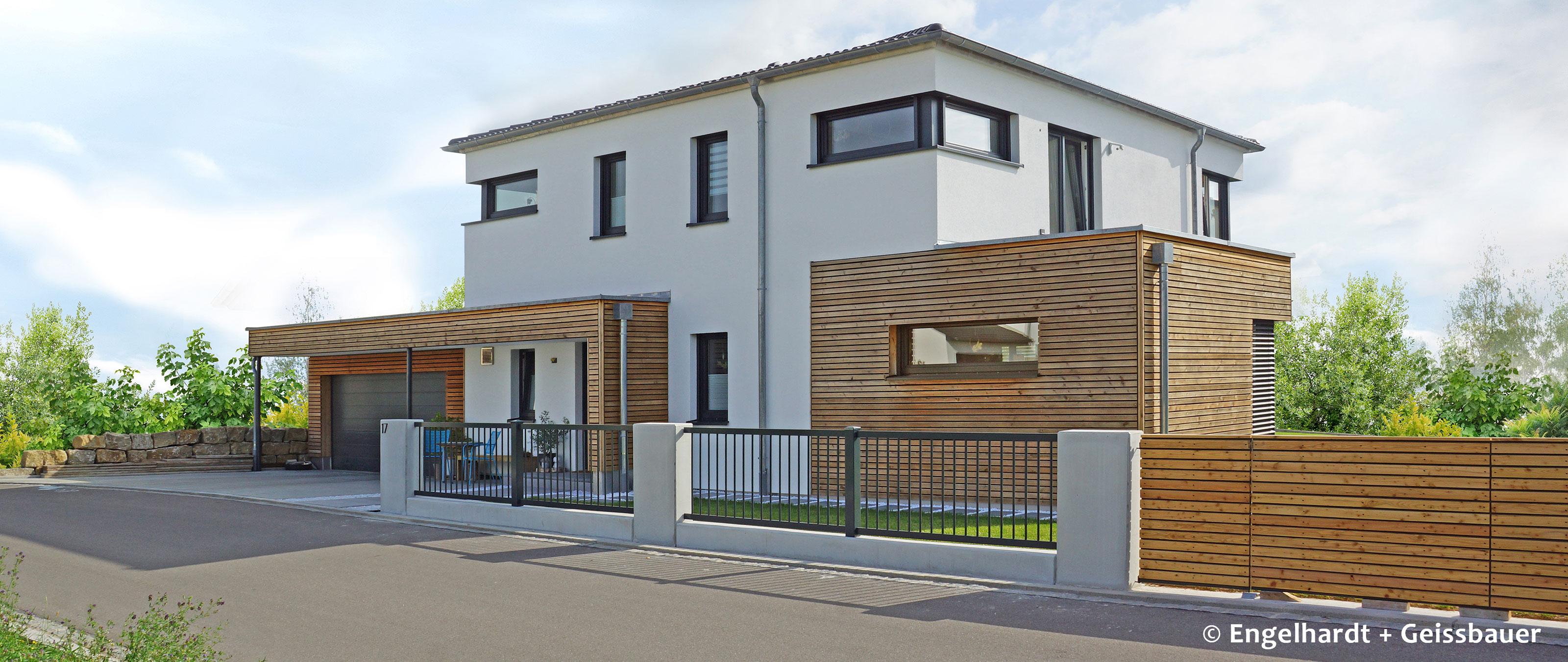
If you look at a new housing estate made up of single-family houses, you might get the impression that a lot of these houses are like peas in a pod. In contrast to a single-family house off the peg, Engelhardt + Geissbauer sets their focus on individuality.
Founded 33 years ago as a small carpentry business in Burgbernheim, in Franconia, Germany, the timber construction company has since become a story of success, with increasing specialization in wood frame construction. To this day, the innovative solutions from WEINMANN help to equip the company for the future and ensure high quality in timber construction.
However, the company is still shaped not only by steadily increasing demand, but also by a turbulent market environment and challenging times.
WEINMANN and Engelhardt + Geissbauer have been working closely together for several years. How did you first come into contact with WEINMANN?
SB (Stefan Bauereiß): Contact was first made in 2012, when we wanted to purchase an assembly table. At that time, we already had two assembly tables from other manufacturers and were thinking about expanding production by one table and broadening our capacities. It was more of a coincidence that we found out about WEINMANN.
This resulted in an appointment with a sales representative from WEINMANN. When we explained our thinking, he looked at us in surprise and said, "It's not an assembly table you need; you need a multifunction bridge." Finally, we bought a bridge and at the same time decided that we needed a new hall to house this and the existing assembly tables, which we then built. However, during the course of the discussions, we also realized that the multifunction bridge only works if the framework conditions also match. Allowing such a machine to fall from the sky into the production hall will not result in an optimal production process. Material supply, disposal and many other factors have to be consistent in order for a specific workflow to occur. It was precisely this issue that became the subject of the first consulting discussion. So that's how we arrived at our first plant, which was installed in 2013.
After many successful years, the hall fire in 2021 was a major incident. Can you tell us a little more about what happened at the time?
SB: On May 13, 2021, there was a fire in the production hall due to a short circuit on a compressor. Unfortunately, this happened on a public holiday, Father's Day of that year, which meant that the fire wasn't discovered until late. On that day, our wall line, a multifunction bridge and four assembly tables fell victim to the flames. That very evening, we discussed the next steps for the company. We called WEINMANN the same day and explained our problem. It was immediately clear to us that we would not be able to recreate production 1:1, as we were at the absolute capacity limit at the time with 35–40 houses per year. However, we quickly decided to expand production and build a new hall. As a result, we have more than doubled the capacity of the exterior walls. A pure roof line is now installed in the old location that burned down. I wouldn't wish an experience like this on any colleague with a wood processing business. In the aftermath, you have a great hall and a good production setup — but it's not a journey you want to go through regularly.
This must have been a very stressful time for you and the team at Engelhardt + Geissbauer. How did WEINMANN support you in these difficult times?
SB: We have always maintained good contact with WEINMANN. We already had a friendly relationship with our salesperson Stefan Rach — he looked after us very well back then. Without WEINMANN, we would not have been able to rebuild in the time it took. My aim was to be producing again a year after the fire, which included the construction of a new hall and a new production line. Despite all obstacles, we managed to complete the new hall by Christmas 2021, which meant that WEINMANN was able to begin setting up the system the following January, as agreed. Of course, there were discussions, but we noticed that everyone involved tried to work together rather than against each other. Even when things became really tight and critical, we tried to find joint solutions together with WEINMANN — and always on an equal footing. That was impressive. Assigning blame was never the order of the day. We thus found a solution for every problem, and we eventually achieved the overall goal through these solutions. Looking back, it was even fun.
In your opinion, what are the hallmarks of solid cooperation between two companies?
SB: In a partnership, it's important to work together on an equal footing. There will always be situations in which one participant is better positioned than the other. But there will also be situations in which it's the other way around. In my opinion, this balance should not be exploited by either party. In particular, in times of material shortages and the associated price increases, we made note of who we can and cannot work well with. My mantra here is to achieve a certain continuity on a level playing field. It's also fun to be there for each other every now and then — it means that you can get through anything together.
What do you appreciate about working with WEINMANN?
SB: I appreciate that we act on an equal footing and do not exploit each other. This is fun, and for me, essential for long-term cooperation.
In the past, you have not only relied on systems from WEINMANN, but you have also used services such as production support from the WEINMANN Academy. Would you recommend WEINMANN solutions to other companies with regard to the range of products and services, and if so, why?
SB: Yes, I would recommend them, because they work. Ultimately, this also includes the development that WEINMANN has undergone. The WEINMANN experts know exactly what they are doing and have implemented numerous systems for a range of customers. The solutions are simple for carpenters. There are other competitors, but the machines for house construction have to be designed properly and be able to withstand certain loads. It's not just a table, a bridge or software that brings success — all influencing components in a system must be ideally coordinated with one another, and WEINMANN is streets ahead in this regard.
Your company has developed steadily over the years. What's the outlook for the future? How will your company continue?
SB: For us, the aim is to continue to grow every year. I still see a lot of potential in multi-story residential construction and commercial construction. This is the segment in which we want to be even more active. In general, I think timber construction in Germany still has a long life ahead of it. I think that at Engelhardt + Geissbauer, we are now very well positioned, particularly due to our latest investment in the exterior wall line.
An interview from the customer magazine performance issue 23 | 2024 Find out more
Engelhardt + Geissbauer GmbH
Engelhardt + Geissbauer has been planning and building natural and healthy timber houses for 30 years. More than 150 employees work in the company and around 75 homes are built annually. The portfolio includes "bare-bones" houses for customer expansion, turnkey construction, individually planned houses and prefabricated houses. Engelhardt + Geissbauer GmbH has been a subsidiary of Ziegler Holding GmbH since 2019.
Learn more about the company