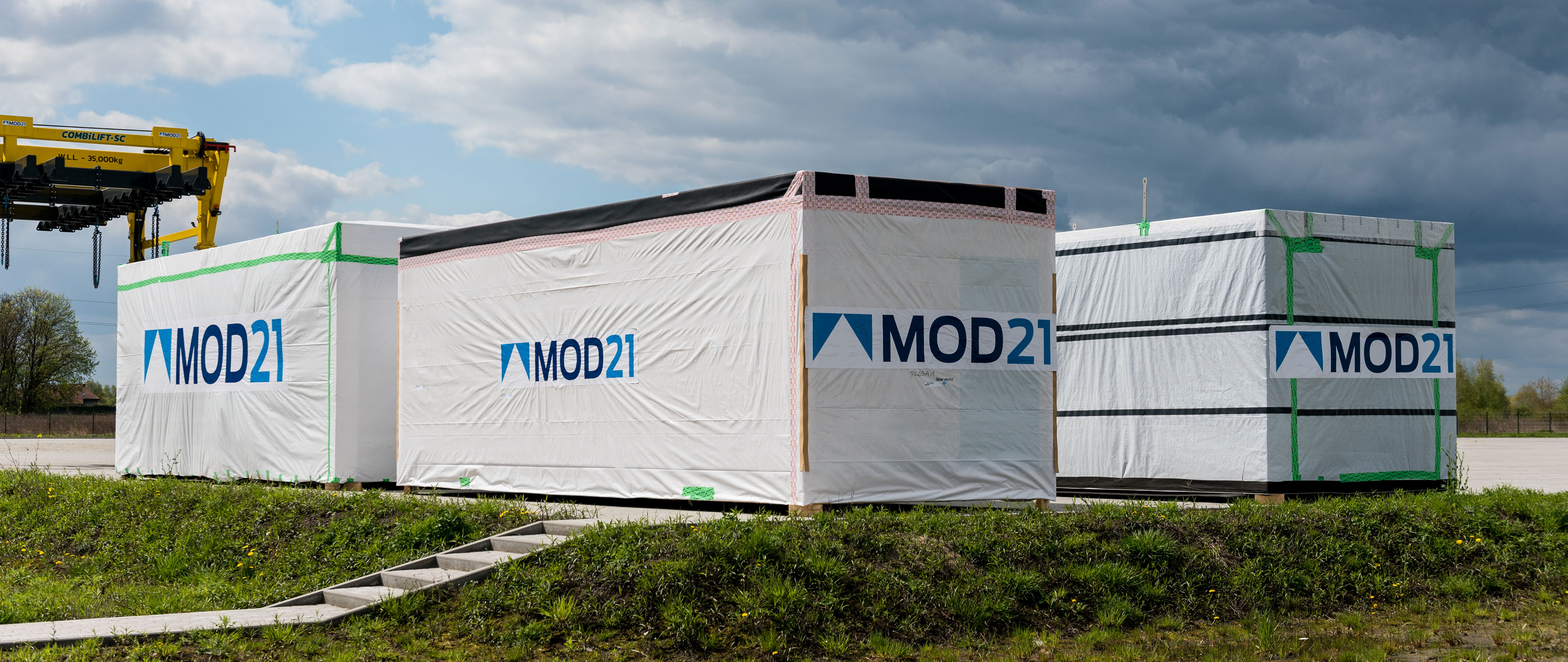
For timber construction, multi-story construction brings with it a certain level of internationalization. This is reflected in the increasing market participation of foreign companies in large-scale projects in Germany, although these are currently still predominantly larger suppliers from Switzerland and Austria. Other big players in the timber construction market arise from startups with investor backing or conventional construction companies that shift their activities to timber construction.
Modular timber construction
MOD21 GmbH in Düsseldorf is also an old acquaintance in this sense, as the subsidiary of the Polish group ERBUD SA, and has been carrying out large projects in the Düsseldorf area since 1993—at that time still under the name GWI and exclusively in steel and concrete. The company also has many years of experience in modular steel construction. In 2021, a radical restart took place, accompanied by a change of company name: on the initiative of ERBUD's managing director Dariusz Grzeszczak, who had already launched several initiatives to restructure the Group ecologically, the company reinvented itself under the name MOD21. Projects that had already been started will be completed by next year in conventional construction; since 01/01/2022, new projects are carried out in modular timber construction only. Sales Director Marius Schneider: "In view of the climate targets and the changed political framework conditions—in particular, the promotion of serial construction with sustainable building materials—for us, the future lies in timber construction." The company's response to the new requirements on the market is clear and consistent: in the future, the company wants to use only external partners, even for excavation, underground garages, etc., except in the Düsseldorf area. As a modular timber construction company, the company is more or less a startup, but at the same time, can draw on its experience, networks and contacts gained over 30 years of building construction. The starting conditions are therefore better than with a brand new company, especially since the public and commercial clientèle increasingly wants to see their construction projects realized using timber construction. Against this background, MOD21 has been noticing for several years that the German market is opening up for modular construction, and that architects, for example, are increasingly interested in modular buildings. Marius Schneider: “It is becoming increasingly clear that modular constructions are not just containers or temporary solutions, but high-quality buildings for long-term use in which the type of construction is not immediately evident. In this respect, we are now on a par with conventional building construction, but we offer the consistent quality of a building prefabricated under controlled conditions, which is significantly higher.”
Restart on 22,000 m2 production area
Even though the modular construction sector currently still has a modest market share of around five percent, in Düsseldorf, excellent growth potential can be expected. That is why the decision was taken to become a modular startup, and with considerable financial resources. Founded in March 2021, MOD21 GmbH acquired the founding site of ERBUD SA in Toruń, Poland, a plot spanning 150,000 m2, which already had a 14,000 m2 hall and an office building with 3000 m2 of usable space. A further hall covering 8000 m2 was added to the existing hall, as well as an open transition area, which means that today, the company has a continuous production area of more than 22,000 m2. The old hall, which had a significantly lower ceiling height of six meters, was equipped with two Weinmann production lines on which wall, floor and ceiling elements are manufactured. The layout of the hall was designed together with the mechanical engineering firm from Lonsingen, which was chosen “because they offered us the most plausible complete solution for production and comprehensive advice in the field—for example, hall logistics or conveying system options.” The wall line is highly automated and has the usual workstations: a Weinmann BEAMTEQ B-660 carpentry machine with all-round component processing and semi-automatic material feed, a frame work station, the obligatory turning table with multifunction bridge and two buffer tables on which, among other things, fire protection sheathing can be realized without bottlenecks. The line ends with a tilt table that transfers the finished wall elements to several distribution trolleys. These trolleys move the upright wall elements into an eight-track wall slot, in which some go through a finishing process including window installation, plaster, etc. Upon exit, they enter module production via a distribution trolley and a crane. For cost reasons, insulation is currently still manual, but there is already space for a WALLTEQ M-300 insuFill. Industrial robots have also been dispensed with, as for managing director Theodor Kaczmarczyk, the potential disadvantages of this technology still outweigh the advantages for the planned quantities. Floor and ceiling elements are produced on the similarly equipped line 2. Floor elements are picked up by a crane at the end of production and transported to the module line in the eleven-meter-high new hall space.
Module production in a separate line
Here, they are immediately placed on trolleys and leveled so that the modules are absolutely perpendicular for assembly. The room cells are then assembled. They are moved from station to station not via rails, but on carriages. MOD21 managing director Theodor Kaczmarczyk states, “This gives us more flexibility, because we can also turn the modules, move them diagonally and arrange them next to each other in different quantities depending on the width. If there is a bottleneck, a finished module can also be brought forward past a module that is still in progress.” Wall elements are produced in a cycle of 29 minutes, floor and ceiling elements take 59 minutes—a difference that results primarily from the higher proportion of manual work steps. In the floors, there are diagonal connections between the construction timbers, which are still manually performed. Twelve employees currently work in element production. Room cells are ready in two days, including the production of the elements. The interior takes another 12 days, which means that the total cycle for a finished module is 14 days—including finished installation, built-in cabinets, kitchens and sanitary objects, right up to the toilet brush in the wall holder. MOD21 works predominantly with its own employees and contracts external workers only for specialized trades such as roofing and facade work, which require reworking on the construction site. The benefit is that the time and cost advantages of the trade services provided in the hall are included in the overall costing. External construction contractors, on the other hand, are not yet willing to price these advantages into their services.
By 2026, 100,000 m2 of building space per year
For the first year, MOD21 set itself an ambitious target of selling and delivering 30,000 m2 of building space, but according to managing director Theodor Kaczmarczyk, this plan is well on schedule. 6000 m2 are already in production, the rest is in the pipeline. Given the short assembly times in modular timber construction, it is realistically possible to meet the target by the end of the year—even if private investors are currently acting cautiously on the market given the trends in costs and interest rates. By 2026, the company wants to gradually increase it to 100,000 m2 of building space. Then, in Toruń, the company will operate in two shifts. A third shift is not planned, but a second production site is, and Theodor Kaczmarczyk has already begun initial planning discussions for this site with Weinmann. The new site will allow significantly higher quantities and have a significantly higher degree of automation because the slanted metal connections in floors and ceilings, among other aspects, will be replaced by milled timber connections at the recommendation of the machine manufacturer. Industrial robots will also be used at this plant. The new site may be in Germany. This is consistent insofar as MOD21 currently serves exclusively customers in Germany. Exports to German-speaking countries are being considered, while Polish customers are not yet very open to modular buildings. The plant site in Poland was therefore chosen for other reasons. "We were able to use the resources of our parent company here," explains Theodor Kaczmarczyk. "Furthermore, ERBUD enjoys an excellent reputation as an employer in Poland, which is why we have absolutely no staffing problems at this site." There are hardly any cost benefits from the choice of site: according to Theodor Kaczmarczyk, the wage structure in Poland is now at almost the same level as in Germany. “And because for that reason, young Poles therefore prefer to work in their own country, we brought the plant to them.” Because the managing director still considers visiting the factory crucial in order to get an idea of his company's services by touring the modern production facilities including a showroom with samples, MOD21 pays for travel and accommodation for those keen on it.
Planning and services
During the visit, the company gives preference to projects for which the advantages of serial production are particularly noticeable: educational properties such as schools, kindergartens and university buildings, office and administration buildings, hotels or healthcare facilities such as wards and retirement homes, as well as building extensions and additions. All this with the now well-known advantages of modular timber construction:
Worry-free implementation in which the customer is required only in the planning phase and at handover, meaning that they save on personnel resources
Transparent quality management and high, consistent building quality thanks to largely automated, high-precision production processes under controlled conditions
Extremely fast completion thanks to a high level of prefabrication and parallel processing of construction site preparatory work and module production
This requires merely a short closure of public thoroughfares, low impairment to residents (additions!) and safe construction of schools and kindergartens during school breaks
Versatile use with dismantling of modules and reconstruction at another site, whereby a large building can also be divided into several small buildings if desired. The disassembly concept is standard at MOD21, and the company also offers its customers rentals.
For all of this to work, the building should of course match the module system. For this reason, it makes sense for MOD21 to join a project as early as the planning phase. Although you can plan and build any individual floor plan, straying away from the system increases the time required and, above all, the costs. Which is why the planning, handled by our in-house architects, external partners and also together with the client's own architects, is carried out in a module-compliant system. The modular DNA of the constructed result is virtually unnoticeable. This is ensured by versatile modules up to 12.00 m in length, 4.20 m in width and 3.20 m height clearance, which are also suitable from a transport standpoint. In the case of special requests, the modules can be combined vertically and horizontally, so that large classrooms, high-ceilinged reception areas or stairwells can be mapped in modular design. Where this is not possible, external partners can be brought in.
CO2 calculator based on a university study
An offer that fits seamlessly into our modern era with its serial and sustainable aspects, as confirmed by the praise of Federal Minister for Housing, Urban Development and Building Klara Geywitz, who recently visited the Toruń plant. An exterior wall standard is also contemporary, which with a 140 mm insulated timber frame, two gypsum fiberboards inside and an OSB panel with curtain wall facade or EIFS outside, forms the structural prerequisite for a good energy standards. But MOD21 goes even further: prospective customers can use a CO2 calculator on the company's website to calculate how much CO2 is generated during the construction of their building—this is not just for show; this computation is backed by a complex study by the University of Krakow, which "included a huge amount of data relevant to construction projects". In a current project for a refugee center with 3700 m2 of usable space in Munich, the calculation showed a CO2 saving of 97 percent compared to conventional construction. "Of course, road transportation has a negative impact, which is why we are currently thinking about hydrogen fuel," explains Theodor Kaczmarczyk. “But this level of transport bears no relation to months worth of contractors traveling to and from a conventional construction site.” For many customers, this sustainability aspect is reason enough to accept the slightly higher construction costs of modular timber construction. This is especially true because the additional costs are put into perspective thanks to the short processing time: anyone building up to 70 percent faster saves their customers financing costs and enables them to earn money more quickly by moving in, renting out or selling. If these benefits are taken into account, modular constructions are, in the eyes of Theodor Kaczmarczyk, around the same price as other construction methods.
An article from the trade magazine "mika-do," November 2023 issue. More information is available here.
“The most suitable complete solution for our production and comprehensive consultation.”Managing director MOD21 Theodor Kaczmarczyk
MOD21
The Düsseldorf-based company was founded in 1993 in the Rhineland and is now active throughout Germany. As part of the ERBUD Group, which operates throughout Europe, MOD21 has an excellent network and extensive know-how in the field of modular construction. The new production site was built within just 12 months. On an area of 22,000 m², approximately 375 m² of module area are produced almost fully automated.
More information