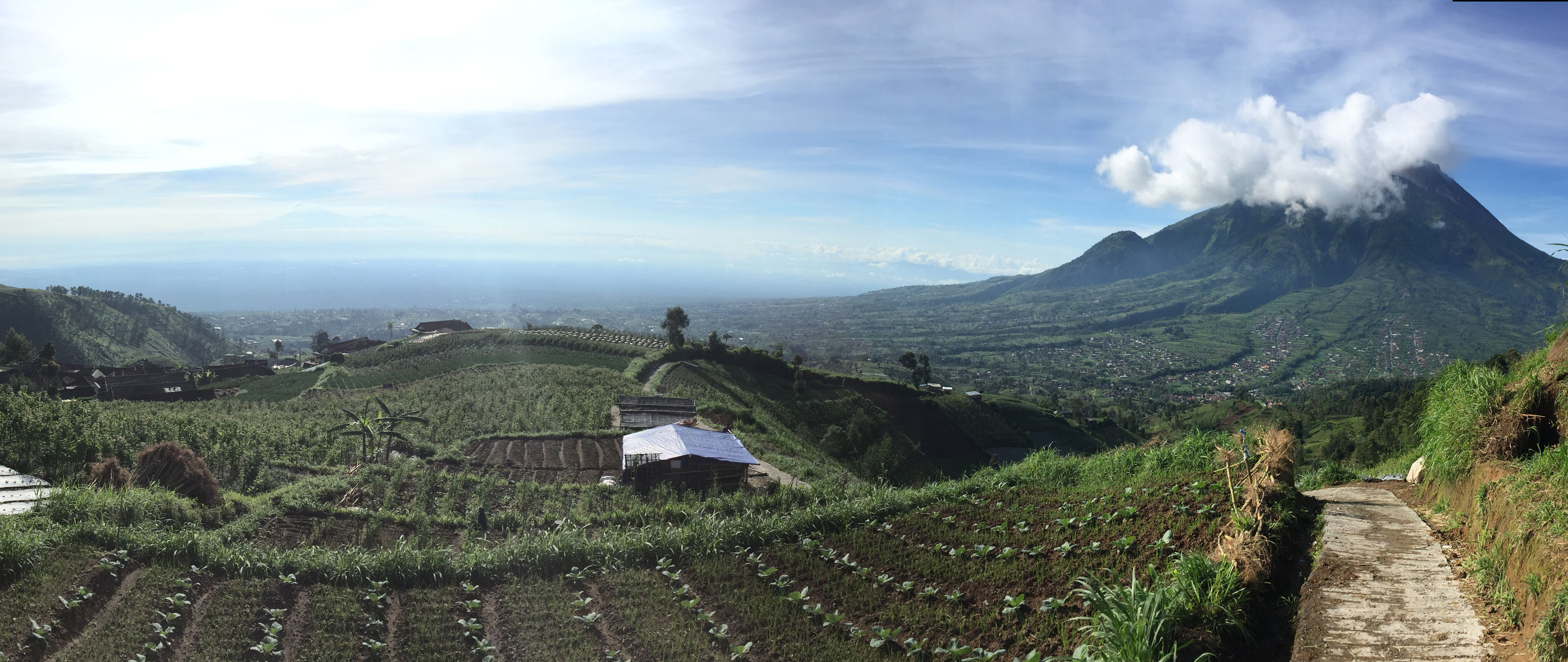
Die Möbelherstellung im indonesischen Semarang sind auf die Produktion von antik wirkenden Vollholzmöbeln spezialisiert. Das dort ansässige Unternehmen PT Ebako Nusantara liefert seine Objekte schwerpunktmäßig in die USA. Immer wieder kämpfen die Mitarbeiter mit dem Termindruck, den das Exportgeschäft mit sich bringt. Deshalb strukturierte SCHULER Consulting die betriebsinternen Abläufe neu. Im Rahmen der HK-Serie „Internationale Möbelproduktion“ beschreibt Björn Henseler, wie verlässlichere Fertigungszeiten erreicht wurden.
Wer sich vorstellt, dass alle antiken Möbel, die man auf dem Möbelmarkt kaufen kann, tatsächlich alte aufgearbeitete Objekte sind, die aus gesunkenen Schiffen geborgen und dann von spezialisierten Schreinern in aufwändiger Handarbeit restauriert wurden, liegt leider falsch. Sicher gibt es diese Form der Restauration noch, aber bei den Möbelproduzenden im indoneischen Semarang auf der Insel Java sind es Prozesse wie „Cowtailing“ (mit Kuhschweifen ähnelnden Werkzeugen Farbe auf das Möbel aufpeitschen) und „Spattering“ (mit der Spritzpistole ohne Luftdruck Farbe auf das Möbel sprenkeln), die den antiken Eindruck erwecken sollen. Hier kann man erleben, wie neue Möbel auf alt getrimmt werden.
Indonesien hat insgesamt 255 Millionen Einwohner und 17.000 Inseln von denen ungefähr 6.000 bewohnt sind. Eine von ihnen ist Java Island. Sie ist eine der größten Inseln in Indonesien und beherbergt die Hauptstadt Jakarta mit ihren 30 Millionen Einwohnern, welches im Westen der Insel liegt. Weiter Richtung Zentral-Java finden wir Semarang, ein für indonesische Verhältnisse eher ruhiges Städtchen mit „nur“ 1,5 Millionen Einwohnern.
PT Ebako Nusantara produziert Möbel dort bereits seit vielen Jahrzehnten Möbel und hat sich inzwischen als Unternehmen etabliert, das antike Möbel speziell für den US-amerikanischen Markt liefert. Die Produktpalette ist vielseitig, denn das ist der Markt auch. Die nachgefragten Losgrößen bewegen sich zwischen einem und 20 Stück. Der aufwändige Fertigungsprozess mit seiner langen Produktionskette erfordert daher viel Know-how bei Logistik, und Planung von den Möbelherstellern.
Im ersten Gespräch wurde deutlich, dass er jeden Tag mit den internen Lieferterminen kämpft, um die Möbel rechtzeitig in den Schiffscontainer zu bringen. Deshalb steht eine Produktionsanalyse an, um die Fertigung auf Herz und Nieren zu untersuchen. In seinen Abteilungen unterscheidet sich Ebako nicht von anderen Unternehmen dieser Produktsparte. Die Produktionsschritte sind; Rohmateriallager und Trocknung, Grober Vorschnitt des Materials, Feinbearbeitung der Einzelteile, schleifen, montieren, min recht aufwändiger Lackierprozess und schließlich das Fertigstellen und Verpacken der Möbel.
Bei vielen Unternehmen in diesem Land bestehen die Optimierungsmöglichkeiten im Kapazitätshandling der unterschiedlichen Abteilungen. Weiter haben sie Probleme in der internen Organisation der Feinbearbeitung mit ihren vielen kleinen Einzelprozessen und der Vielfältigkeit der unterschiedlichen Arbeitsablaufpläne. Im nachgelagerten Produktionsprozess geht es dann um die Optimierung des sehr manuellen und personen-intensiven Schleifens. Hier fehlt der Überblick über den meist nach dem Werkbank Prinzip organisierten Montage mit ihren unzähligen Schreinerbänken. Zum Schluss zieht sich das auch bis zum überaus zeitintensiven Lackierprozess durch.
Obwohl eine Fertigung wie diese recht stark von manuellen Bearbeitungsprozessen geprägt ist, so kann man doch eine gewisse Automation innerhalb der Produktionsbereiche schaffen. Man konzentriert sich auf einen Teilbereich der Produktion und deren Kapazitäten und koordiniert diese Bereichsübergreifend. Automation hat unterschiedliche Ausprägungsformen – wir Europäer denken häufig an Roboter, wenn wir das Wort Automation verwenden. Aber in einem Arbeitsbereich mit vielen Kleinmaschinen in dem jedem Arbeiter eine Maschine zugeordnet ist, zeigt sich Automation schon in einem klar strukturierten internen Transport der Möbelteile.
Wenn der Transport des Materials gut geregelt ist, fallen schon ein Großteil der Verteilzeiten weg, was die Ausbringungsmenge deutlich erhöht. Im nächsten Schritt galt es einen Aktionsplan zu schreiben und mit Prioritäten zu versehen, bevor es dann die Implementierung startete. Die Priorität lag hier beim Wunsch des Firmeninhabers, es rechtzeitig mit den Möbeln in den Container zu schaffen, um so die Liefertreue zu erhöhen. Bei den kleinen Losgrößen von oft nur drei Stück, meist auch noch Prototypen, ist es fast unmöglich eine detaillierte Kapazitätsplanung zu erstellen. Es fehlen bei den sehr unterschiedlichen Arbeitsablaufplänen die detaillierten Zeitaufnahmen der Einzelprozesse. Somit ist eine Rückrechnung des Produktionsstarts kaum möglich und entsprechend werden Reservetage eingeplant. Somit fehlen die Möbel oder stehen dann lange im Container.
Es braucht also verlässlichere Fertigungszeiten, die nach dem Top-to-Bottom Prinzip eher grob auf Ebene der Fertigungsplanung mit Referenz Möbeln verglichen und ergänzt werden. Bewusst haben wir die Abteilungen untereinander als Zulieferer der nachfolgenden Abteilung oder als Kunde der vorigen Abteilung definiert. So kann die Fertigung in einzelne Verantwortungsbereiche aufgetrennt werden, was die vorgängige Angabe der je benötigten Fertigungszeiten vereinfacht und damit die gewünschte Genauigkeit erreicht. In den Abteilungen wird nun tatsächlich im Detail geplant und beobachtet, welches Teil wann, wo und wie bearbeitet wird, damit es rechtzeitig beim Folgeprozess bereitliegt. Entscheidend für den Erfolg ist in dieser Situation, das Training des Managements und der Abteilungsleiter. Sie müssen in der Lage sein, ihre Kapazitäten selbständig zu planen und auf Probleme und Veränderungen sofort reagieren zu können. Auch der Umgang mit Schnellschüssen darf hier nicht außer Acht gelassen werden.
Die Mitarbeiter und das Management von Ebako haben unsere Vorschläge überraschend schnell verstanden. Unsere Ideen wurden schnell angenommen und bereits nach unserem ersten und vor dem zweiten Besuch nach drei Wochen hat das kreative Team weitere effiziente Lösungen entwickelt. Wo beim ersten Besuch ein Schrank zur Aufbewahrung und Säuberung der Spritzpistolen und aller für die Reinigung notwendigen Werkzeuge stand, sprießen neu gestaltete effiziente Arbeitsplätze wie Pilze aus dem Boden.
Parallel zur neuen Produktionsplanung haben wir mit dem Ebako ein Qualitätssystem entwickelt und eingeführt. Jetzt werden die Produktionsfehler standardisiert und die entsprechenden Maßnahmen können direkt und sofort gestartet werden. Als nächsten Projektschritt steht nun die Verkürzung der Durchlaufzeiten an. Die Nachbearbeitungsrate an den unterschiedlichen Vollholzteilen sind immer noch zu hoch. An den Tafeln in der Shopfloor-Ecke kann dieser Wert täglich nachverfolgt werden. Wenn die Nacharbeiten reduziert werden, verkürzt sich der Produktionsprozess gleich um einige Tage.
Als Hauptergebnis aus diesem ersten Teilprojekt von SCHULER Consulting hat sich Ebako eine funktionierende Produktionsplanungs- und ein Shopfloor-Management aufgebaut. Wie die Zahlen zeigen, verlässt heute jeder Container das Werk rechtzeitig.Für uns als Unternehmensberater ist es immer wieder eine große Freude, wie rasche und nachhaltig eines komplett neuen Produktionsplanungssystems in einem asiatischen Unternehmen umgesetzt werden kann. Wenn wir es schaffen, die Mitarbeitenden für neue Ideen und Prozesse zu begeistern, dann sprudeln deren nächsten Ideen von selber und werden sogleich selber umsetzt. Die erreichten Zahlen und der geordnete Materialfluss beweisen das.
Fotos: SCHULER Consulting (Björn Henseler)
Ein Artikel des Fachmagazins HK, Ausgabe 01/2018. Hier lesen Sie das HK-Magazin online.