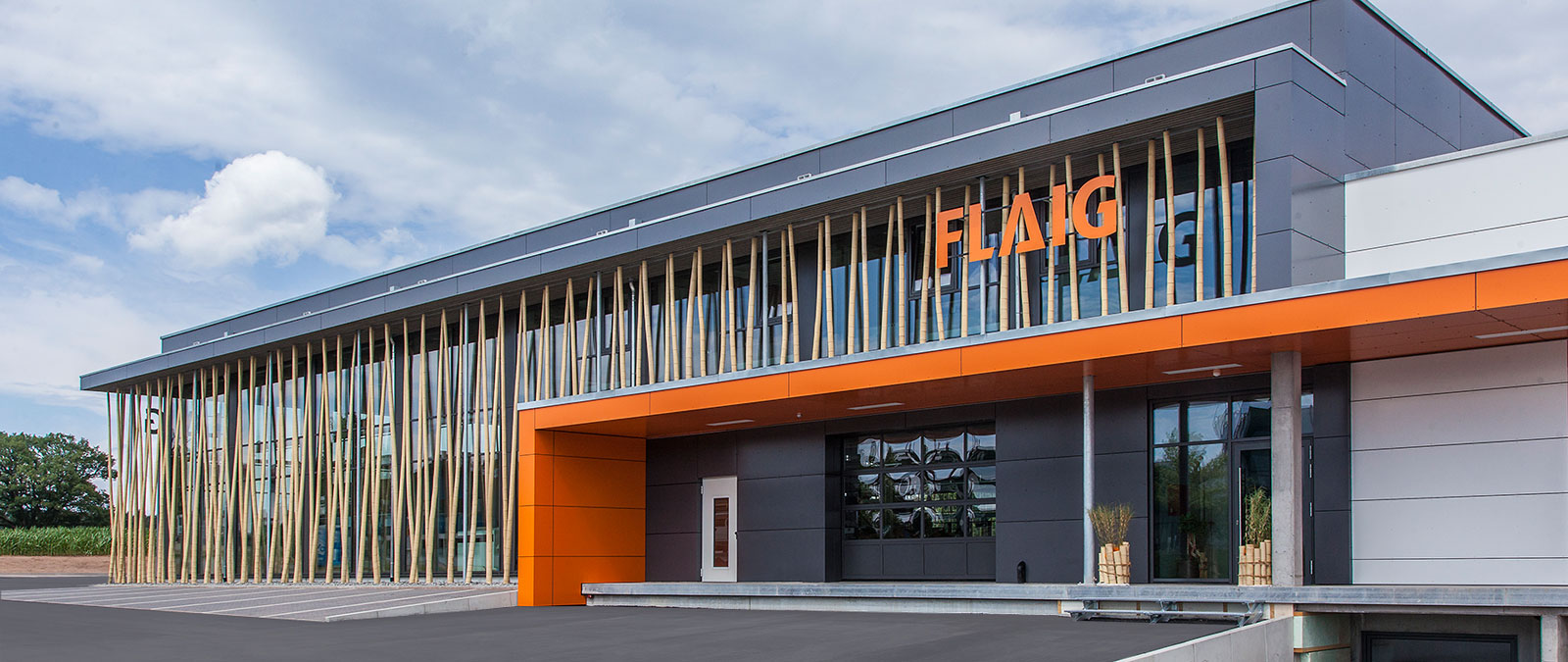
Ein Artikel des Fachmagazins DDS, Ausgabe 05/2016. Hier lesen Sie den Artikel auf DDS Online.
Es ist Donnerstag, 10 Uhr. Der allwöchentliche Produktionsauftrag mit Waschtisch-Kommoden für einen Badmöbel-Hersteller ist im Werk II der Schreinerei Flaig eingetroffen. Die Kommode hat es in sich: Schichtstoff-Oberflächen von hochglänzend bis supermatt, ebene Formteile und Schubkästen, bei denen Vorderstück und Seitenteile zu einem schichtverleimten 3D-Formteil zusammengefasst sind. Zu fertigen sind jetzt 243 Stück dieser Kommode in 19 verschiedenen Farbtönen beziehungsweise Oberflächen, und zwar bis Dienstag um 10 Uhr. Dann muss alles verpackt und sortiert an der Laderampe bereitstehen. Jetzt sollte der Betrieb vor allem an der CNC aber auch an der sich anschließenden Formteil-Bekantung sowie der Montage wie am Schnürchen laufen. Im Voraus, ohne Kundenauftrag, beschichtete Formteile, aus denen sich zwei oder drei Schubkasten-Elemente herausschneiden lassen, liegen im Zwischenlager bereit, ebenso supermatt lackierte Spanplatten für den Schubkasten-Boden im Format von etwa 80 x 100 cm.
Vier Standbeine
Die Schreinerei Flaig in Hardt im Schwarzwald bei Schramberg beschäftigt 60 Mitarbeiter und erwirtschaftet jeweils 20 Prozent ihres Umsatzes mit Bauschreiner-Arbeiten, dem Möbel- und Innenausbau für Privatkunden und im Objektgeschäft. 40 Prozent entfallen auf Zulieferprodukte für die Möbelindustrie und den Sauna-Bau. Als die Schreinerei vor einem Jahr ihre Zulieferproduktion in eine vom Stammhaus 2 km entfernte, 5.000 m² große Neubauhalle ausgelagert hatte, entschied sie sich für das 5-Achs-Bearbeitungszentrum BMG 611 von HOMAG mit dem TBA-Beschicker.
Die Maschine sollte sowohl große Serien mit relativ einfachen Bearbeitungen und große Wandelemente für den Sauna-Bau als auch 5-Achs-Bearbeitungen für die Möbelindustrie ausführen. Bevor der Maschinenführer Rolf Auber die Rohlinge für die 3D-Teile zusammensucht, fährt er mit dem Hubwagen einen ungefähr einen Meter hohen Stapel mit den lackierten Spanplatten an den Beschicker der CNC. Es trennt die Rohplatte in der Mitte auf, fräst die Kontur und bohrt Löcher für Beschläge. Pro Takt entstehen zwei fertige Werkstücke. Der TBA stapelt sie so, wie sie auf dem Tisch nebeneinander liegen, neben dem Rohplatten-Stapel auf eine Palette ab. Rolf Auber braucht sich darum nicht zu kümmern. Stattdessen sucht er das Material für die Formteile zusammen, wartet die Spannvorrichtung, auf der er morgen die 3D-Rohlinge aufteilt und die Formteile in derselben Aufspannung komplett bearbeitet. Dann hilft er an der Pressenstraße. Der Beschicker ist für eine Stapelhöhe von rund 50 Platten ausgelegt. Das lastet die Maschine vielleicht zwei oder drei Stunden aus.
Fotos: Fachmagazin DDS / Georg Molinski
„Das Bearbeitungs-Zentrum bewältigt den Spagat zwischen dem effizienten Abarbeiten großer Serien im mannlosen Betrieb und empfindlichen, komplizierten 3D-Teilen.“Hubert Flaig, Inhaber Schreinerei Flaig