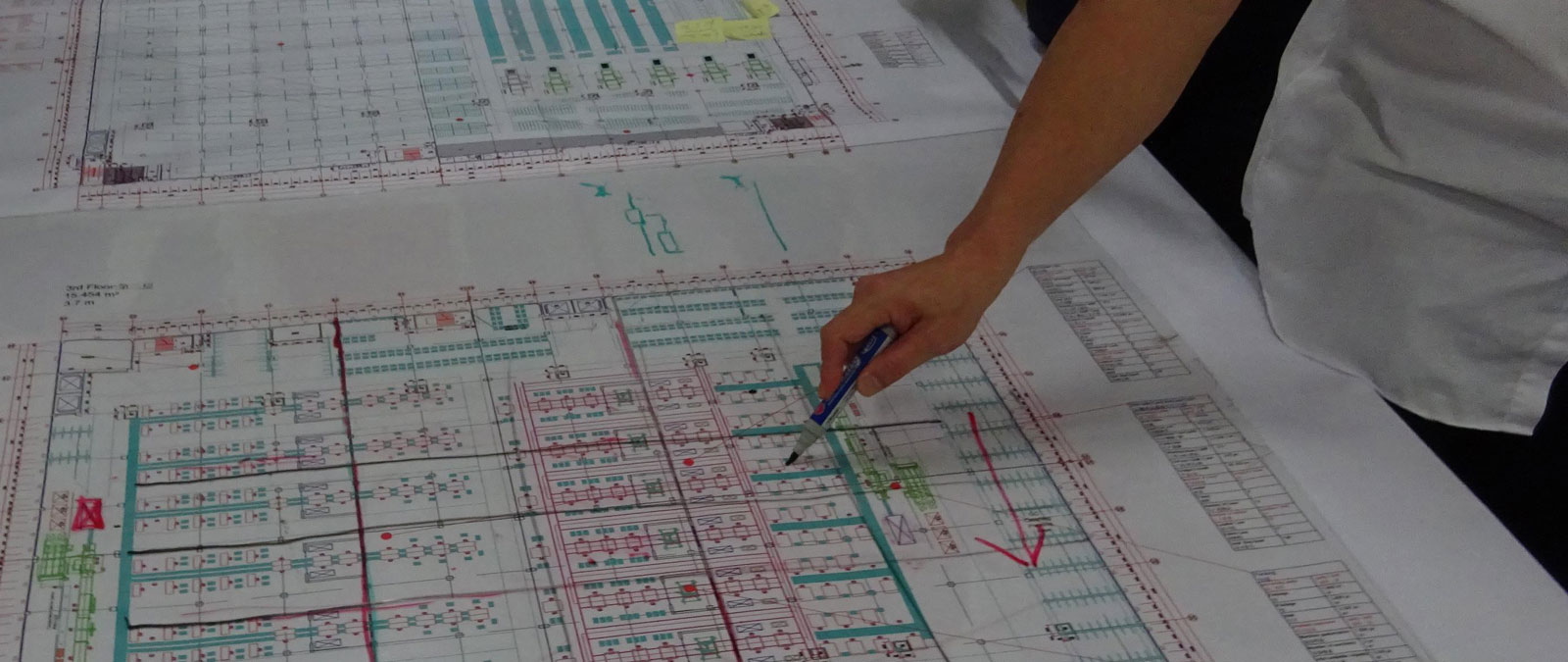
Das chinesische Unternehmen De Rucci fertigt hochwertige Polsterbetten und Nachttische. Erst 2004 gegründet, hat man sich in nur 13 Jahren zum Marktführer entwickelt. Der Anbieter aus Dongguan beschäftigt rund 2 000 Mitarbeiter und betreibt über das ganze Land verteilt mehr als 2 200 Showrooms. Um die stetig steigende Nachfrage zu befriedigen, baut der Hersteller im Moment ein komplett neues Werk inklusive Logistik-Zentrum und Verwaltungsgebäude. Für die strategische Planung ist er eine Partnerschaft mit Schuler Consulting eingegangen.
Denkt man an Möbelproduktion in China, vermutet man Massenherstellung von Möbeln im unteren und mittleren Preissegment. Beim ersten Besuch in der Produktion von De Rucci wurden die Mitarbeiter von Schuler Consulting jedoch eines Besseren belehrt.
Das Unternehmen aus Dongguan fertigt hochwertige Polsterbetten und Matratzen nach Kundenbestellung, die absolut deutschen Qualitätsansprüchen entsprechen. Da sich der Kunde sein Bett- und Schlafzimmerzubehör im Shop und/oder online selbst zusammenstellen kann, produziert man nach Bestellung auftragsbezogen. Betten, Nachttische, Matratzen, Bettwäsche und Kopfkissen entstehen komplett im eigenen Design und in eigener Produktion. Die hochwertigen Produkte beinhalten eine Zwei-Jahres-Garantie, was es in China sonst fast nie gibt.
Auf dem chinesischen Markt ist die Marke etabliert und hat ihre Kunden gefunden. Vor zwei Jahren wagte De Rucci dann den Schritt auf das internationale Parkett. Mit den „Healthy Sleeping Systems“ ist das Unternehmen inzwischen in vielen Metropolen der Welt anzutreffen, insgesamt 150 Showrooms gibt es, unter anderem in New York, Köln, Paris, Rom und in Ländern wie Dubai, Australien, Japan, Kanada und Ägypten. Um die steigende Nachfrage zu befriedigen, muss De Rucci nun die Produktionsfläche vergrößern. Geplant sind ein komplett neues Produktionsgebäude, ein Logistik-Zentrum sowie ein Verwaltungs- und Ausstellungsgebäude mit insgesamt 280 000 Quadratmetern. Aktuell hat man schon 140 000 Quadratmeter fertiggestellt, davon 80 000 Quadratmeter für die Polsterbetten- und Nachttischproduktion.
De Rucci und Schuler sind für die strategische Werksplanung eine Partnerschaft eingegangen. Die Hauptaufgabe war, alle verschiedenen Modelle der Polsterbetten und Nachttische in einem Produktionsgebäude zusammenzulegen und die Effizienz der Produktion um mindestens 30 Prozent zu steigern. Weiter sollten die Materialausnutzung erhöht und die Produktionsprozesse optimiert werden. Dies geschah alles mit dem Ziel, die Produktionskosten zu senken.
Aktuell erhalten die Angestellten bei De Rucci etwa den gleichen Lohn wie ihre Kollegen aus der Möbelbranche in Polen. Nur steigt dieser stetig, jährlich um etwa 20 Prozent. Besonders Mitarbeiter mit höheren Qualifikationen sind in China mittlerweile schwer zu finden. Deshalb soll das neue Werk nach den Richtlinien von Industrie 4.0 geplant und mit höchsten technischen Standards gebaut und ausgestattet werden: in Bezug auf Maschinen, innerbetrieblichen Transport und Informationstechnologie, besser bekannt als Produktionssteuerung. Zusätzlich soll die Produktion als Beispiel für moderne Fertigung, hohe Qualität und Zuverlässigkeit stehen. Das Werk liegt nämlich neben dem Ausstellungs- und Verwaltungsgebäude und eine Besichtigung ist für Kunden jeweils in den Werksrundgang integriert.
Als die Mitarbeiter von Schuler Consulting den Kunden das erste Mal trafen, waren sie noch etwas skeptisch, ob die hohen Zielvorgaben für das Unternehmen realistisch sind. Doch rasch wurde klar, dass die Reorganisation und die Optimierung zwingend sind. Entsprechend dem stetig steigenden Umsatz von De Rucci war über Jahre die Produktion schrittweise erweitert worden. Aus Platzmangel hat man die Produktion auf mehrere Standorte innerhalb des Großstadtbezirks Dongguan verteilt. Schon während des ersten ausführlichen Rundgangs durch das Unternehmen war ersichtlich, dass man hier „keinen Stein auf dem anderen“ würde lassen können. Erforderlich erschien eine komplette Neuplanung, gekoppelt mit der Zusammenlegung der einzelnen Teilwerke.
Die Fertigungstiefe der Produktion bei De Rucci ist enorm; Leder, Stoff, Watte, Schaum und Holzteile werden zugeschnitten, entsprechend vorgefertigt, zusammengeführt und zu Betten oder Nachttischen montiert und gepolstert. Deshalb haben die Mitarbeiter von Schuler Consulting als erstes die Prozesse der einzelnen Produktionsstandorte aufgenommen und analysiert. Die Menge an verschiedenen Konstruktionen, Formen und Materialien, welche in den Produkten mit unterschiedlichstem Design verwendet wird, ist überwältigend. Pro Schicht kommen rund 800 Betten und Nachttische aus der Produktion. Das heißt, dass täglich etwa 135 000 Holzteile, 60 000 Stoff- und Lederteile produziert, koordiniert, zusammengeführt und montiert werden müssen. Es war offensichtlich, dass die verschiedenen Prozesse standardisiert werden müssen, um sie dann als Einheit in einem Werk zusammenfassen zu können. Mit den standardisierten Prozessen ließen sich die Kapazitäten errechnen und Entwicklungsszenarien definieren. In der Diskussion mit der Geschäftsleitung hat man anschließend die Entwicklung bezüglich Umsätzen, Mitarbeiter und Investitionen definiert. De Rucci entschied sich für einen Investitionsplan in zwei Schritten.
Das Gesamtprojekt wurde in fünf Teile aufgeteilt: In die Bereiche Polsterbezugsfertigung, Schaumzuschnitt, Montage/Polsterei, Holzteile – als letzter Teil konnte erst zum Schluss die eigentliche Produktionsplanung gestartet werden. Denn erst wenn die Kapazitäten, Prozesse und Maschinen der einzelnen Bereiche definiert sind, ist es möglich, mit dem Zusammenfügen der Teilbereiche zu beginnen. Das Projektteam von De Rucci und Schuler hatte sich für eine kommissionsweise Fertigung entschieden. Die Produktionsmengen schwanken je nach Produkt zwischen einem und 20 Stück. Entsprechend müssen alle Fertigungsbereiche auch diese Flexibilität bieten. Der erste Projektteil war die Polsterbezugsfertigung. Die Bezugsmaterialien haben einen großen Anteil an den gesamten Materialkosten eines Polstermöbels. Hier simulierte und verglich man entsprechende Zuschnitt- und Nesting-Optionen. Für den Stoff-Zuschnitt wurde eine Kombination aus Mehrlagen- und Einzellagencuttern geplant. Beim Lederzuschnitt entschied man sich für eine InlineLösung, die die Häute zusammenhängend nacheinander scannt, nestet und schneidet. Alle weiteren Teilprozesse wie der Wattezuschnitt und die einzelnen Nähschritte wurden optimiert und dann für die neue Werksplanung vordefiniert. Das zweite Teilprojekt war der Schaumzuschnitt. Hier entwickelte man zusammen mit dem Schaumlieferanten ein neues Fertigungssystem, sodass der Kunde jetzt die A- und B-Teile zugeschnitten bezieht und die C-Teile maschinell selber zuschneidet.
Die Montage und Polsterei, das dritte Teilprojekt, bietet viel Optimierungspotenzial. Bis dato hat der Kunde mit einer Werkbankfertigung alle Möbel einzeln gepolstert. Dieser Vorgang wurde nun als Linienfertigung geplant. Die einzelnen Linien sind mit halbautomatischer Materialzuführung ausgestattet.
Die Holzteile-Fertigung als viertes Teilprojekt bestand bisher aus vielen Einzelschritten mit dem entsprechenden Handling und Transport. Das Ziel von De Rucci war, die Fertigungsprozesse zu vereinfachen, die Bestückung der Maschinen soweit wie möglich zu automatisieren und jeden Transport zu vermeiden. Um dies zu erreichen, hat man mit mehreren Maschinenherstellern zusammen eine Komplettlösung entwickelt. Sämtliche Plattenwerkstoffe für die Bettkästen und Nachttische werden jetzt in kleinen bis mittleren Losgrößen über automatische Linien gefertigt und in ein Teilelager gelegt. Die einzelnen Maschinen sind in drei flexiblen Maschinenstraßen verbunden. Daneben stehen noch fünf Einzelmaschinen für spezielle Prozesse wie die Schubkastenfertigung oder die 3D-Bearbeitungen.
Erst nach diesen Vorarbeiten konnte das letzte Teilprojekt, die gesamte Layoutplanung im neuen Gebäude, gestartet werden. Die Durchlaufzeit der Produktion hat De Rucci auf maximal fünf Tage definiert. Die verschiedenen Vorfertigungsprozesse (Teilprojekte) erhielten in der Layoutplanung den nötigen Platz und die geeigneten Materialbereitstellungen. Als Produktionskonzept entschied man sich für eine Kombination von auftragsbezogener und auftragsneutraler Fertigung.
Stoff und Leder werden künftig komplett kundenbezogen zugeschnitten und genäht, Schaum und Watte ebenfalls nach Kommission gefertigt beziehungsweise angeliefert. Sichtbare Holzteile werden in ein Teilelager produziert und dann kundenbezogen für die Montagelinien entnommen. Nur Spezialteile stellt man auftragsbezogen her. Die gesamte Layoutplanung ist nun abgeschlossen und die Pflichtenhefte für die Maschinen und Prozesse sind geschrieben. Die Produktion hat in den vorgesehenen 80 000 Quadratmetern Fläche Platz gefunden, die Fertigungs- und Montagelinien sind entsprechend dem Materialfluss angeordnet. Die Produktion gliedert sich übersichtlich und das Handling und die Transportwege sind kurz.
Für Schuler Consulting ist dieses Projekt komplex und mit den vielseitigen Produktionsprozessen anspruchsvoll. Um De Rucci gut zu verstehen und gezielt und effizient auf die hohen Anforderungen eingehen zu können, waren die Mitarbeiter sehr oft, teilweise über Wochen vor Ort. Dadurch hat sich eine gute, respekt- und vertrauensvolle Zusammenarbeit entwickelt. Das Projektteam von De Rucci brachte bei vielen Details klare Vorstellungen mit, die man dann stets diskutierte und gemeinsam definierte. Nur so war es möglich, die Werksplanung derart detailliert und qualitätsvoll zu gestalten und umzusetzen.
Für das Unternehmen stehen nun zwar hohe Investitionen an, die sich aber durch die Einsparungen rechnen werden. Die Wirtschaftlichkeit dieser Investitionen wurde mit Tests ausgewiesen. Weiter konnte der Output der Fertigung mit gleich viel Personal deutlich gesteigert werden. Derzeit bestellen die Verantwortlichen von De Rucci auf Basis der strategischen Werksplanung die Maschinen und innerbetrieblichen Transport- und Lagersysteme gemäß den Pflichtenheften. Die Zuschnittmaschinen für Stoff und Leder sind bereits angeliefert.
Mit der Umsetzung des Projekts kommt nun der schwierigste Teil für De Rucci. Die Fertigungen von verschiedenen Standorten müssen in das neue Gebäude umziehen. Bereichsweise wurde die Optimierung der Prozesse gestartet. Da fast alle Prozesse geändert werden, muss man die Mitarbeiter intensiv schulen. Der Umzug muss aus Kapazitätsgründen gestaffelt und auf die nächsten drei bis zehn Monate verteilt werden. De Rucci und Schuler Consulting setzen nach der strategischen Werksplanung die Partnerschaft fort. Schuler Consulting wird die gesamte Umsetzung und Implementierung für die nächsten 18 Monate begleiten. Ein zweites Team entwickelt den Informationsfluss von der Auftragsannahme bis zur Logistik für die Polster- und Matratzen-Produktion, sucht die entsprechende Software aus und unterstützt die Angestellten von De Rucci bei der Implementierung
Text und Bilder: Schuler
Ein Artikel des Fachmagazins HK, Ausgabe 3 / 2017 Lesen Sie den Artikel hier.