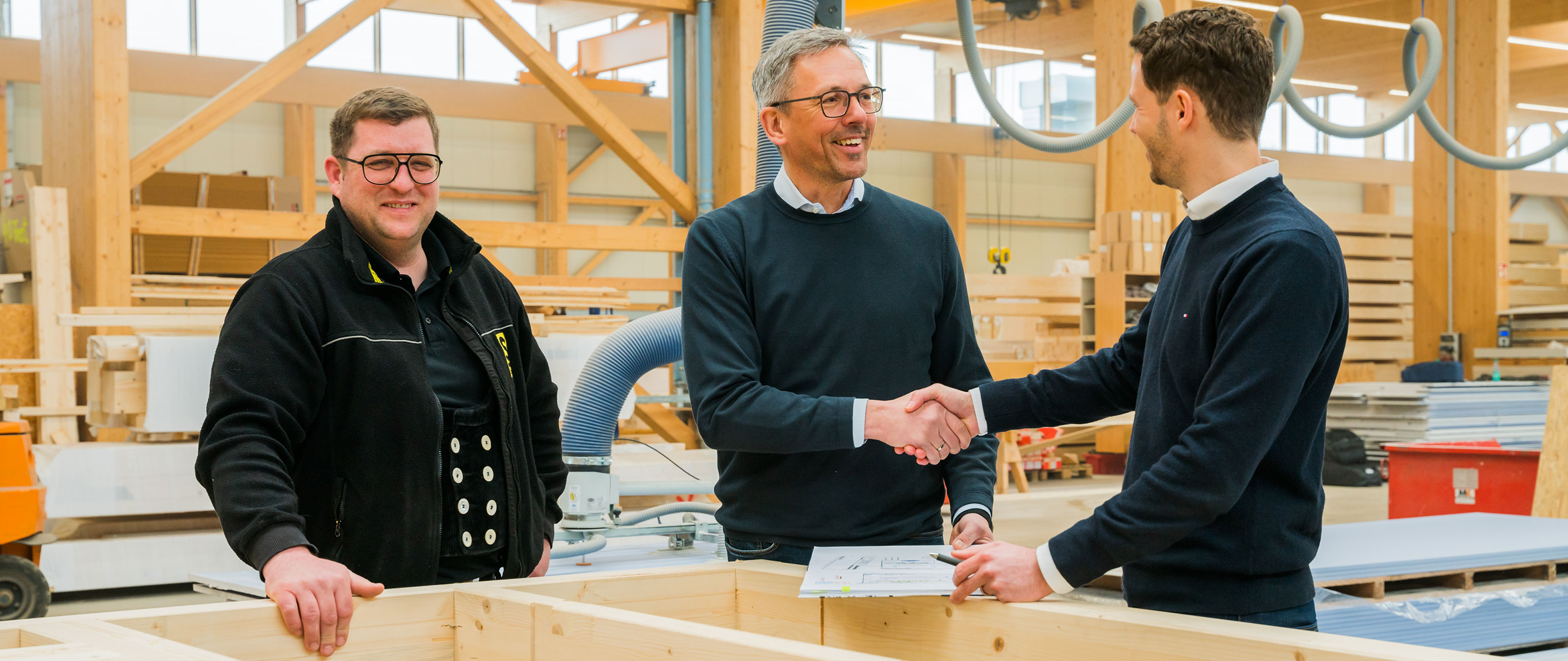
Die Geschichte der Gebr. Schütt KG ist eine Geschichte des Wachstums: Vor über 130 Jahren als Zimmerei gegründet, baute die Familie Schütt in den 60er-Jahren eine Brettschichtholz-Produktion auf und entwickelte das Unternehmen in den folgenden Jahrzehnten zu einem bundesweit tätigen Bauunternehmen mit eigenem Architekten- und Ingenieurbüro weiter. Heute geht der Betrieb den Schritt in die industrielle Fertigung und setzt dabei auf seine Mitarbeiter und die Unterstützung von Schuler Consulting. Tillmann Schütt, Geschäftsführer in fünfter Generation und Michael Postulart, Berater bei Schuler Consulting, sprechen über kleine Erfolge, große Veränderungen und die wichtige Rolle der Mitarbeitenden auf diesem Weg.
Das Interview führte Dr. Stefan Bockel.
Herr Schütt, Ihr Unternehmen entwickelt sich derzeit von einem mittelständischen Ingenieurholzbaubetrieb zu einem industriellen Bauunternehmen. Was war für Sie der Anlass auf diesem Weg die Unternehmensberatung Schuler Consulting miteinzubeziehen?
Tillmann Schütt (TS): Wir haben in unserem Unternehmen eine langjährige Mitarbeiter-zugehörigkeit: Viele Mitarbeiter sind mehr als 25-30 Jahre im Unternehmen, teilweise hat schon der Vater bei uns mitgearbeitet. Ich bin Geschäftsführer in fünfter Generation. Wir wollen heute den Schritt in die industrielle Fertigung gehen und kämpfen mit Gewohnheiten – mit Dingen, die wir ‘schon immer so gemacht haben’. Unsere Projekte werden größer. Wir brauchen eine schlanke Produktion, um dieses Wachstum zu bewältigen. Dabei habe ich gemerkt, dass ich mit meinen Mitteln zu langsam vorankomme. Ich habe schon länger mit dem Gedanken gespielt, externe Unterstützung zu suchen. 2021 war mein Produktionsleiter auf dem Weinmann-Treff, hat Schuler Consulting kennengelernt und kam mit leuchtenden Augen zurück. Das war für mich der Impuls, es jetzt anzugehen.
Herr Postulart, bei Ihrem Projekt mit der Firma Schütt geht es darum, Prozesse in der Produktion „schlanker“ zu machen und so die Produktivität im Betrieb zu erhöhen. Wie sind Sie ins Projekt gestartet?
Michael Postulart (MP): In unserem ersten Gespräch ging es darum, dass die neue Anlage in der Produktion nicht die gewünschte Leistung erreicht. Bei Schütt steht eine 4-Tisch Anlage mit einer Wallteq-Brücke und einer halbautomatischen Einblasdämmung. Das war der Anlass für einen Besuch vor Ort, durch den das Lean-Projekt ins Rollen kam. Wir sind mit einem kleinen Team von Schuler vorbeigekommen, um zu untersuchen, warum die Maschine zu viel Stillstand hat. Zuerst haben wir uns einen Überblick über die Brettschichtholzproduktion und den Holzrahmenbau verschafft. Dann haben wir eine Analyse der Holzrahmenbau-Produktion gemacht und Multi-Moment-Studien durchgeführt. Wir haben anhand von Spaghetti-Diagrammen die Arbeitswege der Mitarbeiter in der Produktion analysiert und festgestellt, dass die Mitarbeiter am Tag viele ‘unnötige’ Wege laufen, um beispielsweise Werkzeug zu holen und sie dadurch nicht an der Maschine stehen. Die Laufzeiten der Mitarbeiter zu reduzieren, war der erste Ansatzpunkt, um kurzfristige Verbesserungen in der Produktivität zu erzielen. Herr Schütt war mit unserer Arbeit zufrieden, sodass wir im Anschluss einen Katalog an Verbesserungsmaßnahmen für die ganze Produktion erarbeitet haben, den wir nun nach und nach abarbeiten.
Herr Schütt, es soll sich also noch einiges an den Prozessen in der Produktion verändern. Wie reagieren Ihre Mitarbeiter darauf? Wie nehmen Sie Ihr Team bei diesen Veränderungen mit?
TS: Meine Leute sind unglaublich fleißig. Wir setzen viel durch, aber man kann den Bogen nicht überspannen. Ab einem gewissen Punkt muss man einen Veränderungsprozess einleiten – auch aus dem Grund, die eigenen Leute nicht zu überfordern. Was man nicht tun sollte, ist mit jemanden von außen, einfach in die Produktion zu gehen und die Mitarbeiter nicht zu informieren. Man muss die Mitarbeiter mitnehmen und vorher mit ihnen sprechen, wer da kommt und was passiert. Sonst sind sie zutiefst misstrauisch und machen sich Sorgen, ob zum Beispiel ihr Arbeitsplatz wegrationalisiert wird oder Ähnliches. Mit Herrn Postulart und unserem Team passt das gut. Er spricht die Sprache der Mitarbeiter, bezieht sie ein und motiviert sie, am Veränderungsprozess teilzunehmen. So kommt etwas in Gang. Wichtig ist, dass wir die Ideen aufgreifen und danach auch umsetzen. Das passiert bei uns im vollen Arbeitsablauf. Diese Sachen sind keine Weltraumtechnik, aber man setzt sie oft nicht um. Durch die externe Unterstützung verpflichtet man sich selbst, die Sachen anzugehen und sich dafür ein Zeitfenster einzuräumen.
Herr Postulart, wie gehen Sie die Mitarbeitereinbindung im Projekt konkret an?
MP: Von der manuellen Arbeit zur Industrie – das ist ein Umdenken. Dafür braucht man Akzeptanz und ein Verständnis, wie eine schlanke Produktion aussehen kann. Wie Herr Schütt sagt, ist es enorm wichtig, dass man die Mitarbeiter dabei mitnimmt und mit ihnen kleine Erfolge feiert. Im Kern sprechen wir dabei über die simple Frage: „Was können wir machen, um euch den Tagesablauf zu vereinfachen?“ Dazu haben wir einen Workshop gemacht und das Ergebnis sofort in die Praxis umgesetzt. Das Ergebnis ist eine mobile Kappstation, mit der man in der Produktion nun flexibler arbeiten kann. Für mich ist es wichtig, dass jeder sieht: Ich kann etwas bewirken, wenn ich mich einbringe. Wir sind also mit einer kleinen Idee gestartet und haben diese umgesetzt. Das war ein kleiner, aber wichtiger Erfolg, den wir gemeinsam erreicht haben.
Welche “kleinen Erfolge” auf dem Weg zur industriellen Produktion haben Sie schon erreicht? Was steht als Nächstes an?
TS: Eine der ersten Verbesserungen in der Produktion war ein Rungenlager. Früher haben wir die Wände mehr oder weniger behelfsmäßig abgestützt. Jetzt haben wir einen zentralen Platz für die weiteren Bearbeitungsschritte und können die Fassaden fertig stellen und die Fenster einbauen.
MP: Das Rungenlager ist eine Eigenkonstruktion der Firma Schütt. Damit konnten wir den Materialfluss vor der Verladung optimieren. Ein Ziel des Projekts ist es, den allgemeinen Materialfluss in der Produktion zu optimieren, die Nutzung der Lagerflächen und die Logistik insgesamt zu optimieren.
Welches Optimierungspotential gibt es im Bereich Logistik?
TS: In den letzten zwei Jahren haben Lieferengpässe das Arbeiten bestimmt. Wir haben viel Material angeschafft und eigentlich unsere beste Halle als Lagerhalle „missbraucht“. Das wollen wir jetzt ändern. Unsere Leute laufen zu viele Wege, um ihr Material zu bekommen. Das ganze Thema Logistik wollen wir langfristig verbessern, indem wir einen Logistik-Mitarbeiter einstellen. Kurzfristig können wir die langen Wegzeiten bereits reduzieren, indem wir zusätzliches Werkzeug bereitstellen. Das ist günstiger als die Laufzeiten der Mitarbeiter.
MP: Der Logistik-Mitarbeiter kümmert sich um die Bereitstellung des Materials. Damit nicht ein Mitarbeiter, der gerade an der Riegelwerkstation steht, „mal eben“ einen LKW ablädt. Oder ein Werkstück manuell zur Kappstation getragen wird. Das sind zuerst viele kleine Themen, die den Materialfluss und die Ausnutzung der Lagerflächen verbessern. Danach widmen wir uns den großen strategischen Dingen.
TS: Die Zusammenarbeit mit Schuler ist gut definiert, wir fahren auf Sicht mit gutem Tempo und wollen langfristig zusammenarbeiten. Wir wollen das Projekt noch ausweiten und in der Leimhalle die gleichen Prozesse durchgehen. Es ist noch ein Umbau geplant und dann werden wir die Lagerlogistik umstellen.
Herr Schütt, die Optimierungen in der Produktion sind nur ein Teil der vielen Veränderungen, die in Ihrem Unternehmen anstehen. Wie gelingt es Ihnen an diesen Themen dranzubleiben?
TS: Ich bin durch Verbandsarbeit und die Teilnahme an Holzbauforum u.ä. gut informiert, was sich in der Branche tut – diese Dinge wissen meine Mitarbeiter nicht zwangsläufig. Es ist sehr wichtig, dass man die eigenen Ideen zur Unternehmensentwicklung und zur Entwicklung des Marktes an die Mitarbeiter weitergibt. Wir haben deshalb vor zwei Jahren ein Zielbild für die ganze Firma erstellt und eine PMO-Stelle (Project Management Office) geschaffen, die den Prozess begleitet. Der Prozess betrifft die ganze Firma. Es gibt verschiedene Arbeitsgruppen in Modulen, die alle 14 Tage zusammenkommen und alle 3 Monate machen wir einen „Deep Dive“. Die Arbeitsergebnisse aus diesen Gruppen werden regelmäßig an alle Mitarbeiter weitergegeben. Niemand kann sagen, er wisse nicht, was bei uns passiert.
Was würden Sie heute Ihren Branchen-Kollegen empfehlen, die auch ihren Betrieb industrialisieren wollen?
TS: Zuerst kann ich jedem, der seine Produktion automatisieren will, empfehlen, Schuler sofort mit einzubinden. Je klarer die Aufgabenstellung ist, umso besser kann man seine Fertigung auf den Punkt planen. Wenn ich zurückblicke, ist klar: Wir hatten kein eindeutiges Produktbild. Wir haben nicht das Einfamilienhaus, von dem wir wussten, wir bauen heute 80 Häuser und möchten uns nun auf 120, 150 steigern. Im gewerblichen Bereich sind wir mit unterschiedlichen Geschosshöhen unterwegs. Das sind Sonderbauten. Es war also nicht genau klar, worauf wir unsere Weinmann-Anlage ausrichten. Wir sind gestartet, indem wir die Anlage gekauft und dann den Schritt mit der Beratung nachgezogen. Das kann man auch anders machen. Außerdem finde ich die Beratung von Schuler, das „Firmen EKG“, sehr gut. Das eignet sich für alle, die überlegen, wo sie stehen. Man weiß mit der Beratungsleistung, was man zahlt, und hat schon mal einen richtigen Katalog mit Maßnahmen. Ich kann nur empfehlen, die externe Begleitung beizubehalten, damit man auch in der Umsetzung bleibt.
Videos
Bitte bestätigen Sie, dass bei der Nutzung von YouTube Daten wie Ihre IP-Adresse, Browser-Kennung und ähnliches an Google übermittelt werden können.
» Datenschutzerklärung
"Lean Production" in der Praxis.