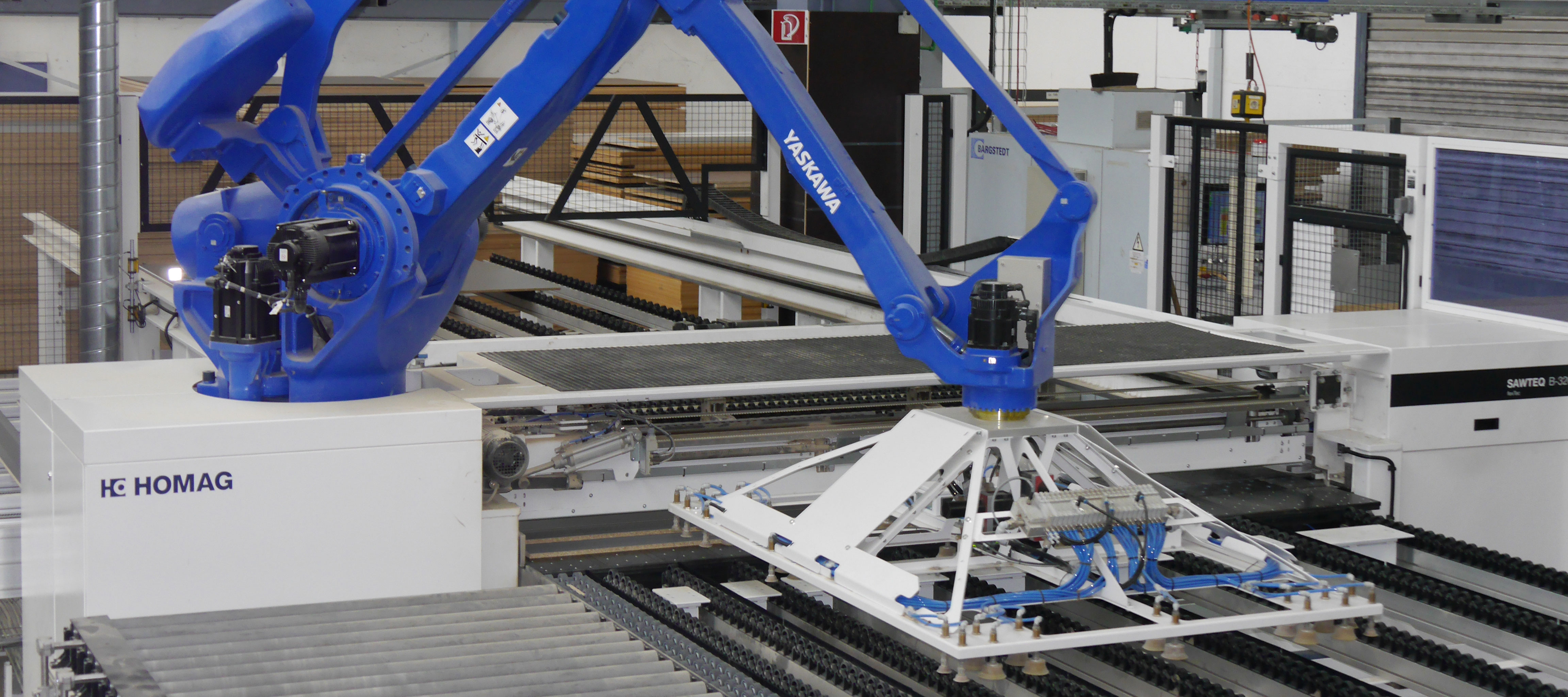
. To właśnie dlatego producent mebli łazienkowych zakupił dwie identyczne linie pilarskie ze zrobotyzowanym załadowywaniem firmy Homag Plattenaufteiltechnik, które są zasilane surowcem z automatycznych systemów magazynowania płyt. Dzięki zastosowaniu robotów przemysłowych Duravit osiąga dostępność prawie 100%. HK odwiedził firmę w Schenkenzell.
„Mamy około 87 000 aktualnych części oraz 20 000 części wycofanych z produkcji, które musimy być w stanie wyprodukować natychmiast”, mówi Ulrich Weber, dypl. inż. (FH) i kierownik zakładu w fabryce mebli Duravit AG w Schenkenzell w Schwarzwaldzie, opisując swoją pracę i sytuację zadaniową. „Nie mamy przy tym żadnych miejsc dla elementów meblowych – każda część produkcji jest częścią partii”. Nie ma więc znaczenia, jak duży jest element. W automatycznym procesie produkcyjnym występują dwa łożyska, ale są one nazywane buforami warstwowymi i sortującymi. Zapewniają one, że w linii formatu jest jak najmniej zmian i że system cięcia może optymalnie przetwarzać swoje plany cięcia. W sumie w ramach procesu Duravit opracowano 20 kryteriów i przedstawiono je w układzie sterowania procesem produkcyjnym w celu osiągnięcia jak największej efektywności.
Ulrich Weber w 1993 r. był producentem mebli łazienkowych i w znacznym stopniu przyczynił się do rozwoju zakładu, który do 1992 r. był fabryką mebli. Producent ceramicznych wyrobów sanitarnych chciał zwiększyć zakres produkcji, włączając do oferty meble łazienkowe i szafki pod umywalkę. Jako młody kierownik zakładu Weber od samego początku chciał realizować optymalny przebieg produkcji. Wraz z zespołem udało mu się to osiągnąć.
Każdy, kto odwiedza dziś fabrykę mebli Duravit w Schenkenzell, przeciera oczy ze zdumienia, myśląc, że odwiedza zakład produkcyjny dla przemysłu motoryzacyjnego. Cała produkcja jest zorganizowana w pełni automatycznie i zabezpieczona dwoma metrami ogrodzeń zabezpieczających. Mosty dla pieszych zapobiegają zakłóceniom procesu produkcji przez odwiedzających lub pracowników. „Dzięki wysokiemu poziomowi automatyzacji udało nam się również osiągnąć wysoką jakość, ponieważ nie ma już żadnych uszkodzeń podzespołów”, jak wyjaśnił Ulrich Weber. Wszystko zaczyna się od przycinania. W tym miejscu znajdują się dwie identyczne piły, każda składa się z jednej maszyny „Sawteq B-320 Flextec” ze zrobotyzowaną obsługą. Oba urządzenia są połączone za pomocą transporterów rolkowych i taśm transportowych z całą produkcją zorganizowaną w przemyśle. Obie „zrobotyzowane piły” są zaopatrywane w materiały płytowe z dwóch magazynów powierzchniowych, które są zorganizowane chaotycznie i sterowane komputerowo. Chodzi o magazyny, które odpowiadają w nowemu nazewnictwu Homag „Storeq S-500”.
Drugi magazyn powierzchniowy znajduje się w sąsiedniej hali i ma pojemność magazynową o jedną trzecią większą. Za pomocą wózka widłowego płyty surowe transportowane są w razie potrzeby do magazynu 1 i tam przejmuje je sterowanie komputerowe.
Magazyn powierzchniowy przejmuje zarówno magazynowanie, jak i sortowanie oraz wydawanie z magazynu dla pił, które są przeznaczone jako komórki do podziału do indywidualnego przycinania pojedynczych płyt i produkcji związanej ze zleceniem. Ze strony systemu sterowania procesem produkcyjnym zlecenia klienta zestawiane są według rodzaju materiału, aby wytworzyć możliwie najmniej odpadów. Po opracowaniu odpowiednich planów cięcia elementy, które nie muszą być okrawane, trafiają bezpośrednio do rozładunku. Elementy, które otrzymują obrzeże, są tymczasowo przechowywane w magazynie warstwowym „Sorteq H-600”, który działa jako bufor odsprzęgający, i w razie potrzeby podawane do jednostronnej okleiniarki „Edgeteq S-800” przez pośredni system transportowy. W ten sposób części o różnych rozmiarach mogą być uruchamiane jedna po drugiej — zlecenie po zleceniu.
Okleiniarka „Loopteq C-500” została zaprojektowana jako linia O, w której elementy są całkowicie oklejane w jednym do trzech przejść. Następnie elementy przechodzą do urządzenia sortującego 4-krotnie „TLB 210” lub bezpośrednio do rozładunku. Stacja odkładania z odkładaniem za pomocą robota zapewnia w tym miejscu wyprowadzenie elementów bez sortowania w podanej kolejności. W zależności od funkcji elementy są ponadto doprowadzane do centrów obróbkowych, które wykonują specyficzne dla danego elementu frezowanie, wiercenie lub cięcie. Część obrabianych przedmiotów jest poza tym lakierowana na kolory wybrane przez klienta. Zwłaszcza tutaj widoczne są zalety produkcji partii.
Roboty mają znaczący udział w sukcesie całej linii produkcyjnej, ponieważ przemieszczają panele za pomocą delikatnej technologii próżniowej. Ponadto zapewniają najwyższą jakość dzięki precyzyjnym ruchom. Dzięki skutecznym robotom przemysłowym przerwy w produkcji są wykluczone tak, że osiągnięta została prawie stuprocentowa dostępność. Dochodzi do tego również niezwykle niska częstotliwość występowania błędu.
Drukarka etykiet ze zintegrowanym skanerem kontrolnym zaznacza wszystkie elementy w pełni automatycznie, przy czym każda piła ma własną drukarkę, która na krótko przed opuszczeniem urządzenia przykleja etykietę z kodem kreskowym na przycięty element. Etykiety zawierają wszystkie informacje potrzebne do późniejszej obróbki.
Przy wydajności sięgającej 1500 elementów na zmianę znacznie zmniejszone są koszty sztuki w produkcji partii 1. Tym, co nie rzuca się w oczy zwiedzającym przyglądającym się procesom produkcyjnym, jest moc obliczeniowa komputerów, które bezgłośnie i niezawodnie pracują w czarnej skrzynce. Ponieważ to właśnie system Homag połączony w sieć z systemem sterowania „Controller MES” umożliwia w pierwszej kolejności realizację celów użytkownika. „Controller MES” przejmuje zadania klienta i produkcyjne z systemu planowania Duravit i odtwarza dane do sterowania poszczególnymi obrabiarkami.
„To, co podczas rozmowy handlowej wydaje się tak proste, w praktyce wygląda zupełnie inaczej” — podsumowuje swoje doświadczenia Ulrich Weber. „Radziłbym każdemu, kto chce kupić taki system, aby pomyślał o aspektach informatycznych, tak aby można było go wdrożyć”. Dla Ulricha Webera inwestycje w dwie „zrobotyzowane piły” i automatyczną linię wymiarowania nie mogą być podsumowane w prostym rachunku zwrotu kosztów. „Bo nie tylko kupiliśmy maszyny, ale też zmieniliśmy systemy i przygotowaliśmy się na przyszłość”, mówi Weber. Oczywiście kierownik zakładu sam wie, jaką wartość w kalkulacji zwrotu kosztów stanowi zaoszczędzony pracownik. W jaki sposób można jednak przedstawić dane dotyczące krótszych dostaw, wyższej jakości, elastyczności i wysokiej dostępności urządzeń?
Ulrich Weber nie udziela odpowiedzi, ale odkrył już nowe pole działania. Chce zmniejszyć ilość odpadów na swoich „zrobotyzowanych piłach”. „Każdy procent to 50 000 euro”, mówi.
„Dzięki wysokiemu poziomowi automatyzacji udało nam się również osiągnąć wysoką jakość, ponieważ nie ma już żadnych uszkodzeń podzespołów”Ulrich Weber, i kierownik zakładu w fabryce mebli Duravit AG w Schenkenzell