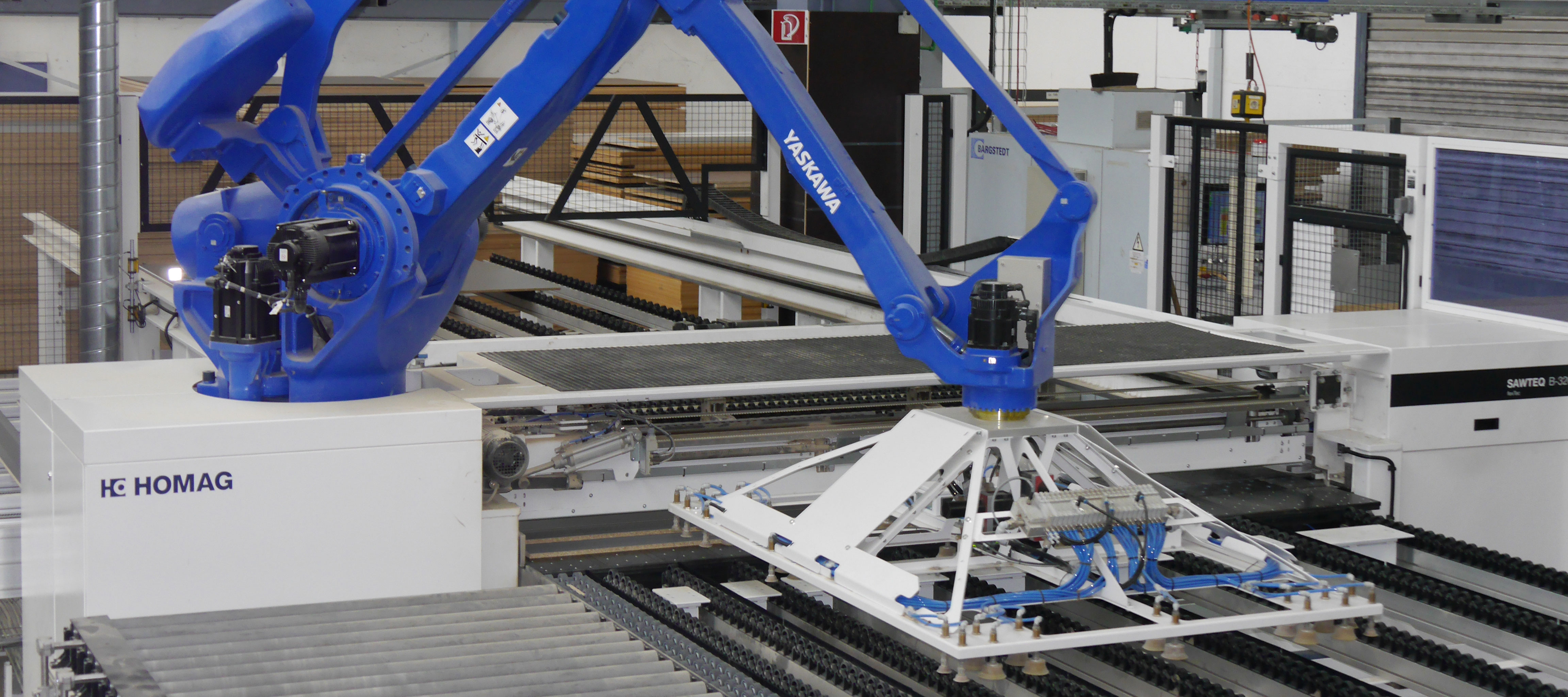
Por este motivo, o fabricante de móveis para banheiro comprou dois sistemas de corte idênticos com alimentação por robô, uma tecnologia de corte de painéis da Homag, que são alimentados com painéis a partir de gerenciadores de estoque. Ao utilizar robôs industriais, a Duravit alcança praticamente 100% de disponibilidade. A HK visitou a empresa em Schenkenzell.
"Temos atualmente cerca de 87 000 peças, mais 20 000 peças de saída, que temos de ser capazes de produzir imediatamente", afirma Ulrich Weber, engenheiro (FH) e gestor da fábrica de móveis Duravit AG em Schenkenzell, na Floresta Negra. "Não temos espaço de armazenamento para peças de mobiliário; cada peça produzida pertence a um pedido." Portanto, o tamanho da peça não faz diferença. É verdade que existem dois estoques no processo de fabricação automática, mas estes correspondem a buffers e posições de classificação. Ambos garantem que existe o mínimo possível de alterações na linha de esquadra bordas e que as seccionadoras conseguem processar os respectivos planos de corte de forma ideal. No total, na Duravit foram desenvolvidos 20 critérios que são armazenados no controle de produção para atingir a máxima eficiência.
Ulrich Weber juntou-se ao fabricante de móveis para banheiros em 1993 e desempenhou um papel fundamental no desenvolvimento da fábrica, que até 1992 era uma fábrica de tecidos. O fabricante de cerâmica sanitária pretendia expandir a sua produção e também incluir móveis para banheiros e bases para lavatórios no seu portfólio. Enquanto jovem gestor de fábrica, Weber teve vontade de concretizar um fluxo de produção ideal desde o início, o que conseguiu realizar juntamente com sua equipe.
Qualquer pessoa que visitar a fábrica de móveis Duravit em Schenkenzell ficará impressionado, porque achará que está visitando uma fábrica de produção na indústria automobilistica. Toda a produção é totalmente automatizada e protegida com cercas de protecção de dois metros de altura. As pontes pedonais impedem que os visitantes ou trabalhadores interfiram no fluxo de produção. "Com o elevado grau de automatização, conseguimos também um aumento da qualidade, pois praticamente não ocorrem danos aos componentes", explica Ulrich Weber. Isto começa com o corte. Existem dois sistemas de corte idênticos, cada um constituído por uma "Sawteq B-320 Flextec" com manuseio automatizado. Ambos os sistemas estão ligados a toda a produção, organizada através de transportadores de rolos e esteiras de transporte. Ambas as "seccionadoras robóticas" são alimentadas com painéis através de dois gerenciadores de estoque, que são organizados de forma caótica e controlados por computador. Estes são os gerenciadors "Storeteq S-500" da Homag.
O segundo sistema de estoque está localizado no galpão vizinho e tem uma capacidade de armazenamento três vezes maior. Os painéis são transportados para o gerenciador 1 com uma empilhadeira, onde são assumidos pelo controle computarizado.
O gerenciador de estoque controla o armazenamento e a separação, bem como o transporte para o corte, ou seja, para as seccionadoras de corte de painéis individuais sob medida. O comando de produção reúne os pedidos de clientes de acordo com o tipo de material, de forma a gerar o mínimo de desperdício possível. Depois de processados os planos de corte, as peças que não necessitam da aplicação de bordas vão diretamente para o empilhamento. As peças que precisam passar pela colagem de bordas, são armazenados temporariamente num armazenamento por camadas "Sorteq H-600", que atua como um pulmão de peças, e deslocadas através de um transporte intermédio para a coladeira dupla "Edgeteq S-800". Desta forma, as peças com tamanhos diferentes podem ser transportadas em rapidamente, uma após a outra.
O sistema de retorno de peças "Loopteq C-500" foi programado como uma linha em "O" - circular, na qual todos os lados das peças podem ser colados em três passagens. Os componentes vão então para um separador de 4 vias "TLB 210" ou diretamente para o empilhamento. A estação de empilhamento com desempilhamento robotizado garante o desarmazenamento dos componentes de um lote de separação na sequência especificada. Dependendo da funcionalidade, os componentes também são conduzidos para centros de usinagem e furação que realizam trabalhos de fresagem, furação ou cortes específicos. Uma parte do lote de peças também é conduzida para a pintura, onde são aplicadas as cores específicas do cliente. Aqui, as vantagens da produção em série tornam-se particularmente evidentes.
Os robôs têm um papel significativo no sucesso de toda a linha de produção, uma vez que movem as placas com uma tecnologia de vácuo suave. Além disso, garantem a mais elevada qualidade possível através de movimentos precisos. De acordo com os próprios dados da empresa, as interrupções da produção são praticamente impossíveis com o robô industrial testado, e é alcançada uma disponibilidade de praticamente 100%. Além disso, a taxa de erro é extremamente baixa.
A impressora de etiquetas com scanner de controlo integrado marca todas as peças automaticamente, pelo que cada sistema de corte tem a sua própria impressora, que cola a etiqueta do código de barras à peça cortada pouco antes de sair do sistema. As etiquetas contêm todas as informações para o processamento posterior.
Com um desempenho de até 1500 peças por turno, os custos unitários na produção de lote de tamanho 1 são significativamente reduzidos. O que o visitante não compreende imediatamente ao olhar para as sequências de produção é o desempenho dos computadores que funcionam de forma silenciosa e confiavel no Black Box. A razão para tal é que o sistema da Homag, que está ligado em rede com o sistema de controle "Controller MES", e que permite ao usuário atingir os seus objectivos. O "Controller MES" assume os pedidos de clientes e as tarefas de produção a partir do sistema de planejamento da Duravit e envia os dados para os comandos das máquinas de processamento.
"O que soa tão simples durante uma conversa de vendas, parece consideravelmente diferente na prática", afirma Ulrich Weber. "Aconselho qualquer pessoa que pretenda comprar este tipo de sistema a pensar do ponto de vista técnico, a fim de poder implementar algo assim." Para Ulrich Weber, os investimentos nas duas "seccionadoras robotizadas" e na linha de esquadra borda automática não devem ser realizados com um cálculo de amortização simples. "Porque não só compramos máquinas, como também mudamos sistemas e nos preparamos para o futuro", acrescenta Weber. Naturalmente, o próprio gestor da fábrica sabe o valor que representa a economia de um funcionário no cálculo da amortização. Mas como podemos mensurar tempos de entrega mais curtos, a qualidade mais elevada, a flexibilidade e a elevada disponibilidade da fábrica em números?
Ulrich Weber não fornece respostas, mas já descobriu uma nova atividade. Pretende reduzir o desperdício nas suas "seccionadoras robóticas". "Cada ponto percentual nos retorna 50 000 Euros", afirma com astúcia.
«Com o elevado grau de automatização, conseguimos também um aumento da qualidade, pois praticamente não ocorrem danos aos componentes»Ulrich Weber, da fábrica de móveis Duravit AG em Schenkenzell