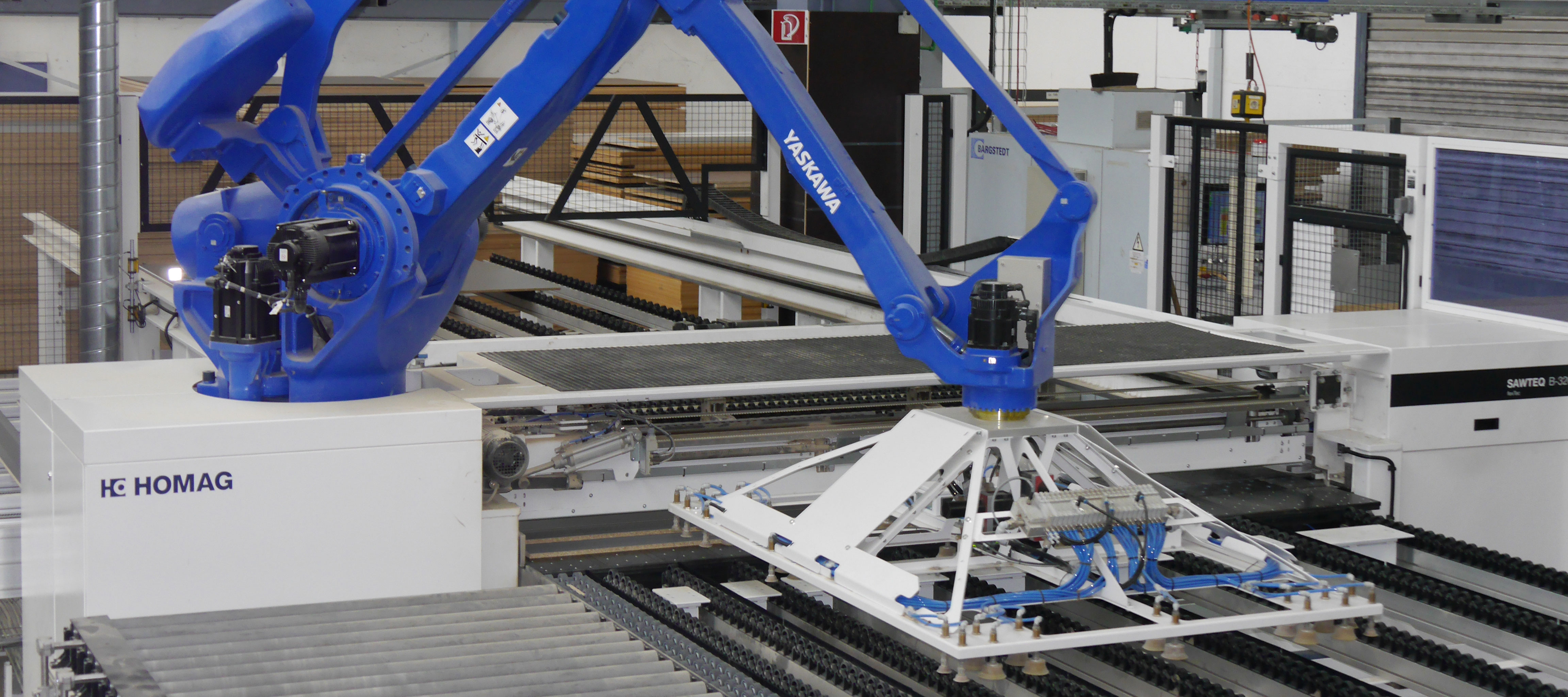
Chez Duravit, les dirigeants accordent une importance capitale à la rapidité et à la souplesse. C'est la raison pour laquelle le fabricant de meubles de salle de bain a fait l'acquisition de deux installations de sciage identiques, avec alimentation robotisée issue de la technique de découpe de panneaux Homag, et dont le chargement en matières premières s'effectue automatiquement depuis un stockeur à panneaux. L'utilisation des robots industriels permet à Duravit d'atteindre une disponibilité proche des 100 %. HK s'est rendu dans l'entreprise, à Schenkenzell, pour une visite.
« Nous avons environ 87 000 pièces actuelles et 20 000 pièces de fin de série que nous devons être en mesure de produire immédiatement », explique Ulrich Weber, ingénieur diplômé (FH) et directeur de l'usine de meubles Duravit AG à Schenkenzell dans la Forêt Noire, pour décrire son travail et ses missions. « De ce fait, nous n'avons pas de lieu de stockage pour les éléments de meubles : chaque pièce en production fait partie d'une commande ». La taille de la pièce n'a donc aucune importance. Le processus de fabrication automatique comprend deux stockeurs, appelés tampon de couches et tampon de triage. Tous deux veillent à ce qu'il y ait le moins de changements possible sur la ligne de calibrage et à ce que le système de découpe puisse traiter ses plans de coupe de manière optimale. Au total, Duravit a développé 20 critères et les a enregistrés dans le système de contrôle de la production, afin d'atteindre une efficacité maximale.
Ulrich Weber a rejoint le fabricant de meubles de salle de bain en 1993 et a joué un rôle important dans le développement de l'usine, qui était jusqu'en 1992 une usine de draperie. Le fabricant de céramique sanitaire souhaitait augmenter le niveau d'intégration de sa production et inclure dans sa gamme des meubles de salle de bain et des structures sous lavabo. En tant que jeune directeur d'usine, Ulrich Weber avait la volonté dès le début de mettre en place un flux de production optimal. Avec son équipe, il y est parvenu.
Quand on visite aujourd'hui l'usine de meubles Duravit à Schenkenzell, on se frotte les yeux car on croirait visiter une usine de production pour l'industrie automobile. L'ensemble de la production est organisé de manière entièrement automatique et sécurisée par des grillages de protection de deux mètres de haut. Les passerelles pour piétons empêchent les visiteurs ou les opérateurs de perturber le flux de production. « Avec ce haut niveau d'automatisation, nous avons également pu améliorer la qualité, car les pièces de construction ne sont pratiquement plus endommagées », explique Ulrich Weber. Tout commence avec la découpe. Il y a deux installations de sciage identiques, chacune composée d'une « Sawteq B-320 Flextec » avec manipulation robotisée. Les deux installations sont reliées à l'ensemble de la production par des convoyeurs à rouleaux et des bandes transporteuses, dans une organisation industrielle. Les deux « scies robots » sont alimentées en panneaux de manière aléatoire par deux stockeurs à plat commandés par ordinateur. Il s'agit de stockeurs qui correspondent à la nouvelle appellation Homag « Storeteq S-500 ».
Le deuxième stockeur à plat se trouve dans une salle voisine et offre une capacité de stockage supérieure d'un tiers par rapport à l'autre. Les panneaux bruts sont transportés vers le stockeur 1 par chariot élévateur à fourche, en fonction des besoins, où ils sont pris en charge par le système de contrôle informatique.
Le stockeur à plat gère à la fois le stockage et le triage, ainsi que l'acheminement vers les scies, qui sont conçues comme des cellules de découpe avec coupe individuelle de chaque panneau et production en fonction des commandes. Le système de contrôle de la production regroupe les commandes des clients selon le type de matériau, afin qu'il y ait le moins de chutes possible. Après avoir été traitées par les plans de coupe correspondants, les pièces qui n'ont pas besoin de finition de chant sont directement acheminées vers l'empilage. Les pièces de construction qui reçoivent une finition de chant sont stockées temporairement dans une unité de stockage « Sorteq H-600 », qui fonctionne comme un tampon de découplage, et sont acheminées vers la machine d'usinage de chants unilatérale « Edgeteq S-800 », via un système de transport intermédiaire. De cette manière, des pièces de tailles différentes peuvent être produites les unes après les autres, commande par commande.
Le système de circulation de pièces « Loopteq C-500 » est conçu comme une ligne en O, sur laquelle un placage de chants complet est effectué sur les pièces en un à trois passages. Ensuite, les pièces de construction passent dans un trieur quadruple « TLB 210 » ou directement à l'empilage. La station d'empilage robotisé assure alors la sortie stockeur des pièces d'un lot de triage dans l'ordre indiqué. En outre, selon leur fonctionnalité, les pièces sont amenées vers des centres d'usinage qui effectuent des travaux de fraisage, de perçage ou de sciage. Une partie des pièces est également mise en peinture, avec les couleurs spécifiées par le client. C'est là, en particulier, que les avantages de la production à la commande sont les plus évidents.
Les robots jouent un rôle important dans la bonne exécution de l'ensemble de la chaîne de production, car ils déplacent les panneaux en douceur à l'aide d'une technologie d'aspiration. En outre, ils assurent une qualité optimale grâce à des mouvements précis. Selon l'entreprise, les interruptions de production sont quasiment impossibles avec ce robot industriel éprouvé ; il atteint un taux de disponibilité de presque 100 %. A cela s'ajoute un taux d'erreur extrêmement faible.
L'imprimante d'étiquettes, avec scanner de contrôle intégré, identifie automatiquement toutes les pièces. Chaque installation de sciage dispose de sa propre imprimante qui colle son étiquette à code-barres sur la pièce découpée, juste avant qu'elle ne quitte l'installation. De ce fait, les étiquettes contiennent toutes les informations nécessaires à un usinage ultérieur.
Avec un rendement allant jusqu'à 1 500 pièces par équipe, les coûts unitaires sont ainsi considérablement réduits par lot unitaire. Ce que ne perçoivent pas immédiatement les visiteurs qui découvrent le déroulement de la production, c'est la puissance des ordinateurs qui fonctionnent silencieusement et efficacement dans la boîte noire. En effet, l'installation Homag connectée au système de guidage « Contrôleur MES » permet d'atteindre les objectifs de l'utilisateur. Le « Contrôleur MES » gère les commandes des clients et de la production dans le système de planification de Duravit et transmet les données aux commandes des différentes machines de traitement.
« Ce qui semblait si simple lors de l'entretien de vente s'est révélé bien différent dans la pratique », souligne Ulrich Weber pour résumer son expérience. « Je conseillerais à tous ceux qui veulent acheter une telle installation de penser aux aspects informatiques afin de pouvoir mettre en œuvre tout ceci ». Pour Ulrich Weber, les investissements dans les deux « scies robots » et la ligne de calibrage automatique ne peuvent se résumer à un simple calcul d'amortissement. « Parce que nous ne nous sommes pas contentés d'acheter des machines, nous avons changé de système et nous nous sommes préparés pour l'avenir », a-t-il ajouté. Bien sûr, le directeur de l'usine sait ce que représente un collaborateur de moins dans le calcul de l'amortissement. Mais comment traduire en chiffres la réduction des délais de livraison, l'amélioration de la qualité, la flexibilité et un haut niveau de disponibilité des installations ?
Ulrich Weber ne donne pas de réponse, mais il a déjà découvert un nouveau domaine d'activité. Il veut réduire les chutes de ses « scies robots ». « Chaque pour cent rapporte 50 000 euros », dit-il avec malice.
« Avec ce haut niveau d'automatisation, nous avons également pu améliorer la qualité, car les pièces de construction ne sont pratiquement plus endommagées, »Ulrich Weber, et directeur de l'usine de meubles Duravit AG à Schenkenzell