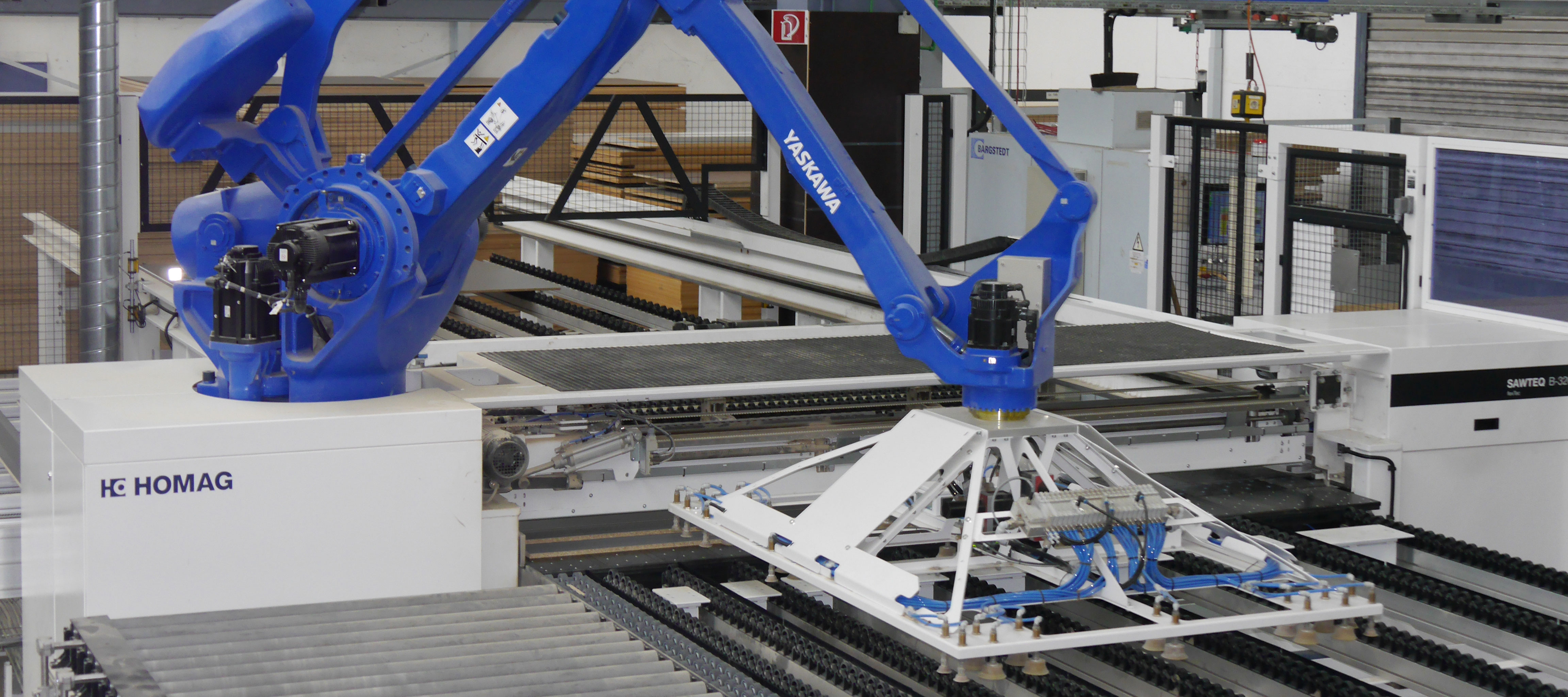
Поэтому на фабрике этого производителя мебели для ванных комнат работают две идентичные пильные установки Homag Plattenaufteiltechnik, оснащенные устройством роботизированной загрузки, подключенным к автоматическим складам плит. Благодаря внедрению промышленных роботов эксплуатационная готовность оборудования на производстве Duravit достигает почти 100 процентов. Журналист HK посетил предприятие в Шенкенцеле.
«В нашем ассортименте 87 000 деталей, кроме того, мы в любой момент можем изготовить еще 20 000 деталей для уже снятых с производства моделей», — описывает свою задачу Ульрих Вебер, дипломированный инженер и начальник производства в Шенкенцеле (Шварцвальд). «При этом у нас нет склада, на котором можно было бы хранить детали мебели — сразу после изготовления они распределяются по соответствующим комплектам, поэтому размер детали не имеет значения. В процессе автоматизированного производства задействованы только два склада: буферный и сортировочный. Работа обоих организована таким образом, чтобы сократить со минимума количество перемещений на линии форматной обработки и оптимизировать работу оборудования согласно схемам раскроя. В общей сложности компания Duravit разработала 20 критериев, которые используются в управлении производственным процессом для обеспечения его максимальной эффективности.
Ульрих Вебер пришел в компанию в 1993 году и с тех пор активно участвует в развитии фабрики в Шенкенцеле, на которой до 1992 года производили сукно. Компания Duravit, основное направление деятельности которой — изготовление санитарно-технической керамики, решила углубить производство и включить в свое портфолио мебель для ванных комнат и тумбы под раковину. С самого начала своей работы Вебер, тогда еще молодой руководитель производства, поставил перед собой цель оптимизировать технологические потоки. С помощью своей команды он достиг этой цели.
Сегодня посетители мебельной фабрики Duravit в Шенкенцеле не верят своим глазам — им кажется, что они попали на автомобильный завод. Все производство полностью автоматизировано, оборудование окружено двухметровым защитным ограждением. Посетители и сотрудники передвигаются только по пешеходным мостикам, что помогает избежать нарушений технологических потоков. «Высокий уровень автоматизации позволил нам значительно повысить качество, полностью исключив повреждения деталей», — поясняет Ульрих Вебер. Технологический процесс начинается с раскроя. На этом участке работают две пильные установки, каждая из которых состоит из станка Sawteq B-320 Flextec и роботизированного загрузочного устройства. С другими производственными участками установки соединены рольгангами и ленточными транспортерами. Плитные материалы на «роботизированные пилы» подаются из двух управляемых компьютером систем штабельного хранения с неупорядоченной укладкой плит. Сейчас такое оборудование поставляется компанией Homag под названием Storeteq S-500.
Вторая система штабельного хранения, вместимость которой на треть больше, размещена в соседнем цеху. При необходимости вилочный погрузчик перевозит необработанные плиты на склад 1, где их принимает система компьютерного управления.
Система штабельного хранения обеспечивает загрузку на склад, сортировку и подачу в зону загрузки настроенных на позаказное производство пильных станков, которые раскраивают отдельные плиты согласно индивидуальным схемам. Система управления производством группирует заказы по типу материала, чтобы сократить количество отходов. После раскроя в соответствии со схемами детали, на которые не нужно наносить кромочный материал, выгружаются в штабели. Если деталь должна быть окантована, ее перемещают в накопитель Sorteq H-600, выполняющий функцию разделительного буфера, и при необходимости по промежуточному транспортеру передают на односторонний станок для обработки кромок Edgeteq S-800. Таким образом обеспечивается последовательная комплектация заказов, включающих детали разного размера.
Транспортировочная система Loopteq C-500 представляет собой O-образную линию, по мере прохождения которой на детали за один-три цикла наносится кромочный материал. После этого заготовки перемещаются в сортировщик TLB 210 с 4 транспортерами или непосредственно в устройство укладки штабеля. Участок отгрузки штабелей с роботизированным устройством штабелирования обеспечивает выгрузку рассортированных согласно заказам деталей в заданной последовательности. После этого детали транспортируются к обрабатывающим центрам, где выполняются требуемые операции фрезерования, сверления и раскроя. Часть заготовок отправляется на участок покраски, где окрашивается разные цвета согласно заказу. На этом этапе становятся особенно очевидными преимущества позаказной организации производства.
Успешной работой производственная линия в значительной степени обязана роботам, так как благодаря вакуумным присосам они перемещают плиты особенно бережно. Исключительная точность перемещений также помогает поддерживать высочайший стандарт качества. По данным компании зарекомендовавшие себя на практике промышленные роботы позволили практически полностью исключить остановки производства и обеспечивают почти стопроцентную эксплуатационную готовность. Также здесь стоит упомянуть крайне низкую частоту ошибок.
Принтер для этикеток с интегрированным контрольным сканером в полностью автоматическом режиме маркирует заготовки. Каждая пильная установка оснащена собственным принтером, который наклеивает этикетку со штрихкодом на деталь перед ее выгрузкой из установки. Этикетки содержат всю информацию о последующих обрабатывающих операциях.
При производительности до 1500 деталей в смену себестоимость каждой детали при производстве индивидуальной продукции значительно сокращается. Есть еще один важный фактор организации производства, который не сразу бросается в глаза наблюдателю: это тихая и надежная работа компьютеров. Выполнение поставленных задач обеспечивает система управления Controller MES, которой оборудована подключенная к сети обмена данными установка производства Homag. Система Controller MES получает клиентские и производственные заказы из системы планирования компании Duravit и передает соответствующие данные в системы управления отдельных обрабатывающих станков.
«Когда покупатель обсуждает свой заказ с консультантом, все выглядит просто; на практике все совсем иначе», — подводит итог Ульрих Вебер. «Я советую каждому, кто планирует покупать подобное оборудование, обдумать применение компьютерных систем управления». По мнению Ульриха Вебера, решение о приобретении двух роботизированных пильных станков и автоматической линии форматной обработки нельзя принимать только на основании простого расчета окупаемости. «Мы не просто купили станки, мы внедрили новую систему, благодаря которой мы теперь готовы к требованиям будущего», — говорит г-н Вебер. Разумеется, руководитель учел при расчете окупаемости автоматического оборудования возможность использовать сотрудников на других участках. Но как подсчитать эффект уменьшения сроков поставок, повышения качества, гибкости и эксплуатационной готовности оборудования?
Ульрих Вебер не знает ответа, но он открыл для себя новую область приложения усилий. Он собирается сократить количество отходов раскроя, образующихся при работе роботизированных пильных станков. «Сокращение всего на один процент принесет нам 50 000 евро», — объясняет он с хитрой улыбкой.
«Высокий уровень автоматизации позволил нам значительно повысить качество, полностью исключив повреждения деталей»свою задачу Ульрих Вебер, дипломированный инженер и начальник производства