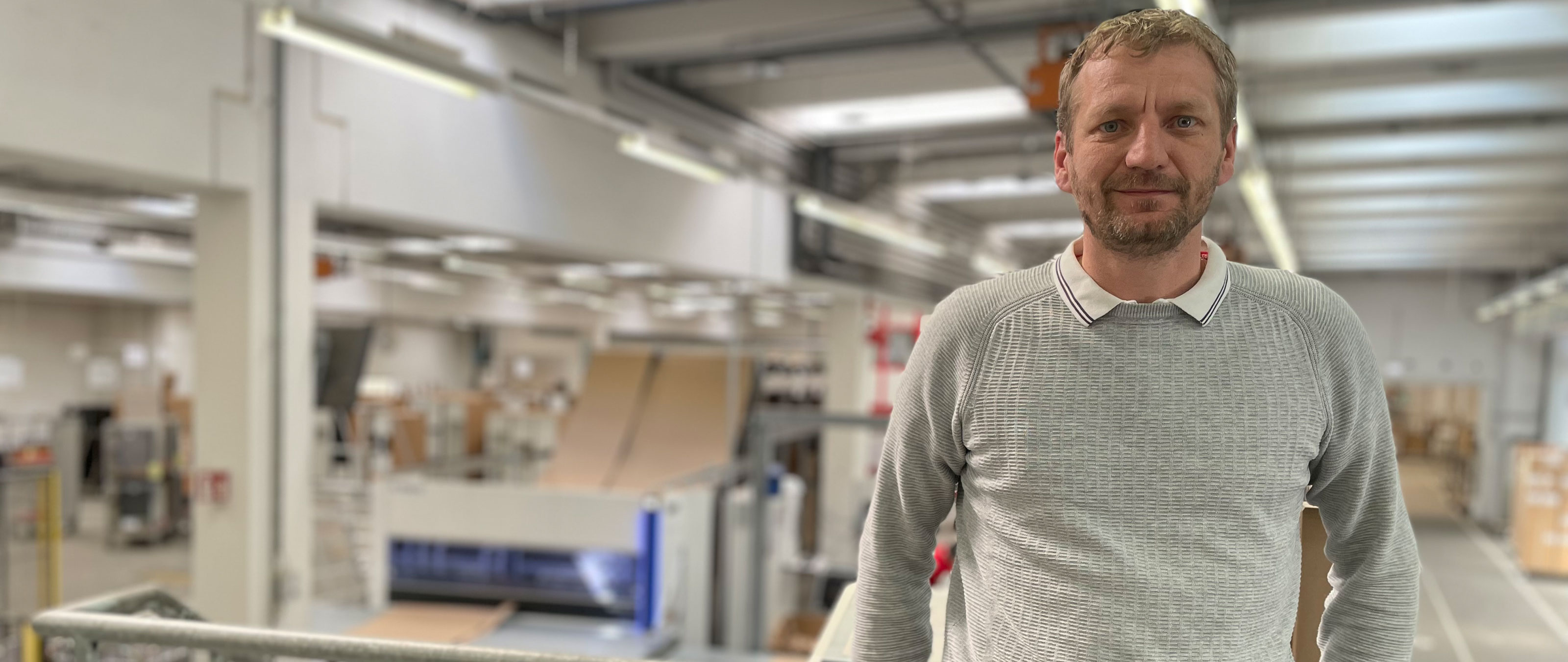
Dlatego takie znaczenie ma tu jakość i dbałość o szczegóły — i właśnie takie kuchnie produkuje w mieście Wels w Górnej Austrii firma ewe Küchen. Aby jej produkty mogły bezpiecznie dotrzeć do odbiorców, od początku roku firma ewe wykorzystuje do pakowania maszynę do cięcia kartonów marki HOMAG.
W 2021 roku w Austrii sprzedano łącznie 209 900 kuchni. Oznacza to, że w nową kuchnię zainwestowało średnio co dwudzieste austriackie gospodarstwo domowe. O sporej dynamice na rynku kuchennym w tym alpejskim kraju wskazuje również wzrost popytu, który w 2021 roku wyniósł całe 7,9% względem roku poprzedniego, a w firmie ewe aż 24%. Towarzyszyło temu także zwiększenie udziału tego przedsiębiorstwa w rynku o 1,3%. Oprócz wzrostu popytu rok 2021 pokazał również, że klienci oczekują coraz wyższej jakości i zwracają szczególną uwagę na detale i wyposażenie.
Samodzielna produkcja na zamówienie
Firma ewe, należąca do grupy Nobia, największego producenta kuchni w Europie, dostarcza wysokiej jakości kuchnie na indywidualne zamówienie. Grupa obejmuje takie marki, jak ewe z nowoczesnymi kuchniami, FM ze współczesnymi kuchniami w stylu tradycyjnym oraz INTUO z projektami awangardowymi. Marki te świetnie się uzupełniają. Dla przykładu kuchnia „ewe Fina” z matową powierzchnią „ewe nanoo” jest najpopularniejszym modelem z Wels, a z kolei „FM Hirschalm” jako nowa interpretacja kuchni klasycznej łączy wpływy tradycyjnej kultury austriackiej z nowoczesnym wykonaniem.
Kuchnie ewe są produkowane w zakładach w Wels i Freistadt. Realizowane są tu zamówienia indywidualne, a praca odbywa się na zasadzie produkcji w sieci w trybie ciągłym i z dużym udziałem produkcji własnej. „Każda szafka jest wykonywana na zamówienie” — podkreśla Michael Sterrer, kierownik ds. inżynierii w Wels. „Każda ścianka, półka czy szuflada jest produkowana indywidualnie. Każdy pojedynczy element jest od początku przypisany do konkretnego zlecenia”. Jeden korpus powstaje w trzy dni, a dziennie z linii schodzi 1000 szafek.
900 indywidualistów na linii A
Zakład w Wels jest wyposażony w system regałowy, który zaopatruje produkcję w około 50 rodzajów płyt powlekanych o dwóch grubościach. „Do produkcji korpusów stosujemy obecnie około 25 dekorów, z których każdy jest dostępny w wersji jedno- i dwustronnej” — kreśli szczegółowy obraz Sterrer. Elementy lakierowane i fornirowane są wytwarzane we Freistadt, skąd następnie przybywają do Wels. Tutaj pracujemy zasadniczo z płytami półformatowymi na dwóch liniach obróbki korpusów, z których główna linia A obejmuje obróbkę wszystkich szafek górnych, dolnych i wysokich. Każdego dnia jest to około 900 sztuk. Obróbka rozpoczyna się od dwóch pił 1-osiowych, które dziennie tną 5500 elementówObróbka rozpoczyna się od dwóch pilarek 1-osiowych, które dziennie tną 5500 elementów. Każdy element otrzymuje tutaj etykietę, która początkowo zawiera tylko dane dotyczące rodzaju płyty i jej wymiarów. W toku dalszej obróbki z płyt tych powstają najróżniejsze komponenty. Najpierw jednak element przechodzi przez tymczasowy bufor na odcinku obrzeży, gdzie cztery urządzenia są połączone szeregowo w taki sposób, że element może przez nie przejść bez zmiany swojego położenia. „Po oklejeniu obrzeży element jest już przypisany do konkretnego zlecenia” — podkreśla Sterrer. Linia kończy się dwoma wylotami, gdzie elementy są sortowane, a następnie umieszczane w kontenerach, w których dostają się na stację kompletowania.
Podczas ręcznego kompletowania wszystkie elementy zarówno z Wels, jak i z Freistadt są układane w dokładnej kolejności wymaganej do produkcji. Teraz przychodzi czas na indywidualny montaż końcowy, który ewe zawsze wykonuje jak najpóźniej. Maksymalna wielkość partii w obszarze korpusów wynosi zatem jeden dzień. „Rozważamy nawet jej dodatkowe zmniejszenie, ponieważ uprościłoby to proces kompletowania i zmniejszyłoby nakłady związane z rozwiązaniami logicznymi i wymaganym know-how”. W końcu indywidualizacja części jest realizowana w wysoce zautomatyzowanej maszynie przelotowej, gdzie następuje wiercenie i kołkowanie elementów, mocowanie okuć oraz montaż korpusów.
Do tego 100 sztuk niestandardowych
Na drugiej linii obróbki korpusów — linii specjalnej C — z której codziennie schodzi około 100 szafek, obrabiane są części niestandardowe: o wyjątkowo małych lub dużych wymiarach, a także o bardzo głębokiej strukturze lub ze szczególnymi dekorami i powłokami o wysokim połysku. W tym miejscu obrabiane i montowane są również wszystkie szafki, które nie mają kształtu prostopadłościanu, na przykład szafy narożne, oraz szafki wymagające dużego nakładu pracy podczas montażu, którego nie można wykonać w ramach produkcji taktowej. Aby móc produkować dziennie 1000 części, linia ta również jest wyposażona w pilarkę 1-osiową, po niej jednak następuje oklejanie obrzeży z transportem powrotnym.
Szafki na obu liniach nie mają ustalonej kolejności, przy czym zlecenia są produkowane jedno po drugim. Na końcu obu linii szafki są kierowane do pakowania.
Pakowanie indywidualnych zamówień
W zakresie dystrybucji mebli kuchennych firma ewe współpracuje głównie z niezależnymi sprzedawcami, którzy otrzymują szafki w formie korpusów. Już od 2009 roku, kiedy to w zakładzie ewe uruchomiono pierwszą maszynę do pakowania, producent kuchni samodzielnie wykrawa opakowania dokładnie dopasowane do danej szafki. „Różnorodność naszych produktów oczywiście wiąże się z dużym zapotrzebowaniem na różne kroje kartonów” — twierdzi Sterrer. „Do samych witryn używamy opakowań składających się z trzech lub czterech elementów”. W ciągu ostatnich dwunastu, trzynastu lat ewe zdobyło dzięki temu znaczne doświadczenie w zakresie pakowania partii na zamówienie. „Sami opracowaliśmy wszystkie wzory i rozwiązania i do dziś korzystamy wyłącznie z nich. Chcemy też nadal używać oprogramowania, które kupiliśmy w tym celu w 2009 roku”.
Wszystkie dane potrzebne do przygotowywania indywidualnych opakowań pochodzą z systemu ERP. Firma ewe stworzyła własny interfejs, przez który do urządzenia przesyłane są wszystkie istotne informacje: nie tylko szerokość, wysokość i głębokość korpusu, lecz także np. grubość materiału frontu. W zależności od tego, czy wynosi ona 18 czy 22 mm, powstają różne projekty opakowań. „Udostępniany jest niewielki zestaw danych historycznych. Mając do dyspozycji bufor w postaci danych około sześciu korpusów, bezpośrednio przed pakowaniem skanujemy kod kreskowy szafki. W systemie ERP powstaje lista zmiennych, która w połączeniu z odpowiednim wzorem opakowania generuje jego wykrój”.
W miarę możliwości zachować strukturę danych
Obecnie w obu zakładach pracują cztery urządzenia pakujące, a firma dysponuje już bogatym know-how w zakresie indywidualnego pakowania partii na zamówienie. Dlaczego więc ten producent kuchni postanowił w ramach inwestycji zastąpić dotychczasowe urządzenie maszyną PAQTEQ C-250 marki HOMAG? Powodów było kilka. „Podobało nam się na przykład to, że będziemy mogli drukować na kartonach. Do niektórych szafek produkujemy więcej niż jeden projekt opakowania. Pracownicy mogą się przy tym pogubić i nie mieć pewności, który wzór należy do której szafki” — tłumaczy Sterrer. „Dzisiaj po prostu drukujemy na kartonie pięciocyfrowy numer elementu i przypisujemy w ten sposób opakowanie do odpowiedniej szafki. Źródło błędu zostało wyeliminowane”.
Kolejnym powodem była liczba narzędzi. Podczas gdy poprzednie urządzenie pracowało z sześcioma narzędziami wzdłużnymi, PAQTEQ dysponuje ośmioma. „Takie zwiększenie produkcyjności opłaci się w momentach, gdy będziemy musieli tymczasowo zwiększyć przerób” — mówi kierownik ds. inżynierii. „W takich wypadkach po prostu przydzielimy do maszyny kolejnego pracownika”. Szczególnie ważne było dla firmy ewe także to, aby przeniesienie danych z systemu ERP odbyło się w sposób sprawny i elastyczny. Dotychczasowa struktura danych w czterech maszynach pakujących miała zostać poddana jak najmniejszym zmianom. „Aby dane można było bezpiecznie przenieść do PAQTEQ, razem z firmą HOMAG wprowadziliśmy pewne modyfikacje do ogólnej struktury” — mówi Sterrer. I to jego zdaniem przebiegło bezproblemowo, podobnie jak dobrze przygotowane pod każdym względem uruchomienie maszyny PAQTEQ: „Zadziałało znakomicie”.
40 sekund
Maszynę zainstalowano na początku roku i jest ona obecnie bezpośrednio włączona w linię. Całe otoczenie, w szczególności technologia transportu szafek i kartonów, mogło pozostać niezmienione. Maszyna PAQTEQ jest wyposażona w sześć stanowisk wykroju. Dzięki temu firma ewe, która używała dotychczas trzech szerokości kartonu, może teraz każdą z tych szerokości wykrawać na dwóch stanowiskach. „Obecnie połowa stanowisk jest redundantna, więc możemy zmieniać wstęgi kartonów podczas przerwy lub między taktami na taśmie montażowej”. W ciągu dwóch zmian można by pakować od 900 do 1000 szafek. „Mówimy o cyklu 40-sekundowym. Do każdej szafki, która schodzi z linii montażowej, w ciągu tych 40 sekund wycinamy karton i wykonujemy obsługę”. Operator musi jedynie uruchomić maszynę i ewentualnie uzupełnić wstęgę kartonową. Wszystkie inne zadania przejmuje PAQTEQ — również pobieranie danych odbywa się automatycznie w tle. Zapakowane szafki są następnie przewożone wózkiem do wysyłki, aby następnego dnia trafić ciężarówką do sprzedawcy.
Dobre efekty
To, że PAQTEQ umożliwia produkcję większej liczby opakowań w Wels, potwierdzono już przy wstępnym odbiorze, kiedy zaobserwowano 7-procentowy wzrost przepustowości. To efekt, który jest firmie ewe bardzo na rękę. Choćby dlatego, że może się przełożyć na większy udział w rynku…