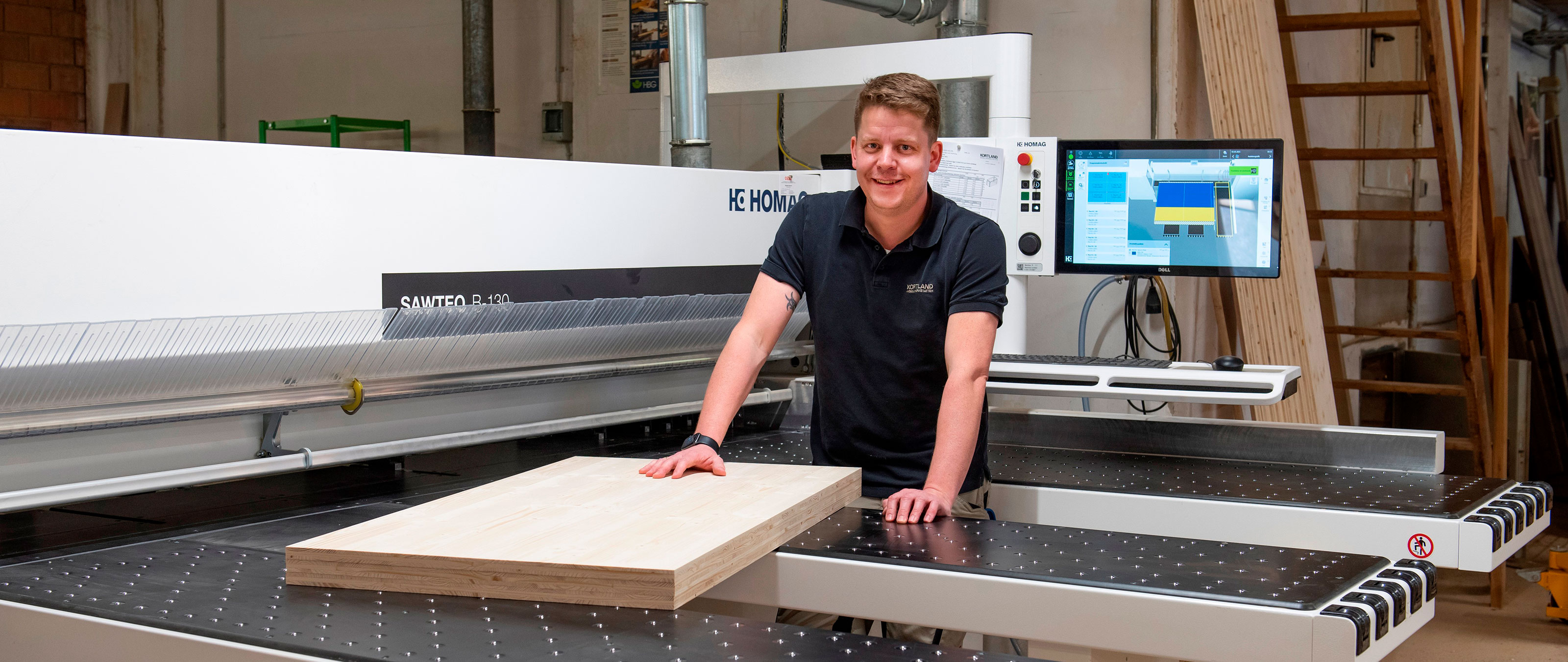
HOMAG の一番小さいパネルソーは、ぴったりでした。ドイツのニーダーザクセン州エッガーミューレンにあるコートラント・ファニチャーワークショップ。そのオーナーであるペーター・コートラントは、最初の決算時にとても驚いたと言います。「導入から 2 か月半しか経っていないのに、この新しい SAWTEQ B-130 で原板 3,000 枚から約 20,000 個の部材を切り出すことができました。全部で 15,000 のシングルカット、つまり切断長さの合計は 15 km にも及びます!」
社内のパネル切断が、主に棚部材の生産などの小さな製品セグメントに使用されるようになったことを考えるとさらに驚きです。これは年間売上の約 15 ~ 20 % を占めます。コートラントは個人向けの住宅設備や家具も作っており、個人取引も同じくらいの割合で推移しています。そして売上の 60 % 以上を占めるのは無垢材家具、特にテーブルプレートとベッドフレームの生産です。これらを、国内の大きな代理店との契約で生産し、その製品をさらに世界で販売しています。
一貫性: 最新の技術を使った成長路線
いつもこんなに順調だったわけではありません。2004 年にペーター・コートラントがおじからこの会社を引き継いだとき、彼はメッレの職業訓練所で木材加工のエンジニア課程を終えたばかりでした。当時の製品ラインナップは、素朴なオーク製無垢材家具だけでした。発展性のない市場セグメントで、会社は破産に追い込まれました。
そこでコートラントはベテラン職人とともに、会社を新しく作り直したのです。その結果、今日では従業員 25 人を抱える会社になり、ゆっくりと成長し続けています。「コロナで大変だった 2020 年でさえ、売上は 5 % も増えました」と、コートラントは言います。この 39 歳の社長のコンセプトはこうです。「当社製品の品質と価格が一致しなければなりません。これは最新の技術、つまり HOMAG でのみ実現します」
定期的: 2 年ごとに新しい HOMAG
最初の HOMAG 機は、オーナーのおじが 1999 年に購入したものです。ルーター加工機 BOF 31/40 で、まだ稼動していて、今でも十分に活躍しています。2014 年には 5 枚のルーターが付いた BMG 311 Venture を追加し、2016 年には HOMAG Group の縁貼機、その 2 年後には小型の CNC 加工センター BHX 55 を導入しました。一番新しいものは、2020 年 12 月に導入した SAWTEQ B-130 です。
HOMAG の一番小さいパネルソーは、エッガーミューレンのメインマシンになっています。「当社は無垢材家具の製造から始まり、今でもそれが売りです」と、コートラント。「パネルソーはその過程では必要なく、ある意味別分野の機械です。しかし、棚の部材の製造が増えたことにより、板材加工も増え続けています。
2021 年 1 月だけで 3,000 m2 以上: 主にブナやシラカバの合板。さらに、針葉樹材や硬質繊維の木板。「以前は、すべての材料をテーブルソーを使って 2 人で切っていました。今では、SAWTEQ B-130 を使って同じ作業を 1 人で、さらに短い時間でできます!」効率だけでなく、この HOMAG エントリーモデルの比較的低価格で省スペースなところが、彼にとって最終的な購入動機になりました。
「2019 年から市場に出回っている製品をチェックし、さまざまなメーカーに問い合わせました。しかし、どのメーカーも SAWTEQ B-130 よりも当社に最適な鋸を提案できませんでした」と、コートラント。さらに「おすすめされた競合他社のエントリーモデルは、当社の目的には大きすぎ、高すぎでした。もしかしたら、ノーブランドメーカーにもっと最適な製品があったかもしれませんが、私にとっては論外です。それで最終的に HOMAG に決めました」
効果大: 従業員の身体的な負担軽減
従業員たちも、新しいマシンに驚いています。「以前は、パネルソーの作業をなんとか説き伏せてやってもらっていました。けれども、今はまったく状況が変わり、新しい HOMAG 鋸での作業を喜んでやってくれます」と、コートラント。主な要因は、大幅に改善された人間工学的な設計です。前は、2 人の従業員が手動でブナ合板の原板を動かし、テーブルソーに乗せなければなりませんでした。寸法 250 x 150 cm、厚さ 15 mm のパネルフォーマットは正直重労働です。
今では、鋸の前にバキュームリフターがあります。これを使って、パネルを 1 枚ずつスタックから簡単に持ち上げることができ、それから鋸をセットし、切断を開始すれば、もう完了です。「身体的な負担軽減がとても大きい」と、コートラントは強調します。「私は、これが SAWTEQ B-130 の最大のメリットだと思います」。部材のデスタッキングも同様にバキュームリフターで快適で、基本的に特別な操作は要求されません。どのみち、棚部材でそのようなことは必要ありませんが。
可能性大: コスト削減
「棚部材では最大 20 週の準備期間を設け、切断ジョブを最適にまとめます」と、コートラントは説明します。これによって、シンプルな切断図面が作成できます。通常、原板は 2 つの部材に加工されます。そのため、鋸にラベルプリンタを装備することをあきらめました。「当社は SAWTEQ B-130 を棚加工用に構成しました。そこで部材のラベリングはあまり必要でないのです」と、コートラントは言います。そして、「今なら、この新しい鋸を個人注文製造にも使用していきたいので、違う決断をするかもしれません。板材からキャビネットを作る場合など。この場合はジョブごとに 50 種類以上の部材が必要になるため、おそらく部材のマーキングがあると便利でしょう」と付け加えます。
さらに、HOMAG のソリューションはこのような複雑なジョブでも能力を発揮します。最適化というキーワード: ソフトウェアがジョブごとに最適な切断図面を算出し、時間と材料を節約します。以前、複雑なジョブでは前もって 20 % の切りくずが考慮されていました。「前は今よりも多くの材料を丸鋸に準備し、従業員に、必要な部材を切り出してと言っていました」と、コートラントは振り返ります。「そうすると、パズルが完成するまでに計算も対策もどこかへ行ってしまうのです。今は、完成した切断図面を HOMAG 鋸に送信すれば、操作担当者が開始ボタンを押すだけで、SAWTEQ が始動します。本当にすごいです!」
要約: いつでも、何回でも!
コートラント・ファニチャーワークショップの板材製品は、小さな市場です。しかし、SAWTEQ B-130 を使えば、いつでも、このセグメントで成長し、新しい顧客を獲得するチャンスがあります。HOMAG を導入するごとに製品のバリエーションが広がっています。これまでの経験を含め、今日もう一度導入を検討するとしたら、また SAWTEQ B-130 を選ぶでしょうか?コートラントは、この質問に迷わず「いつでも、何度でも!」と答えるでしょう。
「この市場で SAWTEQ B-130 の代わりはないと思います。おすすめされた競合他社のエントリーモデルは、当社の目的には大きすぎ、また高すぎました」Peter Kortland