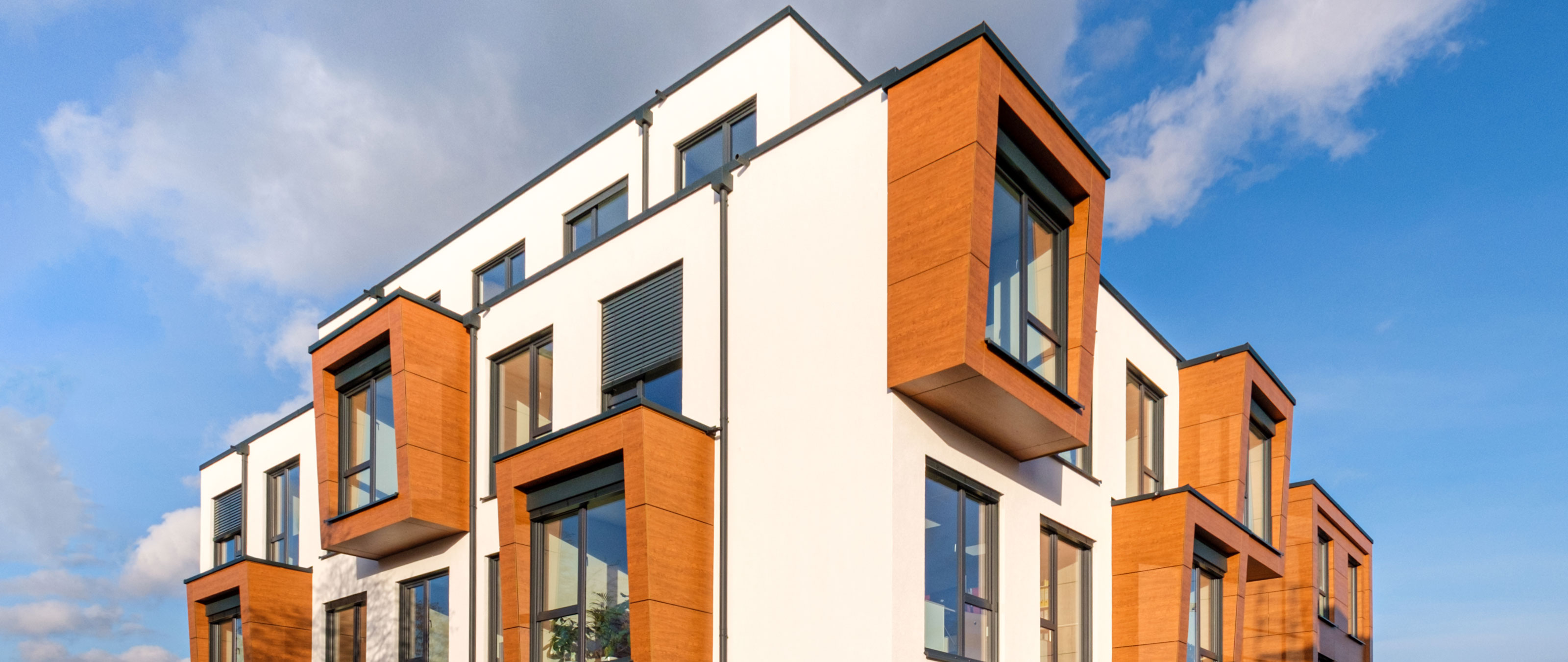
Stefan Höötmann niechętnie odrywa się od pracy. Gdy zdecydował się zautomatyzować produkcję elementów w swojej firmie SH Holz & Modulbau GmbH, nie przystał na żadne opóźnienia w dostawach, jakie mogłyby z tego wynikać: „Stoły montażowe WEINMANN mieliśmy już od samego początku, a na nasz most wielofunkcyjny WALLTEQ M-380 możemy trochę poczekać, bo do tej pory i tak prowadziliśmy produkcję ręczną”. Jednak maszyny ciesielskiej firma potrzebowała natychmiast: „Byłem zdania, że nawet jeżeli nie dostanę Mercedesa, to Volkswagenem też dojadę do celu. Dlatego oglądałem we Włoszech używaną maszynę ciesielską i już byłem gotów ją kupić”. Ostatecznie rzeczywistość niewiele odbiegła od jego założeń, ponieważ firma Weinmann złożyła Stefanowi Höötmannowi ofertę nie do odrzucenia: „Wynajęto mi inną maszynę ciesielską — dla mnie było to świetne rozwiązanie, które udało się również optymalnie wdrożyć. Bo gdy moja maszyna BEAMTEQ B-660 już do mnie dotrze, wynajmowane urządzenie zostanie odebrane i sprzedane. To właśnie uwielbiam: poszukiwanie rozwiązań zamiast wyszukiwania problemów. A to rozwiązanie pasowało doskonale”.
Trudne początki outsidera
Tak napisał się kolejny rozdział w historii przedsiębiorstwa, w którym Stefan Höötmann wykazał się takim samym dynamizmem jak w przypadku zakupu maszyn. Przedsiębiorstwo, założone w 1998 roku w niemieckim Lingen nad rzeką Ems jako klasyczny zakład ciesielski, w 2004 roku wkroczyło na rynek budownictwa szkieletowego: „Tego właśnie chcieliśmy, dzięki temu mogliśmy pewniejszą ręką zarządzać swoimi zleceniami”. Co prawda wtedy jeszcze firma była postrzegana na regionalnym rynku budownictwa drewnianego jako totalny outsider. Pokazała jednak odbiorcom, „jak ogromne możliwości daje drewno”. Działając w zgodzie z tym mottem, zdobyła doskonałą reputację — początkowo wśród inwestorów prywatnych. Ponadto dzięki bliskiej odległości od Holandii przedsiębiorstwo zajęło się również budownictwem modułowym dla holenderskich zleceniodawców — ten rodzaj konstrukcji budynków był już wtedy bardzo rozwinięty poza granicami Niemiec. „To sprawiło nam jeszcze więcej radości” — wspomina dziś Stefan Höötmann. „Tutaj mieliśmy do czynienia z jeszcze wyższym stopniem prefabrykacji i byliśmy jeszcze bardziej niezależni od zewnętrznych fachowców, na przykład od harmonogramu prac monterów okien czy płytkarzy. W ten sposób udało nam się posuwać prace do przodu w jeszcze szybszym tempie”. Dość powiedzieć, że to oni wprowadzili do północnych Niemiec konstrukcje modułowe, które były tam jeszcze zupełną nowością: „Jako firma zajmująca się budownictwem drewnianym i modułowym byliśmy wtedy w regionie wyśmiewani” — co być może miało również związek ze słabą jakością holenderskich budynków modułowych. Również w samej firmie zwrócono na to uwagę, dlatego później przystosowano wykorzystywane moduły do wyższych niemieckich wymogów jakościowych.
Od 2015 roku oficjalnie w budownictwie modułowym
W 2008 roku wraz z projektem BP nadszedł przełom: „Klient chciał stworzyć na cztery lata tymczasowy budynek biurowy dla 120 pracowników. Otrzymaliśmy zlecenie i zbudowaliśmy trzypiętrowy budynek modułowy o powierzchni użytkowej 3500 m2, którego jakość była tak wysoka, że BP korzysta z niego do dziś. Firmie z Lingen realizacja takiego projektu dawała również wgląd w to, „ile czasu i pieniędzy możemy zaoszczędzić podczas dużego projektu. To szaleństwo!”. Stefan Höötmann postanowił zatem dalej rozwijać swoje przedsiębiorstwo w kierunku budowy większych obiektów. Wprawdzie w wyniku kryzysu finansowego musiał początkowo zadowolić się mniejszymi zleceniami, ale czas ten konsekwentnie wykorzystywał do optymalizacji własnego systemu modułów. W 2015 roku rozpoczęto seryjną budowę modułowych domów dla uchodźców, w 2016 roku zawiązano partnerstwo z firmą Vonovia, która zleciła przedsiębiorstwu z Lingen wykonanie modułowych budynków mieszkalnych. „Był to początek szybkiego wzrostu” — podsumowuje Stefan Höötmann. „Wynajęliśmy hale do produkcji modułów — która wymaga szczególnie dużo miejsca — i obecnie w czterech zakładach dysponujemy powierzchnią łącznie 13 000 m2”. Partnerstwo z firmą Vonovia zakończyło się, za to rozpoczęły się ramowe z dużymi miastami — Kolonią i Hamburgiem — którym przedsiębiorstwo regularnie dostarcza budynki mieszkalne po stałej cenie. Poza tym SH Holz & Modulbau GmbH stawia dziś budynki biurowe, szkoły, przedszkola, domy opieki, a w przyszłości prawdopodobnie także hotele. W 2021 roku przedsiębiorstwo postawiło dla siebie nowy, reprezentacyjny modułowy budynek biurowy. Obecnie w Lingen trwa reorganizacja procesów produkcyjnych w halach. Ze współpracą z prywatnymi inwestorami budowlanymi Stefan Höötmann całkowicie się pożegnał. Obecnie przyjmuje jedynie zlecenia o powierzchni użytkowej od 700 m2.
Mały zespół, wielki efekt
W tej decyzji przedsiębiorcy przyświecała przede wszystkim dbałość o rentowność: „Wysiłek związany z budową domu jednorodzinnego jest niewiele mniejszy niż w przypadku dużych budynków — oba należy na przykład wykończyć. Obrót jest jednak znacznie większy w przypadku budowy dużych obiektów. Aby osiągnąć taki sam zysk z domów jednorodzinnych, nie wystarcza mi pracowników”. Przyczyną nie jest ogólny brak wykwalifikowanych robotników na rynku pracy, lecz firmowa filozofia Stefana Höötmanna, która opiera się na działaniu w małym zespole: „Obecnie mamy 35 pracowników, z czego około połowę w biurze, a drugą połowię na hali”. Realizacja nawet dużych projektów przy pomocy tak niewielkiego zespołu udaje się Stefanowi Höötmannowi dzięki współpracy z podwykonawcami: „Nasi pracownicy zajmują się tylko produkcją elementów i montażem modułów. Jeśli nasze zdolności produkcyjne nie wystarczają, to kupujemy również gotowe elementy. Wykończeniówkę zlecamy naszym zaufanym partnerom. Dzięki temu możemy szybko i elastycznie dostosowywać nasze możliwości, a w razie potrzeby przekazać duże zamówienia podwykonawcom, co nie stanowi dla nich problemu ze względu na półroczny termin realizacji”. Tym bardziej że dla fachowców stawianie konstrukcji modułowych wiąże się z kilkoma dodatkowymi zaletami. Pracują oni — w razie potrzeby także w systemie zmianowym — w kontrolowanych i ergonomicznych warunkach, w stałym miejscu osłoniętym przed warunkami zewnętrznymi i z krótkim dojazdami. Materiał mogą wygodnie przewieźć na stanowisko pracy, zamiast rozkładać go piętrowo na placu budowy. To korzyści, które są na rękę również pracownikom SH Modulbau: „Dziś nikt już nie ma ochoty na pracę na budowie. U nas praca na zewnątrz jest zredukowana do 14 dni i odbywa się odbywa się 2–3 razy w roku, a wtedy wszyscy się cieszą, że mają okazję popracować na powietrzu. Dlatego nigdy nie mieliśmy problemów ze znalezieniem nowych ludzi. Jeśli występują u nas wąskie gardła, to nie są to pracownicy, ale zdolności produkcyjne na hali”.
Planowanie zależne od znajomości systemu
Również podczas planowania Stefan Höötmann chętnie współpracuje z dostawcami zewnętrznymi. W biurze firmy SH Holz & Modulbau GmbH pracownicy zajmują się tylko przygotowaniem pracy i planami. Ważne jest, aby firma mogła wejść do projektu na jak najwcześniejszym etapie: „Jest to bezwzględnie konieczne w przypadku produkcji modułów. Dzięki temu można zbudować eleganckie i wysokojakościowe budynki — również indywidualnie dostosowane do potrzeb klienta. Niemniej jednak planowanie wymaga pewnego stopnia zaznajomienia z systemem. Jak bardzo jest to ważne, przekonaliśmy się podczas budowy domu opieki, który został zmodyfikowany przez architekta do takiego stopnia, że przestał to już być budynek modułowy i musieliśmy odrzucić zlecenie”. Dzięki zastosowaniu własnego systemu modułowego można budować bardzo elastycznie budynki do pięciu kondygnacji. Moduły mają zmienne rozmiary, maksymalnie mogą mierzyć 13,50 × 4,70 m, przy czym preferowana szerokość wynosi 3,40 m. „To są ramy, w których się poruszamy. Obecnie budujemy na przykład szkołę z dużymi, otwartymi modułami ramowymi i rozpiętością stropu 8,00 m. To, czego nie da się wyprodukować w systemie modułowym, wykonujemy ze stali i betonu. Z modułów nigdy nie zbudowalibyśmy na przykład auli. Zatem ograniczenia naszych zleceń są niewielkie, jednak istnieją pewne limity elastyczności”. W związku z tym planowanie jest zazwyczaj zlecane trzem biurom, z którymi firma z Lingen współpracuje już od dłuższego czasu. Jest to procedura, która początkowo została przyjęta niechętnie, ale wraz z rosnącą popularnością firmy zadomowiła się na dobre. „Dziś nasi klienci z łatwością tworzą plany we współpracy z naszymi biurami planowania — mimo że wiedzą, że kalkulacja kosztów odbywa się dopiero na końcowym etapie planowania modułów i że tak opracowanych planów nie będą mogli zrealizować w żadnej innej, konwencjonalnej firmie”.
Budynki modułowe jako rozwiązanie problemów
Skąd taki kredyt zaufania? „Ponieważ czujemy ducha czasu i słyszymy naokoło, że takie konstrukcje doskonale funkcjonują i poza innymi korzyściami dają naszym klientom również większe bezpieczeństwo. To jest jak samochodem: producent go planuje i produkuje, a jeśli robi to rozsądnie, to klient wie dokładnie, co otrzymuje, kiedy i w jakiej cenie”. To oczywiście nie wszystko. Klienci cenią w firmie z Lingen również to, że potrafi rozwiązywać problemy. Na przykład gdy w dużym mieście trzeba rozbudować obiekt w bardzo krótkim czasie i przy minimalnym wpływie na otoczenie. Budowa modułowa oznacza tutaj dwa tygodnie sporych prac budowlanych, po upływie których na miejsce muszą dojeżdżać jedynie niewielkie pojazdy. W związku z tym można być nieco droższym, zwłaszcza że jeśli stracone nerwy przeliczy się na pieniądze, to klient często ostatecznie oszczędza. Jako przykład Stefan Höötmann podaje projekt nadbudowy nowych kondygnacji pewnej kliniki: „Tam wybrano dostawcę konstrukcji masywnych, ponieważ jego oferta była o 20% tańsza od naszej. W rezultacie działalność obiektu musiała zostać na kilka miesięcy zawieszona z powodu hałasu, zanieczyszczeń i wilgoci, choć wynagrodzenia dla personelu kliniki nadal były wypłacane. My skończylibyśmy prace praktycznie w dwa tygodnie. Teraz z perspektywy czasu można podsumować, który wariant był ostatecznie korzystniejszy”. Drugim przykładem na to, jaką korzyścią okazuje się bezproblemowy przebieg prac, jest zamknięty 250-metrowy łącznik między dwoma budynkami kliniki. Opiera się on na podporach i znajduje się na terenie kliniki, gdzie występuje duże natężenie ruchu pojazdów i pieszych. Firma SH Holz & Modulbau złożyła ofertę projektu wykorzystującego 20 modułów z 19 podporami. Po przygotowaniu fundamentów pod podpory, które wymagałyby wydzielenia niewielkiego placu budowy, cały montaż odbyłby się w ciągu 20 dni — jedna podpora i jeden moduł dziennie. „Jeden z konkurujących dostawców konstrukcji masywnych zaproponował 80 podpór i pół roku prac” — wspomina Stefan Höötmann. „Chociaż był o połowę tańszy, z łatwością wygraliśmy przetarg”. Kolejną zaletą konstrukcji modułowych jest mniejsze zaangażowanie inwestora. Podczas gdy choćby w przypadku tradycyjnych projektów mieszkaniowych kierownik budowy musi być regularnie obecny na miejscu, to w przypadku projektu modułowego uczestniczy on tylko w procesie planowania i odbiorze obiektu. Nie jest angażowany w produkcję i może zajmować się innymi projektami, co oznacza, że miasto lub spółdzielnia mieszkaniowa może zrealizować około czterech razy więcej projektów budynków modułowych.
Budownictwo przemysłowe
Podstawowym warunkiem, aby uzyskać wszystkie te korzyści, jest konsekwentne uprzemysłowienie działalności budowlanej. W takim przypadku budynek modułowy staje się produktem, wytwarzanym w kontrolowanych warunkach i dostarczanym na miejsce przeznaczenia w ramach kompletnej usługi. Czynności budowlane na miejscu ograniczają się do krótkiego montażu, a zależność od czynników zewnętrznych, takich jak warunki pogodowe czy kolidujące prace różnych fachowców, spada do zera. Centralnym punktem projektu budowlanego, poza planowaniem i przygotowaniem pracy, jest produkcja modułów na hali, która podobnie jak w przemyśle motoryzacyjnym powinna być w znacznym stopniu zautomatyzowana i zracjonalizowana. Budownictwo przemysłowe umożliwia również konsekwentne wykorzystanie efektu synergii między standaryzacją a seryjnością. O korzyściach przekonał się Stefan Höötmann podczas produkcji 13 jednakowych domów dla uchodźców: „Dzięki powtarzaniu tych samych czynności nasza praca była mniej podatna na błędy i udało się zaoszczędzić nawet 30% czasu. Zmierzyliśmy to, więc mamy pewność, że to dla nas właściwa droga. Dzięki zautomatyzowanej produkcji będziemy mogli w przyszłości jeszcze lepiej wykorzystać tę synergię”. Nawiązanie kontaktu z producentem maszyn WEINMANN, należącym do Grupy HOMAG i zajmującym się automatyzacją w branży budownictwa drewnianego, było z tego punktu widzenia kolejnym krokiem we właściwym kierunku. Dla Stefana Höötmanna był to element jego dążenia do tego, aby „wszystkie procesy związane z budową były oferowane przez jednego dostawcę i podlegały konsekwentnej optymalizacji. W zakresie produkcji oznacza to szybszy przepływ pracy dzięki zautomatyzowanej produkcji, a także większe liczby sztuk przy szybkiej reakcji na zwiększoną liczbę napływających zleceń. Nie można też zapomnieć o wyższej jakości — ręcznie popełnialiśmy wciąż zbyt wiele błędów”. W przyszłości firma chce wykorzystać jeszcze więcej możliwości racjonalizacji również na etapie montażu modułów: „Obecnie wciąż odkładamy wyprodukowane moduły w hali, tam je montujemy, demontujemy, pakujemy i transportujemy na miejsce budowy. Wyzbywamy się ich więc stąd dopiero wtedy, gdy wszystkie są już gotowe — w razie jakiegoś problemu cała hala jest zablokowana. Taki system funkcjonował przez długi czas, ale przy obecnej wielkości produkcji napotyka na ograniczenia. W związku z tym od 2023 roku przedsiębiorstwo wdroży system przesuwania modułów na hali. „Będą one kierowane do określonego fachowca, który będzie miał w hali swoją stałą stację. W ten sposób będziemy mogli każdego dnia wykonać jeden moduł i przechowywać go na zewnątrz”. Tak firma SH Holz & Modulbau GmbH odrabia swoje lekcje. W dziedzinie współpracy z podwykonawcami Stefan Höötmann widzi jednak jeszcze wiele do zrobienia: „Nawet podwykonawcy mogą zaoszczędzić pieniądze dzięki racjonalizacji pracy w naszej hali. Nie udało się jednak jeszcze wszystkich przekonać, że przynajmniej część tych oszczędności mogłaby zostać wykorzystana na poprawę struktury kosztów”. Ponadto elektrycy i instalatorzy mogliby samodzielnie wykonywać wiązki przewodów i montować je w hali. „W ten sposób można by wykorzystać dodatkowy potencjał w zakresie kosztów, ale niestety wielu fachowców jeszcze tego nie akceptuje. Jestem jednak przekonany, że jeżeli będziemy podejmować dalsze kroki we właściwym kierunku w zakresie rozbudowy modułów, a także intensywnie wykorzystywać rabaty ilościowe, to konwencjonalne konstrukcje masywne będą dla nas coraz mniej konkurencyjne”. Dowodem na to, że wizje przedsiębiorcy muszą być traktowane poważnie, jest sama historia powstania jego firmy. Przyczyniła się ona w znacznym stopniu do tego, że budownictwo modułowe jest na ustach wszystkich także w północnych Niemczech i od dawna nie jest już uważane za konstrukcje o niskiej jakości. Firma SH Holz & Modulbau GmbH ugruntowała swoją pozycję na rynku, na którym jest teraz jednym z niewielu dostawców koncentrującym się wyłącznie na budynkach modułowych. A potwierdzeniem jest fakt, że w regionie zaczęli się już także pojawiać jej pierwsi naśladowcy.
Artykuł z magazynu klienta performance 22 | 2023. Więcej informacji znajdziecie tutaj!
„W zakresie produkcji oznacza to szybszy przepływ pracy dzięki zautomatyzowanej produkcji, a także większe liczby sztuk przy szybkiej reakcji na zwiększoną liczbę napływających zleceń. Nie można też zapomnieć o wyższej jakości — ręcznie popełnialiśmy wciąż zbyt wiele błędów.”Stefan Höötmann