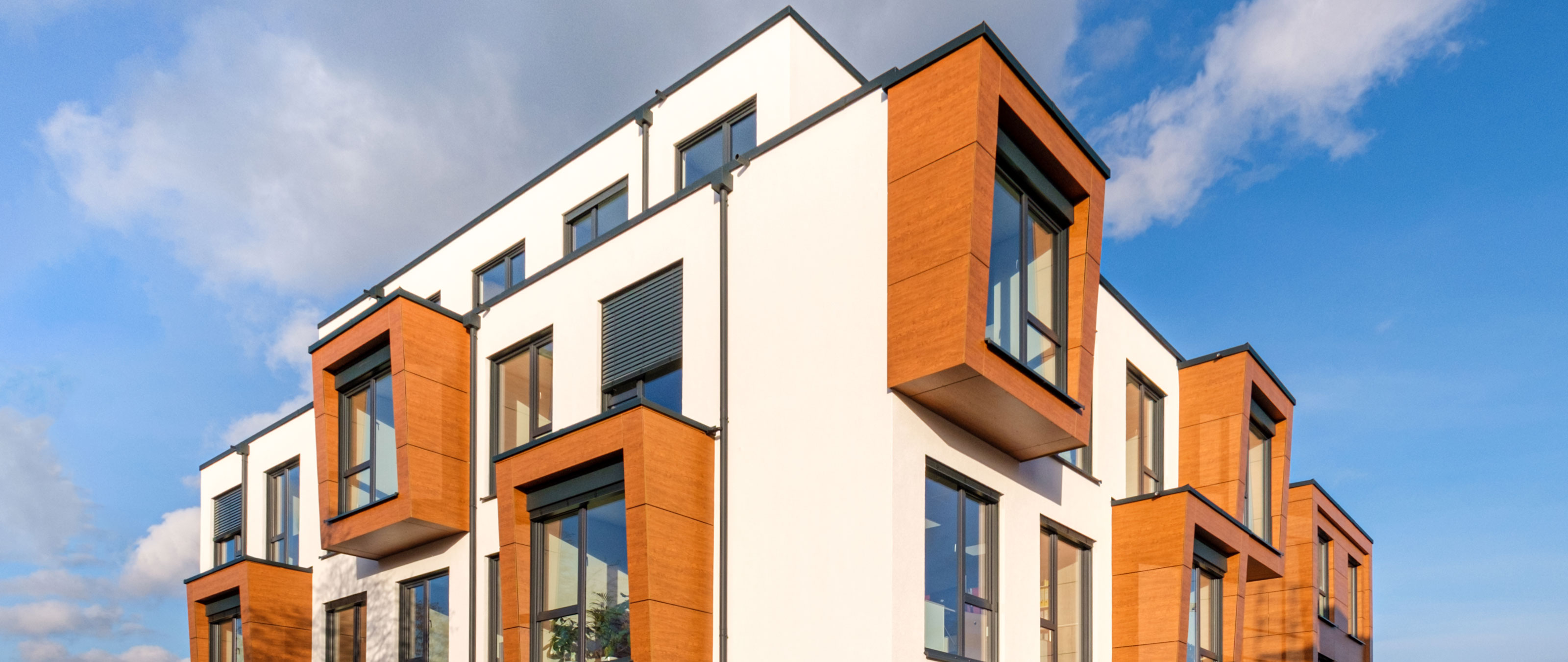
Stefan Höötmann n'aime pas qu'on l'empêche de travailler. C'est pourquoi, lorsqu'il a décidé d'automatiser la fabrication des éléments dans sa société SH Holz & Modulbau GmbH, il n'a pas accepté de retards dus aux délais de livraison : « Nous avons obtenu les tables en kit WEINMANN tout de suite. Pour notre pont multifonctions (un WALLTEQ M-380), nous pouvons attendre un peu, car nous produisions déjà manuellement jusqu'à présent ». Mais l'entrepreneur tenait à avoir son installation de taille de charpentes tout de suite : « Je me suis dit : à défaut d'avoir une Mercedes, j'arriverai à destination avec une VW. C'est pourquoi j'avais déjà jeté un coup d'œil à une installation de taille de charpentes d'occasion en Italie et j'étais sur le point de l'acheter. Mais les choses en sont restées là, car Weinmann a fait une offre à Stefan Höötmann qu'il n'a pas pu refuser : « On m'a prêté une autre installation de taille de charpentes dans le hall. Cette solution, idéale pour moi, s'est déroulée de manière optimale : lorsque mon BEAMTEQ B-660 sera livré, la machine de prêt sera récupérée et revendue. Voilà ce que j'aime : lorsque l'on cherche des solutions au lieu de se contenter de ressasser les problèmes. Et cette solution convenait parfaitement ».
Une entreprise exotique de la construction bois moquée à ses débuts
Un nouveau chapitre était ainsi écrit dans l'histoire d'une entreprise au cours de laquelle Stefan Höötmann s'était montré aussi dynamique que pour l'achat de machines : fondée en 1998 en tant que charpenterie classique, son entreprise basée à Lingen sur l'Ems s'est lancée en 2004 dans la construction à ossature bois : « C'est ce que nous voulions. Ainsi, nous pouvions tenir nous-mêmes les rênes de nos commandes ». Certes, à l'époque, les constructeurs bois étaient encore considérés comme totalement exotiques dans la région, mais ils ont montré au public étonné « tout ce qu'il était possible de faire avec du bois ». C'est selon cette devise que l'entreprise s'est forgé une excellente réputation, d'abord auprès des maîtres d'ouvrage privés. De plus, la proximité des Pays-Bas a permis à l'entreprise de « glisser » dans la construction modulaire pour les clients néerlandais : ce type de construction était déjà bien développé de l'autre côté de la frontière. « Cela nous plaisait davantage », se souvient aujourd'hui Stefan Höötman : « Ici, nous avions un degré de préfabrication encore plus élevé, nous étions encore plus indépendants des artisans externes, notamment en ce qui concerne la date d'arrivée des constructeurs de fenêtres ou des carreleurs sur le chantier. Nous pouvions ainsi faire bouger les choses encore plus rapidement ». Une raison suffisante pour importer la construction modulaire, alors encore largement méconnue, dans le nord de l'Allemagne : « En tant que constructeur bois et de bâtiments modulaires, on se moquait de nous à l'époque dans la région », ce qui était peut-être aussi lié à la mauvaise qualité des bâtiments modulaires hollandais. Le constat avait également été fait à Lingen, raison pour laquelle on a par la suite adapté la construction modulaire aux exigences de qualité allemandes plus élevées.
Etabli depuis 2015 dans la construction modulaire
En 2008, la percée s'est faite avec un immeuble commercial pour BP : « L'entreprise désirait un immeuble de bureaux temporaire pour 120 employés pendant quatre ans. Nous avons obtenu la commande et avons livré un bâtiment modulaire de trois étages et de 3 500 m2 de surface utile, dont la qualité était telle que BP l'utilise encore aujourd'hui ». A Lingen, l'expérience de ce projet avait permis de constater « combien de temps et d'argent nous pouvions économiser dans un grand projet. De la folie ! » Stefan Höötmann a donc décidé de faire évoluer son entreprise vers la construction d'éléments. Certes, suite à la crise financière, il a d'abord fallu faire des économies, mais le temps a été mis à profit afin d'optimiser le système de construction modulaire de l'entreprise. En 2015, l'entreprise s'est ensuite lancée dans la construction modulaire en série de centres de réfugiés, puis en 2016 dans un partenariat avec Vonovia, qui souhaitait acquérir des bâtiments d'habitation modulaires provenant de Lingen. « C'était le coup d'envoi d'une croissance fulgurante », conclut Stefan Höötman avec le recul. Nous avons loué des halls pour la production modulaire, pour laquelle il faut avant tout disposer de beaucoup de place, et nous atteignons aujourd'hui une capacité de 13 000 m2 de halls sur quatre sites ». Le partenariat avec Vonovia a pris fin et a été remplacé par des contrats-cadres avec les grandes villes de Cologne et de Hambourg, auxquelles des logements sont régulièrement livrés à prix fixe. En outre, la société SH Holz & Modulbau GmbH construit aujourd'hui des immeubles de bureaux, des écoles, des crèches, des maisons de soins et, comme on l'espère, bientôt à nouveau des hôtels. En 2021, l'entreprise a emménagé dans son nouvel immeuble de bureaux représentatif, qu'elle a construit selon une méthode modulaire. En ce moment, les déroulements de production sont en train d'être réorganisés dans les halls de Lingen. Stefan Höötman s'est complètement retiré des affaires avec les maîtres d'ouvrage privés : il n'accepte aujourd'hui des commandes qu'à partir d'un projet de 700 m2 de surface utile.
Petite équipe, grand impact
L'entrepreneur a surtout en tête la rentabilité : « Le travail n'est pas beaucoup moins important pour une maison individuelle que pour un grand bâtiment ; les deux doivent par exemple être échantillonnés. Mais le chiffre d'affaires est bien plus important dans le cas d'une construction d'éléments. Pour réaliser le même bénéfice avec des maisons individuelles, je n'aurais donc pas suffisamment de personnel ». Non pas à cause de la pénurie générale de main-d'œuvre qualifiée, mais parce que la philosophie de l'entreprise de Stefan Höötmann est de réaliser beaucoup de choses avec une équipe réduite : « Actuellement, nous avons 35 employés, dont environ la moitié travaille au bureau et les autres dans le hall ». Stefan Höötmann parvient à maîtriser de gros volumes avec une équipe aussi réduite en faisant appel à des sous-traitants : « Avec nos collaborateurs, nous nous chargeons uniquement de la fabrication d'éléments et du montage modulaire. Si nos capacités ne suffisent pas, d'autres éléments sont achetés. Nous confions le montage à des partenaires éprouvés de l'artisanat. Ainsi, nous pouvons adapter nos capacités de manière rapide et flexible, et si nécessaire faire appel à des artisans supplémentaires pour les grosses commandes, ce qui ne pose aucun problème à leurs entreprises compte tenu d'un délai de six mois ». D'autant plus que la construction modulaire présente de nombreux avantages pour les artisans : ils travaillent (si nécessaire en équipe) dans des conditions contrôlées et ergonomiques sur un site fixe, à l'abri des intempéries et avec des temps de déplacement réduits. Ils peuvent facilement conduire leur matériel jusqu'à leur lieu de travail au lieu de le répartir sur plusieurs étages du chantier. Des avantages dont profitent également les collaborateurs de SH Modulbau : « Aujourd'hui, plus personne n'a envie de travailler sur un chantier. Chez nous, les interventions extérieures se réduisent à deux ou trois fois quinze jours par an, tout le monde prend donc plaisir à sortir de temps en temps. Nous n'avons donc jamais eu de problèmes pour trouver de nouvelles personnes. S'il y a un goulot d'étranglement chez nous, il ne s'agit pas du personnel, mais de la capacité du hall ».
Planification et affinité avec le système
Stefan Höötmann aime également collaborer avec des intervenants externes pour la planification : seules la préparation du travail et la planification des tâches sont réalisées dans le bureau bien rempli de la société SH Holz & Modulbau GmbH. Il est important que l'entreprise puisse intervenir le plus tôt possible dans le projet : « Pour la construction modulaire, cela est absolument nécessaire. Il est ainsi possible de construire des bâtiments chics et de grande qualité, voire de les personnaliser selon les souhaits du client. Mais il faut tout de même avoir une certaine affinité avec le système lors de la planification. Nous avons justement pu constater à quel point cela est important dans le cas d'une maison de soins, qui a été modifiée par un architecte au point qu'il ne s'agissait plus d'un bâtiment modulaire et que nous avons dû refuser la commande ». Et ce, malgré le fait qu'il soit possible de construire de manière très flexible jusqu'à cinq étages avec le système modulaire propre à l'entreprise. Les modules ont des dimensions variables allant jusqu'à 13,50 x 4,70 m, la mesure préférentielle étant de 3,40 m pour la largeur. « Dans ce cadre, nous sommes en mesure de jouer. Nous construisons par exemple actuellement une école avec de grands modules d'espaces ouverts et une portée de plafond de 8,00 m. Ce que nous ne pouvons pas faire avec des modules, nous le faisons aussi avec de l'acier et du béton. Nous ne construirions par exemple jamais un auditorium avec des modules. Nous avons donc peu de contraintes concernant nos commandes, mais il y a tout de même des limites à la flexibilité ». C'est pourquoi, à Lingen, la planification est généralement confiée à trois bureaux de planification avec lesquels l'entreprise coopère depuis longtemps. Une procédure qui, au début, n'a été acceptée qu'avec réticence, mais qui s'est établie au fur et à mesure que l'entreprise gagnait en notoriété. « Aujourd'hui, nos clients collaborent sans problème avec nos bureaux de planification, même s'ils savent que le calcul des prix n'intervient qu'à la fin de la planification modulaire et qu'à ce moment-là, ils ne peuvent pratiquement plus réaliser nos plans avec une entreprise conventionnelle ».
La construction modulaire comme solution aux problèmes
D'où vient cette confiance ? « Parce que nous sommes aujourd'hui dans l'air du temps, parce que nous savons que ce mode de construction fonctionne parfaitement et qu'il apporte aux clients, outre de nombreux avantages, une plus grande sécurité. C'est comme pour une voiture : elle est planifiée et produite par un fabricant, et si celui-ci s'y prend bien, le client sait exactement ce qu'il obtient, quand et à quel prix ». Ce n'est évidemment pas tout. Ce que les clients apprécient également chez le constructeur modulaire de Lingen, c'est qu'il propose des solutions à leurs problèmes. Par exemple, lorsqu'il s'agit de réaliser une surélévation dans une grande ville en un temps de construction extrêmement court et avec un impact minimal sur l'environnement. Une construction modulaire se traduit ici par deux semaines de grand chantier, après quoi seuls des petits véhicules circulent de temps à autre. On peut donc se permettre d'être un peu plus cher, d'autant plus que si l'on tient compte des éventuels problèmes, il n'est pas rare qu'en fin de compte le client économise de l'argent. Stefan Höötmann cite l'exemple d'une surélévation au-dessus d'une clinique : « Là, le choix s'est porté sur un constructeur en dur parce qu'il proposait un prix de 20 % inférieur au nôtre. Au final, l'activité de la clinique a dû être suspendue pendant plusieurs mois à cause du bruit, de la saleté et de l'humidité, mais les salaires du personnel de la clinique ont continué à être versés. Nous aurions pratiquement terminé ce travail en deux semaines. On peut faire le calcul pour savoir quelle variante était la plus avantageuse au final ». Deuxième exemple illustrant que l'entreprise apporte des solutions aux problèmes : un couloir fermé de 250 m de long qui relie deux bâtiments de clinique. Il traverse, sur des piliers, le site d'une clinique où circulent de nombreux véhicules et piétons. SH Holz & Modulbau a proposé pour ce projet 20 modules avec 19 piliers. Après que les fondations des piliers ont été préparées sur de petits chantiers, ils devaient être montés sur le terrain en 20 jours : un pilier et un module par jour. « Un constructeur de maisons en dur concurrent avait proposé 80 piliers et six mois de construction », se souvient Stefan Höötmann. « Bien qu'il ait été deux fois moins cher, nous avons remporté le contrat sans problème ». Un autre point positif de la construction modulaire est la ressource nécessaire du maître d'ouvrage. Alors que le responsable de chantier d'une ville, par exemple, doit être régulièrement présent sur le chantier dans le cadre de projets de construction de logements conventionnels, dans un projet modulaire, il n'intervient que dans le processus de planification et lors de la remise. Pendant la phase de production, il dispose de capacités libres et peut s'occuper d'autres projets, ce qui explique pourquoi une ville ou une société de logement peut réaliser environ quatre fois plus de projets avec le même effectif grâce à la construction modulaire.
La construction industrielle
La condition centrale de tous ces avantages est une industrialisation conséquente de l'activité de construction. Une fois cette étape franchie, un bâtiment modulaire devient un produit fabriqué dans des conditions contrôlées et livré à son lieu de destination sous forme de prestation complète. L'activité de construction sur place se réduit à une courte fenêtre de temps pour le montage, la dépendance aux influences extérieures telles que les conditions météorologiques ou les interactions négatives entre les différents corps de métier tombe à zéro. Outre la planification et la préparation du travail, la fabrication des modules dans le hall, qui doit être largement automatisée et rationalisée sur le modèle de l'industrie automobile, est au cœur du projet de construction. La construction industrielle permet ensuite d'utiliser de manière conséquente les effets de synergie de la standardisation et de la sérialité. Ce n'est pas pour rien que Stefan Höötmann a constaté, lors de la production de 13 centres de réfugiés de construction identique, « qu'en répétant toujours les mêmes déroulements, nous étions moins sujets aux erreurs et que nous avons enregistré des économies de temps de travail allant jusqu'à 30 pour cent. C'est ce que nous avons mesuré, c'est le chemin que nous devons prendre. Avec une production automatisée, nous pourrons exploiter ces effets de synergie de manière encore plus approfondie à l'avenir ». Sous cet aspect, la prise de contact avec le constructeur de machines WEINMANN, qui fait partie du groupe HOMAG et qui est synonyme d'automatisation dans la construction bois, a été un pas de plus dans la bonne direction. Pour Stefan Höötmann, cela fait partie de son ambition de « maîtriser lui-même tous les processus liés à la construction et de les optimiser de manière conséquente. Dans le domaine de la production, cela signifie un flux de travail plus rapide grâce à une fabrication automatisée, ainsi que des quantités plus élevées et une réaction rapide aux pics de commandes. Sans oublier une meilleure qualité car nous faisions encore trop d'erreurs manuellement ». Le charpentier veut également exploiter à l'avenir d'autres potentiels de rationalisation dans le montage des modules : « Actuellement, nous déposons les modules dans le hall, nous les montons, nous les démontons, nous les emballons et nous les transportons. Ainsi, nous ne sortons les modules que lorsqu'ils sont tous terminés ; si l'un d'entre eux pose problème, l'ensemble du hall est bloqué ». Un système qui a longtemps fonctionné, mais qui atteint ses limites avec les volumes actuels. C'est pourquoi, à partir de 2023, l'entreprise veut mettre en place un système coulissant qui permettra de déplacer les modules à travers le hall. « Ils arrivent ensuite chez l'artisan, qui a un poste fixe dans le hall. Nous pouvons ainsi réaliser un module par jour et le stocker à l'extérieur ». Ainsi, la société SH Holz & Modulbau GmbH a bien fait ses devoirs. Stefan Höötmann estime toutefois qu'il y a encore du retard à rattraper dans les activités extérieures : « Les sous-traitants ont en effet eux aussi réalisé des économies grâce au travail rationnel dans notre hall. Cependant, l'idée de pouvoir intégrer au moins une partie de ces économies dans une amélioration de la structure des coûts ne s'est pas encore imposée ici ». En outre, les électriciens et les installateurs pourraient préfabriquer des faisceaux de câbles ou de conduites et les installer dans le hall. « Ils pourraient ainsi exploiter des potentiels de coûts supplémentaires, mais malheureusement, de nombreux artisans manquent encore de compréhension à ce sujet. Néanmoins, je suis convaincu que si nous faisons de nouveaux pas dans la bonne direction en ce qui concerne le développement des modules et si, en outre, nous utilisons intensivement les possibilités de remises sur les grandes quantités, la construction en dur conventionnelle pourra de moins en moins rivaliser avec nous ». L'ascension de son entreprise prouve que les idées du charpentier sont à prendre au sérieux. Il a largement contribué à ce que la construction modulaire soit aujourd'hui aussi connue dans le nord de l'Allemagne et qu'elle ne soit plus considérée depuis longtemps comme un mode de construction de qualité inférieure. Il a assuré à la société SH Holz & Modulbau GmbH une position sur le marché qui lui permet d'être l'un des très rares fournisseurs à pouvoir se concentrer exclusivement sur la construction modulaire. Depuis que cette information s'est répandue, les premiers émules sont apparus dans la région.
Un article du magazine clients performance 22 | 2023. Pour plus d'informations, cliquez ici!
« Dans le domaine de la production, cela signifie un flux de travail plus rapide grâce à une fabrication automatisée, ainsi que des quantités plus élevées et une réaction rapide aux pics de commandes. Sans oublier une meilleure qualité car nous faisions encore trop d'erreurs manuellement. »