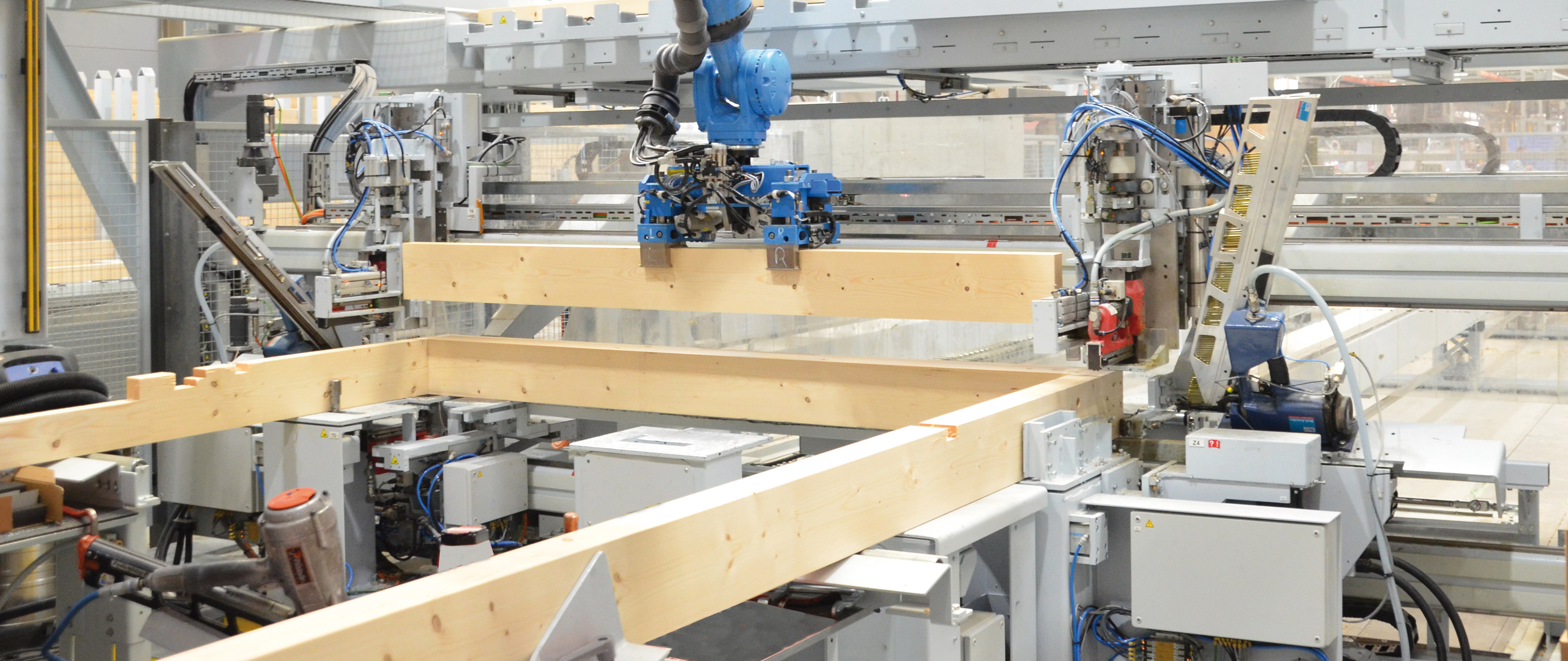
Construction de bâtiments préfabriqués : Bien-Zenker GmbH située à Schlüchtern dans la Hesse (Allemagne) est l'une des premières entreprises de construction bois à mettre en place un robot industriel dans leur ligne de production. Le robot intégré dans une station d'assemblage pour ossatures bois offre non seulement une flexibilité et une rapidité sans précédent, mais il rend également plus attrayants les postes de travail pour la construction de bâtiments préfabriqués.
Après l'automatisation de la taille de charpentes, la modernisation des outils de production entre dans sa deuxième phase dans de nombreuses entreprises de charpentes. Mais pendant qu'elles investissent dans la fabrication entièrement automatique d'éléments, la troisième phase s'annonce déjà pour la construction de bâtiments préfabriqués. Outre l'automatisation des systèmes de manutention et de logistique, cette troisième phase apporte aux entreprises de construction bois une innovation majeure dans les entrepôts de production : le robot industriel. Comme l'expérience nous a prouvé que la construction de bâtiments préfabriqués anticipe souvent de quelques années l'évolution du secteur des charpentes et comme les systèmes utilisés peuvent en fait intéresser les petites entreprises de construction bois, cette évolution mérite d'être examinée de plus près.
L'objectif visé : plus de précision et de capacité
Située à Schlüchtern dans la Hesse, l'entreprise Bien-Zenker GmbH est l'un des précurseurs de cette nouvelle technologie. Cette entreprise de charpentes et scierie fondée en 1906 à Birstein a évolué vers sa forme actuelle à la fin des années 90 suite à sa fusion avec Zenker Hausbau. Aujourd'hui, cette entreprise fait partie des leaders allemands de la construction de bâtiments préfabriqués.
Cette année, 780 maisons ont quitté l'usine de Schlüchtern, l'année prochaine, ce chiffre devrait clairement dépasser les 800. Ces maisons sont actuellement conçues, fabriquées et assemblées par plus de 500 employés. Le chiffre d'affaires de l'entreprise s'élève à environ 150 millions d'euros. Bien-Zenker connaissant une croissance depuis plusieurs années déjà, un processus de renouvellement des installations de production a été engagé en 2014/15. Selon le directeur technique M. René Honrath, l'objectif était d'une part d'anticiper la hausse du nombre de pièces à produire dans les années à venir, car l'ancienne ligne de production aurait alors atteint sa limite de capacité. D'autre part, " nous misons sur l'amélioration de la précision grâce à la production automatisée ". Le site de production à Schlüchtern était beaucoup plus " manuel " avant la modernisation. Ainsi, dans l'ancienne station d'assemblage pour ossatures bois, les montants étaient partiellement placés à la main, tout comme les fraisages et les perçages sur le cadre étaient en partie effectués manuellement. De temps à autre, un employé devait également réaligner les bois afin d'obtenir la précision requise.
Transport de matériaux entièrement automatique
Face à cette situation, les conditions de production actuelles se révèlent être un grand pas en avant : les montants, ainsi que les lisses inférieures et supérieures, sont stockés automatiquement dans un stockeur de ridelles par un portique de chargement WEINMANN, le STORETEQ H-700, et sont amenés vers le centre de taille en fonction des besoins. Le matériel est transporté en douceur grâce à des ventouses à vide, de sorte que le portique de chargement peut également déplacer le bois en qualité visible sans aucun problème. La taille de charpentes est prise en charge par un WEINMANN BEAMTEQ B-660, équipé d'une unité de sciage Flex-25 de 20 kW pour les usinages 5 axes (par exemple, pour les coupes angulaires, longitudinales et d'empannons). A cela s'ajoutent une unité de fraisage par en dessous 6,6 kW pour les fraises à queue, les fraises à queue d'aronde ou les forets et une unité à 4 axes de 18,5 kW avec changeur d'outils à douze cavités. Ainsi équipée, la machine offre d'excellentes performances de taille de charpentes, ainsi qu'une grande précision et une flexibilité accrue. Grâce à l'unité de fraisage par en dessous, aucun retournement n'est nécessaire pendant l'usinage. Chez Bien-Zenker, des unités de marquage et d'étiquetage sont fréquemment utilisées, ce qui permet aux employés travaillant sur des stations de travail ultérieures de connaître clairement l'affectation des composants aux éléments correspondants. Cela s'applique en particulier aux composants des lignes de pignons et de murs de jambette, qui sont retirés manuellement de la sortie du centre de taille. Les lisses inférieures et supérieures sont séparées après la taille et guidées automatiquement par des convoyeurs transversaux jusqu'à la station d'assemblage pour ossatures bois, où elles sont positionnées de manière entièrement automatique. Les montants spéciaux préparés sont transportés par un transporteur à chaîne horizontale dans ce qu'on appelle la tour des montants. Il s'agit d'un système de stockage hétérogène dans lequel chaque montant est stocké de manière contrôlée afin de pouvoir être récupéré immédiatement au moment du montage et mis à disposition automatiquement à un poste d'enlèvement de la station d'assemblage pour ossatures bois. Les montants standard se trouvent empilés dans un deuxième stockeur et sont automatiquement acheminés vers un " mini-centre de taille " qui se charge uniquement des perçages et des marquages. De là, ils ne sont pas transportés vers la tour des montants, mais vers un deuxième poste d'enlèvement sur la station d'assemblage pour ossatures bois via un deuxième système de manutention STORETEQ H-700.
Intérêt croissant pour les robots dans la construction bois
Les montants sont retirés des deux stations de retrait par un robot industriel à six axes, qui les place automatiquement dans l'ossature. Le robot Kuka a été fourni par HOMAG et intégré dans la cellule de production en collaboration avec WEINMANN. Il offre une vitesse et une précision supérieures à celles de technologies comparables pour la production d'ossatures. Il garantit également une grande disponibilité des machines et une excellente sécurité de production. Les attentes de Bien-Zenker concernant la nouvelle installation ont été pleinement satisfaites à cet égard. Le directeur de la production, M. Herbert Vestert, a ainsi déclaré : " Aujourd'hui, nous constatons à la fois une augmentation significative des performances et une nette amélioration de l'exactitude des dimensions des composants ". Avec l'utilisation d'un robot industriel dans la production d'ossatures en bois, WEINMANN reprend une avancée technologique qui a déjà révolutionné la construction automobile. Il y a de nombreuses raisons de penser que la construction bois connaîtra un développement similaire, même si nous ne sommes qu'au tout début.
On constate depuis un certain temps déjà que l'intérêt pour les robots dans la construction en bois ne cesse de croître.
Il y a plusieurs raisons à cela :
1. Les robots sont polyvalents. En réseau avec la commande de production globale de l'entreprise de maisons préfabriquées, le robot de Bien-Zenker s'adapte à toutes les nouvelles situations dans le processus de production. Cela signifie tout d'abord qu'il reçoit en temps réel des informations sur le montant qu'il doit retirer d'une station de prélèvement et placer à la position actuelle dans le cadre. Sa polyvalence permet également au robot d'insérer n'importe quel type de montant sous n'importe quel angle. C'est pourquoi des pignons et des murs de jambette ou des ouvertures de fenêtres et de portes peuvent également être fabriqués de manière entièrement automatique sur la station d'assemblage pour ossatures bois de Schlüchtern.
2. Les robots nécessitent peu d'entretien et ne connaissent pas la fatigue. Non seulement ils travaillent très vite, mais ils maintiennent cette vitesse sans compromis et sans pause pendant toute la journée de travail. Le travail physique est considérablement réduit, ce qui soulage les employés. Comme le poids du bois utilisé dans la production ne cesse d'augmenter, cet avantage est de plus en plus important. De plus, l'ergonomie optimisée valorise le poste de travail.
3. Les robots sont des produits fabriqués en série. Cela signifie, d'une part, que les entreprises de construction bois peuvent s'appuyer sur des systèmes sophistiqués et éprouvés et, d'autre part, que les investissements restent maîtrisés.
4. Ces nouveaux systèmes sont plus facilement acceptés, car le " collègue robot " peut soulager les employés, mais ne peut pas les remplacer. L'industrie automobile a montré que la main-d'œuvre humaine bien formée est indispensable à la production. Bien-Zenker était déjà informée de ce fait avant l'investissement.
5. La grande polyvalence des robots industriels leur permet en outre d'être utilisés à d'autres postes dans la production. Les robots sont la solution idéale pour les étapes de travail en série, où ils travaillent rapidement et précisément et soulagent leurs collègues humains. Ils sont également tout indiqués pour travailler sur des machines dangereuses pour l'homme (par exemple, les scies à ruban). Une fois programmé, un robot peut être employé, par exemple, dans le transport de matériaux et la logistique d'entrepôt, pour trier et stocker les matériaux de revêtement. Dans la ligne de production, c'est encore une fois un robot qui peut se charger de prélever les panneaux de l'entrepôt ou du système de transport et de les placer sur les éléments. De telles idées existent déjà dans la construction de bâtiments préfabriqués et de premiers pas en ce sens ont déjà été faits. Il est également imaginable que les robots soient utilisés à long terme dans d'autres domaines, par exemple pour appliquer de la colle ou du crépi. La production des éléments se déroule sur trois lignes Chez Bien-Zenker, pour l'instant, l'isolation est insérée de façon manuelle. Cela est réalisé sur une ligne de production, qui comprend au total cinq tables de travail et tables de retournement et deux ponts multifonctions WEINMANN de la gamme WALLTEQ M-380. Ces ponts sont équipés d'un changeur d'outils 12 positions, ainsi que de support d'agrégats et de deux agrafeuses travaillant en parallèle sur les deux côtés, pour obtenir une grande flexibilité d'usinage et un flux de travail rapide. Ce qui est remarquable, c'est que les tables de travail sur lesquelles sont préparés les éléments sont en service à Schlüchtern depuis 1996. Les matériaux de revêtement sont préconfectionnés par un centre d'usinage de panneaux HOMAG BHC 911, qui est chargé par un système de manutention automatique WEINMANN STORETEQ H-700. Les panneaux sont simplement découpés pour la ligne de production automatique et sont apportés par chariot à galets à l'emplacement de transfert des ponts multifonctions. Ces ponts prennent en charge les étapes d'usinage restantes à l'aide d'une ventouse après la pose du revêtement. Pour les panneaux pour les lignes manuelles, les ouvertures pour les prises, les interrupteurs, etc., sont également préparées dans le centre d'usinage de panneaux. Malgré la polyvalence de la ligne principale, ces lignes annexes sont exploitées en parallèle pour amortir les pics de charge de travail sur la ligne principale et pour produire des murs de jambette, qui ne peuvent pas être réalisés sur la station d'assemblage pour ossatures bois en raison de leur faible hauteur (≤100 cm). Après le deuxième revêtement sur la ligne principale, les chemins des différents éléments se séparent : les cloisons intérieures partent en direction du contrôle qualité, puis vers les stations de chargement, tandis que les cloisons extérieures traversent les stations pour le montage des fenêtres, ainsi que la pose du système ETICS et de la façade avant le chargement.
Ne pas réduire le nombre d'employés, mais les sources d'erreurs
Grâce à la ligne de production mise en service en 2017, Bien-Zenker GmbH a bénéficié d'une hausse significative en matière de qualité et de capacités, même si l'entreprise reste discrète et ne publie pas de chiffres précis. Pour donner une idée de l'efficacité de l'installation, on peut toutefois se baser sur le nombre d'unités actuellement livrées, en moyenne trois à quatre maisons par jour, produites par deux équipes. Au cœur de l'automatisation se trouve le robot industriel intégré dans la ligne de production qui permet d'adapter le processus d'insertion à différents montants grâce à sa technologie six axes. Cela augmente non seulement la flexibilité et la rapidité du processus, mais cela garantit également une plus grande sécurité de fonctionnement. Bien-Zenker est la preuve parfaite que l'automatisation dans la construction bois ne se fait pas au détriment des employés : " Nous voulions supprimer les sources d'erreurs humaines du processus de travail, pas l'homme lui-même. C'est pourquoi nous n'avons pas réduit nos effectifs au cours de la modernisation, mais au contraire embauché de nouveaux employés. Leurs postes sont devenus beaucoup plus attrayants, parce qu'il était important pour nous que l'automatisation facilite le travail de nos employés ". L'une des conditions préalables au bon fonctionnement de l'installation est que la qualité du bois doit être adaptée aux exigences du degré d'automatisation accru. D'autres secteurs au sein de l'entreprise, en particulier la logistique, ont également dû être développés dans le cadre de la restructuration. A titre d'exemple, René Honrath mentionne la manipulation des matériaux de revêtement : " Par le passé, nous ne travaillions qu'avec une seule pile de panneaux. Aujourd'hui, ils sont préassemblés et nous avons besoin d'un concept bien pensé pour trier, stocker et retrouver rapidement les différentes couches des panneaux ". René Honrath recommande également une ligne de production complète provenant d'un seul fournisseur : " Comme tous les composants d'une ligne de production doivent être reliés et parfaitement coordonnés, il est logique qu'ils proviennent d'un seul fabricant. Ce dernier doit en particulier assumer la responsabilité du logiciel de commande ". De ce fait, WEINMANN a non seulement fourni la nouvelle ligne de production, mais aussi un composant de la commande de production.
Article de bauen mit Holz, 09/2018. Lisez l’article complet.
« En utilisant un robot industriel, nous obtenons désormais une augmentation significative des performances et une nette amélioration de la précision dimensionnelle des composants. »Herbert Vestert, directeur de production