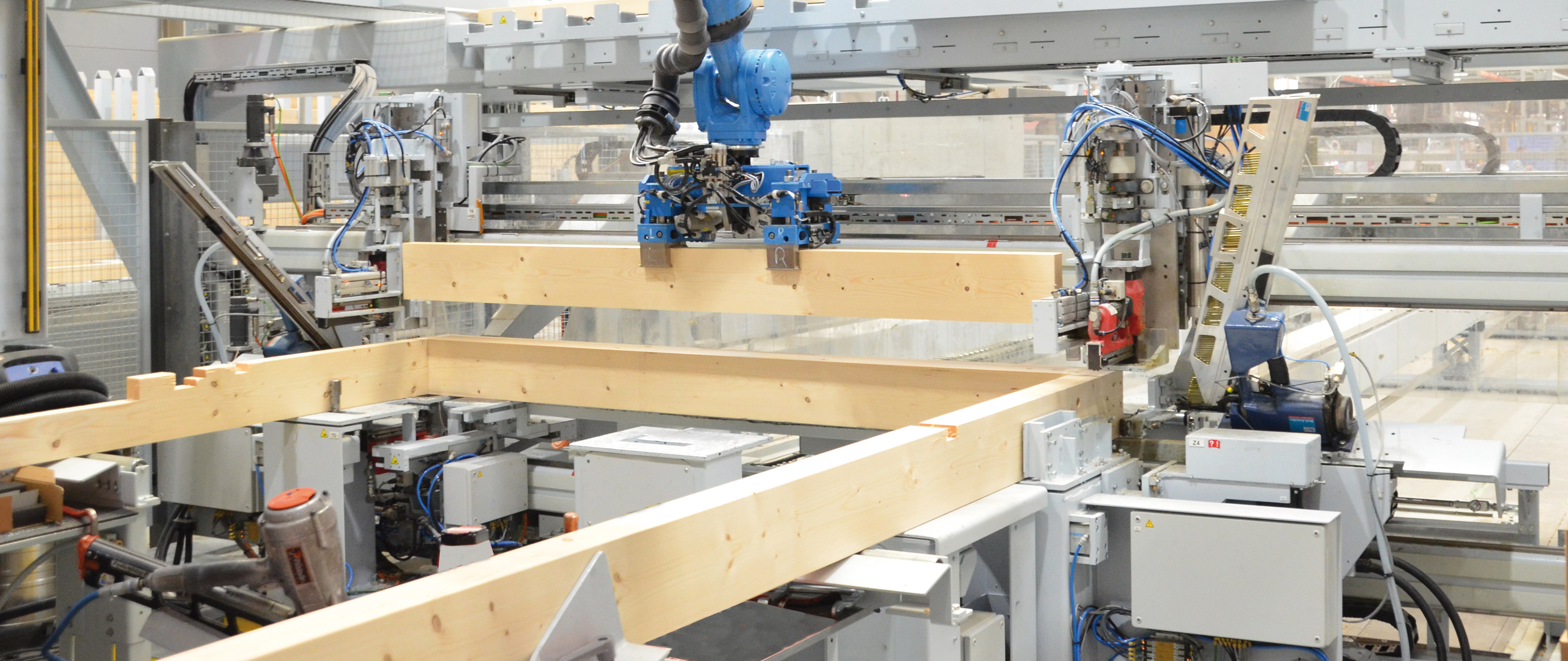
Prefabrication: Bien-Zenker GmbH, in Schlüchtern in the German state of Hesse, is one of the first timber construction companies to use an industrial robot in its production line. The robot, which is integrated in a frame work station, not only achieves an unprecedented amount of flexibility and speed, it also makes the workplaces at the prefabricated construction manufacturer look more appealing.
Following the automation of beam processing, the modernization of production processes is now entering its second phase in many carpentry businesses. While these businesses are investing in fully automated element production, the prefabrication industry is already entering phase three. In addition to automating the handling and logistics systems, this third phase is bringing a groundbreaking innovation into the production halls of timber production companies: the industrial robot. As experience shows that the prefabrication industry often preempts developments in the field of carpentry by just a few years, and because the systems used could actually be of interest to smaller timber construction companies, it is worth looking at this development in more detail.
The objective: greater precision and capacity
One of the pioneers of the new technology is Bien-Zenker GmbH, from Schlüchtern in the German state of Hesse. The company was founded as a carpentry business and sawmill in Birstein in 1906, and at the end of the 1990s, took on its current form after a takeover by Zenker Hausbau. The company is now one of the big players in the German prefabrication industry.
This year, 780 houses will leave the plant in Schlüchtern. Next year, the aim is to produce significantly more than 800 houses. These houses are currently planned, produced and assembled by more than 500 employees, and the company's annual sales are around EUR 150 million. As Bien-Zenker had been showing signs of growth for some years, in 2014/15, the company started the process of modernizing its production systems. According to technical manager René Honrath, on the one hand, the aim was to put the company in a position to cope with increasing quantities in the coming years - quantities that would have brought the previous production line to its capacity limit. On the other hand, "we were looking for the improvement in precision that can be achieved with automated production." This indicates that before the modernization, processes in the production hall at Schlüchtern were significantly more manual. For example, at the previous frame work station, not only were the studs occasionally inserted by hand - in some cases, routing and drilling on the frame work were also performed manually. Sometimes an employee also had to realign timber to achieve the required precision.
Fully automatic material transport
In light of this background, the current production conditions appear to have taken a huge step forward: studs, top plates and bottom plates are automatically kept in an upright store by a WEINMANN STORETEQ H-700 feed gantry and then supplied to the beam processing system as required. The transport takes place using vacuum panel suckers which protect the material, meaning that the feed gantry can also move timber without causing visibility problems. The beams are processed by a WEINMANN BEAMTEQ B-660, equipped with a 20-kW Flex-25 sawing unit for five-axis processing (e.g., for angled, curved, rafter assembly, and rip cuts). The machine also has a 6.6-kW underfloor unit for finger routers, dovetail routers, or drills, and a four-axis unit with 18.5 kW and a twelve-part tool changer. With all of this equipment, the machine offers high beam processing performance, precision, and flexibility. Thanks to the underfloor unit, no tilting is required during processing. At Bien-Zenker, the marking and labeling units are used frequently. These units enable employees at subsequent work stations to assign the components to the respective elements uniquely. This applies in particular to components for the gable and knee wall line, which have to be removed from the outfeed of the beam processing machine manually. After beam processing, top and bottom plates are separated and fed to a frame work station automatically via cross transports. At this station, they are positioned fully automatically. Processed special studs enter the "stud tower" via a horizontal chain transport. This tower is a random storage system in which each stud is stored in a controlled way so that it can be accessed immediately when it has to be installed, and can automatically be provided at a collection station on the frame work station. Standard studs are held in stacks in a second storage facility. From there, the studs are fed into a mini beam processing machine which executes bore holes and markings. They then go not to the stud tower, but to a second collection station on the frame work station via a second STORETEQ H-700 handling system.
Interest in robots in timber work is constantly increasing
The studs are removed from both collection stations by a six-axis industrial robot, which places the studs in the frame work automatically. The KUKA robot was supplied by HOMAG and integrated into the production cell together with WEINMANN. Here, the robot achieves higher levels of speed and precision than are possible with comparable technologies for creating frame works. The robot also offers a significant degree of machine availability and production reliability. The expectations that Bien-Zenker had of the new system in this regard have been fulfilled. Production manager Herbert Vestert: "We are noticing both a remarkable increase in performance and a clear improvement in the dimensional accuracy of the components." By using an industrial robot in timber frame production, WEINMANN is seizing on a development that has already revolutionized the automotive industry. There are lots of signs that a similar development will be triggered in the timber work industry, even though we are at the very beginning of any such development.
What is noticeable, however, is that for some time, the interest in robots in the timber work industry has continued to increase.
There are reasons for this:
1. Robots are flexible. Networked with the overarching production control system of the prefabricated house company, the robot at Bien-Zenker can be adjusted to new situations in the production process at any time. Primarily, this means that the robot receives information in real time about which stud to remove from which collection station and place in the current position in the frame work. Flexibility also means that the robot can insert any type of stud at any angle. Hence, gable and knee walls and window and door openings can be created fully automatically on the frame work station in Schlüchtern.
2. Robots require little maintenance and do not tire. Not only do they work quickly, they maintain this speed over the entire shift without any drop in performance or breaks. The amount of physical work required is significantly reduced, which relieves the burden on the employees. As the weight of timber in production is continuously increasing, this topic is becoming ever more important. The improved working ergonomics also make the workplace more appealing.
3. Robots are commodities. On the one hand, this means that timber construction companies can access mature and proven systems; on the other hand, it means that the level of investment is manageable.
4. One factor that has a positive effect on the acceptance of the new systems is that the "robot colleague" can relieve the burden on craftspeople, but cannot replace them. In the automotive industry, a well-trained human workforce in production has proven to be irreplaceable. Bien-Zenker was well aware of this before making the investment.
5. Thanks to the flexibility of the industrial robot, it is feasible to imagine using it at other points in production. Robots are the ideal solution for work steps performed in sequence, where they work quickly and precisely and ease the workload on their human colleagues. They are also suitable for work on machines that pose a risk for humans (e.g. band saws). For example, once instructed, a robot could be used in material transport and storage logistics for sorting and storing sheathing materials. The production line could then include a robot that removes the panels from storage or the transport system and places them on the elements. This sort of thinking is already happening in the prefabricated construction industry, and first steps in this direction have already been taken. It is also feasible to imagine that in the long term, robots will be used in further areas such as the application of glue or plaster.
Elements are produced on three lines
At Bien-Zenker, insulation is currently inserted manually. This takes place on a production line that encompasses five work and turning tables and two WEINMANN WALLTEQ M-380 multifunction bridges. The latter are equipped with a twelve-part tool changer, carriers on both sides, and two clamping devices that work in parallel to achieve a high level of processing flexibility and a fast workflow. What is remarkable is that the work tables that the elements are produced on have been in use at Schlüchtern since 1996. A HOMAG BHC 911 panel processing center preassembles the sheathing materials and is itself fed by an automatic WEINMANN STORETEQ H-700 handling system. For the automatic production line, the panels are simply cut to contour and brought to the transfer point on the multifunction bridges via trolley. Once the panels have been placed on the multifunction bridges via suction lifting devices, the bridges perform the remaining processing steps. In the case of panels for the manual lines, the openings for sockets, switches, etc. are also prepared in the panel processing center. Despite the flexibility of the main line, these auxiliary lines operate in parallel to absorb load peaks on the main line and to produce knee walls which cannot run via the frame work station due to their low height (≤100 cm). After the second sheathing on the main line, the individual elements go their separate ways: internal walls go to the quality check and from there to the loading stations, whereas outside walls run through the stations for window installation and the application of the EIFS and the facade before loading.
Eliminating human errors, not humans
The production line launched in 2017 has brought Bien-Zenker a significant increase in quality and capacity, even if the company is reserved when it comes to publishing precise figures. However, one indicator for the performance of the system is that the quantity currently delivered-on average three to four houses per day-is produced in two-shift operation. At the heart of the automation is the industrial robot integrated into the production line. Thanks to six-axis technology, this robot enables the insertion process to be adapted to different studs. This not only increases the flexibility and speed of the robot, but also provides greater operating safety. Bien-Zenker is a good example of the fact that automation in timber work does not have to be to the disadvantage of employees: "We wanted to remove sources of human error from the work process, not the humans themselves. Therefore, as part of the modernization, we have recruited new employees rather than reducing the level of staff. Their workplaces have become significantly more attractive because it was important to us to relieve the burden on the people as part of the automation." The prerequisites for smooth operation of the system include aligning the quality of the timber with the requirements of the increased level of automation. Other areas of the company-especially logistics-also had to be developed further as part of the restructuring. As an example, René Honrath cites the handling of sheathing materials: "Previously, we worked with the panels from the stack. Today, the panels are preassembled and we need a well thought-out concept for sorting and storing the panels and then finding the individual panel positions again." René Honrath also recommends using a complete production line from one source: "Because all the components of such a production line have to be networked and perfectly aligned with one another, it makes sense if they all come from one manufacturer. In particular, the manufacturer should take over the responsibility for the control software." WEINMANN has therefore supplied not only the new production line but also a production control module.
An article from bauen mit Holz, 09/2018. Here you can read the article.
“By using an industrial robot, we now have a significant increase in performance and a clear improvement in the dimensional accuracy of the components.”Herbert Vestert, Production Manager