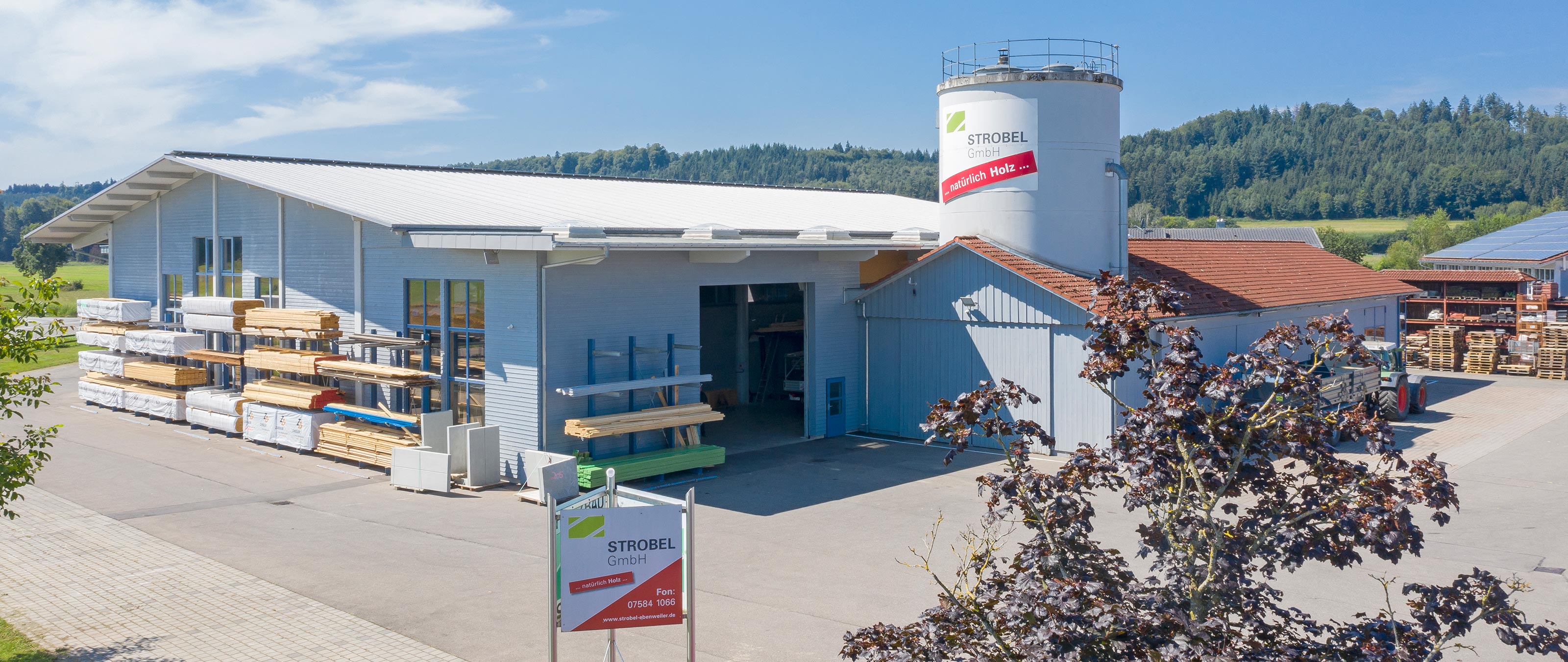
Gdybyśmy podzielili historię konstrukcji drewnianych na epoki, prawdopodobnie trwałaby teraz era uniwersalistów. Spadek ilości zamówień w sektorze budynków jednorodzinnych, a także w sektorze budownictwa użytkowego i mieszkaniowego pokazały bowiem wyraźnie, że warto być wszechstronnym. W ten sposób przedsiębiorstwa mogą sobie zrekompensować straty w jednym obszarze działalności poprzez ekspansję na innym polu. W takiej sytuacji znalazła się firma Strobel GmbH z niemieckiej miejscowości Ebenweiler, w Badenii-Wirtembergii. Sektor domów drewnianych, którym założyciel tego przedsiębiorstwa Arthur Strobel zajął się już pod koniec lat 80. ubiegłego wieku, został dotknięty znacznym spadkiem koniunktury także w tym regionie. Mimo to właściciel nie wstrzymywał swoich codziennych prac stolarskich w swoim zakładzie. Z biegiem lat rozszerzał działalność o kolejne obszary, takie jak wielokondygnacyjne budownictwo użytkowe i mieszkaniowe, budowa przedszkoli i szkół, renowacje, nadbudowy, a w pewnym stopniu także budownictwo modułowe. Coraz wyraźniejsza stała się przy tym tendencja do realizacji pod klucz, również w ramach indywidualnych projektów rozbudowy według życzeń klienta. Oprócz tego w zakładzie w Ebenweiler, zatrudniającym około 45 pracowników, do dziś wykonywane są zlecenia na wiaty samochodowe, domki ogrodowe i więźby dachowe – łącznie z planowaniem, nowoczesną produkcją i pracami blacharskimi.
Region silny gospodarczo
Przedsiębiorstwo Strobel GmbH działa w regionie o silnej gospodarce, a swoją działalność poszerzało o obszary o zwiększonym popycie kształtowanym między innymi przez umiejscowione tam duże firmy farmaceutyczne i technologiczne. Do dziś niewiele się w tym zakresie zmieniło, choć nastąpiły pewne ruchy. Gdy zapotrzebowanie na budynki jednorodzinne spadło z 30–35 domów rocznie do około 10, szansą na wyrównanie strat była działalność w sektorze budownictwa wielokondygnacyjnego. Do tego doszły renowacje i nadbudowy, na które wciąż jest dużo zleceń w tym regionie, dzięki czemu firma Strobel GmbH dalej w dużym stopniu wykorzystywała swoje moce przerobowe. Współpracowała przy tym z odbiorcami w stosunkowo niewielkiej odległości 40–50 km i to bez konieczności reklamowania swoich usług – także dziś niemal wszyscy klienci trafiają do firmy z polecenia.
„Mały” most z piłą
W 2016 r. Johannes Strobel dołączył do swojego ojca Arthura i wspólnie z nim stanął na czele firmy. W 2019 r. ze względu na dobrą sytuację na rynku ojciec z synem podjęli pierwszą próbę automatyzacji produkcji elementów ram drewnianych: „Zależało nam na pile do obróbki płyt pilśniowych, ale musielibyśmy wtedy zainwestować w duży most wielofunkcyjny. To nas zniechęciło”. W 2023 r. wraz z wprowadzeniem do sprzedaży maszyny WEINMANN WALLTEQ M-300 sytuacja zasadniczo się zmieniła. Ten most wielofunkcyjny stanowi dobre rozwiązanie na początek dla zakładów dysponujących niewielką przestrzenią, a przy tym zapewnia nie tylko funkcję frezowania, lecz poza agregatem do łączenia klamrami, gwoździarką i agregatem do oznaczania jest wyposażony także w piłę. Dla Johannesa Strobela, który chciał zainwestować w automatyzację produkcji przede wszystkim z uwagi na utrzymanie jednolicie wysokiej precyzji, było to „opłacalne rozwiązanie, skrojone na miarę przedsiębiorstw naszych rozmiarów”.
Precyzja i ergonomia
Oprócz precyzji kluczową kwestią dla Johannesa Strobela była również ergonomia: „Zależało mi na ułatwieniu pracy moim pracownikom. Chciałem, żeby nie musieli już klęcząc ręcznie układać płyt”. Dodatkowym pozytywnym efektem okazał się fakt, że starsi pracownicy, którzy nie chcieli już działać na placu budowy, zamiast odchodzić z firmy mogli przejść do zespołów pracujących na hali. W obliczu niedoboru pracowników w regionie jest to istotna korzyść. Ponadto za sprawą automatyzacji firma Strobel nie musi już angażować tak wielu pracowników w produkcję, a zamiast tego może skierować ich do innych obszarów. Pod koniec 2022 r. Johannes Strobel wznowił kontakt z przedstawicielem firmy WEINMANN: „Jest to człowiek, który pochodzi z tego regionu i od lat zna nasz zakład. Pod względem planowania nie trzeba więc było mu zbyt wiele tłumaczyć”. Z uwagi na szeroką ofertę produktów, dla właściciela zakładu ważne było również to, żeby na nowej linii produkcyjnej można było obrabiać także elementy dachowe i stropowe.
Maksymalna elastyczność
Rozmowy zakończyły się zamówieniem na maszynę WALLTEQ M-300 ze stołem montażowym. Ponieważ firma posiadała już jeden stół montażowy marki WEINMANN, powstało gniazdo złożone z dwóch stołów, które uzupełniono o dwa podnośniki płyt. Jedyne ograniczenie zastosowane na życzenie samego zakładu polega na tym, że elementy są obracane nie za pomocą stołu motylkowego, lecz przy użyciu dźwigu halowego. „To nam jednak w zupełności wystarcza. Początkowo myśleliśmy o dodatkowym stole montażowym, jednak postanowiliśmy nieco zwolnić tempo. Według mnie ma to sens, ponieważ tego rodzaju restrukturyzacja wymaga także dostosowania i optymalizacji dotychczasowych procesów w zakładzie pod kątem nowo wprowadzonej technologii. A jeżeli będziemy chcieli później rozbudować maszynę, nie będzie z tym problemu dzięki modułowej konstrukcji rozwiązań WEINMANN”.
Sprawne przejście
Krótki termin realizacji inwestycji okazał się dla zakładu niemal sportowym wyzwaniem: „Nowa technologia miała zostać wdrożona w około trzy miesiące. W tym czasie musieliśmy nie tylko rozbudować halę, lecz także zaznajomić nasz dział przygotowania produkcji z nowymi zadaniami” – wyjaśnia Johannes Strobel. Ze wszystkim zespół poradził sobie brawurowo: z punktu widzenia kierownictwa rozbudowa hali łącznie z uzyskaniem pozwolenia na budowę, a także samą produkcją i montażem elementów przebiegła „w miarę bezproblemowo”. Dodatkową korzyścią dla firmy jest jasny podział między produkcją a innymi obszarami pracy, dzięki czemu można było w pełni zoptymalizować procesy w każdej ze stref. Stolarze są też bardzo zadowoleni z procesów przygotowania produkcji. „Gdy obaj mistrzowie z tego działu usłyszeli termin realizacji całego przedsięwzięcia, zrobili wielkie oczy. Jednak w pełni popierali pomysł restrukturyzacji, zaangażowali się i wszystkie zadania wykonali śpiewająco”. Przygotowania zaczęły się od kilkudniowego szkolenia u dostawcy oprogramowania SEMA. Następnie pracownicy usiedli do tworzenia firmowego katalogu elementów, który obowiązuje do dziś: „Taki proces wymaga dużo czasu i wysiłku, zwłaszcza że katalog trzeba wciąż na bieżąco aktualizować. W międzyczasie przydzieliliśmy do działu przygotowania produkcji trzeciego pracownika i to jest chyba dobry układ”. Jednak pierwszy cel udało się osiągnąć już przy pomocy dwóch pracowników – uruchomienie nowej maszyny wiosną 2023 r. odbyło się sprawnie i bez komplikacji, przestojów czy przerw w produkcji. „Podziękowania za to należą się także pracownikom WEINMANN, którzy towarzyszyli nam w uruchomieniu produkcji” – wspomina Johannes Strobel. „Byli znakomicie przygotowani – zarówno jeśli chodziło o oprogramowanie CAD, jak i o samą obsługę maszyny. Przez wiele dni pracowali z naszymi ludźmi nad rozwiązaniem newralgicznych kwestii, za co jesteśmy bardzo wdzięczni”.
O 30% szybciej
Oprócz zwiększenia tempa produkcji początki pracy z nową maszyną dostarczyły też dużo informacji i praktycznych wniosków. Firma Strobel GmbH produkowała wówczas elementy do dużego projektu. Dwa z trzech identycznych budynków wielokondygnacyjnych zostały już ręcznie wyprodukowane i zmontowane, a trzeci w całości powstawał na nowej linii produkcyjnej. Można więc było w łatwy sposób porównać wydajność obu procesów – po około pięciu dniach szkolenia pracownicy mogli już samodzielnie pracować z nową maszyną i przy pierwszym projekcie udało im się skrócić czas produkcji z sześciu do czterech tygodni. „Byliśmy pod wrażeniem, jak szybko wszystko przebiegało i jak dużo czasu zyskaliśmy. Od razu przyspieszyliśmy produkcję o 30%, zgodnie z zapowiedziami przedstawicieli WEINMANN, a z czasem, gdy jeszcze lepiej zaznajomimy się z nowymi procesami roboczymi, oszczędności czasu będą nawet większe”. W ostatecznym rozrachunku oznacza to znaczne zwiększenie zdolności produkcyjnych, co jest dużą zaletą, gdy trzeba w krótkich terminach dostarczać elementy ścian, stropów i dachów do dużych przedsięwzięć. Większy przerób nie był jednak dla kierownictwa głównym celem tej inwestycji – wzrost mocy produkcyjnych miał posłużyć w dużej mierze do zwiększenia stopnia prefabrykacji. Wzrost wolumenu nie jest więc proporcjonalny: „Dziś możemy produkować więcej, a moce maszyny są w dużym stopniu wykorzystywane, jednak obecnie wytwarzamy też takie elementy, których ręczne przygotowanie było dla nas kiedyś zbyt skomplikowane” – mówi młodszy z szefów. Przykład? Złożone geometrie dachów, które realizuje się dziś za pomocą odpowiednio ukształtowanych elementów dachowych, a które kiedyś trzeba było formować dopiero na budowie belka po belce.
Pozytywne konkluzje
Dziś więc wszystkie elementy pochodzące z zakładu z Ebenweiler są dostarczane w postaci w pełni prefabrykowanej, a informacje zwrotne z montażu są pozytywne. Jak mówi Johannes Strobel: „Już w czasach produkcji ręcznej byliśmy bardzo precyzyjni, ale dziś wszystko jeszcze lepiej do siebie pasuje na budowie. Elementy dachowe niemal same się układają we właściwej pozycji, a poprawki odeszły już właściwie do przeszłości. W kwestii nowej technologii panuje ogólna zgoda co do tego, że powinniśmy byli wprowadzić ją dużo wcześniej”. Dotyczy to także pracowników produkcji, których liczba zmniejszyła się do czterech lub pięciu w trybie zmianowym: „Pracownicy chwalą sobie nowy sposób pracy, który nie obciąża już ich pleców i kolan” – wyjaśnia Johannes Strobel. „Jeden z naszych ludzi powiedział mi ostatnio, że od czasu wprowadzenia nowej maszyny nie wraca już do domu całkowicie wykończony. Napawa mnie to nadzieją, że on i inni pracownicy będą mogli dłużej dla nas pracować”. Podsumowanie inwestycji w Ebenweiler jest zatem jednoznaczne: wszystkie cele zostały osiągnięte! Precyzja produkcji jest większa, złagodzono problem niedoboru pracowników i znacznie skrócono czas produkcji. Klienci również są zachwyceni nową technologią. Doceniają przemysłową precyzję i automatycznie generowaną dokumentację wszystkich etapów pracy, co przekłada się na bezproblemowy montaż na budowie. Nie jest przy tym nawet potrzebna żadna reklama – wciąż niemal wszyscy klienci dowiadują się o firmie pocztą pantoflową. I wygląda na to, że jeszcze przez długi czas tak pozostanie.
„Byliśmy pod wrażeniem, jak szybko wszystko przebiegało i jak dużo czasu zyskaliśmy. Od razu przyspieszyliśmy produkcję o 30%, zgodnie z zapowiedziami przedstawicieli WEINMANN, a z czasem, gdy jeszcze lepiej zaznajomimy się z nowymi procesami roboczymi, oszczędności czasu będą nawet większe.”Johannes Strobel, dyrektor Strobel GmbH
Strobel GmbH
Firma Strobel GmbH z siedzibą w Ebenweiler, w Niemczech, produkuje drewniane elementy konstrukcyjne, takie jak elementy ścian, stropów i dachów, a także inne komponenty drewniane do zastosowania w różnych projektach budowlanych, m.in. do budowy budynków wielokondygnacyjnych, przedszkoli, szkół i do realizacji projektów renowacyjnych. W 1987 r. Alfons Strobel założył firmę we własnym garażu. W 1990 r. przeniósł ją do parku przemysłowego, a w roku 2016 jego syn Johannes Strobel po zaliczonym egzaminie mistrzowskim dołączył do ojca jako drugi szef. Dziś na terenie zakładu liczącym 11 000 m2 stoją cztery duże hale. Firma zatrudnia około 45 pracowników, w tym pięciu uczniów.
Więcej informacji