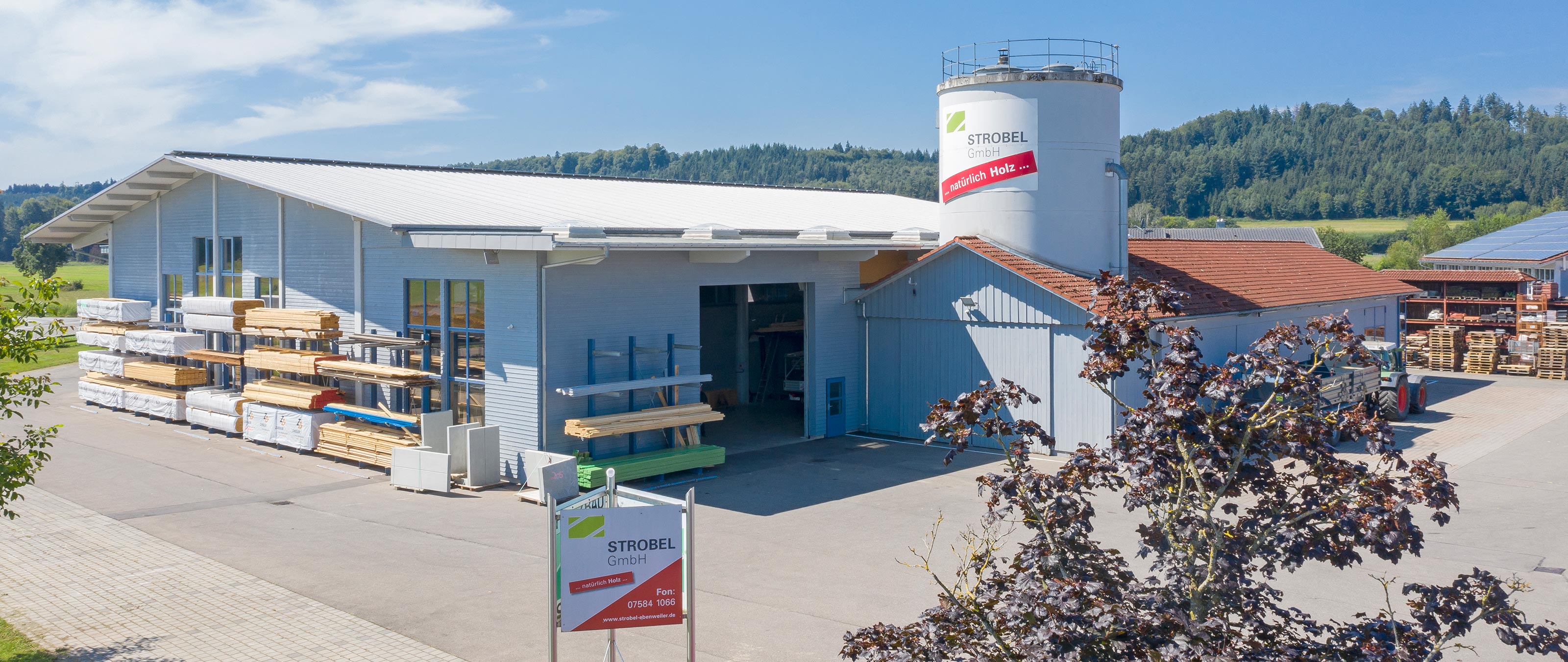
If you were to categorize timber construction into eras, now would probably be the age of the universalists. This is because the decline in the number of orders in detached house construction, commercial construction and residential construction has made one thing particularly clear — it is advantageous to have a broad base. Because then it is easy to offset losses in one business area by moving to another. This is also the situation at Strobel GmbH, which is located in Ebenweiler, a village in the district of Ravensburg, Germany. Timber house construction, which company founder Arthur Strobel started at the end of the 1980s, had also experienced significant decline in this area. However, Arthur Strobel continued the classic carpentry business in the company. Over the years, many new business areas have been added, such as multi-story commercial and residential construction, construction of kindergartens and schools, renovation projects, extensions and some modular constructions. All of these are becoming turnkey offerings, even if extension levels are offered according to individual customer requirements. And in Ebenweiler, around 45 employees continue to build carports, summer houses and roof trusses — including planning, modern production and sheet metal work.
Economically strong region
As Strobel GmbH is located in a strong economic region with large pharmaceutical and technology companies, the new business areas were added in the wake of increased demand for the company. To date, little has changed in this situation, even though there have been some sideways movement in the business areas. When detached house construction fell from 30 to 35 houses per year to around 10, multi-story construction was a way to offset the losses. Together with renovation projects and extensions, for which there is still strong demand in the region, the capacity at Strobel GmbH continues to be very well utilized. The company has a relatively small delivery radius of 40 to 50 km and does not advertise — even today, almost 100 percent of customers are obtained by word of mouth.
"Small" bridge with saw
In 2016, Johannes Strobel joined his father Arthur on the management board. In view of the good market situation, father and son made a first attempt in 2019 to automate the production of wood frame elements: "At that time, however, we would have had to invest in a large multifunction bridge because a saw was important to us for processing fiberboards. That put us off." In 2023, this situation fundamentally changed with the introduction of the WEINMANN WALLTEQ M-300. This multifunction bridge is also an entry-level solution for woodworking shops, requiring only a small amount of space. It not only offers a trimming function, but is also equipped with a saw in addition to the usual bracket, nailing and marking units. For Johannes Strobel, who wanted to invest in automated production primarily because of the consistently high level of precision, this was "an affordable solution tailored to suit companies of our size."
Precision and ergonomics
In addition to precision, Johannes Strobel was also focused on ergonomics: "Making work easier for employees was very important to me. They should no longer have to kneel on the elements and lay panels by hand." A positive side effect is that older employees who no longer want to work on the construction site can now be deployed in the hall, so that they remain at the company for longer. Given the strained staffing situation in the region, this is a clear advantage, all the more so because automation reduces the number of employees required in production, enabling them to be deployed in other areas. At the end of 2022, Johannes Strobel contacted the relevant WEINMANN employee again: "They come from the region and have known our company for years, so there was little to clarify when it came to planning." In view of the wide product portfolio, something that was important to Strobel was being able to also process roof and ceiling elements on the new production line.
Maximum flexibility
At the end of the discussions, the order for a WALLTEQ M-300 with an assembly table was placed. Since the company already had an assembly table from WEINMANN, the result is a two-table system that the master carpenter supplemented with two panel positioners. The only restriction, at the request of the carpentry business, is that the elements are not currently turned with a butterfly turning table, but by an overhead crane, "but that is completely sufficient for us. We first thought of having an additional turning table, but then decided on a somewhat slower pace of development. This makes sense to me in the case of such restructuring, because the processes in the company must also be adapted to the new technology and optimized. And if we want to expand the system at a later date, this is no problem thanks to the modular design that come as standard at WEINMANN."
Seamless change
The short delivery time proved to be a physical challenge for the carpentry business: "The new technology was to arrive in around three months, and during this time, we not only had to complete a hall extension, but also prepare our work preparation for the new tasks," explains Johannes Strobel. And the company managed all this with ease. From the management's point of view, the hall extension, including the building application, component production and assembly, was "fairly unproblematic." The company benefits from a clear separation between production and other work areas, so that processes in each area can be better optimized. He is also highly satisfied with the work preparation processes. "When they heard about the delivery date, the two foremen in this department raised their eyebrows somewhat. But they were fully behind the restructuring, were committed and they did a great job." Their preparation began with a training course lasting several days at the software company SEMA, after which they went on to develop the company's own component catalog, which is still running today: "A process like this means a lot of work and takes time, especially since such a component catalog has to be maintained even after it has been finalized. In the meantime, we have recruited a third employee in work preparation, and that seems to be working well now." However, the short-term goal was achieved with just two employees: The commissioning of the new technology in the spring of 2023 went smoothly, without standstill or production downtimes. "We also owe this to the WEINMANN employees who supported us at the start of production," remembers Johannes Strobel: "They were very competent, in terms of both the CAD software and the work on the machine. For several days, they worked out solutions with our employees in key areas, and that was really great."
Thirty percent faster
And, thanks to an unlikely turn of events, it was also extremely informative. At that point in time, Strobel GmbH was producing components for a large-scale project: Two of the three identical multi-story buildings had already been produced and assembled manually, while the third ran completely on the new production line. This allowed a direct comparison to be made. Although the employees were working independently with the new technology after around just five days of training, they succeeded in reducing the production time from six to four weeks for this first project. "It all happened extremely quicky and we saved an amazing amount of time in production. We reached the 30 percent increase stated by WEINMANN from the offset, and it's probably even higher now, because we are even better acquainted with the work processes." The bottom line is that this is a significant increase in capacity, which is something that Strobel is happy about when wall, ceiling and roof elements have to be delivered for large projects in a timely manner. However, higher quantities were not the primary objective of the managing directors' investment, which is why they use the increase in capacity to a large extent to increase the level of prefabrication. The volume did not increase proportionally: "We are already producing more and the machine is well utilized, but we are now also producing components that were too complicated for us when our production was still manual," says the junior manager. An example? Complicated roof geometries, which are now realized with roof elements, whereas they were previously assembled on-site, beam by beam.
Positive verdict
Today, all components made in Ebenweiler arrive at the construction site completely prefabricated, and the feedback from assembly is also insightful. Johannes Strobel: "We already had a high level of precision when our production was manual, but today everything fits together even better on the construction site. Roof elements slide to the correct position as if by themselves, reworking is practically no longer an issue. In general, everyone is of the same opinion about the new technology — that we should have introduced it much earlier." This also applies to production employees, whose number has shrunk to four or five in one-shift operation: "There is a lot of praise here for the new way of working that is gentle on the back and knees," explains Johannes Strobel. "One employee recently told me that since the transition, he has been feeling less tired in the evenings after work. I hope that he and the others will be able to work for us for longer." The verdict in Ebenweiler: All objectives achieved! Production is more precise, the problem of staff shortages has eased and production times have been drastically reduced. Customers are also impressed by the new technology and welcome the construction reliability, which is linked to industrial precision and the automatic documentation of all process steps. However, the restructuring is not advertised, as almost all customers are still obtained through recommendations. And there is much to suggest that this will remain so for a long time to come.
mmen. Und es spricht viel dafür, dass dies noch lange so bleiben wird.
An article from the trade magazine "mikado," October 2024 issue. To the trade magazine
“It was extreme how quickly it all went and how much time we gained in production. We reached the 30 percent increase stated by WEINMANN from the offset, and it's probably even higher now, because we are even better acquainted with the work processes.”Johannes Strobel, Managing Director Strobel GmbH
Strobel GmbH
Strobel GmbH, based in Ebenweiler, in the district of Ravensburg, Germany, produces timber construction elements such as wall, ceiling and roof elements as well as other wood components for use in various construction projects, including multi-story buildings, kindergartens, schools and renovation projects. In 1987, Arther Strobel founded the company in his own garage. In 1990, the company moved to the industrial estate, and in 2016, son Johannes Strobel joined the management board after passing the master craftsman examination. Today, the company premises cover approximately 11,000 square meters with four large halls. The company employs around 45 people, including 5 apprentices.
More information