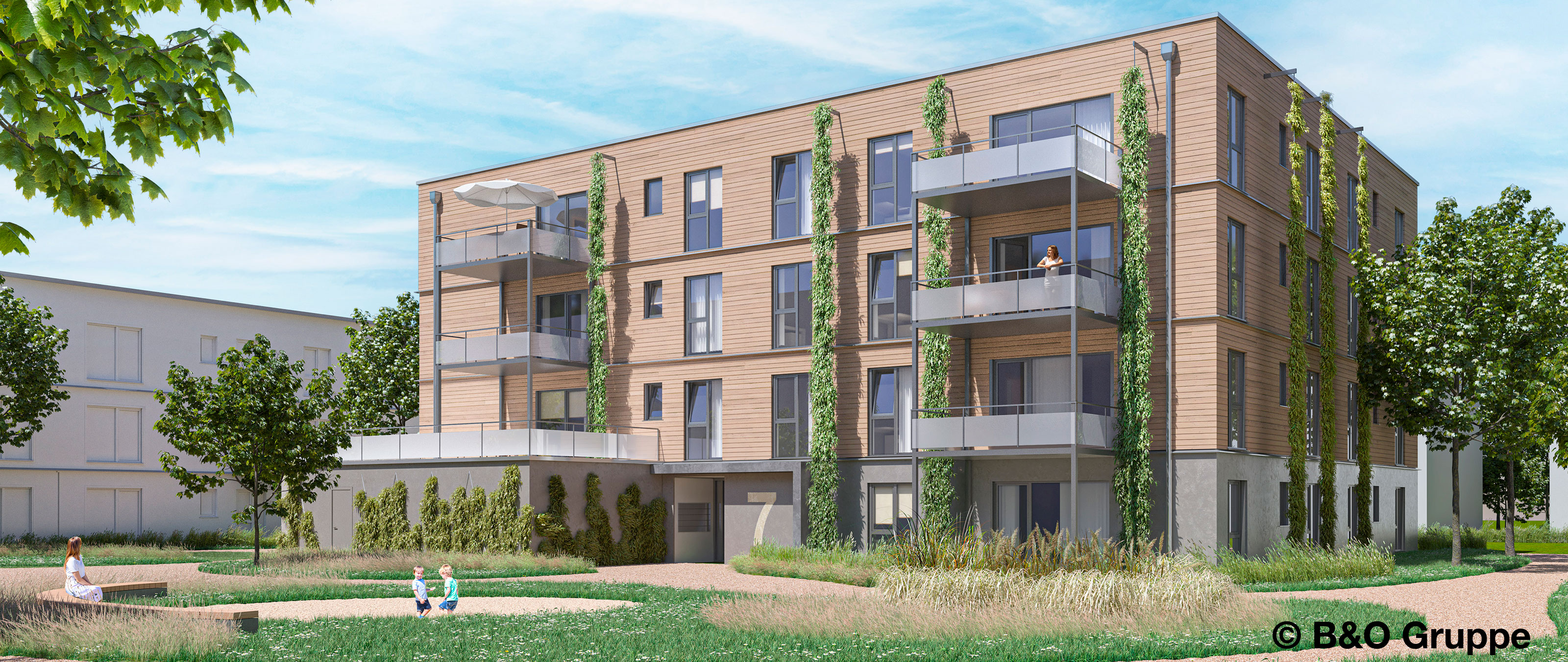
Kreatywne wykorzystanie surowca stanowi nieodłączną część pracy w sektorze budownictwa drewnianego, który wciąż wdraża nowe materiały i systemy budowlane. Ze względu na nowe obszary działalności i nowych uczestników rynku motywacja do wprowadzania świeżych rozwiązań jest obecnie szczególnie duża. Można się więc spodziewać niespodzianek. Jedna z nich kryje się w nowym zakładzie produkcyjnym we Frankfurcie nad Odrą należącym do firmy B&O Bau GmbH z siedzibą w Bad Aibling. Ciekawe jest tam nie tylko wyposażenie od firmy WEINMANN Holzbausystemtechnik: całkowicie automatyczna stacja montażu szkieletu, cztery mosty wielofunkcyjne, jeden most wdmuchujący oraz trzy rzędy stołów roboczych i obrotowych. Zaskakujący jest przede wszystkim produkt, który powstaje na linii produkcyjnej. Uwagę przyciąga już stacja montażu szkieletu – jak mówi kierownik ds. rozwoju w B&O Michael Schäpers, jest to jedno z kilku unikatowych urządzeń indywidualnie opracowanych we współpracy z firmą WEINMANN. Stacja wyposażona jest w robot i wykonuje obróbkę słupków, łączonych ze sobą w sąsiedniej hali na maszynie BEAMTEQ B-660 i doprowadzanych przez w pełni automatyczny magazyn. Nietypowe w tym procesie jest to, że dzięki specjalnemu oprogramowaniu robot nie tylko tworzy drewniane konstrukcje szkieletowe, ale również zespala ze sobą po dwa słupki – przy użyciu dwóch gwoździarek na gwoździe faliste. W ten sposób powstaje wytrzymały element pionowy z litego drewna konstrukcyjnego, którego pas górny i dolny stanowią wąskie płyty CLT mocowane po bokach. Elementy oporowe regularnie rozmieszczone w pasach dbają o to, aby konstrukcja zachowywała dokładne wymiary na całej długości. W zależności od potrzeb statycznych między słupkami można zamontować podpory o większej nośności (stalowe lub bukowe). Okna i drzwi nie są wycinane, jak w przypadku innych konstrukcji z drewna litego, lecz wieńczone nadprożem, co pozwala oszczędniej wykorzystywać zasoby. Dla Michaela Schäpersa „jest to jedyny sposób, aby zapewnić ciągły i wydajny materiałowo proces produkcji, podobny do stosowanego w przemyśle motoryzacyjnym. Skraca się dzięki temu czas obróbki, można oszczędzić czas i koszty związane z usuwaniem resztek i nie trzeba płacić za materiał, który traci się przez wycinanie otworów”.
Modułowe konstrukcje drewniane na pięciu do ośmiu kondygnacji
Unikanie konstrukcji z elementami leżącymi w ścianie nośnej już pokazuje, że B&O Bau mierzy wysoko. W istocie – firma zajmuje się przede wszystkim budynkami wielopiętrowymi, obejmującymi od pięciu do ośmiu kondygnacji. Dokładnie mówiąc, są to wysokiej jakości i korzystne cenowo konstrukcje wielopiętrowe wykonane (niemal) w całości z drewna. Połączenia między ścianami a stropami są wykonywane przy użyciu wieńców ze zbrojonego betonu wylewanego na miejscu. Wysoką jakość elementów drewnianych udaje się osiągnąć między innymi dzięki wysokiej precyzji maszyn i dwuwarstwowej budowie ścian. Części lite i konstrukcje szkieletowe są produkowane na przemian i łączone ze sobą na koniec pierwszej fazy produkcyjnej, przy czym elementy z litego drewna pełnią funkcję nośną, a konstrukcje szkieletowe – izolacyjną. Na linii produkcyjnej elementy konstrukcyjne przechodzą jeszcze przez inne nowe urządzenia, takie jak WALLTEQ M-300 insuFILL z mechanizmem czyszczenia, który dba o czystość powierzchni płyty izolacyjnej. Do zastosowanego wyposażenia dodatkowego należy także „mechanizm płukania wstecznego”, który wprowadza z powrotem do magazynu dużą część materiału izolacyjnego pozostającego w przewodach wdmuchiwania. W ten sposób proces ważenia jest bardziej precyzyjny („wypłukany” materiał izolacyjny jest ponownie ważony), a ponadto proces ten ułatwia zmianę rodzaju izolacji, ponieważ materiał izolacyjny osadza się tylko na jednym, krótkim odcinku przewodu. W zależności od życzeń klienta we frankfurckim zakładzie stosuje się wdmuchiwany materiał izolacyjny z celulozy lub wełny mineralnej. Cztery duże magazyny materiału izolacyjnego wraz z doprowadzeniem pakietów izolacyjnych są własnymi konstrukcjami firmy B&O Bau. Pod koniec produkcji odbywa się łączenie dwóch rodzajów elementów na stole obrotowym. Są one układane jeden na drugim i transportowane na przesuwnym stole roboczym do linii numer 3, gdzie następuje śrubowanie obu warstw – zmodyfikowane agregaty śrubujące z wkrętami o długości 200 mm to kolejne unikatowe urządzenie. Proces produkcyjny kończy się mocowaniem uszczelnienia fasady, maszynowym ustawianiem i mocowaniem łaty i kontrłaty za pomocą dwóch mostów wielofunkcyjnych i wreszcie montażem fasady.
Niemiecki dostawca kompleksowych rozwiązań
Równie złożone, jak ta wielowarstwowa konstrukcja ścian, jest przedsiębiorstwo, które ją opracowało. Rodzinna firma B&O od 30 lat zajmuje się renowacjami, a od 15 lat działa w sektorze budownictwa drewnianego i hybrydowego. Obecnie tworzy grupę spółek obejmującą dwie główne dywizje: B&O Service i B&O Bau. Jednostka B&O Service świadczy takie usługi, jak nadzór nad osiedlami mieszkaniowymi, łącznie z naprawami i obsługą awarii, a B&O Bau działa jako główny wykonawca projektów budowlanych pod klucz. Prowadzi budowę nowych obiektów, modernizację istniejących, dobudowę parkingów i renowacje – w tym coraz częściej także modernizacje modułowe, które uznaje się za sektor rynku o dużym potencjale. B&O Bau zatrudnia około 750 pracowników, w tym 350 rzemieślników, w zakładach w całych Niemczech. Te lokalne spółki przejmują klientów z rynku mieszkaniowego i zapewniają im wsparcie w trakcie całego projektu za pośrednictwem partnera działającego w danym regionie. Dla przedsiębiorstw z sektora budownictwa mieszkaniowego, biur projektów lub inwestorów posiadają szeroki zakres produktów o różnych standardach jakości – oferta obejmuje np. parkingi o konstrukcji z drewna bukowego. Projekty są opracowywane przez wewnętrznych lub zewnętrznych ekspertów z grupy, którzy specjalizują się w danej dziedzinie budownictwa. Elementy wykorzystywane do realizacji pochodzą częściowo z zewnętrznych zakładów partnerskich, a w coraz większej mierze są także produkowane we własnych zakładach grupy – np. moduły łazienkowe powstają w Chorwacji, a w Bad Aibling planuje się rozpocząć produkcję stropów. To wzmacnia własną zdolność produkcyjną firmy, co dobrze wpisuje się w kontekst optymalizacji kosztów. Od ukończenia zakładu we Frankfurcie nad Odrą wszystkie projekty będące w zaawansowanym stadium realizacji przechodzą dodatkowo proces weryfikacji zgodności ze standardami konstrukcyjnymi stosowanymi w grupie.
Nowy system konstrukcji wzbogaca portfolio grupy o bardzo interesującą ofertę: „Klient może odebrać budynek znacznie szybciej i przy mniejszych kosztach niż ma to miejsce w przypadku innych rozwiązań konstrukcyjnych” – wyjaśnia Michael Schäpers. „A do tego zyskuje bardzo wysoką jakość”.
System modułowy do produkcji seryjnej
Aby osiągnąć swoje cele, firma nie spoczęła na korzystnym cenowo systemie konstrukcji ścian. Zmiana paradygmatu będzie możliwa dopiero wtedy, gdy nastąpi połączenie minimalnego wykorzystania zasobów i zautomatyzowanego wytwarzania wysoko znormalizowanych elementów – z wykorzystaniem znacznie zautomatyzowanego procesu cyfrowego, który pozwala na skrócenie wszystkich operacji w ramach modelu BIM utworzonego w programach REVIT i AutoCAD. „Przykładowo na podstawie jasno zdefiniowanych parametrów profili montowanych w ścianie system może mi powiedzieć bezpośrednio po wykonaniu projektu, który z profili jest obciążony w 23%, a który w 89%” – wyjaśnia Michael Schäpers. Mówiąc wprost: duża część wartości statycznych jest generowana automatycznie i musi zostać jedynie zweryfikowana. „Nasze narzędzia statyczne pozwalają nam działać w sposób niezwykle wydajny pod względem zużycia materiałów, a więc do produkcji ścian zużywamy dokładnie tyle drewna, ile potrzeba, i ani milimetra więcej”. Wymaga to wysokiego stopnia standaryzacji modułów produkcyjnych i obszernej biblioteki cyfrowej z zapisanymi wszystkimi elementami i szczegółami konstrukcji – ich stworzenie było ogromnym zadaniem, które wymagało dużego nakładu pracy i wiedzy. Na podstawie danych wygenerowanych głównie przez spółki regionalne, oprogramowanie do planowania może np. obliczyć właściwości termiczne wybranych przegród zewnętrznych, tak aby fizyk budowlany mógł sporządzić ocenę bezpośrednio na podstawie planu. Ciągły proces cyfrowy obejmuje również inne instalacje, takie jak instalacja elektryczna. Gdy w modelu 3D projektu tworzy się gniazdko elektryczne, w tle automatycznie aktualizowany jest schemat obwodowy, podczas gdy w systemie CAD powstaje otwór na gniazdko i normatywna płyta gipsowo-włóknowa z prowadzeniem przewodów. Wykorzystanie tego rodzaju procesów niezwykle skraca przygotowanie pracy – Schäpers mówi o redukcji o 95% z około 30 do nawet zaledwie 2 dni na budynek. „Choć podczas planowania indywidualnego trzeba od nowa narysować każdy budynek, to w większości przypadków podział na elementy opiera się na gotowym projekcie i danych z biblioteki”. Michael Schäpers oszacował potencjalne oszczędności w całym projekcie na niebagatelne 50%. System modułów ma przy tym charakter otwarty, dzięki czemu można stosować bardzo indywidualne rozwiązania. Ponieważ elementy nośne, warstwa izolacyjna i fasada tworzą wielowarstwową konstrukcję, to konstrukcja nośna – zazwyczaj wykonana ze słupków o grubości 12,5 cm – zależnie od wartości statycznych wzmacnia się dzięki zwiększonym przekrojom. Klient, który ogląda model BIM budynku, może wybierać z systemu różne fasady, a także różne poziomy izolacji. W ten sposób na etapie planowania dostępny jest cały szereg rozwiązań ściennych i stropowych, szybów instalacyjnych i innych szczegółów. Elastyczność ta daje również dodatkowe korzyści: umożliwia np. stałe magazynowanie CO<1>2</1> w litym rdzeniu budynku odwracalnego, którego fasadę można po upływie czasu bez problemu odnowić, a poziom izolacji w razie zwiększenia wymagań – zastąpić nowymi materiałami. W produkcji model trójwarstwowy ma tę zasadniczą zaletę, że elementy drewnianego szkieletu do niższych budynków – grupa posiada również takie rozwiązania – przechodzą przez linię bez konieczności przezbrajania maszyn. To samo dotyczy elementów szkieletowych do modernizacji modułowej, które stanowią obecnie większość zleceń we frankfurckim zakładzie. Pod względem produkcyjnym izolacja niczym się nie różni w porównaniu z tą stosowaną w nowych budynkach, nawet jeśli planistyczne przygotowanie projektu modernizacji – ze skanem stanu zastanego, chmurą punktów 3D i cyfrowym modelem budynku – jest bardziej złożone. Aby wyrównać odchylenia wymiarów, budynek osłania się dodatkowo warstwą izolacyjną o grubości 30–40 mm, która zapewnia dopasowanie do standardowej przegrody zewnętrznej.
Rozwiązanie idealne do dużych ilości sztuk
System modułowy – w połączeniu z linią produkcyjną we Frankfurcie nad Odrą – zapewnia zdolność produkcyjną niezbędną do realizacji dużych projektów. B&O Bau określa obecnie moce produkcyjne swojego zakładu na poziomie 25 000 m<1>2</1> rocznie, ale przy pracy jednozmianowej i przy czasie taktu wynoszącym 40 minut na element dwuwarstwowy i około 20 minut na element konstrukcji szkieletowej nie jest to jeszcze ich ostatnie słowo. Michael Schäpers, który uważa, że możliwa jest dalsza optymalizacja czasu taktu i że wprowadzenie drugiej zmiany w przyszłości jest prawdopodobne, ocenia potencjalne moce przy pełnym obciążeniu nawet na 200 000 m<1>2</1> rocznie. Należy przypuszczać, że ze względu na korzyści, jakie niesie ze sobą ten sprawdzony i bezawaryjny system w zakresie oszczędności kosztów, czasu i poziomu jakości, liczba sztuk w zakładzie we Frankfurcie będzie tylko rosnąć. Wynika to również z tego, że w ramach weryfikacji zgodności około 95% projektów realizowanych przez B&O Bau jest zgodnych ze stosowanymi modułami. Przy wielkości rastra 12,5 cm nie jest to zaskoczeniem, ponieważ w dużych projektach takie różnice wymiarów nie mają znaczenia.
Wspólnie wypracowane rozwiązania
We frankfurckim zakładzie firmie B&O Bau udało się to, co z perspektywy czasu Michael Schäpers określa jako graniczące z cudem: „W ciągu dwóch lat stworzyliśmy całkowicie nowy system konstrukcyjny i dostosowany do niego proces produkcyjny”. Pomysł ten pojawił się na posiedzeniu zarządu w 2021 r., kiedy to wspólnik dr Ernst Böhm zasugerował, aby w przyszłości samodzielnie prowadzić produkcję: „Już wtedy można było przewidzieć, że popyt na przystępne cenowo mieszkania będzie można zaspokoić jedynie poprzez kompleksową optymalizację procesów. Stało się więc jasne, że rozwój produkcji budynków wielopiętrowych był krokiem w kierunku zwiększenia stopnia naszego uprzemysłowienia. Jeśli chcemy pozostać na rynku, musimy być liderami i tworzyć nowe trendy w planowaniu i produkcji”. Pracę nad nowym systemem konstrukcji modułowych Michael Schäpers, który jako inżynier technologii drewna od wielu lat zajmował się projektowaniem maszyn, rozpoczął od pustej kartki papieru oraz spotkań z producentami maszyn i podzespołów – początkowo z niewielkim powodzeniem. Dopiero propozycja firmy WEINMANN, polegająca na połączeniu stacji montażu szkieletu z robotem, doprowadziła do powstania koncepcji produkowania litego elementu ściany ze słupków: „Taka maszyna może pracować z dużą prędkością. W ten sposób mogliśmy osiągnąć wysoką wydajność materiałową, niezwykle wysoką nośność i ciągłość procesu, który objął wszystkie maszyny, sterowane ze stanowiska MES dostarczonego przez granIT”. Firma WEINMANN była otwarta na nowe rozwiązania, „więc omawialiśmy krok po kroku całą instalację, aż układ maszyny był gotowy”. Początkowo firma B&O Bau korzystała z doradztwa SCHULER Consulting, „co było bardzo pomocne przy rozpoczęciu projektu, ponieważ zaczynaliśmy praktycznie od zera. Jednak ze względu na nasze wyjątkowo specyficzne wymagania bardzo szybko przystąpiliśmy do planowania wspólnie z działami rozwoju i sprawnie opracowaliśmy nasz dzisiejszy układ. Dzięki współpracy na równych zasadach znaleźliśmy dobre rozwiązanie dla każdego zadania. Dziś jako inżynier technologii drewna jestem w pełni zadowolony ze sposobu pracy maszyn w naszym zakładzie. Firma WEINMANN również bardzo dobrze poradziła sobie z takimi kwestiami, jak konserwacja zapobiegawcza oraz prewencyjna kontrola agregatu”. Z wdrażaniem procesów produkcyjnych w nowym zakładzie się nie spieszono – rozpoczęto je w 2022 r. od głównej części instalacji i wielu prac ręcznych. Dzięki temu można było przeszkolić pracowników i zaznajomić ich z nowym produktem. Produkcje seryjną uruchomiono dopiero na początku tego roku. „Po upływie dwóch i pół miesiąca od uruchomienia instalacji osiągniemy solidny poziom od 90% do 95% we wszystkich obszarach, a nasze docelowe wartości taktu już teraz okazały się mocno zaniżone. Oznacza to, że jedną ścianę nośną, która na konwencjonalnej linii podlegałaby 40-minutowemu frezowaniu, a w zakładzie rzemieślniczym potrzebowałaby od 4 do 6 godzin, my już teraz możemy wyprodukować w 15 minut. Wszyscy zaangażowani w ten projekt mogą więc być z siebie dumni”.
„Dzięki współpracy na równych zasadach znaleźliśmy dobre rozwiązanie dla każdego zadania. Dziś jako inżynier technologii drewna jestem w pełni zadowolony ze sposobu pracy maszyn w naszym zakładzie.”Michael Schäpers, kierownik ds. rozwoju, B&O Bau GmbH
B&O Gruppe
Rodzinna firma B&O od 30 lat zajmuje się renowacjami, a od 15 lat działa w sektorze budownictwa drewnianego i hybrydowego. Obecnie tworzy grupę spółek obejmującą dwie główne dywizje: B&O Service i B&O Bau.
Jednostka B&O Service świadczy takie usługi, jak nadzór nad osiedlami mieszkaniowymi, łącznie z naprawami i obsługą awarii, a B&O Bau działa jako główny wykonawca projektów budowlanych pod klucz. Prowadzi budowę nowych obiektów, modernizację istniejących, dobudowę parkingów i renowacje – w tym coraz częściej także modernizacje modułowe, które uznaje się za sektor rynku o dużym potencjale. B&O Bau zatrudnia około 750 pracowników, w tym 350 rzemieślników, w zakładach w całych Niemczech.