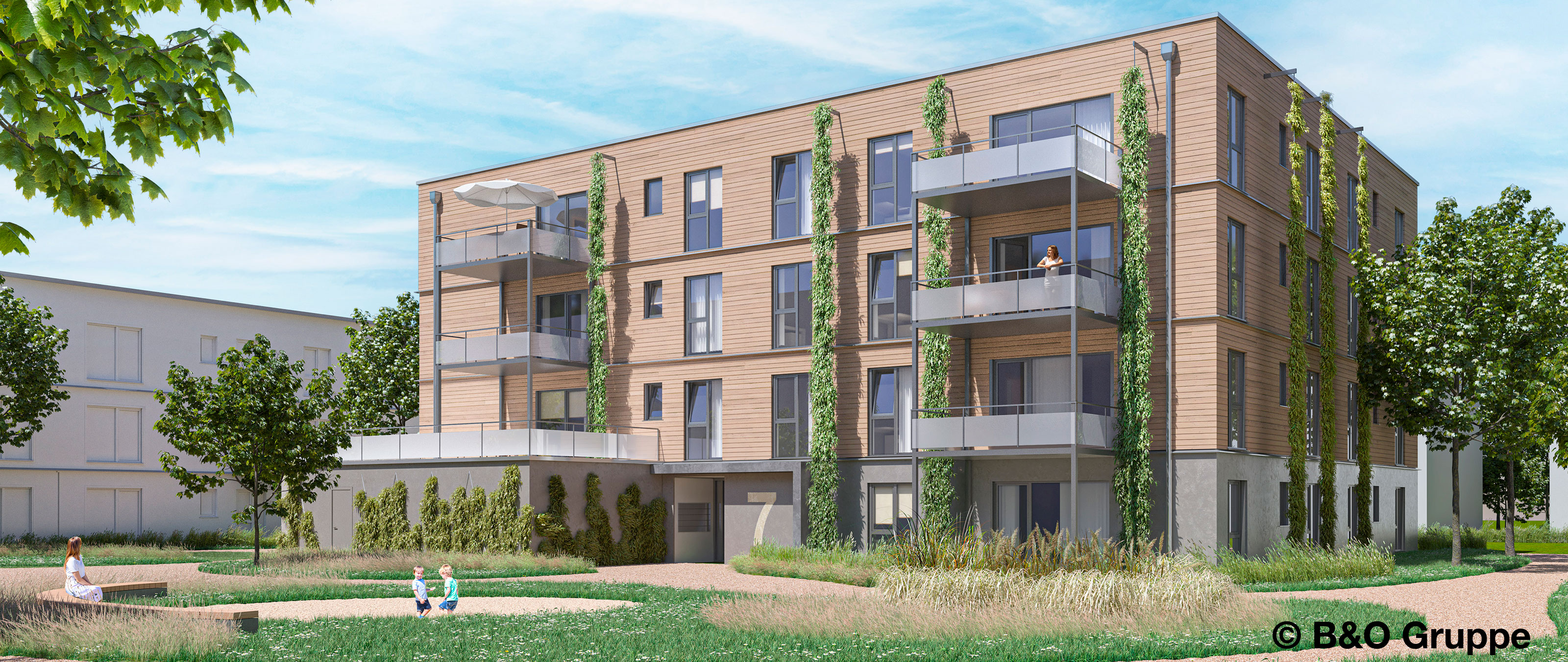
L'utilisation créative du matériau initial fait partie intégrante d'un ADN de la construction en bois qui offre sans cesse à la branche de nouveaux matériaux et systèmes de construction. Compte tenu des nouveaux secteurs d'activité et des nouveaux acteurs du marché, l'incitation à de nouveaux développements est actuellement particulièrement forte. Les surprises sont donc de mise. Les visiteurs de la nouvelle usine de production de B&O Bau GmbH, basée à Bad Aibling, à Francfort-sur-l'Oder, en vivront une. Non seulement en raison de l'équipement fourni par WEINMANN Holzbausystemtechnik, qui mérite d'être vu avec une station d'assemblage pour ossature bois entièrement automatique, quatre ponts multifonctions, un pont d'insufflation et trois rangées de tables de travail et de tables de retournement. Le produit qui traverse la ligne de production est particulièrement surprenant. La différence se manifeste déjà au niveau de la station d'assemblage pour ossature bois, selon Michael Schäpers, directeur du développement de B&O Bau, l'une des nombreuses pièces uniques développées lors des entretiens de planification avec WEINMANN. Equipée d'un robot, la station traite des montants taillés dans le hall voisin sur une BEAMTEQ B-660 et alimentés via un stockeur entièrement automatisé. Ce qui est exceptionnel dans ce processus, c'est que grâce à un logiciel spécial, le robot ne pose pas seulement des constructions à ossature bois, mais aussi montant contre montant : après la pose, le nouveau montant est relié au précédent par deux cloueuses à clous ondulés. On obtient ainsi un élément de construction massif et porteur en KVH vertical, dont les lisses supérieures et inférieures ne se situent pas au-dessus du bois vertical, mais sur les côtés du composant sous forme de fines planches CLT. Des butées régulières dans les lisses garantissent que le composant conserve ses cotes sur toute la longueur. En fonction de la nécessité statique, il est possible d'insérer des piliers plus résistants (acier, hêtre de construction) entre les bois verticaux, les fenêtres et les portes ne sont pas découpées comme dans d'autres systèmes de construction massive, mais sont reliées par des linteaux, ce qui permet d'économiser des ressources. Pour Michael Schäpers, « c'est la seule façon de mettre en place un processus de production continu et efficace en matière de matériaux, comme dans l'industrie automobile, par exemple. Je gagne du temps pour ce qui est de l'usinage, j'évite les pertes de temps et les frais d'élimination des restes et je ne dois pas payer le matériau dans les ouvertures. »
Construction bois de série pour 5 à 8 étages
Le fait d'éviter les bois horizontaux dans le noyau du mur statiquement porteur laisse déjà présager qu'avec sa construction murale, B&O Bau vise haut. En effet, on vise en premier lieu les constructions à plusieurs étages entre cinq et huit étages. Pour être précis, il s'agit d'une construction à plusieurs étages de haute qualité et peu coûteuse, réalisée (presque) exclusivement en bois : la jonction entre les murs et les plafonds est pourvue sur le chantier d'une sorte d'ancrage circulaire en béton armé coulé sur place. La qualité élevée des pièces de construction en bois est obtenue entre autres grâce à une grande précision mécanique et à une structure de mur à double paroi : des éléments massifs et des ossatures bois produits en alternance sont combinés à la fin de la première phase de fabrication, les éléments massifs faisant office d'éléments porteurs et les ossatures bois d'éléments isolants. Sur le trajet à travers la chaîne de fabrication, les composants passent par d'autres nouveautés, comme un WALLTEQ M-300 insuFILL doté d'un mécanisme de nettoyage qui assure une surface d'appui propre du panneau isolant après chaque élément. Un autre équipement spécial est le « mécanisme de rétro-rinçage » qui renvoie la majeure partie de l'isolant résiduel contenu dans les conduites d'injection au magasin. Le processus de pesée est ainsi plus précis : le matériau isolant renvoyé est pesé une nouvelle fois, et par ailleurs, le « rétro-rinçage » simplifie le changement de matériau isolant, car il ne reste du matériau isolant que dans une courte pièce d'alimentation. Selon les souhaits du client, on insuffle à Francfort-sur-l'Oder des isolants en cellulose ou en fibres minérales. Les quatre grands magasins de matériaux isolants, y compris l'alimentation pour les paquets de matériaux isolants, sont des constructions propres à B&O Bau. A la fin de la fabrication de l'élément, le « mariage » des deux éléments se déroule sur une table de retournement. Superposés, ils se déplacent sur une table de travail mobile vers la ligne trois, où le vissage des deux coques est effectué ; les agrégats de vissage modifiés avec des vis d'une longueur de 200 mm sont une autre pièce unique sur la ligne. Le processus de fabrication s'achève par la pose de la membrane d'étanchéité de la façade, la mise en place et la fixation mécanique du lattage et du contre-lattage par deux ponts multifonctions et enfin, par le montage de la façade.
Fournisseur complet dans toute l'Allemagne
La construction murale est aussi diversifiée que la société qui l'a développée. Actif depuis 30 ans dans l'assainissement et depuis 15 ans dans la construction bois et hybride bois, le groupe familial B&O se répartit aujourd'hui dans les principales divisions B&O Service et B&O Bau. Tandis que B&O Service est responsable des domaines de services tels que le suivi de complexes résidentiels, y compris les réparations et les services de dépannage, B&O Bau agit en tant qu'entrepreneur général de projets de construction clés en main. En tant que telle, l'entreprise prend en charge la réalisation de nouveaux bâtiments et de surélévations, recouvre des places de stationnement et procède à des assainissements, avec une tendance croissante aux rénovations de série, lesquelles sont considérées comme un « marché en pleine croissance ». B&O Bau emploie environ 750 personnes, dont 350 artisans, sur des sites régionaux répartis sur l'ensemble du territoire fédéral. Ces sociétés régionales se chargent de l'acquisition de clients et proposent à leur clientèle du secteur du logement un suivi de l'ensemble du projet par un interlocuteur de proximité. Pour les personnes intéressées, lesquelles comptent des sociétés de construction de logements, des développeurs de projets ou des investisseurs, elles proposent une vaste gamme de produits de différents niveaux de qualité ; le portefeuille comprend par exemple des parkings en bois de hêtre. Les projets sont planifiés par des planificateurs internes ou externes du groupe spécialisé dans le domaine de la construction spécifique. Les pièces de construction pour la réalisation proviennent d'une part d'entreprises partenaires externes, dont les éléments en bois continuent d'être utilisés dans le cadre de projets correspondants. D'autre part, le groupe produit de plus en plus sur ses propres sites, par exemple des modules de salle de bains en Croatie, et la fabrication de ses propres plafonds est également prévue à Bad Aibling. Une extension de ses propres compétences en matière de fabrication qui s'inscrit dans le contexte d'un changement de paradigme vers la construction de systèmes à coûts optimisés. Depuis l'achèvement de l'usine de Francfort-sur-l'Oder, tous les projets à un stade avancé sont soumis à un processus supplémentaire de vérification de leur compatibilité avec les systèmes de construction du groupe.
Le nouveau système de construction enrichit le portefeuille du groupe d'une offre extrêmement intéressante : « Le client obtient son bâtiment beaucoup plus rapidement et à moindre coût qu'avec une autre méthode de construction », explique Michael Schäpers. « Et ce, dans une très grande qualité. »
Un système modulaire pour la construction en série
Un système pour ossature à bois bon marché ne suffira pas pour y parvenir Ce changement de paradigme est possible uniquement avec la combinaison d'une utilisation minimale des ressources et d'une fabrication automatisée de pièces de construction hautement standardisées avec un processus numérique largement automatisé qui permet de raccourcir des étapes de travail entières via un modèle BIM créé par le biais de Revit et d'AutoCAD. « Sur la base des performances clairement définies des profilés installés dans le mur, le système peut par exemple me dire, dès la fin de la conception, quel style est chargé à 23 % et quel style est chargé à 89 % dans le mur », explique Michael Schäpers. En clair : une grande partie des données statiques principales est éditée automatiquement et doit seulement être vérifiée. « Grâce à nos outils de statique, nous pouvons en outre procéder de manière extrêmement efficace en matière de matériaux, nous n'avons donc pas un millimètre de bois en trop dans le mur ». Les conditions préalables sont un système modulaire de fabrication largement standardisé et une bibliothèque numérique complète dans laquelle sont consignés tous les éléments et détails du système de construction : une tâche gigantesque au sein du projet qui a nécessité beaucoup d'efforts et de connaissances.. Sur la base des données générées principalement dans les sociétés régionales, le logiciel de planification peut également calculer, par exemple, les propriétés thermiques de l'enveloppe du bâtiment choisie, ce qui permet au physicien du bâtiment de déduire une évaluation de la physique du bâtiment directement à partir de la planification. Le processus numérique continu comprend également des équipements tiers tels que l'installation électrique : si une prise électrique est prévue dans le modèle 3D de l'ébauche, le schéma des circuits est automatiquement mis à jour en arrière-plan, tandis que le système de CAO crée un trou pour la prise femelle et une plaque de plâtre renforcée par fibres de cellulose conforme aux normes avec les guidages de câbles. La préparation du travail est extrêmement réduite grâce à de tels processus, Schäpers parle d'une réduction de 95 pour cent, passant d'environ 30 à jusqu'à deux jours par bâtiment. « Tandis qu'un préparateur de travaux dessine à nouveau chaque bâtiment dans le cadre d'une planification individuelle, chez nous, la fabrication des éléments est en grande partie issue de l'ébauche finie et de la bibliothèque. » Le potentiel d'économies sur l'ensemble du projet est énorme, Michael Schäpers le chiffre à 50 pour cent. Le système modulaire est ouvert pour tout typage, ce qui permet la mise en œuvre de solutions très individuelles. Dans la mesure où le système porteur, le niveau d'isolation et la façade forment un système multicouche, il est possible, en fonction de la statique, de renforcer le noyau porteur, normalement fabriqué à partir de montants de 12,5 cm d'épaisseur, avec des sections plus grandes. Le client, qui voit le bâtiment au préalable dans le modèle BIM, peut choisir une autre façade, mais aussi un autre niveau d'isolation, dans le système modulaire. Il dispose ainsi, lors de la planification, de toute une série de systèmes de parois et de plafonds, de noyaux de développement et de détails éprouvés. Cette flexibilité a également d'autres avantages : elle permet par exemple de stocker durablement du CO2 dans le noyau massif d'un bâtiment réversible, dont la façade peut être renouvelée sans problème à la fin de sa durée de vie et dont le niveau d'isolation peut être remplacé à tout moment par de nouveaux matériaux en cas d'exigences plus élevées. Dans la fabrication, le modèle à trois couches présente l'avantage essentiel que les éléments d'ossature bois pour les bâtiments bas à surface habitable efficace (le groupe a également des solutions à proposer dans ce domaine) passent par l'installation et ne nécessitent aucune transformation. Il en va de même pour les éléments d'ossature bois dans la rénovation en série, qui représente actuellement la majorité des commandes à Francfort-sur-l'Oder. Du point de vue de la technique de fabrication, il n'y a ici aucune différence avec le niveau d'isolation des nouveaux bâtiments, même si la préparation de la planification d'un projet de rénovation est plus complexe avec un scan de l'existant, un nuage de points 3D et un modèle numérique du bâtiment. Pour compenser les écarts de dimensions, on enveloppe en outre le bâtiment existant dans une couche d'isolation de 30 à 40 mm d'épaisseur, qui assure la précision d'ajustage lors du montage de l'enveloppe systémique.
Parfaitement équipé pour un grand nombre de pièces
En combinaison avec la ligne de production de Francfort-sur-l'Oder, le système modulaire fournit également les capacités indispensables pour les grands projets. B&O Bau indique que la capacité de production de son usine est actuellement de 25 000 m2/an, mais avec un travail en une équipe et des temps de cycle de 40 minutes pour un élément à double coque et d'environ 20 minutes pour un élément à ossature bois, on est probablement encore loin du compte. Michael Schäpers, qui estime qu'une nouvelle optimisation du temps de cycle est tout à fait possible et qu'une deuxième équipe est probable dans un avenir proche, voit dans l'installation à pleine charge de la place pour jusqu'à 200 000 m2/an. On peut supposer que le nombre de pièces produites à Francfort-sur-l'Oder devrait augmenter rapidement, compte tenu des avantages en matière de coûts, de temps et de qualité du système éprouvé, plus résistant aux pannes. Ceci également parce que, lors du contrôle de compatibilité, environ 95 % des projets réalisés par B&O sont compatibles avec les modules. Avec une trame de 12,5 cm, ce n'est pas une surprise, car de telles modifications dimensionnelles ne jouent aucun rôle dans les grands projets.
En bonne collaboration, nous avons trouvé des solutions
Avec l'usine de Francfort-sur-l'Oder, B&O Bau a réussi quelque chose qui, rétrospectivement, tient du miracle pour Michael Schäpers : « En deux ans environ, nous avons créé un système de construction radicalement nouveau et l'usine de fabrication correspondante ». L'idée est née lors d'une réunion de la direction en 2021, lorsque l'associé Dr Ernst Böhm a suggéré de prendre en main le processus de production à l'avenir : « Il était déjà prévisible à l'époque que la demande de logements abordables ne pourrait être satisfaite que par une optimisation globale des processus. Il était donc clair que le développement de la construction à plusieurs étages allait vers l'industrialisation. Pour participer, nous devions jouer un rôle de pionnier et apporter de nouvelles touches à la planification et à la fabrication. » Le développement du nouveau système modulaire a commencé pour Michael Schäpers, qui a conçu des machines lourdes pendant plusieurs années en tant qu'ingénieur en technologie du bois, avec une feuille de papier vierge et des visites chez les producteurs de composants et les fabricants de machines, sans grand succès dans un premier temps. Ce n'est que l'option proposée par WEINMANN de combiner une station d'assemblage pour ossature bois avec un robot qui lui a donné l'idée de produire un élément de cloison massif à partir de montants : « La machine peut le faire à grande vitesse. Nous obtenons ainsi une grande efficacité des matériaux avec une gamme de matières premières avantageuse, une capacité de charge extrême et un processus continu dans lequel toutes les machines sont intégrées via le poste de contrôle de la production MES de granIT ». Chez WEINMANN, on était ouverts aux nouveaux développements, « et c'est ainsi que nous avons parcouru l'installation point par point jusqu'à ce que le plan d'agencement de la machine soit terminé ». Au début, B&O Bau a profité des conseils de SCHULER Consulting, « ce qui a été très utile pour commencer, car nous partions pratiquement de zéro. Toutefois, compte tenu de nos souhaits très spécifiques, nous avons rapidement commencé la planification avec les départements de développement et nous sommes rapidement arrivés au plan d'agencement actuel. Une collaboration d'égal à égal a permis de trouver une bonne solution pour chaque tâche. Aujourd'hui, en tant qu'ingénieur technique du bois, il n'y a rien qui me rende nerveux sur les machines de notre usine. WEINMANN s'est également révélé très bien placé sur des sujets tels que l'entretien préventif et l'observation préventive des agrégats .» Lors de la mise en œuvre des processus de fabrication dans la nouvelle usine, on a pris du temps, on a commencé en 2022 avec une installation de fuselage et beaucoup de travail manuel. Nous avons ainsi pu former le personnel et nous rapprocher du nouveau produit. L'interrupteur de mise en service de la production en série n'a été remis en place qu'au début de cette année. « Deux mois et demi après la mise en service, nous atteignons de solides 90 à 95 % dans tous les domaines, et la cadence cible est déjà nettement inférieure. En d'autres termes, nous pouvons fabriquer en 15 minutes un mur porteur qui serait soumis à un fraisage de 40 minutes sur une seule ligne conventionnelle et qui, dans un environnement artisanal, requiert de 4 à 6 heures. Tous les participants peuvent en être fiers. »
« Une collaboration d'égal à égal a permis de trouver une bonne solution pour chaque tâche. Aujourd'hui, en tant qu'ingénieur technique du bois, il n'y a rien qui me rende nerveux sur les machines de notre usine. »Michael Schäpers, responsable développement B&O Bau GmbH
B&O Gruppe
Actif depuis 30 ans dans l'assainissement et depuis 15 ans dans la construction bois et hybride bois, le groupe familial B&O se répartit aujourd'hui dans les principales divisions B&O Service et B&O Bau.
Tandis que B&O Service est responsable des domaines de services tels que le suivi de complexes résidentiels, y compris les réparations et les services de dépannage, B&O Bau agit en tant qu'entrepreneur général de projets de construction clés en main. En tant que telle, l'entreprise prend en charge la réalisation de nouveaux bâtiments et de surélévations, recouvre des places de stationnement et procède à des assainissements, avec une tendance croissante aux rénovations de série, lesquelles sont considérées comme un « marché en pleine croissance ». B&O Bau emploie environ 750 personnes, dont 350 artisans, sur des sites régionaux répartis sur l'ensemble du territoire fédéral.