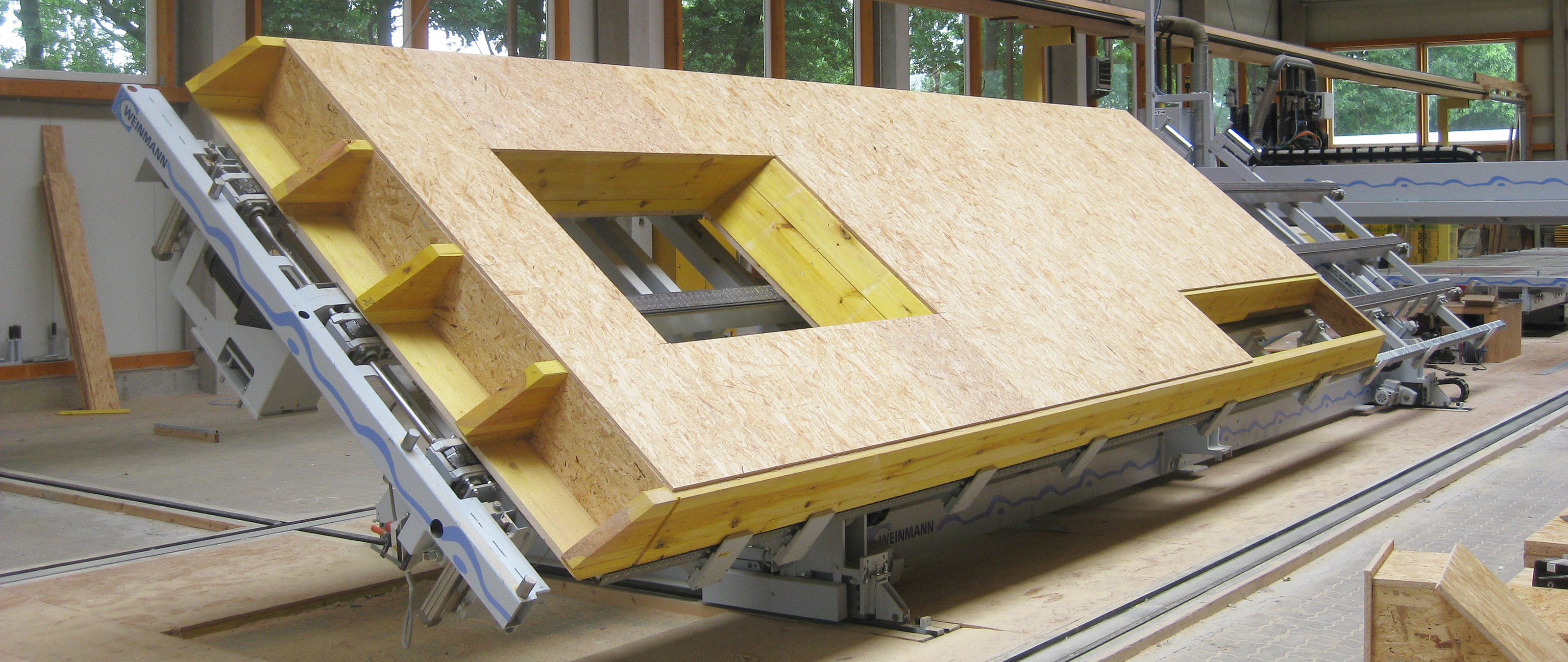
Article de HOLZBAU-MAGAZIN, 2/2017. Lecture de HOLZBAU-MAGAZIN Online.
Redacteur: Dr. Joachim Mohr, Tübingen
En 2008, la capacité atteint ses limites
En pleine période de crise, Daniel Harmdorf modernise la construction de panneaux en bois. Dans d'autres domaines d'activité, sa menuiserie de 50 employés se charge des travaux de menuiserie classiques comme les charpentes de toiture, fabrique et assemble des charpentes clouées, couvre les toits et fabrique des éléments de façade. Elle fournit, en outre, des pièces de construction à d'autres collègues menuisiers. Actuellement, ces produits livrés représentent environ 45 % du chiffre d'affaires.
La priorité de M. Hamdorf dans la construction à ossature bois porte sur la construction d'éléments et la construction commerciale. Or, la demande pour les immeubles, les garderies, les bureaux, les écoles ou les centres pour réfugiés est en constante augmentation dans sa région. C'est pour cette raison qu'en 2008, la menuiserie a atteint ses limites de capacité pour la fabrication d'éléments à ossature bois. A cette époque, trois employés produisaient des éléments en bois pour environ 6 maisons par an. « Déjà à l'époque, la demande avait triplé », se souvient Daniel Hamdorf.
Une restructuration menée à bien
Au lieu d'embaucher un ou deux employés supplémentaires et d'acheter une nouvelle table de travail, le maître charpentier est allé au bout des choses en suivant la devise du « tout ou rien ». Dans un premier temps, il installe un nouvel atelier de fabrication à ossature bois sur son site de production : Dimensions de 25 x 60 m, avec une hauteur de crochet de 7 m et une grue à portique d'une capacité de charge de 5 t. Il investit également dans un système Telecargo moderne équipé de 2 remorques et 8 ponts amovibles pour livrer ses pièces de construction au client.
La restructuration de son entreprise était centrée sur l'achat d'un pont multifonctions Weinmann équipé de trois tables de travail, qui a repoussé d'un coup les limites de capacité : Grâce à cette installation de production automatisée, M. Hamdorf a su répondre à la demande déjà existante en éléments à ossature bois mais il a également profité d'une forte hausse des commandes au cours des années suivantes. Aujourd'hui, la menuiserie fabrique des pièces de construction pour environ 60 maisons par an et son volume de construction à ossature bois a nettement décuplé.
L'investissement en termes de préparation du travail a donc augmenté. Toutefois, ceci est largement compensé par les temps de montage plus courts rendus possibles grâce à l'amélioration de la précision des composants et du niveau de préfabrication. Il ne fait aucun doute pour M. Hamdorf que le travail est plus rentable : Il a finalement enregistré une forte augmentation du chiffre d'affaires dans ce secteur d'activité, sans embaucher de personnel supplémentaire.
Cinq tables pour éviter les goulots d'étranglement et les blocages
Entre-temps, le nombre de tables dans la ligne de production est passé à cinq. Quatre tables étaient déjà en service depuis le début : La première table est un ancien modèle Weinmann, qui a été « recyclé » et qui est actuellement utilisé pour la production de l'ossature. Posée à la main, alignée avec un dispositif de serrage et clouée manuellement, une fois prête, l'ossature est transférée à la deuxième table avec un palan d'atelier, la première nouvelle table dans la ligne de production.
L'ossature en bois y est revêtue de planches. Les matériaux de revêtement se trouvent directement à côté de la table et sont manipulés facilement par les employés à l'aide des ventouses à panneaux. Le revêtement est ensuite agrafé par le pont multifonctions, puis il est usiné avec une scie et une fraise, avant d'être découpé et pourvu d'ouvertures destinées aux fenêtres, prises, interrupteurs, etc.
La séparation de ces opérations de production d'ossature aboutit finalement à des temps d'arrêt plus courts du pont multifonctions pendant les pics de commande, à condition qu'il n'y ait pas de goulot d'étranglement ou de blocage en amont.
A l'étape suivante, le cadre revêtu sur un côté pénètre dans un dispositif de retournement sur la troisième table. Là, l'isolation est posée avant que l'élément soit transporté par un convoyeur longitudinal vers la quatrième table, qui peut être déplacée transversalement. Sur cette table, le deuxième revêtement est posé puis fixé et usiné par le pont multifonctions.
Puis, il est transféré à la cinquième table que M. Hamdorf a achetée un peu plus tard : « C'est là que se déroulent aujourd'hui les usinages spéciaux, par exemple la pose de bardages en bois, de fenêtres ou d'espaces d'installation.
La table sert aussi à stocker temporairement un ou deux éléments de cloison en cas de goulot d'étranglement lors du chargement. Chez nous, les éléments de la dernière table sont transportés directement sur un pont amovible. »
Grâce à cette double fonction, la table 5 est une station importante qui permet de « soulager un tant soit peu » le flux de travail dans l'atelier et d'éviter les goulots d'étranglement dans la ligne de production.
Un bond en avant de la qualité
En 2009, l'installation est installée dans le nouvel atelier et mise en service par le personnel sans grandes difficultés initiales. Aucune phase d'optimisation prolongée des processus de production n'a eu lieu à Fahrenkrug. Daniel Hamdorf : « Bien sûr, il est important de discuter au préalable de ces changements avec les employés, mais beaucoup de ces changements sont évidents et nous avons aussi de bons employés capables de mettre en œuvre ces processus sans problèmes, ce dont je suis particulièrement fier. » « Par ailleurs, Weinmann offre d'excellents conseils dans la phase préparatoire, élabore un plan d'atelier en collaboration avec le client et propose des formations pour toutes les personnes concernées. Et puis, je me suis évidemment préalablement renseigné auprès de mes collègues. Cela permet de savoir rapidement à quoi il faut faire attention sur une ligne de production automatisée. »
En plus de l'augmentation voulue de la capacité, cette nouvelle technologie de production a permis de répondre rapidement à d'autres attentes : « A ce moment-là, nous voulions notamment transférer nos expériences positives de l'assemblage automatisé dans la fabrication d'éléments » se souvient Daniel Hamdorf. Il associe la notion « d'expériences positives » en premier lieu à une gestion professionnelle de la qualité.
Sur ce point, les résultats de l'entreprise sont probants : « Nous offrons aujourd'hui à nos clients une qualité constante et prévisible, à savoir, un niveau de préfabrication élevé de précision industrielle sans pour autant compromettre la qualité. »
Plus de souplesse et respect des délais
M. Hamdorf a également concrétisé son souhait d'optimiser sa flexibilité : Sur la machine Weinmann, nous fabriquons en taille de lot unitaire et pouvons donc livrer tout ce que le client désire. »
Cela est vrai non seulement pour les différents matériaux d'isolation que l'entreprise insère ou insuffle avec un système Isocell, mais également pour les constructions murales complexes, les détails sophistiqués et les panneaux muraux soumis à de fortes charges statiques, que l'on peut trouver dans la construction d'éléments : « Le client n'est pas obligé de s'adapter à notre construction murale car nous nous adaptons à la sienne, comme ce serait le cas dans l'artisanat. »
La gestion du temps est également devenue plus flexible à Fahrenkrug. D'une part, cela signifie que l'on peut répondre rapidement aux demandes urgentes pendant les périodes chargées. D'autre part, les processus de la production sont mieux planifiés, ce qui explique pourquoi les délais promis par M. Hamdorf peuvent être strictement respectés : « Pour mes clients et moi-même, c'est un avantage non négligeable en termes de sécurité. »
Un prix fixe grâce à des coûts clairement définis
Ce dernier point est également valable en termes de calcul. Pour Daniel Hamdorf, la gestion est plus simple depuis que chaque pièce de construction (même aussi compliquée qu'une lucarne en chapeau de gendarme) est fabriquée automatiquement : « La production automatisée permet de planifier les temps d'usinage avec beaucoup plus de précision, et les détails compliqués sont plus clairement définis en termes de coûts. Aujourd'hui, nous résolvons les problèmes des pièces de construction complexes pendant la préparation du travail, pas sur la table de travail. En tant qu'entrepreneur, je profite pleinement de cette sécurité de calcul, tout comme mes clients auxquels je peux offrir un prix fixe pour mes produits. »
C'est un avantage concurrentiel particulièrement important dans les activités de sous-traitance, l'une des raisons pour lesquelles la menuiserie Hamdorf a connu une croissance considérable dans ce secteur d'activité depuis 2009.
Les petites entreprises qui considèrent la construction en bois comme un pilier professionnel sont les meilleurs clients de l'entreprise dans ce domaine. Toutes les deux semaines environ, l'un de ces clients vient visiter l'installation de production moderne. « La technique devient alors un véritable argument de marketing. Lorsqu'un client nous rend visite, il est convaincu : Il peut avoir une maison parfaitement étanche en un ou deux jours s'il achète tous les éléments chez moi. »
De cette manière, Daniel Hamdorf génère actuellement un pourcentage de chiffre d'affaires beaucoup plus élevé dans l'entreprise que sur le chantier. Dans l'ensemble, la part de la production de panneaux de bois est passée de 8 % en 2008 à 40 % actuellement.
« Rentable » aussi pour le personnel
L'investissement s'est aussi avéré « rentable » pour le personnel de la menuiserie : « Sur le chantier, ils sont plus motivés car le montage est plus rapide et moins problématique, même avec les pièces de construction complexes, grâce à une plus grande précision et un niveau de préfabrication supérieur.
Même pour le personnel de la production, la vie est devenue plus facile parce que ces pièces, qui étaient un véritable casse-tête auparavant, traversent désormais l'installation sans aucun problème. »
Pour M. Hamdorf, lui-même ancien ouvrier dans la production d'éléments, c'était un effet secondaire recherché : « Je tenais à améliorer les conditions de travail dans mon entreprise grâce à la production automatisée. C'est pourquoi j'attachais beaucoup d'importance aux ventouses à panneaux, par exemple. »
L'environnement de travail s'est aussi amélioré dans la menuiserie Hamdorf. Lumineux et bien équipé, l'atelier de production de Fahrenkrug profite aujourd'hui non seulement au personnel mais aussi à l'entreprise elle-même. En période de pénurie de personnel, la tâche de M. Hamdorf est quelque peu facilitée, lorsqu'il est contraint de rechercher de nouveaux collaborateurs.
En outre, le maître charpentier voit un lien direct, à juste titre, entre la satisfaction du personnel et la qualité des pièces de construction : « Nous profitons également d'un lieu de travail favorable aux employés car c'est seulement avec un personnel motivé que nous pouvons produire durablement des produits de qualité exceptionnelle. » Un concept d'entreprise porteur d'avenir : L'atelier de production est déjà prêt pour de futurs agrandissements.
Source photos: Hamdorf
Exécution artisanale, fiabilité, qualité et conseil compétent forment la philosophie de la société Hamdorf. Nos halls de production ont un équipement moderne qui nous permet de nous adapter à vos souhaits. Notre entreprise artisanale dotée d'une production hightech forme une base évolutive pour vos exigences futures.
En tant que l'une des entreprises de charpentes leader dans le nord de l'Allemagne, nous employons 46 salariés qui réalisent un chiffre d'affaires d'env. 6,5 millions d'euros.
Website Hamdorf