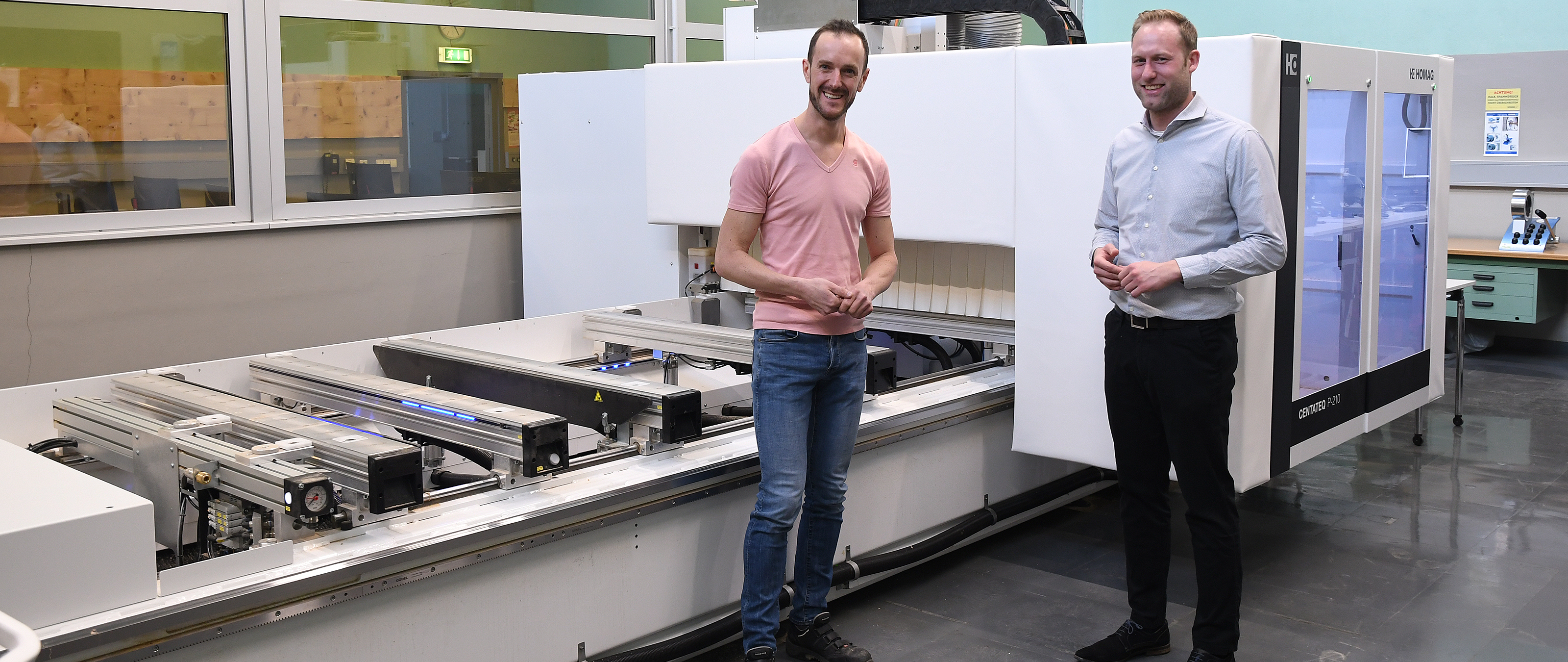
The Institute for Economic Promotion (WIFI) of the Upper Austrian Federal Economic Chamber sees itself as a partner of people and organizations that want to develop themselves further. Tens of thousands of people take advantage of the wide range of training courses offered each year. The reason for this success lies in a consistent practical approach. This is also demonstrated by a five-axis processing center from HOMAG, on which carpenters and master carpenters are trained.
In 2021, WIFI invested in HOMAG's "CENTATEQ P-210". An older five-axis machine had to be replaced, so WIFI wanted to take several steps forward with the new processing center. A whole range of requirements were therefore also on the agenda. In Linz, the machine pool of the wood technology department is generally equipped with high-quality machines. When thinking of the apprentices, those responsible try to keep the technology up to date at all times. Against this background, the configuration of the CENTATEQ was based on the general training structure at WIFI, while on the other hand, the special requirements of the wood technology department had to be met. The key points were flexibility and a wide range of processing, but above all, the safety of the operators and short distances when implementing projects. What does this actually mean in concrete terms? For this, the concept of WIFI must be understood.
From the economy, for the economy
WIFI Linz is a company that offers a broad portfolio of dual vocational training up to MBA level. The wood technology department offers courses with recognized qualifications, primarily skilled worker and master craftsman training courses, as well as special courses such as CAD, CNC or interior design courses, which certify the participants as experts. In 2020/2021, WIFI organized more than 9600 courses, seminars and training sessions attended by around 87,000 people. Priority is always given to the essential practical orientation of the learning content and methods. "We offer in-demand advanced training courses and therefore meet the demands of the economy, for the economy," emphasizes Christian Hintersteiner, head of the wood technology department. "Therefore, we don't have a fixed training plan; instead, we address what's needed at the present time. By constantly monitoring the market, we know where specific skilled workers are needed and offer corresponding courses."
In the wood technology department, for which Hintersteiner is responsible, carpenters, carpentry technicians and master carpenters are trained, as well as joiners, paintwork technicians, decorators, boatbuilders, model builders or flooring specialists. The aim here is also the qualification or further training with a certificate. According to Hintersteiner, the overall demand is big, even considerably bigger than the current training figures. "The shortage of skilled workers is acute, especially in medium-sized companies," he explains. "We are therefore called upon to provide several training courses and qualifications with a broad knowledge and skillset in the shortest possible time."
The component forge
Against this backdrop, it is easy to understand that a processing center in the wood technology department has to offer a wide range of processing options, and that it must combine high flexibility with the potential for complex processing operations. The five-axis capability of the machine was therefore never in any doubt for WIFI. HOMAG has fulfilled this central point with a "DRIVE5CS" spindle, which—with liquid cooling—provides 12 kW of power. The "V12/H4X2Y" drilling gear of the CENTATEQ works with 18 spindles, 12 of them in the vertical direction, four horizontally in the X direction and two horizontally in the Y direction. A groove saw with a diameter of 125 mm can also be used here, which can be swiveled from 0° to 90°. "A 14-part tool holder that travels piggyback in the X direction can also hold a saw blade up to 300 mm in diameter," reports Manuel Nöbauer, Account Manager Sales at Homag Austria. "The machine also has access to a linear changer with 10 tool slots that can provide a 350-mm blade." While the previous machine from a competitor was equipped with an automatic console table, the new concept uses a manual version. "This is because this table can meet the various requirements far better, especially as it is supported by a ceiling laser," explains Nöbauer. "Starting from the dual-circuit vacuum system of the table, the vacuum suction units can be positioned as required on the consoles, meaning that various parts can be securely clamped. The LED positioning aid ensures precise and fast setup." The ceiling laser projects the clamping equipment and workpiece contours, therefore enabling easy placement of the parts and maximum utilization. "In the training area especially, it is important that participants see the trimming contour and the contour of the suction units. That makes them feel secure in their work," emphasizes Hintersteiner. "The fact that many participants work on the CENTATEQ and execute a wide range of projects was the deciding factor for the manual console table with flexible suction unit positioning."
The dual-circuit vacuum allows the halves of the table to be controlled individually and enables shuttle operation between processing tasks. To ensure that the training sessions can be conducted in as quiet an atmosphere as possible, both vacuum pumps were set up in the basement below the machine. With a total performance of 130 m³/h, they are now also operated separately depending on the work task. Last but not least, the centrally lubricated machine was equipped with a swarf belt, which ensures that the offcuts and chips are transported away reliably.
Safety and short routes
A processing center that many people with different qualification levels work on must obviously meet specific safety requirements. This includes not only a barrier that performs this task mechanically at WIFI, but also precautions on the software side. "Effective collision control was therefore a matter of course for us," stresses the head of the department. This tool fits into a "woodWOP" full configuration, which includes in particular "woodMotion" for the simulation of five-axis processing and the CAM plug-in for the import of 3D models and the automatic generation of milling paths. WIFI can also use the software beyond the scope of generous school licenses — because vocational schools also work with woodWOP for final exams, training and exams are further aligned. "HOMAG delivers a very compact package," says Hintersteiner in summary. "The distances between the machine, software and tools are very short, which pays off especially in the school and exams."
A must for training
The results are regularly demonstrated in day-to-day business. "One of our most important courses is the one for master carpenters, which we use to prepare the participants as best we can for their exam," the department manager explains. Each participant has to produce a masterpiece with a defined level of difficulty, which is then checked by an approval committee and submitted. "Because every masterpiece has a CNC component, the CENTATEQ is absolutely essential when it comes to implementation," says Hintersteiner. However, CNC processing is also a must for the final exam. For example, the training program includes the carpentry technician with a focus on CNC, who produces a workpiece on the CENTATEQ as their exam work. When doing such work, skilled workers and master craftsmen have a lot of freedom. "They go to the CENTATEQ on their own and decide what they want to make. We don't put any obstacles in their way," says Hintersteiner, with a wink. "That's why we have the collision check. In the end, we just look over it again." In any case, the participants are quickly adept at handling the CENTATEQ because the training often involves working with HOMAG machines. The general "powertouch2" user interface would often already be familiar to them from other machines.
Short distances from programming to manufacturing, flexibility and safety during processing, software integration and the possibility of implementing even complex projects with a great level of independence — these are the core factors for WIFI in today's work with the CENTATEQ. With this profile, the CENTATEQ P-210 is now itself a forge for skilled workers in the forge for skilled workers.