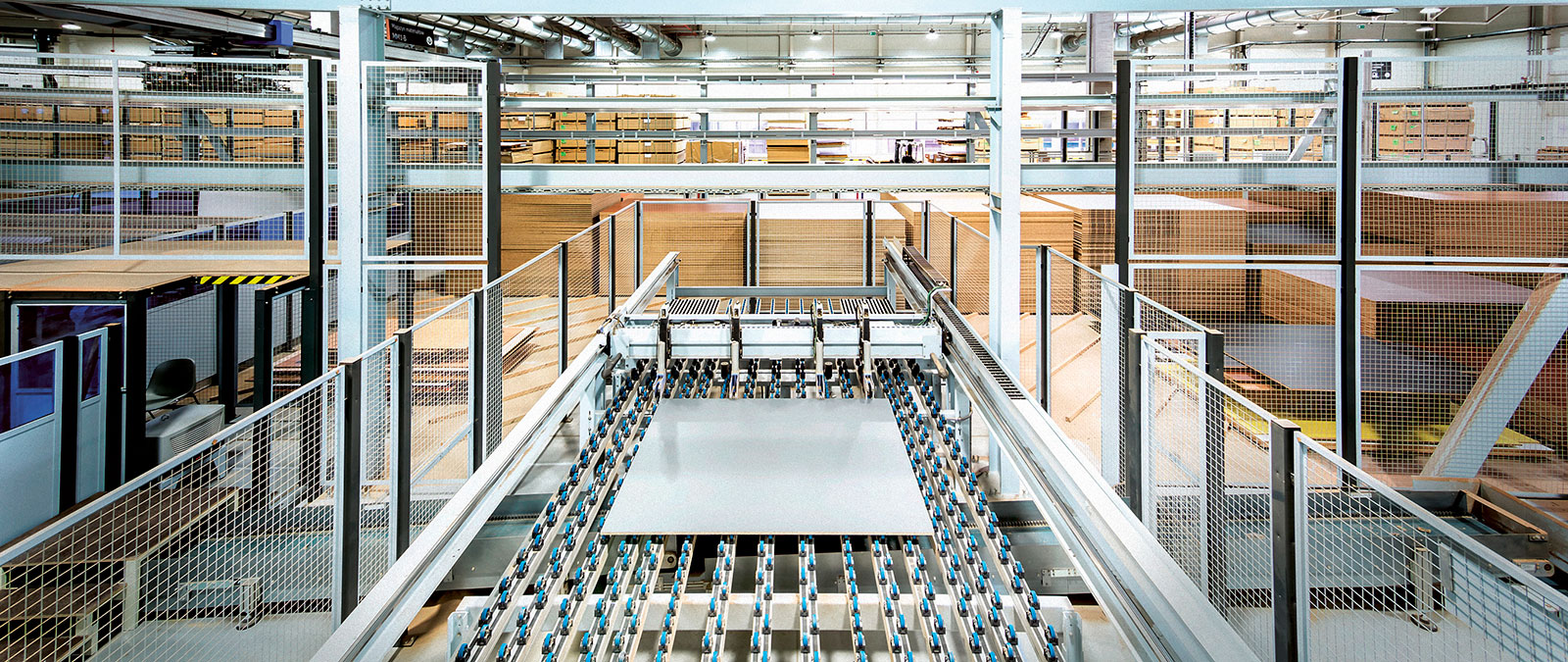
The networked factory not only has fully automatic operation, but is also set up for industrial production of customized items of furniture.
Jerzy Krzanowski’s favorite place is the steel platform from which he surveys the whole production hall. He sees his machines saw, drill and finish edges, and watches wooden parts glide along conveyor belts, disappear into processing stations and finally leave the hall as a table, shelf or cabinet. “Following the flow of parts from up here is fascinating,” says Krzanowski. The co-owner of the fourth largest furniture manufacturer in Europe is proud of his new factory. “I wouldn’t hesitate to use the HOMAG Group again to construct the plant.”
The production line in the 24,000 square meter hall is one of the most state-of-the-art furniture plants in the world. The machines are fully automatic, working with maximum precision and almost clinical cleanness. The employees hardly ever get their hands dirty any more. Their most important job is to oversee the operation.
Up to 4,000 furniture components leave the factory every shift. Usually every part looks different, which is known as batch size 1 production in the industry. The time when standard furniture always left the production line looking identical is over at last. Manufacturers now offer panels, boards and shelves in countless shapes, colors and sizes. Before, joiners would have had to manufacture these different units laboriously by hand. Today the high-end systems from the HOMAG Group produce them within a few minutes and with minimal setup times – for a fraction of the cost.
Sequence of steps
The first section of the plant in Jasło is a storage area in which many coated chipboard panels in different patterns are kept. Two crane bridges flit back and forth over the stacks. Like birds of prey, their vacuum grippers swoop down on the panels and move them around. What looks like a game is in fact perfect organization. The plant is networked and knows the production data. Therefore it knows which panels, and in which color, need to lie on top so that they can be moved into production at the right moment.
First of all a program calculates the best possible cut. A modern saw can cut several panels lying on top of one another in seconds. The individual panels are ideally separated out in another machine, which operates with a trimmer. This allows steps, corners and even zigzag patterns to be cut. Leftover panel parts are automatically gathered after cutting and brought back to the storage area. As soon as they are suitable for another piece of furniture, the intelligent control system sends them back into production.
After cutting, each part receives a sticker bearing a barcode – a kind of electronic name tag. All the subsequent machines in the line can now recognize the component and identify which item of furniture and customer order it belongs to. This is important because production here is carried out exclusively to order.
Read the full story in our "edge magazine " on page 12
Published in dds / november 2016. Editor: Georg Molinski.
Videos
Please confirm that when you use YouTube, data such as your IP address, browser identifier and similar may be transmitted to Google.
» Privacy Policy
Completely networked: Nowy Styl Group manufactures furniture with new batch size 1 plant from HOMAG
“Following the flow of parts from up here is fascinating. I wouldn’t hesitate to use the HOMAG Group again to construct the plant.”Jerzy Krzanowski, Nowy Styl Group Director