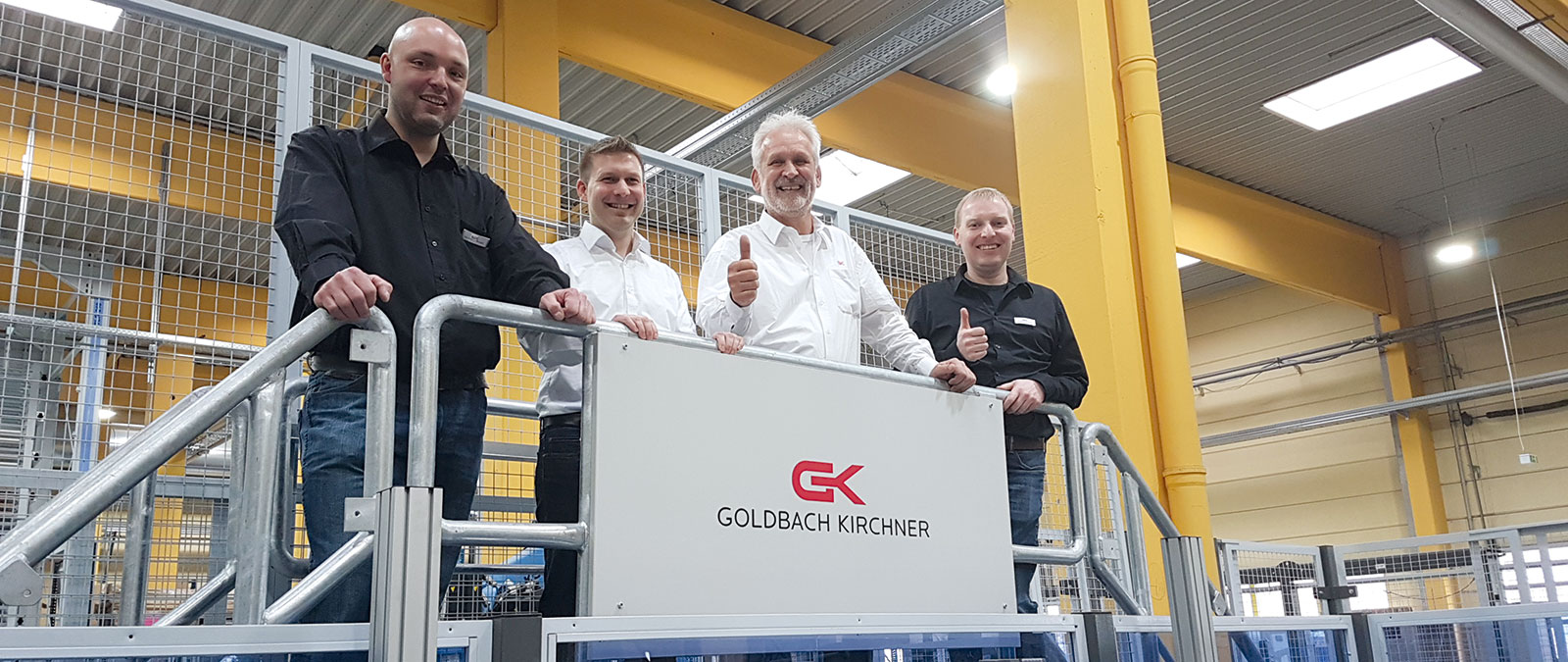
Необычный способ расширения мощностей выбрала специализирующаяся на производстве предметов отделки фирма Goldbach Kirchner Raumconcepte из Гайзельбаха: на территории старой мебельной фабрики в Дессау в сотрудничестве с HOMAG Group возникло высокоавтоматизированное, отвечающее требованиями Индустрии 4.0 производство корпусной мебели и прямоугольных мебельных элементов.
Goldbach Kirchner Raumconcepte GmbH — инновационное семейное предприятие, которым сейчас управляет уже третье поколение владельцев. Фирма из Нижней Франконии изготавливает высококачественные перегородки и встроенные шкафы, а также занимается серийным производством стандартной мебели и предметов отделки и придает большое значение собственным разработкам и поддержанию стандартов продукции made in Germany.
Несмотря на уважение владельцев к традициям, история предприятия изобилует примерами смелых решений уже начиная с основателя, Якоба Кирхнера, зарегистрировавшего патент на «складную лестницу» и начавшего в 1922 году успешное производство в Гайзельбахе.
Управляющий фирмой в настоящее время Бернд Кирхнер любит покой ничуть не больше. Он последовательно расширял свое предприятие, бывшее вначале просто крупной столярной мастерской, а в 2004 году решился на важный шаг, купив фирму Goldbach Raumconcepte GmbH из Гольдбаха, что вблизи Ашаффенбурга. В течение многих десятилетий фирма специализировалась на производстве встроенных шкафов, перегородок и мебели для офисов. В том же году Кирхнер перенес подразделения разработки и производства фирмы Goldbach в Гайзельбах.
Объединение усилий предприятий Kirchner Schreinerei Innenausbau GmbH и Goldbach Raumconcepte GmbH быстро привело к возникновению синергетического эффекта. В 2006 году слияние стало окончательным: возникло существующее по сей день общество с ограниченной ответственностью Goldbach Kirchner Raumconcepte GmbH с местонахождением в Гайзельбахе, занимающееся разработкой и производством высококачественных шкафов, перегородок и предметов внутренней отделки верхнего ценового сегмента для объектного строительства.
Новообразованная компания была нацелена только на рост и расширение. Результатом стало имеющее важное стратегическое значение приобретение: в 2015 году Бернд Кирхнер купил производственные площади в Дессау, вблизи здания знаменитой исторической Высшей школы строительства и художественного конструирования Баухаус.
«Мой знакомый, с которым мы вместе катались на лыжах, упомянул, что одно предприятие объявило о банкротстве и вся его территория теперь продается. Во времена ГДР там был мебельный комбинат, и позднее тоже занимались деревообработкой. Поэтому сначала мне пришло в голову, что там можно воспользоваться существующей инфраструктурой. Наконец я решился посмотреть на возможную покупку, но обнаружил, что организовать там производство будет не просто. Во-первых, из-за состояния здания, а во вторых — из-за сложившейся исторически низкоэффективной организации движения материалов — часть из них транспортировалась километровыми конвейерами — и сильно устаревшего оборудования», — рассказывает предприниматель.
Но г-н Кирхнер разглядел потенциал производственной площадки. «В Гайзельбахе у нас больше не было возможностей расширяться, а ситуация на рынке позволяла нарастить мощности и увеличить объемы производства. Поэтому я подумал об организации сетевого производства в Дессау».
Руководитель производства Себастиан Шмидт дополняет: «Идея состояла в том, чтобы проектировать изделия в Гайзельбахе и отправлять наборы данных для изготовления корпусной мебели и прямоугольных деталей в Дессау. А потом должно быть достаточно нажать кнопку, и высокоавтоматизированное оборудование с минимальным участием персонала изготавливает продукцию само».
Когда стало понятно, что один из цехов в Саксонии-Анхальте, который до недавнего времени использовался как склад, отвечает всем требованиям, г-н Кирхнер решился на приобретение. Всего через месяц после покупки земельного участка и зданий в апреле 2015 года на выставке LIGNA началось планирование новой производственной линии.
«Благодаря возможности планирования с чистого листа нам удалось создать производство, ориентированное на будущее. И выполнить все задачи, которые перед нами ставят индивидуальные заказы клиентов. Благодаря производству в Дессау мы одинаково успешно справляемся и с серийным производством, и с изготовлением единичной продукции, а также поддерживаем высокий уровень инноваций на нашем предприятии», — подчеркивает Кирхнер.
Крупный проект был реализован в сотрудничестве с HOMAG Group. «Компания Goldbach Kirchner сотрудничает с HOMAG еще с 1980 годов. Первым купленным тогда станком стала пила HOLZMA. При выборе оборудования для Дессау мы, разумеется, интересовались и другими производителями, но принять решение нас заставила по-настоящему инновационная концепция HOMAG, отвечающая всем нашим требованиям к станкам и программному обеспечению», — резюмирует Шмидт.
Обработка различных материалов — древесно-стружечных плит, МДФ, столярных плит, многослойных элементов и плит с меламиновым покрытием с защитной пленкой или без нее размером до 3320 x 2100 мм — начинается в системе штабельного хранения STORETEQ S-500 (TLF 411) длиной 50 и шириной 10 метров. Система хранения разделена на 40 мест складирования для плит 2800 x 2100 мм и восемь мест для плит 4100 x 2100 мм. Максимальная вместимость склада составляет примерно 5040 плит толщиной 19 мм каждая.
Станок для раскроя плит SAWTEQ B-300 (HPP 300) с устройством этикетирования с прижимной балкой соединен со складом, но не с основной производственной линией. При необходимости станок для раскроя можно использовать для изготовления заготовок нестандартных размеров.
Основной поток материалов проходит мимо этой пилы — робот портала склада загружает плиты в станок для раскроя SAWTEQ B-320 (HPS 320). На нем необработанные плиты разрезаются в соответствии с данными о детали; все перемещения заготовок, включая передачу для дальнейшей обработки и этикетирования, выполняются роботом. На этом участке за смену можно изготовить до 1500 деталей — в зависимости от схемы раскроя.
За SAWTEQ B-320 (HPS 320) располагается разделяющий буфер SORTEQ H-600 (TPL 220) с 20 ярусами и одновременной укладкой двух деталей. Особенно мелкие детали, размер которых не достигает 240 x 140 x 10 мм, перед буфером отсортировываются, поскольку их обработка на расположенных далее по линии станках невозможна. Также мы поступаем с остатками или уже готовыми заготовками, например, задними стенками.
«Нам была очень важна возможность при обходить при обработке определенные зоны станка и иметь доступ к некоторым точкам. Большинство заготовок проходят всю линию и все этапы обработки — начиная с плиты и заканчивая готовой деталью с кромкой и отверстиями. Но если один из станков оказывается неисправен, благодаря специальной схеме расположения оборудования нам не приходится останавливать всю линию. При большой загрузке и сжатых сроках поставок такая возможность становится «вопросом выживания». Для большей надежности еще на этапе планирования мы продумали ряд «худших из возможных» сценариев, например, случай отключения электроснабжения», — объясняет ответственный за площадку в Дессау руководитель производства Христиан Штоль.
За зоной накопления расположен кромкооблицовочный станок EDGETEQ S-800 (KFR 610) с устройством позиционирования LOOPTEQ C-500 (TFU 820); кромки на заготовки могут наноситься с одной или с нескольких сторон. Возможно приклеивание кромки полиуретановым клеем или с помощью лазера. Используются кромки из АБС, ПП и меламина, для обработки пазов станок снабжен двумя агрегатами типа SF 62.
Далее установлен двухъярусный транспортер, автоматически очищающий плиты с двух сторон. На этом производственном участке возможна укладка на промежуточное хранение мелких деталей. Отсюда заготовки перемещаются в сортировочный накопитель SORTEQ R-200 (TLB 320). При удвоенной глубине накопитель вмещает 1500 деталей и служит для сортировки заготовок с нанесенной кромкой. Если детали не требуют дальнейшей обработки, после накопителя они выгружаются роботом устройства укладки штабеля RKR 180. Также здесь загружаются детали, в которых необходимо проделать нестандартные отверстия.
При выгрузке робот автоматически формирует слои в соответствии с индивидуальными наборами данных, кроме того, он поворачивает детали для загрузки в сверлильный станок. Последнее устройство высокоавтоматизированной линии — проходной сверлильный станок DRILLTEQ L-500 (ABH 100). Здесь детали за один проход обрабатываются с шести сторон без «мешающих» контуров и автоматически устанавливаются дюбели вдоль оси X. Также здесь расположено устройство для 100-процентного измерения и накопитель для 30 готовых деталей.
Линия функционирует под управлением системы управления производством HOMAG ControllerMES. Система генерирует данные для различных элементов производственной линии, что дает возможность изготавливать продукцию с объемом партии, равным 1 изделию. В случае Goldbach Kirchner источником данных для дальнейшей обработки и передачи на производственное оборудование является программное обеспечение Kuhnle и CAD+T – ControllerMES.
Например, если отдел конструирования в Гайзельбахе указывает, что кромка из соображений дизайна должна наноситься вначале на поперечную сторону, а не на продольную, система учитывает это требование и правильное направление загрузки сохраняется на всех предшествующих этапах обработки.
В соответствии с полученными от ControllerMES данными пила самостоятельно определяет последовательность выполнения схем раскроя, а сверлильный станок сам запускает необходимую для работы с соответствующей деталью программу ЧПУ. В любое время возможно изготовление деталей ускоренной обработки. ControllerMES также реагирует на получение сообщений о неисправности, передаваемых автоматической системой контроля качества: система быстро блокирует все выполняемое задание.
Производство начинается за четыре дня до согласованной даты поставки мебели; перед этим выполняется анализ для оптимизации количества отходов при обработке обязательных и дополнительных заготовок. Склад работает практически непрерывно. Последовательность обработки плит определяется заранее заданной приоритетностью, учитываемой ControllerMES при управлении складом. Например, по вечерам выполняется автоматическая предварительная сортировка для выполнения заданий, запланированных на следующий день. Для подготовки к работе оптимизированные задания для склада отправляются из Гайзельбаха в Дессау каждые два часа.
Если для выполнения задания необходимо создать заготовки свободной формы, их производством занимается площадка в Гайзельбахе. Сказанное относится к изготовлению мебели сложной формы — подобные задачи на новой линии решаются с низкой эффективностью. «Где следует изготавливать детали для различных заказов, мы решаем в каждом случае индивидуально. Иногда имеет смысл изготавливать их даже непосредственно на строительной площадке», — говорит господин Шмидт.
Кроме HOMAG в поставках оборудования участвовало только одно предприятие — фирма Scheuch Ligno, специализирующаяся на системах аспирации, у которой была приобретена установка Sepas-Plus производительностью 80 000 кубических метров в час (для мебельного производства), Eta-max-Unit с мощными вентиляторами, КПД которых составляет 85 процентов, а также импульсный фильтр Scheuch-Ligno со встроенным накопителем стружки. Из импульсного фильтра стружка с производительностью 2800 килограммов в час перемещается в центральный накопитель пневматическим транспортером длиной 85 метров. Высокая эффективность расходования энергии обеспечивается при интервальном режиме работы.
Новая производственная линия HOMAG была введена в эксплуатацию в июне 2017, работа в нормальном режиме началась в октябре того же года. Средняя производительность линии — от 600 до 800 деталей в смену.
Максимальная эффективность оборудования еще не достигнута: «Если все настроить абсолютно точно, для обслуживания линии будет нужен всего один работник. Сейчас в цеху обычно присутствует трое. У нас есть и другие идеи. Например, мы планируем внедрить решение с использованием меток RFID вместо штрих-кодов. И нам хотелось бы установить системы с камерами для контроля оборудования и упрощения внутрипроизводственного технического обслуживания. Ясно одно: эта высокоавтоматизированная линия — последнее слово техники, и, вероятно, одна из самых современных в мире. Это воплощение идеи Индустрии 4.0. Поэтому сейчас мы ищем новых поставщиков. Пока только один производитель древесных плит поставляет нам материалы со штрих-кодами, которые считываются нашей установкой», — объясняет г-н Шмидт.
Кроме того, есть планы и по поводу использования имеющейся территории: «Позади цеха, который мы сейчас используем, есть свободное место. Например, там можно вписать здание для администрации и, возможно, современного шоу-рума», — говорит г-н Кирхнер.
Видеоролики
Please confirm that when you use YouTube, data such as your IP address, browser identifier and similar may be transmitted to Google.
» Политика конфиденциальности
Видео Goldbach Kirchner управляет одной из самых современных фабрик 4.0 в мебельной промышленности.