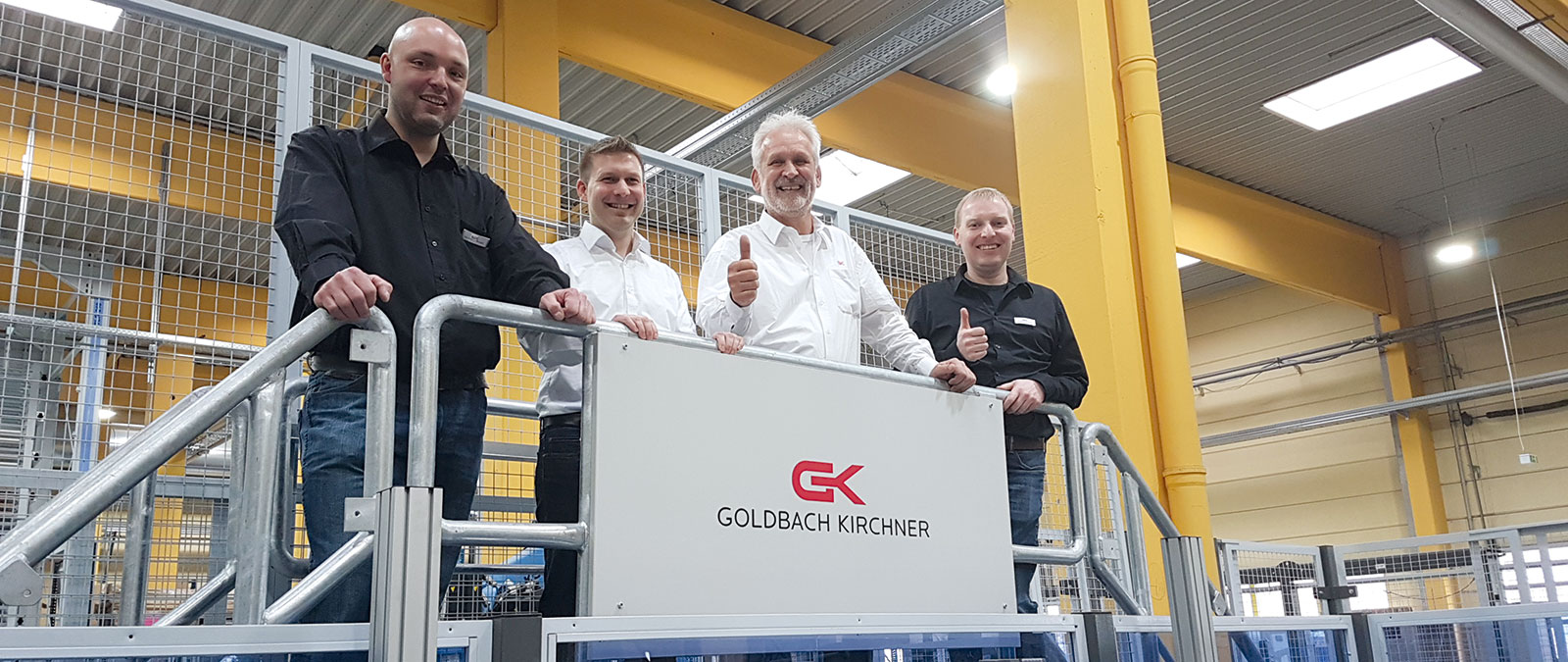
ガイゼルバッハを拠点とする内装業者の Goldbacher Kirchner Raumconcepte は、特別な方法で生産能力拡大に取り組みました。HOMAG Group と協力し、デッサウの古い家具工場の敷地に、収納家具と角型構成部品のための高度に自動化された生産設備をインダストリー 4.0 に従って建設したのです。
Goldbach Kirchner Raumconcepte GmbH は、家族経営で三代続く革新的な企業です。高品質のパーティションシステムやウォールシステム、バッチ生産、高級内装で名高く、持続可能な自社開発と国内生産を重視しています。
地に足の着いた経営を続ける同社ですが、これまで、大胆な意思決定を何度も行ってきました。創業者であるヤーコブ・キルヒナー氏は、1922 年に「Ruckzuck-Treppe(簡易式階段)」で特許を申請し、ガイゼルバッハで自社生産することで、成功の種を蒔きました。
今日の社長であるベルント・キルヒナー氏も引けを取らず活動的です。彼は、会社を徐々に大規模な製作所へと拡張し、2004 年にはアシャッフェンブルク近郊のゴルトバッハの Goldbach Raumconcepte GmbH を買収することで重要な一歩を踏み出しました。会社はそれまで数十年にわたってウォールシステムやパーティションシステム、オフィス家具の製造に専念してきましたが、キルヒナー氏は買収と同年のうちに Goldbach 製品の開発部門と製造部門をガイゼルバッハに移しました。
Kirchner Schreinerei Innenausbau GmbH と Goldbach Raumconcepte GmbH の提携は、ほどなく多数の事業分野で相乗効果を生み始めました。2006 年には完全に統合されました。2 つの企業が合体して今日の Goldbach Kirchner Raumconcepte GmbH が生まれ、ガイゼルバッハを拠点に高品質のウォールシステム、パーティションシステム、高級内装の開発と製造を行うようになりました。
これで、強力な内装業者である同社にとって、成長への道が大きく開かれました。2015 年には、戦略的に重要な次の一歩を踏み出しました。ベルント・キルヒナー氏が、デッサウの由緒あるバウハウスの近くに生産施設用の敷地を購入したのです。
「一緒にスキーに行った知人が、デッサウの会社が倒産して敷地を売りに出しているという話をしました。東独時代には国営の家具工場があり、その後も木材加工が行われていた場所です。だから当然、既存の構造を利用できるのでは、と思いました。しばらくして実際に見学に行くことになったのですが、その地で生産を行うのはそう簡単ではことがわかりました。建物の状態が良くなかったし、コンセプトなしで継ぎ足していった数キロにわたるローラコンベアが効率悪く材料を流していて、機械もとても古いものばかりだったのです。」とキルヒナー氏は言います。
それでも、キルヒナー氏はそれらの資産に潜在的な価値を見出しました。「ガイゼルバッハではもう拡大の余地がないのですが、市場の状況を見れば、生産量を増やせれば成長できることが明らかでした。それで、高度にネットワーク化した生産設備をデッサウに作ろうと考えたのです。」
製造部長のセバスチャン・シュミット氏は言います。「ガイゼルバッハで製品企画を行った後、収納家具と角型構成部品のデータレコードのみをデッサウに送る、という構想です。そしてボタンを押せば、高度に自動化されたデッサウの設備が最小限の人員投入で部品を製造する、というわけです。」
デッサウにあった比較的新しい建物のうち、倉庫として使われていた建物が必要条件を満たしていることがわかり、キルヒナー氏は購入に踏み切りました。2015 年 4 月に敷地と建物を購入してから 1 ヶ月後、見本市のLIGNAで新しい製造ラインの計画が始まりました。
「まっさらな状態だったからこそ、未来志向の生産設備を実現することができました。それぞれの顧客の依頼に合わせて生産ができる設備です。デッサウの生産設備のおかげで、私たちはバッチ生産も単品生産も効率的にこなし、真に革新的なメーカーになるという願いをかなえたのです。」とキルヒナー氏は言います。
この大規模プロジェクトは、最終的に HOMAG Group と共同で実現されました。「Goldbach Kirchner は 1980 年代から HOMAG と協力関係を築いています。当時、初めて導入した機械が HOLZMA の鋸でした。デッサウの設備のために、もちろん他のメーカーも検討したのですが、最終的にはやはり HOMAG の性能の良さや、機械とソフトウェアに対する当社のニーズをすべて満たす真に革新的な設備コンセプトが決め手となりました。」とシュミット氏は言います。
投入材料(パーティクルボード、MDF、合板、複合材料、保護フィルム付き/なしのメラミン化粧板、最大 3,320 x 2,100 ミリの原板)の加工は、長さ約 50 メートル、幅 10 メートルの平面倉庫システムSTORETEQ S-500 (TLF 411)から始まります。このシステムは、2,800 x 2,100 ミリの保管スロット 40 個、4,100 x 2,100 ミリの保管スロット 8 個で構成されます。この平面倉庫システムの最大容量は、厚さ 19 ミリの部材にして約 5,040 枚です。
倉庫システムに接続されていながら、全体の製造ラインには属さないのが押さえビームラベリング装置付きパネルソーSAWTEQ B-300 (HPP 300)です。このパネルソーは、必要に応じて個別のカットに使用できます。
倉庫システムのポータルは、ロボットを使ったパネルソーSAWTEQ B-320 (HPS 320)の部材送りを利用するため、実際の部材フローはSAWTEQ B-300 (HPP 300)を通りません。SAWTEQ B-320 (HPS 320)では部材データに従って原板が切断されますが、その際、ラベリングや加工後の送りも含めた全処理をロボットが行います。この設備部分では、構成によってはシフトあたり最大 1,500 個の部品が生産されます。
SAWTEQ B-320 (HPS 320)の次には、20 層、2 レーン入庫式の分離バッファSORTEQ H-600 (TPL 220)が待っています。同時に、後続の機械エリアで加工できない、サイズが 240 x 140 x 10 ミリを下回る小部品をバッファの手前で振り落とすことができます。残材や、すでに完成した部材(背板など)も同様に扱われます。
「私たちが重視したのは、緊急時に特定の機械エリアを回避できること、複数の場所でアクセスが可能なことです。部品は通常、原板からエッジや穴を含めて完成した部品まで、全工程を通過します。しかし、ある機械に異常が発生した場合、特殊なシーケンス計画によってライン全体が停止するのを防ぎます。これは、作業負荷や納期によっては非常に重要になります。万全を期すため、設備計画の時点ですでに、停電なども含めたワーストケースシナリオを想定しました。」とデッサウの工場長、クリスチャン・シュトル氏は言います。
バッファ場所の次に、エッジバンダー EDGETEQ S-800 (KFR 610)と部材サーキュレーションシステム LOOPTEQ C-500 (TFU 820)が続き、必要に応じて部材のいくつかのエッジを加工します。ここでは、PU またはレーザーによる部材とエッジの接合が行われます。ABS、PP、メラミンエッジが使用され、溝加工用にSF 62タイプのユニット 2 台が装備されています。
その後、パネル両面の自動クリーニング機能を備えた 2 面の部材搬送機が続きます。この部分にも、小規模なバッファが用意されています。そこから、仕分け保管システムSORTEQ R-200 (TLB 320)へと続きます。この設備部分は、入庫レーンの深さが 2 倍になっているため、エッジ加工が完了した部材を約 1,500 個も挿入し、仕分けすることができます。すべての加工作業が終了している部材は、ロボットを使ってデスタッキングシステムRKR 180に送られます。特殊なドリル加工を必要とする部材もここに装入できます。
ロボットは、デスタッキングと同時に、個々のデータレコードに従って自動で層を形成し、ドリル加工に備えて部材を回転させます。高度に自動化された設備の最後に待ち受けるのが、ドリル加工機DRILLTEQ L-500 (ABH 100)です。ここでは、1 つのサイクルで 6 面すべてが干渉輪郭なしで加工され、X 方向での自動ダボ打ちが行われます。さらに、100 % の測定と 30 個分の完成部品バッファがあります。
設備全体の基礎にあるのは、HOMAG 製造制御システムControllerMESです。この設備部分は、個々の設備構成部品のためにデータを生成することで、単品生産を可能にします。Goldbach Kirchner の部材情報は、Kuhnle のソフトウェアと CAD+T が生成し、ControllerMESが製造に向けてデータを準備します。
ガイゼルバッハの設計部門が、たとえばデザイン上の理由でまず横方向のエッジを取り付けてから縦方向のエッジを取り付けると決定した場合、それがシステムによって考慮され、設備全体がそれに合わせて部材を加工・搬送します。
ControllerMESから提供されたデータに従う形で、鋸が切断図面を処理し、ドリル加工装置が個々の構成部品に必要な CNC プログラムを呼び出します。クイックパーツの製造もいつでも可能です。自動品質検査によってエラーメッセージが発生した場合でも、ControllerMESが反応し、すぐにジョブ全体を中断します。
家具の納期の 4 日前が製造開始時点となり、その前に必須部材とオプション部材の残材最適化が行われます。倉庫システムはほぼ休みなしで作動します。どのパネルが優先されるかは、事前に指定された優先順位によって決まり、これを保管制御の際にControllerMESが考慮します。それにより、たとえば夜間に、次の日の製造開始に向けた仕分けが自動的に行われます。2 時間おきに、ガイゼルバッハの作業準備部門によって最適化されたジョブがデッサウの倉庫システムに送られます。
あるジョブで自由形状部品が必要な場合は、製造はガイゼルバッハで行われます。新しい設備では効率良く生産できないような複雑な家具についても同様です。「社内での運搬は定期的に行っていて、ジョブによって部品をどこに集めるかを決定します。建設現場に直接運ぶ場合もあります。」とシュミット氏は言います。
新しい生産設備を整えるにあたって、HOMAG の他に唯一、協力を依頼したメーカーが吸塵機専門メーカーの Scheuch Ligno です。同社が納品した「Sepas-Plus」システムは、家具製造における吸塵性能が時間あたり 80,000 立方メートルあります。高性能ベンチレーターを備え、効率 85 パーセントを誇る「Eta-max-Unit」、チップバンカー内蔵の Scheuch-Ligno インパルスフィルターも同社の製品です。インパルスフィルターから中央チップサイロまでの空気圧搬送システムは、約 85 メートルの距離を運び、1 時間あたり 2,800 キロの搬送性能を誇ります。エネルギー効率の高いインターバル方式が特長です。
新しい HOMAG 生産設備は、2017 年 6 月に稼動を開始し、2017 年 10 月に通常操業レベルに達しました。平均的な能力は、シフトあたりの構成部品数にして 600~800 個です。
しかし、今日もまだ、最大効率を高める努力がなされています。「現在、現場には 3 人以上の従業員がいますが、すべてがスムーズに進むようになれば 1 人の従業員で設備全体を動かせるようになります。その他にも、さまざまなアイデアが出ています。たとえば、バーコードの代わりに RFID ソリューションを使用することも検討しています。また、いつか優れたカメラシステムを現場に設置して、設備を監視し、工場内でのメンテナンスを単純化したいと考えています。一つはっきりしていることは、これが最新の設備であること、このように高度に自動化された形ではおそらく世界最新の設備の一つであることです。インダストリー 4.0 のコンセプトを体現した設備と言えます。そのため、他のサプライヤーも組み入れたいと考えています。現在は、1 軒の木材メーカーが、当社の設備で読み取れるバーコードを付けてパネルを納入している状態です。」とシュミット氏は説明します。
また、敷地に関しても計画があります。「現在使用している生産施設の裏は緑地なのですが、たとえば新しい事務所や最新型のショールームを建てるには十分なスペースです。」とキルヒナー氏は言います。
ビデオ
Please confirm that when you use YouTube, data such as your IP address, browser identifier and similar may be transmitted to Google.
» 個人情報保護
ビデオ:Goldbach Kirchnerは、家具業界で最新のIndustry4.0を工場の1つです。