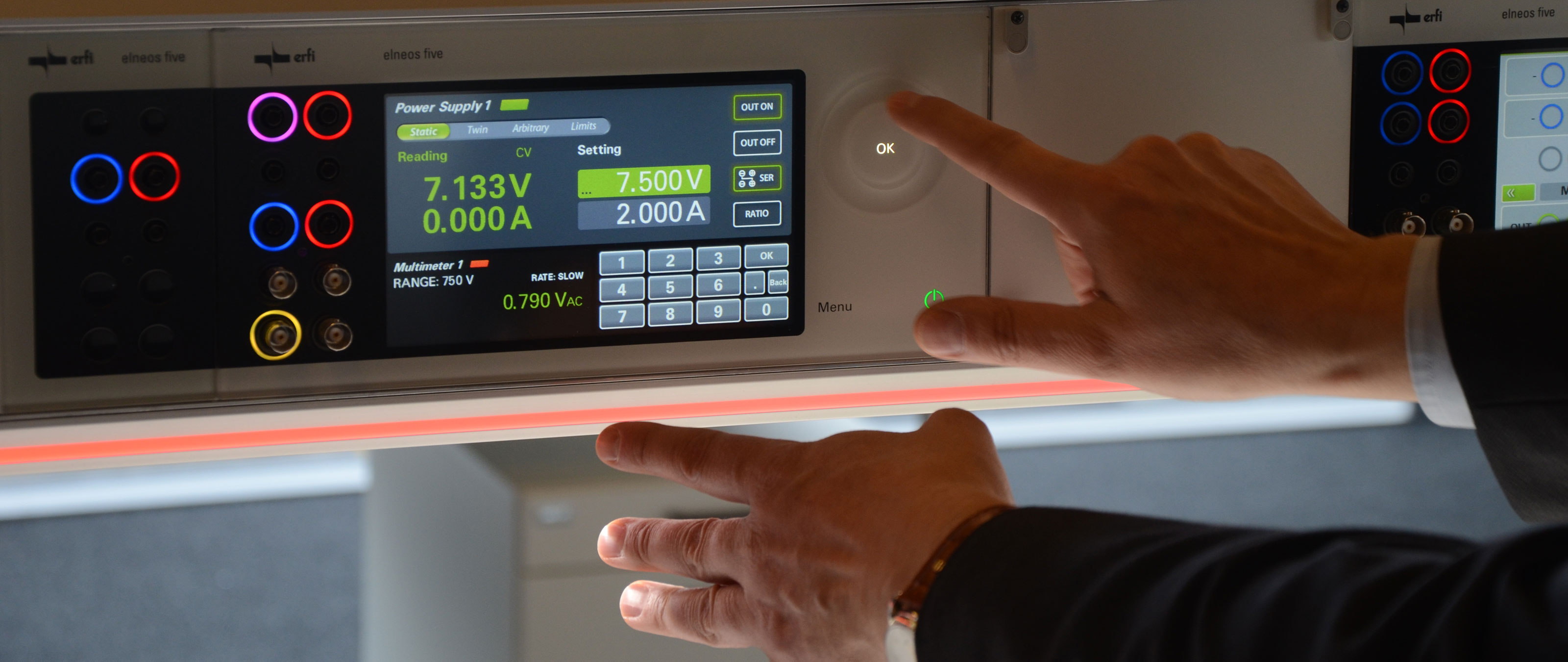
Inizialmente bisognava sostituire solo una bordatrice e installare un nuovo software. Ma già durante la fase di pianificazione, era chiaro che c’era molto di più da fare. Per questo motivo, i responsabili della Ernst Fischer GmbH (Erfi) hanno scelto la soluzione completa. Oggi, tutti i componenti in legno dei tavoli da lavoro e degli scaffali prodotti dagli specialisti dell’elettronica di Freudenstadt sono il risultato di una linea di produzione automatizzata di HOMAG. Un impianto che soddisfa tutti i criteri di Industria 4.0 e che presto avrà anche una predisposizione per la piattaforma digitale tapio.
„Dovevamo fare qualcosa”, così Andreas Fischer, vice responsabile di Erfi, descrive la situazione della produzione di legno nella sua azienda, una situazione che vedeva coinvolte macchine ad azionamento manuale. “Non eravamo più in grado di rispettare la produzione di un numero troppo elevato di varianti e né di sostenere la sempre più pressante richiesta di produzione lotto 1 e in serie”. La ditta produttrice di arredi tecnici da laboratorio, postazioni da lavoro, strumenti di prova e di misura, nonché di sistemi di test si è avvalsa al 100% della consulenza HOMAG e ha adottato la più moderna delle tecnologie delle macchine, una tecnologia che diventa sempre più necessario avere. A Freudenstadt è stato fatto un salto nel futuro: si è passati dalla singola macchina ad un impianto concatenato, e tutto ciò avvalendosi delle applicazioni e dei software di Industria 4.0.
Le macchine dell’impianto concatenato sono state installate in un capannone predisposto. Che si tratta di una produzione caratterizzata da un alto livello di automazione, lo si capisce subito dal flusso automatico dei pezzi. All’inizio della produzione c’è il taglio dei pannelli, realizzato da una sezionatrice di pannelli, la SAWTEQ B-300 (HPP 300 profiLine), con il suo magazzino orizzontale STORETEQ S-500 (TLF 411). La sezionatrice è dotata di una sporgenza lama di 95 mm ed è in grado di dividere pannelli singoli e pacchetti. Per questo, risulta conveniente anche per grandi quantità di tagli. Altre opzioni permettono di aumentare la potenza e la protezione dei materiali. Un’etichettatrice per superfici etichetta il pannello grezzo. Questa operazione accelera ulteriormente il taglio. Ogni pezzo tagliato riceve dalla stampante di etichette un codice a barre adesivo, che ne permette l’identificazione durante tutto il processo, dal taglio al montaggio. Tra le fasi di taglio e incollaggio dei bordi, i pezzi vengono collocati nel polmone di smistamento SORTEQ R-200 (TLB 321), che dispone di una capacità di stoccaggio che raggiunge i 1200 pezzi di diversa grandezza.
L’incollaggio dei bordi avviene tramite una bordatrice estremamente flessibile, la quale realizza bordi a giunzione “0” per la produzione lotto 1 con laserTec – Next Generation. In questo impianto per una produzione flessibile viene utilizzata la bordatrice monolato EDGETEQ S-810 (K 610). La lavorazione plurilaterale, che avviene in successione, raggiunge un’elevata capacità anche nella produzione su commissione che richiede continui cambiamenti di dimensioni. Un altro elemento all’avanguardia della tecnica è il riattrezzaggio rapido tra due pezzi in un intervallo ancora più breve. Grazie al sistema di alimentazione dei pezzi, questi ultimi vengono trasportati, con misure e angoli precisi, in direzione longitudinale e trasversale. In abbinamento al gruppo di rettifica Power, dotato di attrezzi idraulici per la lavorazione del pezzo estremamente precisa e senza scheggiature, si crea una squadratura perfetta in esercizio continuo. Il gruppo di incollaggio è in grado di lavorare dodici diversi angoli in sostituzione automatica, senza l’intervento manuale. Il gruppo laser con tecnologia ai diodi ha un’efficienza energetica migliore. La sua installazione è molto semplice e, in confronto al gruppo laser precedente, è molto più robusto e con un’impronta più piccola. Per soddisfare le esigenze di un’ottima resistenza a caldo e umidità, la macchina offre anche la possibilità di incollare i bordi con PU.
Il ritorno pezzi con portale girevole integrato determina un flusso di materiale concatenato dalle alte prestazioni. I pezzi pronti e già lavorati vengono automaticamente separati: tutti i pezzi rettangolari e senza lavorazione a forma libera tornano al polmone di smistamento, prima di essere trasportati, per un’ulteriore lavorazione automatica, al centro di lavoro DRILLTEQ H-600 (BHX 560) per la foratura e la fresatura in continuo. I pezzi lavorati a forma libera, invece, vengono accatastati sul bordo e trasportati all’isola CNC a gestione robotizzata per un’ulteriore lavorazione.
Il componente principale dell’isola CNC è il centro di lavoro CENTATEQ P-500 (BMG 512). Questo ha una struttura modulare che può essere personalizzata in base alle esigenze e alle richieste del cliente. I responsabili della produzione di Erfi hanno creato il loro BMG per ottenere la massima flessibilità. Per questo è stato scelto il mandrino a fresare Drive-5C+, un mandrino a 5 assi. La flessibilità del centro di lavoro viene messa in risalto dal tavolo a traverse, che garantisce una movimentazione semplice tramite le traverse, con guide lineari estremamente precise e guide di introduzione robuste con due cilindri pneumatici e dall’ “Unità di lavorazione multipla” di foratura con un’inclinazione a 360 gradi, che rende possibile utilizzare il mandrino in ogni angolatura. Ciò vale anche per il dispositivo cambia utensili a catena, il quale grazie a 72 posizioni e tempi di sostituzione brevi, è alla base dell’impiego flessibile di un alto numero di utensili e gruppi. Se per l’incollaggio dei bordi ai pezzi sagomati sia stato scelto il sistema „laserTec“, lo si deve alla necessità di disporre sia di bordi dritti sia curvi della stessa qualità. Questo avrebbe determinato tempi di lavorazione molto più lunghi. Per questo motivo si è deciso di ricorrere al robot industriale a 5 assi. In questo modo, l’operatore può lavorare parallelamente su diverse postazioni.
Il robot salta subito all’occhio del visitatore della linea di produzione Erfi. È l’indizio chiaro di una produzione automatizzata. Infatti l’automazione inizia molto prima; di fatto, inizia già quando nell’ufficio di produzione vengono congiunti i dati specifici dell’ordine con i dati dal sistema CAD/CAM e dalla gestione degli elenchi dei pezzi. Mediante il sistema superiore di produzione ControllerMES di HOMAG, si formano infine i programmi CNC e i dati di produzione di ciascun pezzo, che vengono poi inviati alla macchina prima che inizi il processo di lavorazione. A questo punto, “viene data vita” a ciascun pezzo, ovvero ogni pezzo riceve un numero di identificazione che lo accompagnerà fino al montaggio finale. “Con il sistema superiore di produzione ControllerMES di HOMAG, abbiamo a disposizione una piattaforma con un processo di produzione perfettamente organizzato. In questo modo si perfeziona l’interazione macchina-postazione di lavoro manuale”. Così Peter Bitzer, esperto IT e amministratore di sistema in Erfi, descrive le nuove possibilità tecniche.
“Grazie al sistema modulare, il processo in Erfi viene supportato in modo sostenibile: a partire dalla configurazione intelligente e dall’ottimizzazione dei dati di produzione, attraverso la pianificazione della produzione per arrivare a un controllo completo della produzione dopo il montaggio finale”, completa Harald Sieber, Senior Sales Manager in HOMAG Systems. “Il software crea così le condizioni preliminari per la produzione su commissione di vari prodotti all’interno di una produzione connessa”. Allo stesso tempo, rende la produzione trasparente. Per ogni pezzo di ogni ordine c’è una risposta: l’avanzamento di produzione è chiaro in ogni momento. In questo modo, è possibile controllare e orientare meglio la produzione. Le situazioni problematiche vengono riconosciute immediatamente. In caso di problemi, grazie al codice a barre del pezzo, è possibile attivare subito una nuova produzione senza correre il rischio di rilevare la mancanza del pezzo durante il montaggio. Una funzione del sistema ControllerMES è la possibilità di riepilogo degli ordini di produzione. “Grazie a questa funzione, tagliando i “pezzi necessari” degli ordini attuali, possiamo tagliare subito anche i cosiddetti “pezzi possibili”, ottenendo così uno schema di taglio che ottimizza la produzione e riduce gli scarti”, afferma Peter Bitzer in questa spiegazione che lui definisce un vantaggio.
Tutto ciò non si può riassumere semplicemente con il termine “redditività”, perché l’installazione di ControllerMES è un investimento per il futuro. Piuttosto si può parlare di aumento della produttività, in quanto elementi come il consumo di materiale, i tempi di fermo, le attività inutili e i tempi di lavoro sono ridotti al minimo. Trattandosi di un software standard modulare, il sistema è configurabile in modo flessibile, ampliabile e adattabile a nuovi processi con una possibilità di aggiornamento del 100%. Ed esattamente questo avevano in mente i responsabili di Erfi: volevano utilizzare il sistema superiore di produzione ControllerMES anche per la realizzazione di pezzi di acquisto e di elettronica. Poiché l’impianto è collegato a tapio, la prima piattaforma digitale al mondo per l’industria del legno (vedere HK edizione 6/17), è possibile richiedere la visualizzazione dello stato attuale di una macchina, di un possibile errore o la segnalazione di un guasto sul proprio smartphone grazie all’app MachineBoard. Ma il sistema è anche attivo, ovvero invia allo smartphone dell’operatore avvisi importanti, che rilevano ad esempio possibili guasti. È chiaro, quindi, come Erfi anche sotto questo aspetto si stia muovendo seguendo i criteri di Industria 4.0.
Un articolo del magazzino del settore HK, 01/2018. Fonte materiale illustrativo: Rivista HK. Leggete qui l’articolo sul sito hk-magazin.com.
Videos
Ti preghiamo di confermare che quando utilizzi YouTube, dati come il tuo indirizzo IP, l'identificatore del browser e simili potrebbero essere trasmessi a Google.
» Tutela della privacy
Industry 4.0 at erfi Ernst Fischer GmbH