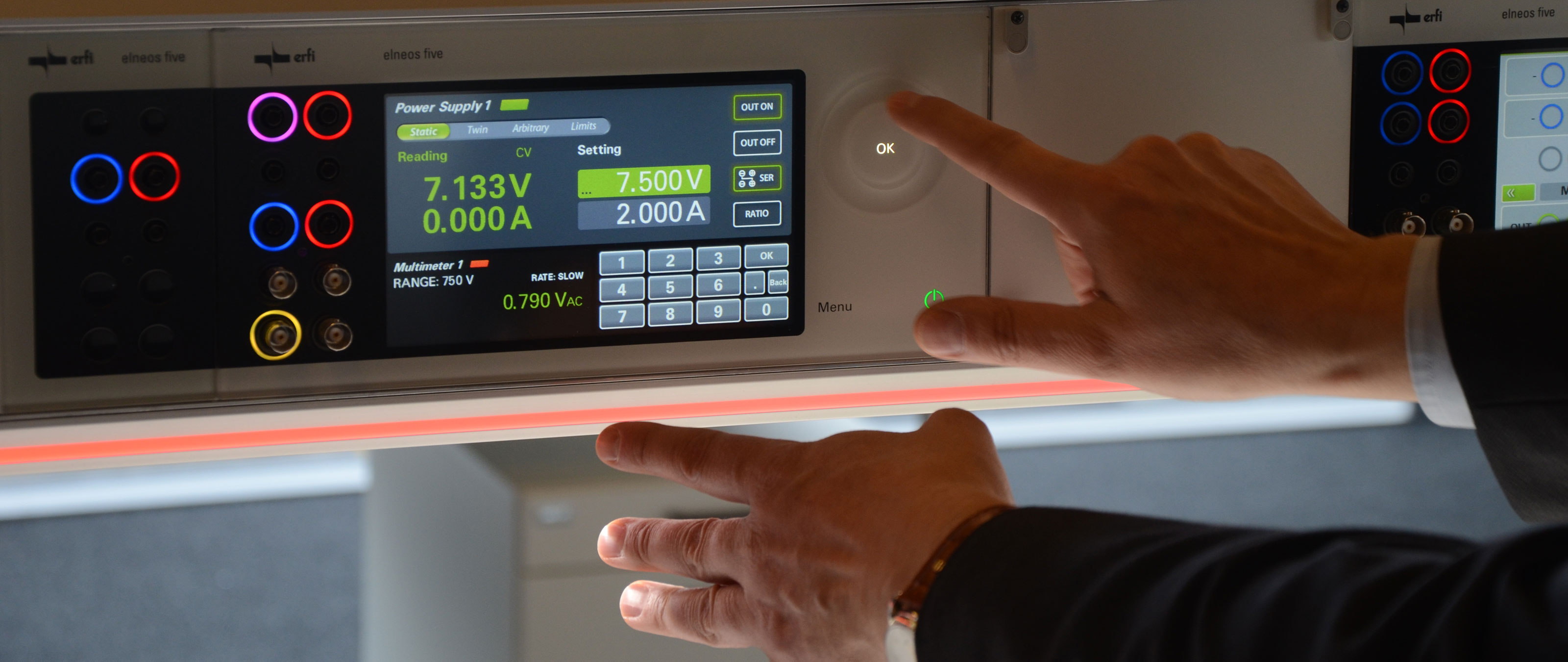
本当は古いエッジバンダーを交換し、新しいソフトウェアをインストールするだけのはずでした。しかし、すでに計画段階で、それでは足りないことが判明したのです。そこでフロイデンシュタットを本拠とする電子機器メーカー、Ernst Fischer GmbH(Erfi)の幹部は、完全ソリューションの導入に踏み切りました。現在では、同社の作業台やシェルフの木材部品はすべて HOMAG の自動製造ラインで生産されています。インダストリー 4.0 の基準をすべて満たし、近々 tapio にも対応する予定の設備です。
Erfi の若社長、アンドレアス・フィッシャーは、木材機械を手動操作していた同社の製造過程について「何かしなければと思っていました」と言います。「市場では、多様なバリアントや、単品生産から大量生産までの柔軟な製造方式が求められ、経済面でそれについて行くことができなくなっていたのです」。電子実験設備、組立作業場、測定・点検機器、テストシステムを製造する同社は、HOMAG によるアドバイスを 100 パーセント実施し、現在入手できる範囲で最新の機械技術を導入しました。同社では、独立した機械から連結された設備へと、インダストリー 4.0 の特徴とソフトウェアアプリケーションのすべてを揃えた大きな一歩を踏み出しました。
連結された設備のための機械群は、既存の工場に最適に配置することができました。これが高度に自動化された製造プロセスであることは、自動化された部材のフローを見ればわかります。工程の最初にパネル切断が行われますが、これはパネルソーSAWTEQ B-300 (HPP 300 profiLine)とその手前の平面倉庫システムSTORETEQ S-500 (TLF 411)が処理します。このパネルソーは、鋸刃突出量が 95 mm で、個々のパネルだけでなくパッケージも分割できます。それにより、個数が多い場合でも経済的な切断が可能です。その他にも、性能や材料の扱いを向上させるオプションが用意されています。鋸の手前で表面ラベリング装置が原板をラベリングするため、切断がさらに加速します。切断部品のひとつひとつにバーコードシールが貼られ、切断から組立までに使用する部品を識別できます。切断と縁貼りの間に、切断された部品はまず仕分けバッファSORTEQ R-200 (TLB 321)に配置されます。このバッファは、異なるサイズの部品を最大 1,200 個収容できます。
縁貼りは、高度に柔軟なエッジセルを使って行われ、「laserTec – Next Generation」により単品生産でもゼロジョイントエッジが実現されます。ここでは、柔軟な加工を行うために片側エッジバンダーEDGETEQ S-810 (K 610)が採用されています。寸法が頻繁に変わる注文ベースの加工で連続加工により複数辺を加工した場合も、高い生産能力を発揮します。2 つの部材の間の非常に短い隙間でもユニットの装備を変更できます。部材は、部材送りシステムにより、縦方向または横方向に正確な寸法、正確な角度で供給されます。油圧式ツールを装備したパワー継ぎ目ルーターが精密で剥がれやまくれのない部材加工を可能にし、サイクルにおける正確なフォーマット加工を実現します。接着部は、自動切替えにより手動介入なしで 12 種類のエッジを処理できます。最新のダイオードテクノロジーを採用したレーザーユニットは、最大性能を発揮しますが、構造が単純なため旧型のレーザーユニットに比べて堅牢で、場所を取りません。さらに、熱や湿気に対する耐性を高めるために PU で縁貼りすることも可能です。
回転ポータルを内蔵した自動リターンコンベア装置が、高出力で連結された材料フローを達成します。完成した部材は、自動的に分離されます。自由形状加工を行わない角型部品は、まず仕分けバッファへと戻り、ドリル加工とルーター加工に備えて加工センターDRILLTEQ H-600 (BHX 560)に搬送されます。自由形状加工が必要な部品は、出口で積み重ねられ、ロボットハンドリングを装備した CNC セルに送られます。
CNC セルの中核を成す加工センターCENTATEQ P-500 (BMG 512)は、モジュール構造になっていて、顧客のニーズやリクエストに合わせて構成できます。Erfi の加工責任者は、BMGで最高の柔軟性を目指しました。そのため、ルータースピンドルには、5 軸ルータースピンドルのDrive-5C+が選ばれました。加工センターの柔軟性の高さは、コンソールテーブルにも現れています。このコンソールテーブルは、精密なリニアガイドと 2 本の空圧式シリンダを使った堅牢な配置支援を備えたコンソールにより操作が簡易化されており、ドリル加工ユニット「Multi-Processing-Unit」は、360 度旋回式ですべてのスピンドルを任意の角度に設定できます。チェーンツールチェンジャも同様に、72 のスロットと、トランスポーザーによるすばやい交換が、多数のツールやユニットを柔軟に投入するための基盤となっています。成型部品の縁貼りにもlaserTecシステムが採用されたのは、直線のエッジと曲線のエッジを同レベルの品質で加工するためです。ここでの加工時間は大幅に長くなるため、部品ハンドリングを 5 軸産業用ロボットに任せることにしました。オペレータは、別の場所で並行して作業することができます。
ロボットは、Erfi の生産設備を訪れた訪問者の目を引きます。加工の自動化を目に見える形で象徴する存在だからです。しかし自動化は、もっと前の時点で始まっています。生産準備段階で、ジョブごとのデータに CAD/CAM システムのデータ、部材リスト管理のデータを組み合わせた時点で始まるのです。HOMAG の製造制御システムControllerMESを通じて各部品のための CNC プログラムと加工データが生成され、それが時間のフローと共に機械に転送されます。ここで、各部品に最終組立まで有効な一意の識別番号が割り当てられ、「息が吹き込まれ」ます。「HOMAG の製造制御システムControllerMESは、製造プロセスを最適に構成し、機械と手作業の連携を完璧にするためのプラットフォームです」と、Erfi の IT システム管理者であるペーター・ビッツァー氏は新しい技術的可能性を説明します。
「このモジュール構造のシステムは、Erfi のプロセスを、インテリジェントなコンフィギュレーションと生産データの最適化から、生産計画、最終組立後の完全性検査まで、持続的にサポートします」と、HOMAG Systems の主任セールスマネージャであるハラルト・ジーバーが付け加えます。「このようにこのソフトウェアは、1 つの連結された生産設備でジョブに応じて多彩な製品を製造するための基盤を提供しているのです」。同時にソフトウェアは、生産プロセスを透明化し、個々のジョブの個々の部品に対してフィードバックを与えるので、いつでも進捗状況を確認できます。その結果、加工の監視や点検、制御が大幅に容易になっています。問題の発生は、早い時点で検知されます。問題が生じた場合、部品のバーコードを通じて早い時点で再加工が開始できるため、組立の段になって部品が不足する事態が起きません。「ControllerMES」の特徴の一つに、加工ジョブをまとめる機能があります。その利点をペーター・ビッツァー氏は、「事前に、現在のジョブの「必須部品」に後のジョブの「オプション部品」を組み合わせることで、最適な切断図面を作成し、残材を抑えることができるのです」と説明します。
これは、「経済性」という言葉では表しきれません。ControllerMESの設置は、未来への投資なのです。すでに今日の時点で、材料消費、停止時間、非生産的な作業が減少し、加工時間が最小限に抑えられることで、生産性が向上しています。このシステムは、モジュール型の標準ソフトウェアとして、柔軟なコンフィギュレーション、拡張、新たなプロセスへの適合が可能で、同時に 100 パーセントのアップデート能力を備えています。そしてそれが、Erfi の幹部が目指していたことでもあります。製造制御システム「ControllerMES」を他社製部品や電気部品の自社生産にも利用しようというのです。設備は、世界初の木材産業向けデジタルプラットフォーム「tapio」(HK 2017 年 6 月号を参照)に接続されているため、MachineBoardのようなデジタル製品を通じて機械の最新のステータスや異常、エラーメッセージをスマホで確認できます。また、システムからオペレータへ、スマホを通じて異常などを知らせる重要なメッセージが送られます。ご覧のとおり、この点においても Erfi はインダストリー 4.0 の基準に完璧に従っているのです。
ビデオ
Please confirm that when you use YouTube, data such as your IP address, browser identifier and similar may be transmitted to Google.
» 個人情報保護
Industry 4.0 at erfi Ernst Fischer GmbH