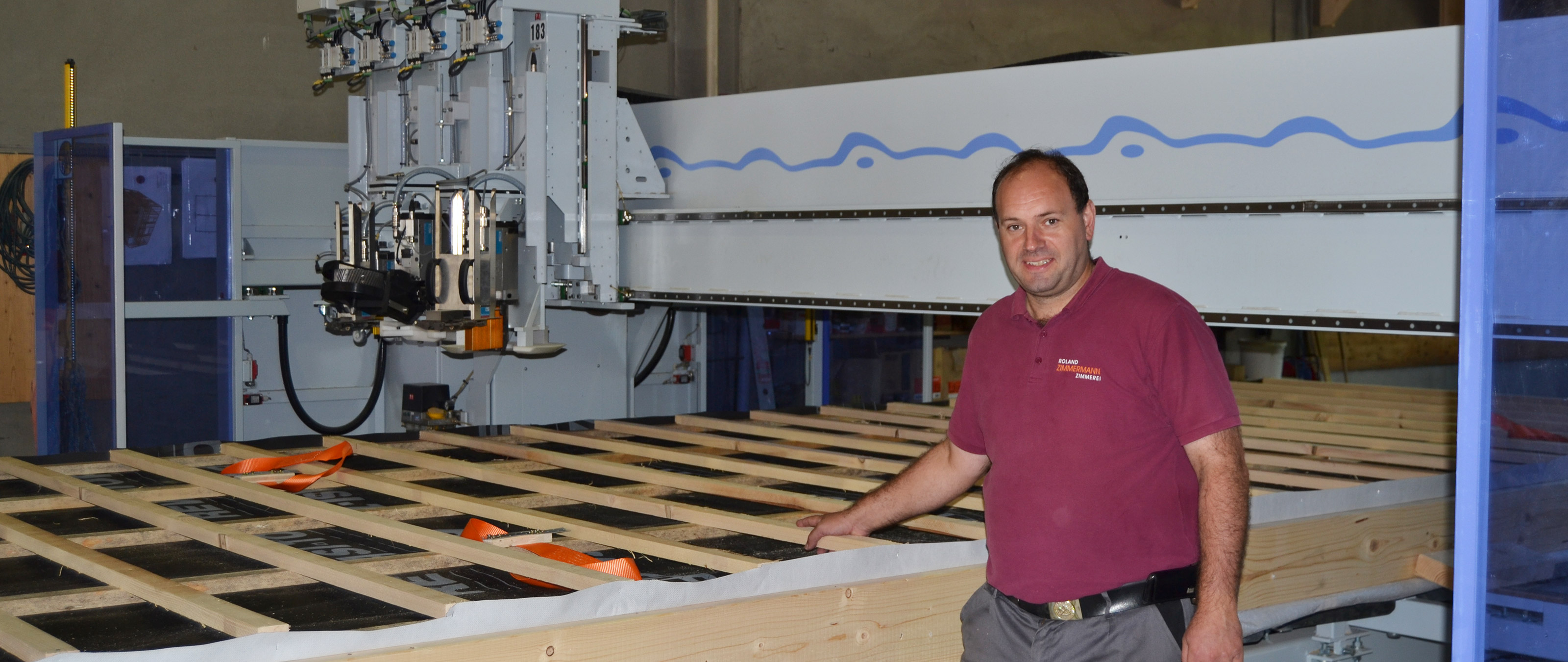
La ligne de production automatisée qu'il a commandée chez WEINMANN l'année dernière se devait donc d'être polyvalente. Elle a rempli toutes ses attentes en la matière, en créant des formes libres que le centre de taille de M. Zimmermann ne pouvait usiner.
Depuis quelques années déjà, on observe, après l'automatisation de la taille de charpentes, une augmentation de l'automatisation de la fabrication d'éléments dans la construction bois artisanale. Les priorités sont évidemment différentes de celles de la production industrielle, où les lignes de production doivent généralement traiter un plus grand nombre de pièces.
Outre le gain en précision, c'est la polyvalence de la ligne de production automatisée qui revêt une importance cruciale aux yeux des entreprises de charpentes, non seulement parce que tous les éléments qu'elles produisent doivent être traités par cette ligne, mais aussi parce que de nombreuses entreprises de charpentes ne proposent pas des pièces de construction standard, mais une vaste gamme d'éléments de cloisons, de plafonds et de toitures différents. La menuiserie Roland Zimmermann de Bad Peterstal-Griesbach ne fait pas exception à la règle et a donc investi dans une installation compacte WEINMANN début 2016.
Des pièces de forme libres sur une installation compacte
Il a fallu plusieurs mois pour que Roland Zimmermann découvre la pleine mesure de la polyvalence de sa nouvelle ligne de production. À l'époque, il avait conclu un contrat dans le cadre duquel il devait fournir à un client français des pièces de construction pour une coupole. Par la suite, il a constaté que certaines pièces de construction qui lui étaient demandées n'étaient pas prévues dans ce contrat. En interrogeant son client, il a découvert qu'elles correspondaient à la base de la coupole et qu'il devait également les fabriquer.
Cette base se compose de huit anneaux de bois massif superposés, constitués chacun de 16 segments annulaires imbriqués. Les rayons de ces segments ne pouvant être usinés par le centre de taille, M. Zimmermann devait trouver une alternative.
Le maître charpentier s'est alors souvenu de la formation qu'il avait effectuée chez WEINMANN : « Je me rappelais que le pack logiciel de mon installation compacte contenait un programme HOMAG qui permettait de créer des formes libres. »
Il a donc pris contact avec WEINMANN et HOMAG afin d'élaborer une solution : « Les techniciens SAV des deux sociétés ont résolu mon problème. Nous avons fait l'acquisition de fraises spécifiques ainsi que d'un échantillon, et HOMAG a généré pour nous les trajectoires de fraisage, ce qui nous a permis de préfabriquer la base de la coupole sur notre pont multifonction. »
Flexibilité « dans toutes les configurations »
Si un tel contrat reste exceptionnel pour Roland Zimmermann, son cahier des charges accordait toutefois une grande importance à la flexibilité, raison pour laquelle il cherchait à automatiser la fabrication de ses éléments. En effet, aidé de ses dix collaborateurs, il ne se contente pas de proposer leurs services dans les segments traditionnels de la charpenterie, tels que la conception de charpentes, la rénovation, l'isolation de toiture ou encore la construction de halls. Grâce au bouche-à-oreille, aux appels d'offres et à sa collaboration avec un promoteur, il s'est également spécialisé dans la construction de maisons d'habitation, en respectant un rayon d'une heure de trajet environ. Au total, ce sont dix à quinze chantiers qu'il mène à terme chaque année, et ce, « dans toutes les configurations », non seulement parce que le charpentier livre des éléments de cloison avec ou sans espace d'installation, dans des matériaux et des épaisseurs d'isolation variés, mais aussi et surtout car il met de temps à autre la fabrication d'ossatures en bois de côté au profit des supports TJI ou d'éléments de bois contrecollé qui sont dotés d'une isolation extérieure sur le chantier. La WMS 150 s'est déjà illustrée dans plusieurs projets : elle a ainsi notamment fraisé des panneaux OSB destinés à un coffrage de gros-œuvre, ou encore formaté des panneaux à trois couches avec différents rainurages envoyés par la suite à Singapour par conteneur pour créer un voligeage.
Il va sans dire que la flexibilité représentait donc un critère essentiel pour M. Zimmermann : « Seul WEINMANN était en mesure de répondre à ce besoin. Les lignes de production concurrentes sont peut-être adaptées à la fabrication de cloisons standard destinées à la construction de maisons préfabriquées, mais rares sont les fabricants dont les machines sont capables d'usiner des pièces de construction personnalisées, qu'il s'agisse de cloisons extérieures et intérieures, d'éléments de toiture et de plafond, ou encore d'éléments en bois massif ou spéciaux. »
La profondeur d'usinage n'est pas en reste : « A l'aide de l'unité Flex 25, nous pouvons usiner des éléments en bois massif ou des panneaux d'isolation en fibre de bois d'une profondeur de coupe pouvant aller jusqu'à 200 mm. »
La WMS 150 de l'entreprise de charpentes, configurée spécialement pour répondre à ses exigences, est par ailleurs équipée de trois cloueuses et agrafeuses, d'une imprimante à jet d'encre et de la broche d'outil 18,5 kW de série et son changeur d'outils à 12 positions. Un pont multifonction doté d'un équipement complet, prêt à faire face à tous les défis de demain.
Défi d'avenir 1 : davantage de préfabrication
A Bad Peterstal, la préfabrication ne cesse d'être perfectionnée. Cela se devine à l'augmentation constante du niveau de préfabrication : alors qu'auparavant, les éléments de cloison étaient souvent livrés ouverts, aujourd'hui, ils sont généralement livrés fermés. L'installation compacte permet également de préfabriquer les éléments de toiture et de plafond. La WMS 150 se charge ainsi notamment de fixer les lattes de toit sur les chevrons.
Afin de garantir un fonctionnement optimal, les charpentiers ont d'abord dû adapter quelques détails aux nouveaux moyens de production : « Aujourd'hui, nous travaillons par exemple avec des chevrons spécifiques pour isoler le toit, car cela facilite notamment le retournement. Le pare-vapeur et la trajectoire de sous-tension des éléments de toiture sont également optimisés et adaptés au cycle d'usinage. »
Les charpentiers ont également complété les paramètres de préparation du travail afin que la WMS 150 dispose de toutes les données dont elle a besoin pour usiner les pièces de construction : « Ce travail, bien que fastidieux au départ, s'est révélé particulièrement utile sur le long terme, car il nous a permis de créer des catalogues de pièces qui réduisent aujourd'hui considérablement la durée de préparation. »
Ces catalogues de pièces comportent également des stratégies d'usinage optimales. Par exemple, un évidement ne doit pas consister uniquement en un fraisage : il est nécessaire d'effectuer une finition nette et précise à chaque extrémité à l'aide d'un trait de scie.
Roland Zimmermann revient sur la démarche adoptée par la menuiserie : « Nous avons d'abord dû comprendre le fonctionnement de la machine et de ses outils, afin d'obtenir les meilleurs résultats possible. Une fois le catalogue de pièces créé, la machine effectue automatiquement tous les fraisages et toutes les découpes nécessaires – lorsqu'une fenêtre est intégrée dans un élément de cloison externe au poste de préparation, par ex. »
Pour l'instant, les fenêtres sont encore montées par un fabricant de fenêtres externe sur le chantier. Roland Zimmermann envisage toutefois d'intégrer cette étape au travail en atelier, dans son objectif d'amélioration de la préfabrication. L'installation compacte va par ailleurs lui permettre à l'avenir de formater les éléments de cloisons massifs en bois contrecollé dont il devait autrefois sous-traiter l'usinage, et d'y intégrer des ouvertures pour les fenêtres, les portes et autres installations.
Défi d'avenir 2 : devenir fournisseur d'autres menuiseries
Ces éléments de cloison massifs pourront également être revendus à d'autres menuiseries, un nouveau secteur d'activité rendu possible par l'automatisation de la production, que Roland Zimmermann compte bien développer dans les années à venir.
Le menuisier souhaite également renforcer la sous-traitance d'éléments à ossature en bois. Il dispose en effet d'une clientèle de sociétés de construction en bois de moyenne taille, qui ne possèdent pas d'équipements de fabrication. Son installation compacte offre de nouvelles perspectives à M. Zimmerman : « Cette nouvelle technologie nous a permis de gagner en efficacité. Nous sommes donc en mesure de proposer des délais de livraison plus courts à nos clients, qui sont notamment implantés à Freibourg et à Karlsruhe, mais aussi de mieux gérer les afflux de commandes. Cela représente un atout non négligeable, car le respect des délais est crucial dans notre secteur.
Les entreprises qui font appel à nous bénéficient par ailleurs d'un niveau de préfabrication élevé : nous pouvons aujourd'hui leur livrer des éléments fermés d'une grande précision qui peuvent être montés rapidement et sans difficulté. Cela permet non seulement d'améliorer la sécurité sur le chantier, mais également de raccourcir les délais de construction. »
Roland Zimmermann a cependant dû faire face à un obstacle pour y parvenir : les contrôles qualité externes. Depuis le mois d'avril dernier, sa menuiserie de Bad Peterstal bénéficie de la marque de conformité « Ü » ; un gage de sécurité supplémentaire pour M. Zimmermann et ses clients.
La nouvelle installation de production compacte a joué un rôle majeur dans cette certification : « Alors que l'auditeur a effectué des vérifications poussées dans plusieurs services de la menuiserie, l'audit de notre production a été particulièrement rapide. Il a examiné les rangées de clous impeccables, en a mesuré une et a validé la section correspondante de l'audit. » Pour le charpentier, il s'agit là d'une reconnaissance du bon travail accompli : « C'est également une des raisons pour lesquelles j'ai investi dans un WMS 150, afin de garantir une précision parfaite et constante des pièces fabriquées. »
La technologie au service de l'argumentaire de vente
Cette précision est non seulement gage de sécurité, mais représente également un réel argument de vente. L'automatisation de la fabrication permet d'améliorer l'apparence des pièces, car les rangées de clous sont disposées en lignes droites et régulières tandis que le fraisage des panneaux de fibres se révèle beaucoup plus net que les anciens perçages, réalisés à partir de machines manuelles.
Les maîtres d'ouvrage ne peuvent donc qu'être convaincus par le professionnalisme de la menuiserie de Bad Peterstal : « Nous gardons cependant en tête que pour nombre de maîtres d'ouvrage, le prix reste l'argument de choix décisif. Mais s'ils hésitent entre un concurrent et nous, nous avons conscience que cette particularité peut faire pencher la balance en notre faveur. Cela vaut également pour les contrats d'architecte, que nous remportons principalement par des appels d'offres. »
Cette nouvelle technique de fabrication a-t-elle permis de réduire les coûts ? « Nous ne sommes pas encore en mesure de l'affirmer, car nous sommes encore en phase d'apprentissage. Une chose est sûre, la production ne nécessite plus que deux collaborateurs, contre quatre auparavant. Mais nous avons davantage de travail de préparation. Par rapport à une fabrication manuelle, nous avons besoin d'une personne en moins, ce qui représente une réduction de coût certaine, dont il reste à déterminer le montant. Elle dépend notamment du taux de charge de la machine. »
Un démarrage sans heurts
Ce dernier point satisfait pour l'instant pleinement M. Zimmermann, qui considère jusqu'ici son investissement comme rentable. « Au début, je n'en étais pas convaincu : il était encore fréquent que quatre collaborateurs travaillent à la production, car nous n'avions pas encore l'habitude de la nouvelle installation. »
M. Zimmermann a-t-il rencontré des difficultés lors du démarrage de la nouvelle ligne de production ? « Pas vraiment, il ne s'agissait que de problèmes mineurs. Avant d'investir dans cette installation, nous avions déjà été très bien conseillés par WEINMANN et Sema. Nous avons ensuite suivi des formations et la production a été lancée très rapidement par la suite. Le collaborateur WEINMANN qui devait nous aider les premiers jours étant malade, nous avons même commencé sans lui.
Tout s'est déroulé sans heurts, nous avons simplement dû effectuer quelques ajustements au début. Et si nous rencontrons un problème aujourd'hui, il peut rapidement être remonté aux techniciens de l'assistance téléphonique et du téléservice. »
Les collaborateurs de Roland Zimmermann ont eux aussi très vite adopté la nouvelle installation. « Notre carnet de commandes a toujours été bien rempli, si bien que personne n'a eu à craindre pour son emploi. Tous les collaborateurs de la menuiserie ont pu voir l'intérêt réel et premier de cette nouvelle installation : un allègement bienvenu de leur charge de travail. Elle a d'ailleurs été accueillie avec enthousiasme : elle nous a ainsi permis de gagner en intérêt auprès des techniciens et des apprentis. »
Depuis la mise en service de l'installation compacte, les collaborateurs de la menuiserie ont mené à bien 32 projets. Dans les années à venir, la fréquence de cycle de la machine pourrait augmenter de façon considérable : depuis la modification de sa production, M. Zimmermann voit la sous-traitance à d'autres entreprises de charpentes comme une tendance grandissante.
Source photos: WEINMANN Holzbausystemtechnik GmbH
Article de "Mikado", 9.2017. Lecture de Mikado online. Lisez l’article complet.